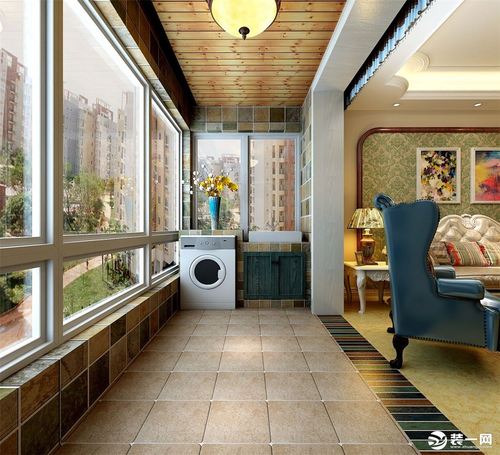
工业防腐蚀涂料施工手册
涂料简介
1、 产品组成及简介
工业防腐蚀涂料广泛应用于各类工矿企业,尤其适合石油钻井塔架的防腐蚀涂装,由底漆、中涂漆和面漆组成。
底漆和中涂层可选用双组份快干氧铁红防锈底漆、双组分环氧富锌底漆、环氧云铁中涂漆等。
面漆可选用快干丙稀酸脂肪、丙稀酸聚氨酯面漆、化橡胶防腐面漆、高氯化聚乙烯防腐面漆等几种产品。
其中,双组分快干环氧铁红防锈底漆由环氧树脂、防锈颜填料及特殊助剂组成,并配成以进口快干型固化剂,可使该涂料在较低的温度下(-5℃以上)施工,使之超越了常规环氧树脂
漆的固化范围,为用户使用提供了极大的方便。双组分环氧副锌底漆由环氧树脂、超细锌粉及助剂组成,通过固化剂的调整,可使涂料在较宽的温度范围内固化,涂膜具有其它底漆无法比拟的防腐性能。
环氧云铁中涂漆由环氧树脂、云母氧化铁防锈颜料、片壮金属颜料、助剂及固化剂组成,因涂料中使用了大量的片状颜填料,使涂料的屏蔽作用大为提高,使之具有优异的耐化学品性能。
快干丙稀酸脂肪 聚氨酯由 基丙稀酸树脂及不黄变的缩二脲固化剂组成,干燥速度快,耐侯性及赖化学品性能极佳,与底漆、中涂漆配套使用时表现出良好的装饰及防腐效果。
另外,面漆也可采用各色氯化橡胶防腐面漆、高氯化聚乙烯防腐面漆、丙稀酸聚氨酯防腐面漆,其组成及特性祥见说明书。
2、固化方式
双组分快干环氧铁红防锈底漆、双组分环氧富锌底漆、环氧云铁中涂漆均为双组分常温固化型环氧树脂涂料,涂料的固化过程为交联固化。甲、乙混合后需熟化(放置)10-20分钟
才能涂刷。常温下,一般需24小时才能干燥固化完全,形成的漆膜与单组分热缩性涂料相比具有优异的机械性能及耐化学介质性能。
快干丙稀酸脂肪 聚氨酯、丙稀酸聚氨酯防腐面漆均为双组分常温固化剂涂料,涂料的固化过程为交联固化,甲、乙组分需按规定比例混合均匀后才能涂刷。常温下,一半需24小时才能固化安全,形成性能良好的涂膜。
氯化橡胶防腐面漆、高氯化乙烯防腐面漆为单组分热缩性涂料,涂料的干燥过程仅为溶剂的挥发过程,干燥完全后,涂膜也可具有良好机械性能及耐化学介质性能。
3、 喷涂工具及使用要求
底、中、面漆涂覆均可采用无空气喷涂或刷涂。底漆/中涂漆采用无空气喷涂时选择喷嘴直径为0.48-0.63毫米,喷嘴处压力不低于176公斤/平方米;采用空气喷涂时压力控制在2—4公斤/平方厘米,漆液粘度控制在20—40秒。刷涂仅限于范围修补,不作特殊要求。
面漆采用无空气喷涂时选择喷嘴直径为0.33—0.45毫米,喷嘴处压力不低于155公斤/平方厘米;采用空气喷涂时压力控制在2—4公斤/平方厘米,漆液粘度控制在20—40秒。刷涂
仅限于范围修补,不作特殊要求。
在施工作业暂停时,应及时清洗管路及喷枪,以防止残留在管路中的油漆固化后堵塞管路及喷枪。
一、油漆施工工艺
二、施工工艺
钢结构毛胚件—— 喷砂除锈,机械除去毛刺 —— 擦洗干净 —— 稀料除油,凉干后,喷底漆—— 空气干燥至符合要求,打磨,擦去浮尘、除油,清扫干净 ——(喷中涂漆 —— 空气干燥至符合要求,打磨,擦去浮尘、除油,清扫干净)—— 喷面漆,空气干燥 —— 组装,调试合格后坼分 —— 喷修补底漆,干燥 —— 修补面漆,干燥 —— 包装,装车,出厂。
施工中应注意的几点问题
1、 基材前处理应注意几个问题
1) 基材除锈、除油应彻底。
2) 基材应干燥,不积水分。
3) 喷沙应达到一顶的粗糙度,露出金属光泽。
2、 喷涂底漆/中涂漆应注意几个问题
1)甲、乙组分混合后,充分搅拌均匀,熟化15—20分钟,然后再喷涂或刷涂。
2)底漆/中涂漆可多喷几道,每一道不要太厚,否则面漆会咬底。
3)最好在干燥24小时后,喷涂中涂漆或面漆。
4)为避免浪费,最好用多少配多少;所配的漆要在规定的胶化期内用完。
5)漆液增稠后,可用专用稀料稀释。
3、喷涂面漆应注意的几个问题
1)喷涂面漆前,应将底漆打磨,吹去灰分,以增加附着力。
2)应在喷底漆24小时后喷涂面漆。本配套系列产品可适当减少喷底、面间隔时间,如夏季需4小时,冬季12小时。
3)每道漆的厚度不宜太厚。薄喷多道的效果优于一道厚喷的效果。
4)使用厂家专用的面漆稀释剂。
4、使用稀料应注意的几个问题
1)稀释剂不应含水。
2)稀释剂要专用:底漆使用底漆的稀释剂:面漆使用面漆自的稀释剂,不可用!
3)稀释剂使用后应密封,防止挥发,影响稀释剂的组成比例。
三、涂料出现的病态及其对策
底漆、中涂漆和面漆均可能出现如下漆病,希望施工时密切注意,避免涂料施工中出现病态。
浑浊
涂料出现微浑浊或变成糊状、浆状的现象
原因:
1、 稀释剂选择不当,只能部分溶解成膜树脂。
2、 稀释剂用量过多,或稀释剂中含有水。
3、 配漆的熟化时间不够,原料中含有杂质。
4、 时有水分及潮气侵入。
5、 时温度过低或过高。
解决方法:
1、 使用厂家专供的溶解性较好的稀释剂。
2、 保证水份勿进入稀释剂或漆桶中。
3、 涂料贮存应在通风的库房中,远离火源、热源,防止日光直射暴晒。
4、 冬季贮存时间,避免过冷。
变厚
涂料在贮存时,出现粘度增稠甚至成胶冻状。
原因:
1、涂料设计 、原材料、生产等环节存在缺陷。
2、贮存过程不当,如:温度过高,太阳暴晒。
3、桶盖密封不当严,溶剂挥发了。
4、潮气、水分进入了油漆桶中。
解决方法:
1、 涂料厂家应严格控制生产质量。
2、 贮存时,库房温度要适当。
3、 油漆贮存要密封,防止溶剂挥发。
4、 防止水分进入油漆中。
结皮
涂料在贮存过程中,表面结出一层薄皮。
原因:
1 、催干剂或增稠剂使用不当。
2、装桶不满,桶盖不严;施工后对剩余的涂料处理不当。
解决方法:
1、 根据实际情况及时调整催干剂或增稠剂的用量。
2、 产品使用后要及时盖严,防止溶剂过度挥发,造成结皮沉淀。
3、 底漆彻底干燥后涂面漆。
四、漆膜涂装缺陷及其对策
渗色
面涂将底层涂料溶解致使底涂的严肃渗透到面涂上的现象。
原因:
1、 底层涂膜在彻底干燥前,面层涂料中的强溶剂将底层涂膜溶解。
2、 底层涂料含有渗透倾向的颜料作底色时,涂面漆前未涂封闭底漆。
3、 底层涂料颜色过深,面涂颜色过浅。
解决方法:
1、 使用专用的面漆或稀释剂;
2、 选择厂家配套的底、面漆。
针孔
涂膜出现如针大小的小孔
原因:
1、 钢材表面翻砂时,有纱眼,填充困难,打磨不好。
2、 连续喷涂两次间隔时间太短,下涂层干燥不完全,上涂层干燥太快。
3、 被涂面有灰尘,压缩空气有水、有污染。
4、 油漆配好后,静止不够》(一般静液放10-25分钟)
5、 一次性厚涂,表面干燥而底层溶剂继续蒸发而凸起。
6、 使用不良的涂料稀释剂,或错用稀释剂。
7、 固化剂加入太多,或借用固化剂。
8、 稀释剂用量太小,涂料粘度过高,气泡产生的针孔。
9、 施工环境温度过高,温度太大。
10、喷涂压力过大或距离太远。
解决方法:
1、 钢材表面充分处理好 ,必要时上一遍腻子,砂纸打磨,达到光滑的要求。
2、 多层涂装时,应尽可能延长看涂时间,让下层充分干燥。
3、 处理好被涂面灰尘和水,打磨后,应除去灰尘和表面的水珠。
4、 分两次或多次施工。
5、 搅拌均匀静置10-20分钟才能使用。
6、 使用配套产品。
7、 按指定的调漆比例正常调漆,并且充分搅拌均匀。
8、 增加稀释剂用量,达到施工最佳粘度。
9、 设法改善施工环境,夏天温度过高,要相应减少固化剂用量,适当加入慢 干溶剂。
10、调整好喷涂严厉和距离。
气泡
涂膜表面出现气泡
原因:
1、 钢材表面沙眼深,填充困难,喷涂成膜后,气体向外喷涂顶起漆膜,引起气泡。
2、 喷涂时,涂料的粘度过高。
3、 喷涂时,空气压缩机的气压过高,涂料混入空气过多。
更多推荐
涂料,面漆,稀释剂,底漆
发布评论