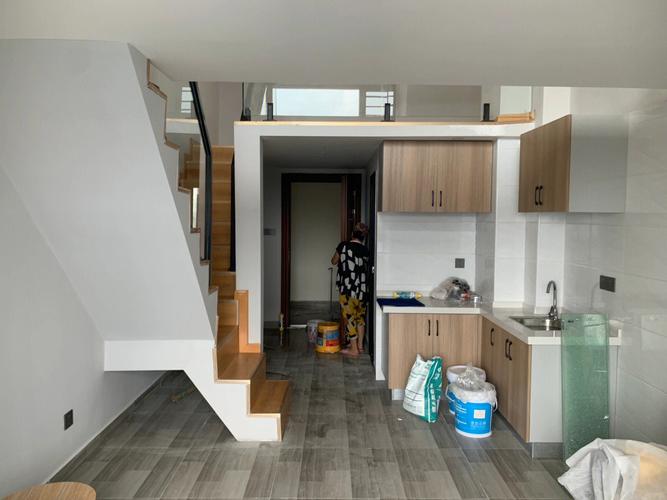
预制单向桁架叠合板施工工艺研究
【摘要】:随着建筑工业化的发展与推进,为建筑行业资源节约、工期管理、绿色生态等带来新的发展方向。结合本工程预制叠合板的使用,重点介绍单向桁架叠合板生产及加工工艺,利用新做法进行施工现场安装质量控制,结合实际施工经验并形成总结,使预制叠合板更好的应用于施工生产。
【关键词】预制装配式住宅、预制叠合板、生产及加工工艺、安装质量控制
一、叠合板设计概况
本工程采用单向桁架钢筋混凝土叠合板,桁架采用A80型。预制叠合板厚度为60mm,现浇层厚度70mm。每栋高层预制混凝土用量约为700m³,叠合板预制率占比为16.47%。
二、预制装配式叠合板施工工艺
(一)设计参数
预制底板混凝土及后浇混凝土叠合层均采用C30。预制底板底面钢筋保护层厚度15mm;预
制底板与后浇混凝土叠合层之间(包括预制底板顶面和四周)的结合面设置粗糙面,其面积不宜小于结合面的80%,粗糙面的凹凸深度不应小于4mm。桁架80mm高,设计共31种板型。
(二)预制叠合板安装施工工艺流程
定位线、标高线、支撑点检查→剪力墙及连梁钢筋、模板施工→叠合板底支撑架检查,墙、梁侧模标高校正→叠合板线位控制点→叠合板吊装、安装→现浇层线管预埋、钢筋绑扎→现浇层混凝土浇筑→混凝土养护
(三)预制叠合板制作、养护先进做法应用
(1)叠合板与安装预埋一体化加工技术应用
根据大货精装深化安装点位,将安装线盒预留于叠合板,减少后续安装施工工作量。优化化叠合板编号及进场顺序,按编号倒序运输,顺序吊装。
(2)全自动温控PC构件养护窑技术应用
预制叠合板采用全自动温控PC构件养护窑进行蒸汽加热养护,制定养护制度对静停、升温、恒温和降温时间进行控制,宜在常温下静停2h-6h,升温、降温速度不应超过20℃/h,最高养护温度不宜超过70℃,预制构件出池的表面温度与环境温度的温差值不宜超过25℃,养护12h强度可达设计强度的75%。
(四)预制叠合板的运输与堆放
(1)施工现场平面布置时,考虑叠合板堆放场地,在施工现场划出构件堆放场地范围,标以标示牌,规范管理,堆放区域应在塔吊工作范围内,避免二次搬运、交叉干扰;堆放时按吊装顺序、规格、品种、所用楼号等分类分区堆放; 水平分层、分型号(左、右)码垛,每垛不超过5块,最下面一根垫木通长,层与层之间应垫平、垫实,各层垫木在一条垂直线上,支点一般为吊装点位置。
(2)叠合板采用平板车平放层叠方式运输;构件分型号装车,垫块应在一条垂直线上,构件装车顺序与卸车顺序一致。
(五)叠合板支撑体系优化
采用铝合金模板支撑体系,下部设置快拆式可调节钢支撑与快拆流星锤,后浇板带区域单独设置铝模及支撑体系。
(六)叠合板安装
(1)线位及标高控制
安装前先弹好叠合板水平及标高控制线,注意核对水暖、消防预留洞的位置,沿着管、洞中心做十字交叉线,在预制板的边缘和安装墙梁的上端都做好标识,作为预制板安装的水平方向的定位点之一。
叠合板安装前将支撑调整至设计标高,叠合板安装后采用激光扫平仪打出标高控制线,对每块叠合板进行标高精确调整,每块板测五个点(四角及中间),尤其控制两块叠合板相邻边标高一致。
(2)自动调平专用吊装工具设计
1)叠合板起吊时,要尽可能减小因自重产生的弯矩,采用专用叠合板吊装工具,吊具设置
自动调平滑轮组,共6个吊点,利用滑轮组连接实现自动调平,并确保叠合板安装时倾斜角度可调。
2)叠合板要从上垂直向下安装,在作业层上空20cm处略作停顿,采用可周转叠合板定位控制器,在叠合板边角处预埋φ8螺帽,配合手字形高强螺杆,形成可循环利用叠合板位置控制装置,一方面,可利用此装置拖拽牵引叠合板前进路线;另一方面可利用此装置固定叠合板安装位置。
(七)施工重难点及解决措施
(1)板端支座胡子筋与梁主筋或竖向钢筋位置冲突,无法安装到位。受箍筋或其它钢筋影响,梁主筋拆除较困难。
解决方案:叠合板板端外伸“胡子筋”在吊装前不得弯折,为方便现场预制板的安装,可根据实际情况,将梁封闭箍筋弯钩放置在下方,方便上部主筋的拆装。注:当遇到墙体纵筋、梁箍筋时“胡子筋”可按1:6水平弯折,错过墙体纵筋和梁箍筋,胡子筋严禁竖向弯折。
更多推荐
叠合,安装,预制,采用,养护,堆放,吊装
发布评论