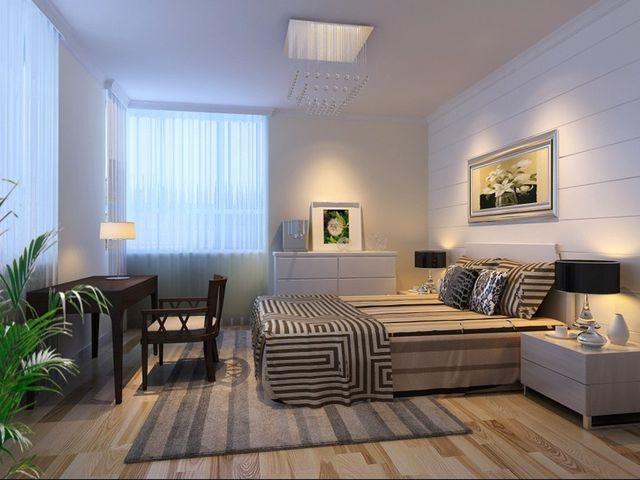
2.2 釉料
第一节釉的作用与分类
1.釉的作用
釉是施于陶瓷坯体表面上的一层极薄的玻璃体。施釉的目的在于改善坯体表面性能,提高产品的力学性能。通常陶坯的表面粗糙,通过施釉使产品表面变得平滑、光亮、不吸湿、不透气。
一般认为釉系玻璃体,但两者是有区别的。釉层的微观组织结构和化学组成的均匀性都较玻璃差,其中经常夹杂一些熔化不透的残留石英和新生的莫来石、钙长石、尖晶石、辉石等晶体,以及数量不一的气泡。
2.釉的分类
(1)按坯体的类型分:瓷釉(硬瓷釉和软瓷釉)、陶釉、器釉。
(2)按烧成温度分;<1100℃的釉称为易熔釉,1100~1250℃的釉称为中温釉,>1250℃的釉称为高温釉。
(3)按釉面特征分:透明釉、乳浊釉、结晶釉、无光釉、无泽釉、碎纹釉、单色釉、花釉等。
(4)按电性能分:普通釉、半导体釉。
(5)按釉料的制备方法分:
1)生料釉
2)熔块釉
3)熔盐釉
4)土釉
(6)按主要熔剂或碱性组分的种类分:
1)以石灰釉为中心—长石釉、石灰釉、镁釉、锌釉、钡釉等;
2)以铅釉为中心——铅釉、无铅釉。
(7)按显微结构和釉性状分:
1)透明釉——无定形玻璃体
2)晶质釉——乳浊釉、析晶釉、沙金釉、无光釉。
3)熔析釉(液相分离釉)——乳浊釉、铁红釉、兔毫釉等。
第二节釉的性质
一、釉的熔融性能
釉的熔融性能包括釉料的熔融温度、釉熔体的黏度、润湿性和表面张力以及釉的特征。
1.釉的熔融温度
釉和玻璃一样无固定熔点,只在一定温度范围内逐渐熔化,因而熔化温度有下限和上限之分。熔融温度下限系指釉的软化变形点,习惯上称之为釉的始熔温度。熔融温度上限是指釉的成熟温度,即釉料充分熔化并在坯上铺展成具有要求性能的平滑优质釉面,通常称此温度为釉的熔化温度或烧成温度。目前多用高温显微镜照相法来测定,即用釉料制成3mm高的小圆柱体,当其受热至棱角变圆时的温度称为始熔温度,软化至与底盘平面形成半圆球形时的温度作为熔化温度。
釉的熔融温度与釉的化学组成、细度密切相关,也因釉浆的均匀程度和烧成时间的长短而有所改变。组成的影响主要决定于釉中的Al2O3 、SiO2 和碱组分的含量和配比以及碱性组分的种类和配比。
2.釉熔体的粘度、润湿性和表面张力
粘度决定釉的铺平程度和均匀性。取决于化学组成和烧成温度。
表面张力过大,高温时对坯体的润湿性不好,易造成缩釉;过小造成流釉。3.釉的熔融性能
二、釉的膨胀系数和抗张强度
(1)热膨胀-引起坯釉间应力的根源
影响因素:化学组成
网络生成体多,热膨胀小;
碱和碱土金属多,热膨胀大;
(2)弹性-有利于消除坯釉间的应力
与引入的离子的极化能力有关
第三节坯釉适应性
坯釉适应性是指熔融性能良好的釉熔液,冷却后与坯体紧密结合成完美的整体,不开裂也不剥落的能
力。主要有以下四个方面的因素,即坯、釉二者膨胀系数之差、坯釉中间层、釉坯的弹性和抗张强度、釉层厚度。
一、膨胀系数对坯釉适应性的影响
当釉的膨胀系数低于坯时,釉比坯体收缩小,具有压缩应力—压缩釉(正釉)当釉的膨胀系数大于坯时,釉受到坯体的拉伸作用,具有张应力—负釉
釉的耐压强度远大于抗张强度,故负釉易裂;正釉不仅不裂,反而能提高产品的机械强度,起着改善表面性能和热性能的良好作用。
只有配制出膨胀系数近于坯而略小于坯的釉料,才能获得合格釉层。
二、中间层对坯釉适应性的影响
坯与釉是两种物质。只有当二者在煅烧时产生一定的化学反应,形成在化学组成和结构上都介于坯、釉的“中间过度层”时,它们才具有成为整体的可能性。
初步认为:中间层在坯釉结合上能否起有利作用,影响程度如何,都与它的厚度和性质以及坯釉的种类有关。
三、釉的弹性和抗张强度对坯釉适应性的影响
具有较高弹性的釉,能适应坯釉形变所产生的应力。弹性的好坏与釉层厚度、釉的化学组成有关。
四、釉层厚度对坯釉适应性的影响
应力变化的总趋势为:釉层加厚,釉的压应力降低,甚至还能转变成张应力。
第四节釉料配制原则、方法及计算(自学内容)
一、釉料配方的制定原则
1.根据坯体性能来调节釉料的熔融性能
2.选配与坯体相适应的釉膨胀系数
3.选配与坯体相适应的釉的酸碱度
4.重视釉的弹性和抗张强度
5.正确选择原料
二、确定釉料配方的方法与步骤
1.掌握必要的资料
确定釉方首先应掌握下列条件:
(1)坯体的煅烧温度、烧成范围和气氛、坯体的主要化学组成;
(2)对釉面性能(如光泽、乳浊、透明等)以及制品机械强度和热稳定性,釉的耐酸碱能力以及硬度等性能指标的具体要求;
(3)制釉原料的化学组成、含杂质情况及工艺性能等
2.借助三元相图和有效的经验
3.利用釉的组成-温度图与有效的经验
4.参考测温锥的组成进行配方
三、釉的配方计算
用釉式或釉的化学组成计算出各原料的配合比称之为釉方计算。生料釉的计算方法与坯料相似。
计算熔块釉时,首先要掌握熔块的配制原则:
1)为使熔块料熔化均匀,在确定酸碱氧化物间的配比时,必须考虑PbO、B2O3 和碱金属组分在高温时的挥发量。一般要求熔块中(RO2 + B2O3)
/ (RO2 +RO)在1:1~3:1之间。
2)用来引入Na2O和K2O的原料均须置于熔块原料之中,长石可以例外。
含硼化合物亦须置于熔块成分内。
3)熔块料中的Na2O和K2O的分子数总和必须较其他碱性氧化物分子数总和要小,这样才能制成不溶于水的熔块。
4)对于含硼熔块料,必须使SiO2 /B2O3 >2(一般为3)。
5)提高熔块料的熔化温度会增加挥发组分的逸失量,故应控制Al2O3 量,使其小于0.2当量数。Al2O3 量过多会使熔体黏度变大,熔块中的物料
不易均匀。
第五节釉浆制备及施釉工艺
虽然一般瓷件上釉层的用料量远小于坯(日用瓷釉约为坯重的1/11),然而它的质量却直接影响产品的性能和等级。
一、釉浆的制备
1.具有合适的细度
釉浆细度直接影响釉浆的稠度和悬浮性,也影响釉浆与坯的黏附能力和釉的溶化温度以及坯釉烧成后的性能和釉面质量。
2.具有适中的釉浆密度
一般规定釉浆密度波动于1.28~1.50g/cm3 之间,即35~50ºBe´(波美度)。对低温素烧坯及干燥生坯,要求釉浆密度为1.43~1.47g/cm3 ;中温素烧坯为1.5~1.6g/cm3 ;烧结坯为1.6~1.7g/cm3 。
二、施釉工艺
陶瓷产品一般在生坯上施釉,一次烧成,或在素坯上施釉,二次烧成。
生产上经常采用浸、烧、喷、滚、涂刷和气化等方法施釉。
第六节釉的形成
釉料在加热过程中将发生如下一系列反应:脱水、固相反应、碳酸盐和硫酸盐的分解。部分原料熔化并生成共熔物,熔融物相互溶解,部分原料挥发和坯釉间的相互反应等。在反应同时釉粒开始烧结、熔化并在坯上铺展为光滑釉面。
陶瓷坯上的薄釉层,有时可使制件的机械强度提高20~40%,热性能也随之有显著改善。但有时却起相反效果,使制件发生弯曲变形,甚至出窑后釉面立即出现纹裂,或者从坯上剥落。前者称之为釉裂或早期龟裂,后者称为剥釉。其主要因素是:釉与坯的膨胀系数的适应性、釉本身的机械强度和弹性的大小。
第七节乳浊釉
用低质原料配成坯料生产陶瓷产品时,广泛应用遮盖力强的乳浊釉以提高釉面质量。生产时,人为地往透明釉中引入一定量的乳浊釉,由于它的不溶性,重结晶或分相等作用而使釉层乳浊。按烧成温度高低,乳浊釉可分为两种:高温生料乳浊釉多用于卫生瓷,低温熔块乳浊釉多用于精陶质釉面砖等。
一、釉料乳浊化机理
熔化的釉料,冷却后并不都能成为具有光泽的透明玻璃体,有时会失去光泽或透明性。其原因在于釉玻璃中产生了析晶、分相或釉料组成的不溶解,以及分解释放出大量气体等作用,使釉中悬浮着许多固相细粒、微小气泡和不相溶的熔滴。由于它们和主体玻璃相间存在着折射率的差别而发生光的散射,造成釉的失透和无光。
如果釉中析出或残留的细晶以及分相的熔滴具有高的折射率,且在釉中均匀分
更多推荐
温度,组成,釉料,性能,熔化,化学,具有
发布评论