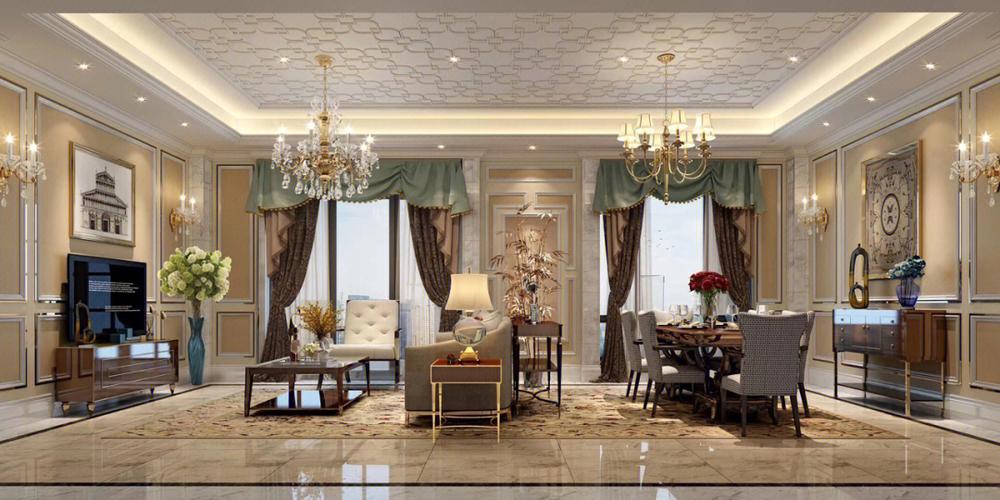
Al 2O 3陶瓷生产工艺中的若干问题3
苗赫濯
(清华大学材料科学与工程系,北京100084)
Main Problems and Solutions for the Production of Alumina Ceramics
MI AO He 2zhuo
(State K ey Laboratory o f New Ceramics and Fine Processing ,Tsinghua Univer sity ,Beijing 100084,China )
Abstract : The problems and s olutions for the production of alumina ceramics were reviewed.The emphasis was paid on the raw materi 2als preparation ,composition ,mixing ,forming and sintering of alumina ceramics.The trends on research and development were proposed.
K eyw ords : Alumina ceramics ;Process ;Raw materials preparation ;F orming ;Sintering
摘 要: 介绍了Al 2O 3陶瓷生产中的若干问题,特别是国内外在Al 2O 3陶瓷原料制备、配料、成型与烧结等方面的生产情况和研发动向,同时提出了自己的看法。
关键词: Al 2O 3陶瓷;生产工艺;原料制备;成型;烧结
中图分类号:T B756 文献标识码:A 文章编号:100228935(2002)0320001205
收稿日期:2002205211
3本篇为“电子陶瓷及其在真空电子行业中应用技术交流会”的特邀报告。
作者简介:苗赫濯,男,清华大学材料科学与工程系教授,博士生导师,国际陶瓷科学院院士,中国机械工程学会材料分会名誉理事,工程陶瓷专业委员会名誉主任委员。长期从事先进结构陶瓷材料的教学与研究工作,主要成果有:透明氧化铝陶瓷与高压钠灯,氮化硅与复合氮化硅陶瓷刀具等,曾荣获国家发明二等奖,日内瓦国际发明展览会镀金牌奖等一系列奖励。
Al 2O 3陶瓷是性能优异,工艺成熟,用途广泛。市场需求较大的一种结构陶瓷材料,它具有耐热、耐磨、耐腐蚀性好、电阻率大、介质损耗小、击穿电压高等特性,广泛用于冶金、化工、电子、机械、军工、航天航空等技术领域。尽管它在我国已有几十年的历史,但时至今日,其性能仍然在不断提高,其应用不断扩展。
1 原料及其加工方法
规模生产的Al 2O 3陶瓷所采用的原料一般为工
业氧化铝,平均粒径为50~70μm ,这种粉体由1~10μm 的原晶聚合而成,但陶瓷生产配料前应将其
粉碎到原晶粒度或更小。在我国目前采用的磨细方法有球磨、气流粉碎、振动球磨和搅拌球磨等。
球磨是以往最常用的方法,这种方法成本低、设备简单,但磨细效率较差,需要较长的时间。其极限细度约为1μm 。
振动球磨是效率较高的一种磨细方法,靠撞击和碾压两种作用对Al 2O 3粉进行破碎。振动球磨所
得到的颗粒往往棱角多、流动性差。振磨的粉碎效果要比球磨高得多,实验表明[1],α2Al 2O 3粉经球磨72h ,粒径小于2μm 的颗粒不到一半,而振磨1h ,粒
度几乎全在2μm 以下。振磨的缺点是震动大,噪音高,设备易损。
气流粉碎是目前陶瓷原料生产厂常用的磨细方法,即将工业Al 2O 3粉购入后进行转相,然后用气流粉碎机磨细向客户供应。气流粉碎是靠高速气流的冲刷,使粉料相互碰撞、剪切、撕裂,达到粉碎的目的,可获得1~2μm 的粉粒。粉粒更小时由于其本身质量太小,碰撞作用力不大,很难继续细化。
搅拌球磨机是美国A.S zegvar 发明的,类似于化学试验的搅拌器,桶体固定不动,位于中央的搅拌棒以700~1400r/min 的速度旋转,带动磨球和粉料在桶内作无规则的碰撞、翻滚、磨擦,达到磨细的效
果。搅拌球磨效率高,可磨至0.5μm 以下的细度。郑州轻金属研究院的实验研究表明[2],采用原晶粒度为2~4μm ,加入粒度为50~70μm 的α2Al 2O 3粉,搅拌
1
2002年第3期 VAC UUM E LECTRONICS
真 空 电 子 技 术
2~3h ,其平均粒度(D 50)可磨细至2~3μm ,而且粒
径范围窄(在0~10μm 之间),而采用普通球磨机则
要磨24h 。如果原晶粒度更细一些,延长搅拌球磨时间,尚可以获得更细的Al 2O 3粉。
随着工业技术的发展,需要采用高纯高密度超细晶粒Al 2O 3陶瓷,例如透明Al 2O 3陶瓷高压钠灯管、高强度Al 2O 3陶瓷零部件等,此时不能采用工业Al 2O 3作为原料,而要采用高纯超细Al 2O 3粉末,一般其纯度应在99.9%以上,其细度在0.3~0.4μm 以下,而且应具备较好的烧结活性。
我国研制和生产的高纯超细Al 2O 3粉主要是采取湿化学法,然后通过热分解来获得超细粉。目前向市场提供较多的方法有硫酸铝铵热分解法、碳酸铝铵热分解法和有机铝热解法等。
硫酸铝铵法是通过硫酸铝和硫酸铵共沉淀,经过多次溶解、结晶和提纯而获得的。其分子式为Al 2(NH 4)2(S O 4)4・24H 2O ,含结晶水的硫酸铝铵晶体经1000℃以下的热分解后便得到纯度为99.97%以上松散状γ2Al 2O 3粉,再经1250~1350℃转相后得α2Al 2O 3粉,这种Al 2O 3粉很容易磨细至0.2~0.3μm 的颗粒,并有很大的活性。
其分解过程为[3]:Al 2(NH 4)2(S O 4)4・24H 2O 200℃
Al 2(S O 4)3・
(NH 4)2S O 4・H 2O +23H 2O ↑Al (S O 4)3・(NH 4)2・S O 4・H 2O 500~600℃Al 2(S O 4)3+
2NH 3↑+S O 3↑+2H 2O ↑Al 2(S O 4)3
800~900℃
γ2Al 2O 3+3S O 3↑,
γ2Al 2O 31300℃
α2Al 2O 3
碳酸铝铵法是近年来发展起来的制备高纯超细
Al 2O 3粉的方法,其分子式为NH 4Al (OH )2C O 3,它是
将铵矾NH 4・Al 3(S O 4)2(OH )6和NH 4HC O 3反应,制得
0.1~0.3μm 大小的纯度为99.99%以上的α2Al 2O 3超细粉,日本大明化学公司就是采用了这种方法[3]。其反应过程为:
NH 4Al 3(S O 4)2(OH )6+3[NH 4・HC O 3]3[NH 4Al
(OH )2・C O 3]+NH 3↑+2H 2O ↑+2S O 3↑2[NH 4Al (OH )2・C O 3]1300℃
Al 2O 3+2NH 3↑
+3H 2O ↑+2C O 2↑
醇铝法是直接用纯铝和醇溶液反应得到醇铝,再水解制备出水合氧化铝,经过热分解得到超细Al 2O 3,其反应式为[4]:
Al +3
CHOH
CH 3
CH 3
(C 3H 2O )3Al +7H 2↑2(C 3H 7O )3Al +4H 2O Al 2O 3・H 2O +6C 3H 7OH
Al 2O 3・H 2O
γ2Al 2O 3+H 2O
此法制备的Al 2O 3粉纯度高、活性好、比表面积大,但工艺方法相对复杂。
制备高纯超细Al 2O 3粉的方法很多,国内目前研制与生产单位亦很多,但很少能够提供稳定的产品,不同时期不同批号的产品质量变化也很大。另外有的产品虽然其纯度和细度也能达到较高的指标,但做成制品的性能与国外产品仍有较大的差距,说明生产中仍有存在许多问题。同时也由于厂家太多,方法太多,加上厂家分分合合,各家销售量都不非常大,也使得难以有足够的效益,不断提高质量,形成规模化的稳定生产。
表1是日本市售典型Al 2O 3原料特性。
表1 日本市售典型Al 2O 3原料特性[3]
方法
硫酸铝铵热介法碳酸铝铵热介法
氯乙醇法
改良拜耳法铝在水中火花放电法
醇盐法
含量
Al 2O 3/%
Fe 2O 3/%S iO 2/%Na 2O/%
>99.99>99.99>99.99>99.99>99.99>99.990.0040.0030.0020.0010.004<0.0010.0090.0080.0020.0030.004<0.0020.0070.0010.0010.004<0.003<0.0004平均粒度D 50/μm
0.52
0.35
0.60
0.50
0.83
0.10~0.30
公司名称
拜柯夫斯基大明化学工业
住友化学工业岩谷化学工业
住友化学工业商品名称
CR 26T N 210
A 2MPST RA 240AK P 250
2 组成
95%Al 2O 3瓷是最常用的Al 2O 3瓷,因为它的力
学、电学和热学性能满足大多数行业技术应用的要求,生产工艺比较成熟,生产设备也较通用,成本较低,所以广泛用于电子、机械、化工、纺织和冶金等行
业。而纯度更高的99%Al 2O 3瓷虽然一些性能比较
好,但原料和工艺设备要求比较高,生产难度较大。所以一般都尽可能不采用99%Al 2O 3瓷。
国内制备95%Al 2O 3瓷,为了形成液相烧结多采用Al 2O 32CaO 2SiO 2和Al 2O 32MgO 2SiO 2两种体系,也
2真 空 电 子 技 术2002年
有采用Al2O32CaO2MgO2SiO2四元体系的,目的都是在保证性能要求的情况下,达到烧结致密的效果。国内生产的添加CaO2SiO2的Al2O3瓷,烧成温度较低,约1630℃,但晶粒较大容易包住封闭气孔,添加MgO2SiO2的Al2O3瓷,晶粒较小,但介质损耗偏高,烧成温度偏高,约1650℃。采用Al2O32SiO22CaO2 MgO体系,不仅烧成温度较低,而且晶粒较小,结构致密,具有较好的性能。
有研究报道,在95%Al2O3瓷中,当MgO,CaO 总添加量相近时,MgO/CaO较高的获得了较好的密度和机械性能,而当MgO/CaO之比相同时,MgO数量高者获得较好的密度和性能,说明MgO促进了烧结,阻碍了Al2O3的晶粒的异常长大,但是当MgO含量大于3%以后,反而不能得到高密度和均匀晶粒结构。高如琴等[5]的研究也得到类似的结果,他们在Al2O32SiO22CaO体系中再加入滑石来引入MgO,在滑石添加量为0.9%时效果最好,如少于0.9%时生成尖晶石的量不足以包覆刚玉晶粒,部分晶粒粗大而且不均匀,闭口气孔较多;滑石量过多超过0. 9%时,效果也不好,认为是MgO超过了其在液相中的溶解度,MgAl2O4浮在液体中,增大了液相粘度,阻碍烧结的进行,引起晶粒发育不完全,气孔率上升,性能下降。
99%Al2O3陶瓷的添加剂很少,主要是靠固相烧结来实现致密化的,而传质过程是靠体积扩散来进行的。为了促进烧结致密化过程,可以添加少量的外加剂,例如MgO,T iO2,La2O3,Y2O3,Cr2O3等都常作为高纯Al2O3陶瓷的烧结助剂。
MgO是最常用的一种烧结助剂,1959年美国R. L.C oble采用MgO使高纯Al2O3陶瓷烧制成无气孔的半透明状态。一般认为是由于MgO与Al2O3高温下反应,在晶界上形成镁铝尖晶石相造成的,因为在Al2O3粉末压实体中原有许多孔隙,在高温烧结时Al2O3晶粒会迅速长大,而Al2O3颗粒间的气孔来不及逸出,就被长大的Al2O3晶粒所包裹形成永久残留的气孔,而MgO・Al2O3(镁铝尖晶石)的出现,则可以阻碍Al2O3晶粒的迅速长大,使气孔有充分时间和机会逸出。但是MgO比较容易蒸发,会形成表
面与内部晶粒的不均匀。ZnO,NiO也能抑制Al2O3晶粒的过分增大,而且不像MgO那样容易蒸发。
T iO2,Cr2O3,Fe2O3,Mn2O3等外加剂,它们的晶格常数与Al2O3都比较接近,能够与Al2O3生成固溶体,增加晶格缺陷,活化晶格,促进烧结。
T iO2是促进Al2O3陶瓷烧结的常用外加剂,因为T i4+与Al3+的离子半径比较接近,相差小于15%,能形成置换固溶体,为了达到电价平衡将产生晶格缺陷。其缺陷方程式如下:
3T iO2
2Al2O3
3T i・Al+6O O+V Al(Al离子空位)
Al2O3
2T iO3
2Al′Ti+3O O+V¨O(氧离子空位)
空位的产生活化了晶格,增加了离子的扩散率,促进了烧结。有资料表明,在Al2O3中加入0.5%~1.0
%的T iO2,可使烧结温度降低100~150℃。有实验报道,T iO2在氧化气氛中起良好的作用,但在还原气氛中会降低瓷体性能,不宜作电绝缘瓷的外加剂。
这一类外加剂虽然能促进烧结,但是因为瓷体内缺少液相,晶粒间气孔很难充分填充,气密性较差。同时电性能也下降很多,因为晶格产生了缺陷,增加了弱连系离子,必然会增加电导如弛张极化,从而降低了材料的电阻值和增加了介质损耗。
La2O3,Y2O3,Sm2O3等一些稀土氧化物在不同程度上可以促进烧结、降低烧结温度并减小晶粒粒度。薄占满等[6]选用高纯Al2O3原料,在95%Al2O3配方基础上添加0.5%~0.7%的La2O3或Sm2O3,能使烧结温度降低30℃左右,晶粒稍有减小而且均匀致密。
3 成型
成型问题一直是影响结构陶瓷制品生产质量和成本的难题之一。陶瓷材料的成型方法可粗略分为干法成型和湿法成型两大类。由于湿法成型的陶瓷料是由陶瓷原料和其他介质(水,有机物等)组成的胶态体系,因此湿法成型也可称为胶态成型。表2列出了一部分常见成型方法。
图1 干压成型生产复杂形状的制品
干压成型虽然是十分传统的方法,而且以往只能成型形状简单的扁平制品,但时至今日,在许多工业
发达国家仍是最主要的成型方法,因为它的效率高,工艺成本低。特别是近年来由于压力机和模具
3
第3期苗赫濯:Al2O3陶瓷生产工艺中的若干问题
技术的进步,它已不仅用来成型形状简单制品,甚至可用来成型形状较为复杂的制品,如图1所示。例如,带孔的水龙头阀片,形形色色的金属切削刀具、齿轮、轴承球、轴承圈、甚至直径小至2~3mm的球体,当然这些制品基本上是扁平状的。在生产过程中,尽可能采用干压成型方法,是规模化、连续化生产的优选方案。
冷等静压成型仍然是目前生产高密度高质量陶瓷制品的最重要成型方法,冷等静压成型分湿袋法和干袋法。早期采用湿袋法等静压,然后机加工,可成型形状比较复杂的制品。虽然效率较低,但成型质量有保证,因此这种方法在国内外都很常用,特别是对于一些体积大,形状很不规则的或者批量很小不宜制造模具的制品,应采用湿袋法等静压成型。
表2 一些常用的成型方法
分类成型方法分散介质成型原理特点
干法成型干压成型加少量粘结剂,如聚乙烯醇
靠单向压力的作用使颗粒聚
集
成型扁平制品,生产效率高等静压成型不加或加少量粘结剂靠静水压力使颗粒聚集成型密度高,可达60%
湿法成型普通注浆成型水或有机介质,分散剂等多孔模具吸收介质
成型薄壁复杂形状制品,坯体
均匀性差
热压铸成型石蜡,表面活性剂石蜡凝固,脱蜡
成型复杂部件,效率高坯体性
能差
凝胶注模成型
有机单体介质,交联剂,催化
剂等
有机单体交联,浆料凝固,脱
脂
成型复杂部件,坯体强度高
直接凝固水,分散剂,催化原位减小电位浆料凝固坯体密度高,均匀性好
注模成型反应添加剂
由于干袋法连续等静压成型机的出现,使得一部分形状复杂但有规则的制品也可以实现高效率的等静压成型。例如Al2O3陶瓷火花塞、透明Al2O3陶瓷灯管、各种陶瓷球坯都已采用连续等静压成型,不仅成型质量好、坯体密度高而且成型效率也十分高,可以构成自动化生产。日本NGK公司生产Al2O3火花塞,采用连续等静压成型,气动传输,自动装卡加工,直至出最终产品,整个工艺过程都不需要人手接触,保证了高质量、高效率、无污染、质量均匀。国内生产用于陶瓷釉料磨细用的90%~95%Al2O3磨球,过去采用湿袋法等静压成型方法效率较低,手工操作很多。近年来新建立的生产线,基本上是采用干袋法连续等静压成型的方法,采用硬橡皮模腔作为传递压力的介质,一般压力为150~200MPa,一次循环时间为30~60s,一次出球8~12个,生产效率非常高,素坯相对密度可达
到60%。
真空管壳以往是采用热压铸方法成型,要求Al2O3颗粒不能太细,但成型密度较低,影响烧成后制品的力学和电学性能。近年来有一些工厂采用湿袋法等静压成型,质量较好。当然湿袋法等静压成型效率较低,成型后还要机加工,车出波纹,工艺比较繁琐。在国外有的公司生产石油用的陶瓷缸套就是采用干袋法连续等静压成型,缸套直径达到<170 mm,长400mm,比一般的真空管壳还要大。可见并不是只有小制品才能采用连续等静压成型。
在胶态成型当中普通注浆成型和热压铸成型是大家十分熟识的方法,热压铸法是20世纪50年代从苏联引进的技术,在电子陶瓷中得到广泛的应用,特别便于形状复杂的小制品的生产。西方国家用这种方法不多,称之为低压注射成型。
注射成型工艺是在陶瓷粉料中加入热塑性树脂、增塑剂、润滑剂等有机结合剂,其熔点在50~150℃范围内,其体积百分比小于50%,将它们充分混合,形成小颗粒,然后将混合料放入注射成型机料斗中。如同塑料制品的注射成型一样,混合料在注射机中受热(≤150℃)而获得塑性,通过注射机的螺旋推进杆,在小于200MPa的挤压力下被注射到金属模具内,冷却后有机质凝固就能获得所需要的形状。注射成型可获得复杂的形状,有较高的素坯密度(≈60%),生产效率高,是一种规模生产精密陶瓷零件的工艺。国外已用来生产复杂形状的发动机零件,如涡轮增压器转子、气门、涡流室锒块、喷油
咀针阀、摇臂锒块、燃气轮机转子动叶片和静叶片等。近年来开发的精密而细小ZrO2光纤连接器也是采用注射成型方法生产的,特别困难的是制造其精密的模具。
值得一提的是,近十年来研究成功的直接凝固注模成型(DCC)和凝胶注模成型是两种胶态成型的
4真 空 电 子 技 术2002年
新方法。
DCC是瑞士联邦技术学院的L.J.G aucK ler教授和T.G raule博士发明的一种净尺寸胶态成型方法[7]。当陶瓷颗粒在水介质中时,调节pH值使之远离等电点,颗粒表面将形成双电层结构,颗粒互相排斥而在介质中呈分散状态,即使颗粒体积含量达到60%仍有流动性。L.J.G auckler和T.G raule在低温的陶瓷料浆中(5℃)放入尿素与尿素酶,此时料浆的pH值仍未改变,保持较低的粘度,可以充模成型,成型后提高温度至20~50℃,此时尿素酶促进尿素的分解,放出OH-,逐步使料浆的pH值调整到等电点上,此时颗粒之间已无互相排斥作用,而靠范德华力团聚在一起成为凝固状态。由于固相体积含量很高,凝固的料浆具有足够高的强度使成型的坯体脱模。
DCC方法采用无孔模具,可成型复杂的形状,坯体密度均匀,由于颗粒经过分散,烧结收缩均匀一致,微观裂纹很少,所以有较高的强度和韦伯模数。采用DCC成型经热等静压烧结的纯Al2O3陶瓷的
强度为680±17MPa,韦伯模数为47。同样的原料如采用冷等静压成型,则强度只有542±50MPa,韦伯模数只有12.8。
现已经成功地用DCC方法制备出Al2O3,SiC, Si3N4形状复杂的制品。德国Ceramtec公司采用此技术来生产人工关节和Al2O3陶瓷刀具。
凝胶注模成型是由美国橡树岭(Oak Ridge)国家实验室M.A.Jenny和O.O.Omatete教授发明的一种胶态成型技术[8,9]。此法是将陶瓷粉料分散在含有有机单体(如丙烯酰胺,AM(C2H3C ONH2))和交联剂(如N,N′—亚甲双丙烯酰胺,M BAM(C2H10N2O2)的水溶液或非水溶液中,制备出低粘度且高固相体积分数的浓悬浮体(>50%),然后加入引发剂和催化剂,将悬浮体注入非孔的模具中,在一定的温度条件下,引发有机单体聚合,悬浮体粘度剧增,从而导致原位凝固成型,最后经过长时间的低温干燥后可得到强度很高而且可进行机加工的坯体。
凝胶注模成型常用的引发剂为过硫酸钾(K2S2O8)或过硫酸铵((NH4)2S2O8),催化剂如N,N, N′,N′—四甲基乙二胺(TE ME D C5H16N2);分散剂如柠檬酸铵,聚丙稀酸铵;增塑剂如丙三醇,聚乙二醇;润滑剂如十二烷基苯横酸钠和吐温80;除泡剂如磷酸三丁脂等。
由于是单体与交联剂反应形成聚合物网络,陶瓷粉末均匀分散于网络中并与聚合物发生吸附作用,因而可获得较高的坯体强度。此外,凝胶注模成型还具有成型周期短,模具可使用多种材料,适于成型
形状复杂的大型薄膜及厚壁部件,坯体缺陷少等优点。
聚合物中单体质量含量占溶剂的(10~20)%,占坯体总质量的(2~6)%,很容易通过脱脂除去,经过烧结,即可得到致密的烧结体。
凝胶注模成型已成功地用于Al2O3,SiC,Si3N4, Sialon,ZrO2等多种陶瓷的成型,在国内已用来制备造纸机刮水板陶瓷元件、大规模集成电路基片等。
4 烧结
烧结工艺制度与原料种类和细度配方组成、成型密度等一系列因素有关,烧结成品要求达到较高的密度,较少的缺陷和微观裂纹,晶粒细小而均匀。在能获得致密烧结的情况下,尽可能烧成温度低,烧结时间短,可以避免晶粒的过分长大。
虽然烧结有常压烧结、热压烧结、气压烧结、微波烧结和热等静压烧结等许多方法,但对于Al2O3陶瓷来说,最经济有效的方法仍然是常压烧结,过去多采用油窑,煤气窑,近年来越来越多采用M oSi2棒隧道窑来进行烧结,这样生产效率较高,控制也比较容易,各个制品都接受到同样的温度历程。
微波烧结是一种体积性加热方法,近年来国内外有许多研究,这种方法能耗少、温度均匀,是一种很有发展前途的烧结技术,但是由于相应的装备研究还不成熟,在国内要达到实用化还有一个过程,所
以目前还不能作为Al2O3陶瓷烧结的产业化技术。5 结论
(1)Al2O3陶瓷历史悠久,应用面广。由于性能优越,成本低,其用途不断扩大,性能也在不断改善。
(2)Al2O3陶瓷原料生产方法很多,品种也多,其发展方向是高纯、超细、高烧结活性。
(3)根据Al2O3含量的不同,Al2O3陶瓷有Al2O32SiO22CaO,Al2O32MgO2CaO,Al2O32MgO2SiO22CaO 等不同材料体系,少量的添加剂如T iO2,La2O3,Y2O3等亦对Al2O3陶瓷烧结性能有很大影响。
(4)成型问题一直是影响Al2O3陶瓷生产质量和成本的难题之一。近十年多来,成型技术有很大发展,除传统的干压、等静压成型方法在技术上有很大提高以外,又出现了许多新的成型方法,如直接凝固注模成型、凝胶注模成型等。(下转第14页)
5
第3期苗赫濯:Al2O3陶瓷生产工艺中的若干问题
更多推荐
成型,烧结,陶瓷
发布评论