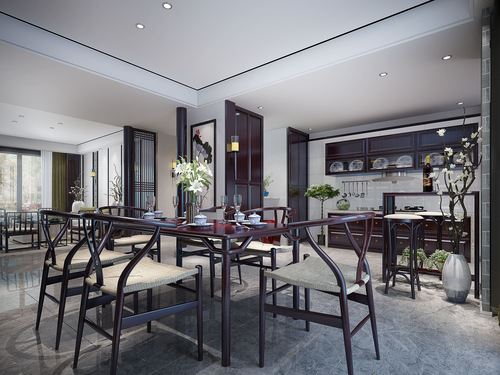
我国是陶瓷生产大国,日用陶瓷和建筑卫生陶瓷的
产量均居世界第一。2019年,我国日用陶瓷产量高达
310亿件,建筑陶瓷砖产量约为101.5亿平方米;按照
15~20kg/m2计算,则需要消耗泥料和石粉1,5000~2,000万吨,
以每平方米陶瓷砖耗能大约为550大卡,消耗1.7m3天
然气/㎡计,则需要消耗天然气大约,172.55亿m3,实属
高耗材、高耗能产业。
近年来,各级部门正按照《建筑卫生陶瓷单位产品
能源消耗限额》(GB21252-2013)和《陶瓷工业污染物排放
标准》(GB25464-2010修订版)标准要求。落实大气污染
防治攻坚战和实现万元产值综合能耗逐年降低,烟气粉
尘排放总量、二氧化硫排放量、氮氧化和二氧化碳排放
总量逐年降低,直至2030年产业全面实现“碳达峰”和
2060年全面实现“碳中和”的总体目标。
多孔陶瓷作为陶瓷的一个类别,它不仅具有普通陶
瓷的化学稳定性好、刚度高、耐热性好等优良特性,还有
更多的因其孔洞结构而具有的性能,如密度小、质量轻、
比表面积大、导热系数小等等。由于其具有独特的化学、
力学、热学、光学、电学等方面的性能,多孔陶瓷已经成
为一类具有巨大应用潜力的材料[1]。目前应用领域已经
涉及到环保、能源、化工、航空、冶金、石油化工、建筑、生
物医药、原子能、电化学等领域。用于分离过滤、吸声隔
音、载体、隔热、
换热、传感器、
曝气、电极、生物植入、蓄
热等场合。
下文分析多孔陶瓷的分类、制造方法和在陶瓷产业
的应用现状。
多孔陶瓷是一种含有较多孔洞的无机非金属材料,
并且是利用材料中孔洞的结构和(或)表面积,结合材料
本身材质,来达到所需要的热、电、磁、光等物理及化学
性能,从而可以用作净化、提纯、过滤、分离、分散、渗透、
保温、隔热、换热、吸声、隔音、吸附、载体、反应、传感及
生物等用途的材料。
多孔陶瓷按照材料成分可分为:氧化物陶瓷和非氧
化物陶瓷,譬如碳化物陶瓷和氮化物陶瓷;氧化物陶瓷
又可以分为:氧化硅质、氧化铝质(刚玉质)、氧化锆质、
莫来石质、堇青石质、氧化钛质、钙钛矿质、氧化锡质、硅
酸锆质、钛酸铝质、硅灰石质、锂辉石质、硅藻土质、硅线
石质、珍珠岩质、长石莫来石质、长石页岩质、煤矸石质、
粉煤灰质、花岗岩尾矿质、钼尾矿质、铜尾矿质、锂尾矿
质、铁尾矿质、赤泥-煤矸石质、沸石分子筛、硅酸盐玻
璃质以及鹏硅酸盐玻璃质等等。按照材料晶相组成,有
可分为:陶瓷质(陶质和瓷砖)、玻璃陶瓷质(有时也叫微
晶玻璃质)、玻璃质(也叫多孔玻璃)。多孔陶瓷也可以按
照孔径和气孔形态分类,譬如按照气孔形态可以分为开
孔型(以开口气孔占主体的多孔陶瓷)、闭孔型(以封闭
气孔占主体的多孔陶瓷)和贯通气孔型(属于开口气孔
多孔陶瓷中的特类);按照孔径可以分为宏孔(孔径>
50nm)、
介孔(孔径>1.5nm,<50nm)、微孔(<1.5nm)
。
多孔陶瓷是一种含有较多孔洞的无机非金属材料,
韩复兴,陈延东,
李玉峰,张晓宇
(安徽瑞蒙科技有限公司,亳州233500)
“高耗材、高耗能”产业,不仅面临着“节能减排、绿色发展”近期目标;而且面临着2030“碳达峰”和2060“碳中和”的双碳目标。文章对多孔陶瓷的制造方法、在陶瓷工业的应用现状进行分析,提出多孔陶瓷是陶瓷工业“清洁、绿色、
低碳”发展的重要基础材料,多孔陶瓷的研究和广泛应用将促进产业转型和实现可持续发展。
;陶瓷产业;
节能环保;碳中和;绿色低碳发展
(1972,6-),男,汉族,河南安阳人,材料工程师,长期
致力于建筑陶瓷功能化、绿色化和固体废弃物资源化研究。E-MAIL:
。
Production&Application
生产与应用
并且是利用材料中孔洞的结构和
(或)表面积,结合材料本身材质,来达到所需要的热、电、磁、光等物理及化学性能,从而可以用作净化、提纯、过滤、分离、分散、渗透、保温、隔热、换热、吸声、隔音、吸附、载体、反应、传感及生物等用途的材料。
多孔陶瓷按照材料成分可分为:氧化物陶瓷和非氧化物陶瓷,譬如碳化物陶瓷和氮化物陶瓷;氧化物陶瓷又可以分为:氧化硅质、氧化铝质(刚玉质)、氧化锆质、莫来石质、堇青石质、氧化钛质、钙钛矿质、氧化锡质、硅酸锆质、钛酸铝质、硅灰石质、锂辉石质、硅藻土质、硅线石质、珍珠岩质、长石莫来石质、长石页岩质、煤矸石质、粉煤灰质、花岗岩尾矿质、钼尾矿质、铜尾矿质、锂尾矿质、铁尾矿质、赤泥-煤矸石质、沸石分子筛、硅酸盐玻璃质以及鹏硅酸盐玻璃质等等。按照材料晶相组成,有可分为:陶瓷质(陶质和瓷质)、玻璃陶瓷质(有时也叫微晶玻璃质)、玻璃质(也叫多孔玻璃)。多孔陶瓷也可以按照孔径和气孔形态分类,譬如按照气孔形态可以分为开孔型(以开口气孔占主体的多孔陶瓷)、闭孔型(以封闭气孔占主体的多孔陶瓷)和贯通气孔型(属于开口气孔多孔陶瓷中的特类);按照孔径可以分为宏孔(孔径>50nm )、介孔(孔径>1.5nm,<50nm )、微孔(
<1.5nm )。
多孔陶瓷的制备工艺过程也包括:
原料加工、配料,成型,干燥,烧成等,很大部分可以借鉴传统建筑陶瓷、日用陶瓷、卫生陶瓷、结构陶瓷、功能陶瓷的生产工艺,譬如成型方法,就有建筑陶瓷的干压成型法、卫生陶瓷的注浆成型法、陶板或石墨电极的挤出成型法、以及功能陶瓷中电子陶瓷的流延成型法、
压延成型法等。多孔陶瓷的造孔技术可以在原料及配方组成中、
也可以在成型、干燥、烧成和冷加工中。传统造孔技术有:颗粒堆积烧结法、添加造孔剂法、有机泡沫浸渍法、颗粒稳定泡沫法、发泡法、溶胶凝胶法和挤出成型法;新型造孔技术包括:薄膜沉积法、阳极氧化法、冷冻干燥法、相分离沥滤法、热分解法、
水热法、超临界干燥法、凝胶注模法、自蔓
延高温合成法、
增材制造法等等。
陶瓷产业固废有三个源头:一个是上游陶瓷原料、釉料开采、加工、生产、制造、包装、运输过程产生的各种固体废弃物;二是陶瓷企业生产、制造、包装、储存、运输过程产生的各种固体废弃物;
三是陶瓷产品在建筑工程中的安装、装修施工过程,以及建筑及陶瓷产品达到实用寿命的回收利用。陶瓷产业固体废料资源化生产多孔
陶瓷,已经引起陶瓷产业从业人员和环保科研人员的极大关注。这些研究为建筑陶瓷产品功能化、绿色化和固废资源化做出极大贡献。
一直以来陶瓷产业固废资源化利通常采用的途径有三个:
(1)作为坯料在陶瓷工业中循环利用;
在建筑陶瓷生产企业,由于废坯、废瓷等固体废料产量巨大,这些废料在工厂内循环利用是比较有效的。
(2)用于生产混凝土透水砖:采用陶瓷工业固体废物生产透水性材料(混凝土或砖)铺筑各种场地和路面,增大透水透气面积,可有效缓解城市不透水硬化地面对城市生态造成的负面影响,同时实现了固体废物的资源化利用。
(3)用于生产水泥及混凝土材料:
陶瓷抛光砖废料和废石膏代替部分原料配料可烧制出合格的硫硅酸盐水泥熟料。
利用陶瓷产业固废生产多孔陶瓷的研究更是方兴未艾,更为建筑陶瓷绿色发展和陶瓷产品功能化走出了一条新的途径。
韩复兴首次利用陶瓷废长石粉、
废粘土粉、废土粉、废瓷粉、废釉粉和粉煤灰,并添加少量焦煤粉和硝酸钾作为发泡剂,硼酸作为助泡剂。采用不锈钢模具或碳化硅模具装填法,
在辊道窑最高850℃生产出强度高、显气孔率高、体积密度低的宏孔多孔陶瓷材料,可以用于墙体隔音、吸声、保温和调湿,
亦可以用于固液分离[2]。发明专利CN105439548B 公布一种含有陶瓷抛光废渣的呼吸砖及制备方法,主要针对现有产品价格昂贵、制备方法复杂及陶瓷抛光废料污染环境的问题。本发明采用陶瓷抛光废渣30%~40%;硅藻土46.5%~57.5%;膨润土1%~3%;吉林土5%~7%;陶瓷坯体增强剂0.5%~1%;陶瓷助烧剂1%~2%;高效减水剂0.5%~1%;纳米二氧化钛0.5%~1.5%;电气石粉0.5%~1.5%。并加入适量的颜料和水,经制备浆料、
喷雾造粒、成型、烧成即得含有陶瓷抛光废渣的呼吸砖。呼吸砖是一种利用开孔型多孔陶瓷,它可以吸附空气中的水分和有害异味气体,具有减少特殊气味、
调节湿度、控制结露的功能。
专利CN102249694B 公开一种轻质陶瓷砖的生产方法,该方法采用陶瓷厂的固体废弃物和污水处理厂生产的污泥作为原料,废渣包括:抛光废渣、经破碎处理的废抛光砖、制坯回收的废坯粉和废泥粉、除尘器回收粉尘、陶瓷厂排水道淤泥、经破碎处理的抛光用废磨块、
废弃
釉料、煤烧结余物、废高岭土、废高温砂、污泥等,几乎涵盖所有固废。生产时将配合料、减水剂和增强剂在湿法球磨机内球磨、泥浆喷雾干燥、干压成型、余热干燥、釉线施釉、烧成发泡、磨边倒角,生产出体积密度在0.35~0.95g/cm3间、线膨胀率在8%~40%、断裂模数在34~0kgf/cm2、导热系数在0.0850~18W/m.k间,具有保温隔热、隔音吸声功能的闭孔型多孔陶瓷,而且综合利用了陶瓷厂的固体废弃物和污水处理厂生产的污泥,达到废弃物资源化的目的和实现建筑陶瓷特别是抛光砖厂固体废物零排放的目的。
近年来,国内关于陶瓷废料制备多孔陶瓷材料的研究方兴未艾,在过滤材料、吸声材料和保温材料等方面都取得了许多成果[3-8]
。
我国是一个缺水国家,全国669个城市中,400个城市常年供水不足,其中110个城市严重缺水,天津、长春、青岛等大中城市已受到水资源短缺的严重威胁。“十三五”以来,我国城镇化率及GDP保持快速增长,年总用水量已达6700亿立方米,2019年我国城镇污水排放量约750亿立方米,但再生水利用量不足100亿立方米,再生水利用量不足城镇污水排放量的15%,亟待加快推进。
《关于推进污水资源化利用的指导意见》提出“到2025年,全国地级及以上缺水城市再生水利用率达到25%以上,京津冀地区达到35%以上;到2035年,形成系统、安全、环保、经济的污水资源化利用格局”的总体目标。同时要求“具备条件的缺水地区对市政管网未覆盖的住宅小区、学校、企事业单位的生活污水进行达标处理后实现就近回用”。
目前,陶瓷产业工业和生活用水大部分不在市政管网覆盖区,尤其是生活用水,大部分来自地下水。工业园区地下水污染隐患多、用于生活用水风险大,而且地下水资源越来越匮乏,已经满足不了居民生活需求和可持续发展。
华东建筑设计研究院有限公司和南京化工大学采用分置式陶瓷微滤膜生物反应器(MBR)对居民生活污水进行了处理实验。原水进人具有较高活性污泥浓度(MLSS不大于20000mg/L)的活性污泥法生物反应装置进行生化处理,同时生化反应装置中的污水经泵加压循环流至无机陶瓷膜分离装置(氧化锆膜管,0.2μm,1m 长,7通,圆柱形膜管)。以1:60的出水、回流比进行分离,得到处理出水。实验原水水质主要指标:COD为
80~800mg/L,氨氮为2.8mg/L;出水相应指标:COD为5.9mg/L,氨氮为“无”。其它指标略,经过长期稳定性考察,实验出水均达到污水排放标准GB8978-88以及可以达到建设部生活杂用水标准CJ25.1-89,可以作为回用水回用[9]。
广西桂平碧清源环保投资有限公司在平板陶瓷膜污水处理领域应用方面,已有每天处理近十万吨的工程项目在运行。涉及领域包括工业废水、生活污水、农村城镇污水以及屠宰废水等行业。其中贺州市旺高工业区污水处理厂处理规模为2万t/d。该工程采用“水力澄清池+NCMT生化池”工艺,工程设计进水COD Cr≤500mg/L、悬浮物≤150mg/L、氨氮≤35mg/L、BOD≤150mg/L、总磷≤7m/L。2016年7月到2017年7月,区污水处理出水年COD Cr平均值18.54mg/L、悬浮物7.62mg/L、氨氮1.04mg/L、BOD53.51mg/L、总磷0.30m/L、总氮6.96mg/L,系统出水水质远优于《
城镇污水处理厂污染物排放标准》(GB18918-2002)中的一级A标准的排放标准要求[10]
。
水是人类赖以生存和发展的物质基础,饮用水安全则是影响人体健康和国计民生的重大问题。中国淡水资源总量约2.8万亿立方米,占全球水资源总量的6%,居世界第四,仅次于巴西、俄罗斯和加拿大。然而,中国的人均水资源量只有约2000立方米,只有世界平均水平的四分之一。中国幅员辽阔,地形多样,造成了水资源分布不均,被联合国列为13个缺水国家之一。水污染加剧了水资源的短缺。
2018年,水利部对31个省(直辖市、自治区)1045个集中式饮用水源地进行了评价,合格率为83.5%。即使是水资源相对丰富的华南地区,也面临着饮用水安全、水资源短缺问题。随着人口的增长和城市化进程的加快,居民对安全饮用水的需求也在不断增长。
近年来,主要应用于饮用水净化的多孔陶瓷膜技术包括微滤(MF)、超滤(UF)、纳滤(NF)和反渗透(RO)。相比传统的水处理技术,压力驱动膜过程更为高效、低耗。其中微滤(MF)技术主要用于去除水体中的悬浮物、细菌等大颗粒物质,在饮用水的预处理和初级阶段应用。超滤(UF)膜孔径较微滤(MF)膜小,对于普通的自然水源,经过超滤膜处理后可以达到饮用水标准。与MF和UF 相比,纳滤(NF)不仅可以保证饮用水的生物安全,同时对各类有机物有较高的截留性能,对无机离子可适度去除,能够满足更广泛水源需求。反渗透(RO)操作压力高、膜价格昂贵,主要用于海水、苦咸水淡化,但对于特殊水源的饮用水,常规多孔陶瓷膜难以达到饮用水标准,
反
渗透膜(RO)则是有效的深度处理技术[11]。
陶瓷产业工业园区大部分远离城市,生活用水大部分不在市政管网覆盖区,而工业园区由于地质条件和工业污染,几乎都无法直接应用,采用多孔陶瓷膜处理生活用水、
尤其是饮用水已经在一些工厂取得了显著成效。
建筑陶瓷工业是一个高污染、高能耗、高消耗的产业。目前,全国共有建筑陶瓷生产线2000多条,产量将近100亿平方米。现有的建筑陶瓷工业烟气排放口多而散,无组织排放现象严重,治理难度较大,行业不仅要面临激烈的竞争,还要面对节能减排的重任。
在我国陶瓷工业中,目前国内针对陶瓷烟气污染控制、除尘、脱硝技术已经成熟,但对NO X、氟化物、氯化物及重金属等污染物的控制技术研究和应用严重滞后或缺乏。对于建筑陶瓷生产而言,烟气的排放有两处:一是喷雾干燥塔的燃烧炉排放的烟气;二是陶瓷辊道窑燃烧后排放的烟气。
陶瓷喷雾塔烟气的主要污染物有粉尘、SO2和NO X。对于使用天然气的生产企业,其排放参数如下:烟气的排放温度:70~150℃,喷雾塔燃烧炉燃烧的温度:850~1100℃,粉尘初始浓度:2200~5600mg/Nm3;SO2初始浓度20~100mg/Nm3,NO X初始浓度:100~250mg/Nm3。采用钢仓旋风除尘和布袋除尘组合工艺,粉尘排放浓度可以达到<10mg/Nm3;采用石灰-石膏半干法或湿法脱
硫工艺,SO2排放浓度可以达到<20mg/Nm3;采用新型选择性非催化还原SNCR技术,NO X排放浓度可以达到<100mg/Nm3。满足修改版《陶瓷工业污染物排放标准》(GB25464),粉尘排放浓度可以达到<10mg/Nm3;SO2排放浓度可以达到<30mg/Nm3,NO X排放浓度可以达到<100mg/Nm3的要求,实现超低排放。
陶瓷窑炉或者干燥窑烟气的主要污染也是粉尘、SO2和NO X。对于使用天然气的生产企业,其排放参数如下:干燥烟气的排放温度:140~180℃,窑炉烟气的初始排放温度140~280℃,一般窑炉烟气二次利用用于干燥窑干燥或喷雾干燥塔掺冷风。窑炉或干燥烟气:粉尘初始浓度:40~200mg/Nm3;SO2初始浓度120~600mg//Nm3,NO X初始浓度:400~600mg/Nm3。采用布袋除尘工艺,粉尘排放浓度可以达到<10mg/Nm3;采用石灰-石膏半干法或湿法脱硫工艺,SO2排放浓度可以达到<5mg//Nm3;为了实现NO X的超低排放,只能研发新型选择性催化还原(SCR)烟气脱硝系统,由于很多使用效果优异的催化剂最佳的工作温度在300℃以上,因此在后段工序还需将除尘后的烟气进行升温,这又消耗很多能源。也只有这样才能将NO X排放浓度控制在<75mg/Nm3。从而满足修改版《陶瓷工业污染物排放标准》(GB25464),粉尘排放浓度可以达到<10mg/Nm3;SO2排放浓度可以达到<30mg/Nm3,NO X排放浓度可以达到<100mg/Nm3的要求,实现超低排放。
目前SCR陶瓷催化剂有蜂窝式、波纹式、平板式三种,多孔陶瓷载体材料主要有(氧化铝、氧化钛、堇青石、钙钛矿等)和活性V2O5、WO3、MoO3、MnO2等组分及掺杂成分Fe2O3、CeO2等。生产
时蜂窝式催化剂一般将载体材料与活性成分及掺杂成分一起混练、挤出成型、高温烧结成陶瓷催化剂,波纹式和平板式则采用在多孔陶瓷载体上涂覆无机催化膜。清华大学环境科学与工程学院、中国科学院过程研究所和南京工业大学是多孔陶瓷催化膜研究的佼佼者,生产企业有大唐南京环保科技有限公司、天河(保定)环境工程有限公司、郑州康宁特环保集团、浙江海亮环境材料有限公司、山东天璨环保科技有限公司、江苏万德环保科技有限公司、启源(西安)大荣环保科技有限公司等。
武汉理工大学何峰等以偏高岭土、氧化铝和滑石为原料,利用压制成型制备出堇青石多孔陶瓷并采用浸渍涂覆法制备锰基低温脱硝催化剂。通过气孔率、抗折强度、热膨胀系数、SEM、BET等测试探究了碳粉和淀粉两种造孔剂及添加量、不同酸处理时间等因素对堇青石性能的影响并考察了不同浸渍次数的催化剂在80~200℃间的脱硝性能。结果表明:造孔剂为碳粉且添加量为4%时,得到的堇青石具有良好的性能,此时气孔率达31.12%,热膨胀系数为3.10×10-6/K,抗折强度为21.41 M Pa;适当的酸处理有助于堇青石表面孔结构的丰富且能大幅提升其比表面积,最佳处理时间为2h;当浸渍次数为4次时,整体式催化剂的性能最佳,牢固度可达90.18%,140℃时的脱硝率可达74.5%以上
[12]
。
VOC即挥发性有机化合物,对人体健康有巨大影响。当居室中的VOC达到一定浓度时,短时间内人们会感到头痛、恶心、呕吐、乏力等,严重时会出现抽搐、昏迷,并会伤害到人的肝脏、肾脏、大脑和神经系统,造成记忆力减退等严重后果。陶瓷生产工艺过程存在多个VOC s排放环节。建筑陶瓷企业大部分建有喷墨打印线,所用的陶瓷墨水含有表面活性剂和有机溶剂,在使用过程中会排放VOC s。日用陶瓷生产的烤花工序,贴花纸中的PVC成分烧失会排放VOC s。特种陶瓷生产的排蜡、
排塑工序,使用有机溶剂(石蜡、桐油等)也存在VOC s排放问题。《排污许可证申请与核发技术规范陶瓷砖瓦工业》(HJ954-2018)将施釉工序、其他通风设备排气筒定义为一般排放口,其污染物为颗粒物,未规定VOC s的排放要求,对烤花等工序也未规定VOC s的排放要求。对于喷墨打印、烤花、排蜡等工序,企业一般会进行废气收集并设置了除尘等系统,但大部分未考虑VOC s的预防和治理,仅少数VOC s排放浓度高的企业采用水洗、UV光解等简单治理工艺,效果较差。
去除陶瓷产业VOC s的传统方法是活性炭吸附+催化燃烧法,原理是利用活性炭的多孔吸附性吸附VOC s,当吸附饱和后,通过热气流将原来已经吸附在活性炭孔洞中的VOC s脱附出来,并经过催化燃烧反应转化成二氧化碳和水蒸气等无害物质。活性炭有很好的孔径分布,价格也便宜,但是却存在不耐高温缺点、尤其是当存在酮类物质时极易燃烧,而且当空气湿度较大时,也严重影响活性炭的吸附性,低温催化燃烧成本也较高。
刘月颖研究了陶瓷基瓦楞纸片及块体、陶瓷基分子筛瓦楞纸片的制备。在制备过程中,探讨了润湿剂、干燥方式和分子筛质量分数对陶瓷基纸片及陶瓷基分子筛块体的影响。最终优化条件为,采用0.15%wt的OP-10润湿陶瓷基瓦楞纸,微波干燥,分子筛质量分数不高于23.08%[13]。
开展多孔陶瓷基沸石分子筛膜VOC s吸附材料,平板式或波纹式多孔陶瓷基沸石分子筛膜和分子筛转轮研究,应用新型多孔陶瓷材料去除VOC s将进一步促进
陶瓷产业绿色发展。
2021年12月24日,全国人大常委会会议表决通过了噪声污染防治法,并于2022年6月5日起施行。噪声污染防治法规定:任何单位和个人都有保护声环境的义务,同时依法享有获取噪声环境信息、参与
和监督噪声污染防治的权利。噪声污染防治法还规定:排放工业噪声的企业事业单位和其他生产经营者,应当采取有效措施,减少振动、降低噪声,依法取得排污许可证或者填报排污登记表。实行排污许可管理的单位,不得无排污许可证排放工业噪声,并应当按照排污许可证的要求进行噪声污染防治。同时又规定:实行排污许可管理的单位应当按照规定,对工业噪声开展自行监测,保存原始监测记录,向社会公开监测结果,对监测数据的真实性和准确性负责。噪声重点排污单位应当按照国家规定,安装、使用、维护噪声自动监测设备,与生态环境主管部门的监控设备联网。
陶瓷产业噪声污染源主要为:原料破碎机、原料球磨机、泥浆搅拌机,喷雾干燥塔物流输送带、抽湿排烟风机、鼓风机,压机成型及布料,窑炉鼓风机、窑炉及干燥窑抽湿排烟风机,磨边机、抛光机,建筑鼓风机、排风机,空压机等。采用静音电机或低噪音风机,对污染源进行隔离,设置消声器、隔音吸声罩、隔音吸声室等措施,采用智能远程操作系统,让操作人员在污染源隔离室外工作,对不得不进入隔离室工作人员做好必要的劳动防护,譬如佩戴保护听力耳塞等措施。
多孔陶瓷吸声材料包括多孔吸音板、吸音砖、吸音管以及园柱形、六棱形、瓦板形等多孔吸音体。吸声结构包括吸声屏、吸声壁以及吊挂吸声结构等。主要用在以下三方面:1)用于高噪声的建筑物内,如锻打车间、冲压车间、铆焊车间、鼓风机房、空压机站等场所作吸声减噪处理;2)用于播音室、电话室、会议室、礼堂等室内消除杂音,改善音质。3)用作阻性消声器的声阻材料和双层隔音壁之间的填充材料,如各类风机消声器内衬和中间通道吸声层。
多孔陶瓷的吸声机理与吸声特性是:多孔陶瓷为高温烧结的颗粒状多孔材料,微孔是以骨料颗粒堆积构成的间隙,有机物燃尽,各种盐类分解和熔蚀等方法形成的。既有互相连通而交错的全开口气孔,又有类似腔室结构的半开口气孔,为孔穴结构。所以它的吸声机理也包括两部分:其一,它和矿棉、玻璃棉、毛毡、木纸板等纤维状多孔材料一样,直接通过微孔管壁的摩擦和空气的粘滞作用将声能转换为热能耗散掉,这部分主要吸收高频声。其二,类似于微孔共振结构,基于著名声学家马大献教授提出的微孔共振理论,当入射声波的频率与微孔中固有振动频率发生贯振时,消耗声能量最大,吸声系数最高[14]。
开孔型多孔陶瓷吸声性能与显气孔率、孔密度、平均孔径、
孔道长度及厚度有关,显气孔率和孔密度越高、平均孔径越小、孔道长度越长和产品越厚,
吸声效果越好。目前多孔陶瓷吸声产品生产厂家不多,在陶瓷工业的应用仍需要探索,但是作为无机防火防水材料,
其优点越来越来突出,相信不久的将来,会在陶瓷生产中普遍应用。
在陶瓷工业“绿色、节能、环保、低碳”发展方面,多孔陶瓷未来必将不局限于饮用水净化、污水处理、烟气脱硫脱硝、吸声隔声、VOC s的吸附、
浓缩和去除中发挥
更多推荐
陶瓷,排放,生产
发布评论