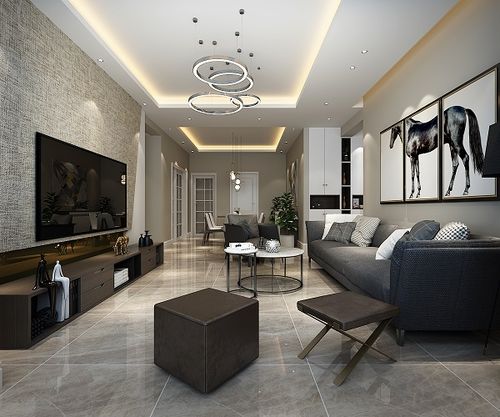
⽔性涂料喷涂⼯艺及设备设计需注意的问题
1、引⾔
随着涂料⼯业的发展,涂料的花⾊、品种、功能越来越多,分⼯也越来越细。但在涂料的制造和施⼯过程中因有机溶剂的⼤量排放⽽对环境造成巨⼤的污染。为限制有机溶剂的排放,涂料的⾼固体化、⽆溶剂化、⽔性化已呈⽇趋壮⼤之势,业内⼈⼠⼴泛赞同的“4E”涂料(Economy,Efficiency,Ecology,Energy)即指上述涂料。其中,涂料的⽔性化是近年来发展⼗分迅速的⼀个领域,但由于⽔性涂料与溶剂型涂料相⽐,存在诸多不同:⽔性涂料以⽔为稀释剂,溶剂型涂料以甲苯、⼆甲苯、醋酸丁酯等有机溶剂为稀释剂;在进⾏喷涂⼯艺及设备设计时,需要充分了解⽔性涂料的特点,根据其特点才能设计出科学合理的喷涂⼯艺及设备。
2、⽔性涂料的特点
⽔性涂料与溶剂型涂料相⽐具有低挥发速率、⾼表⾯张⼒、⾼导电性、腐蚀性以及易产⽣⽓泡的特点,导致⽔性涂料在施⼯设备和⼯艺⽅⾯与溶剂型涂料相⽐有所不同。⽔性涂料使⽤的主要溶剂⽔与溶剂型涂料使⽤的⼀些常⽤溶剂的特性⽐较见表1。
表1⽔与常⽤溶剂主要特性对⽐
⽔性涂料中⽔的挥发主要是通过喷漆室的温湿度来进⾏控制的,⽽溶剂型涂料可以通过调整稀释剂的挥发速率来调整施⼯固体含量。⽔性⾊漆的施⼯固体含量通常为20%~30%,⽽溶剂型⾊漆的施⼯固体含量⾼达60%~70%,因此⽔性⾊漆的平滑性较好。涂料流变性的控制技术是⽔性涂料的设计关键,⽔性⾊漆的流变特性如图1所⽰。
图1 ⽔性⾊漆的流变特性
当⽔性涂料喷涂时,在⾼剪切⼒的状态下,⽔性涂料的黏度迅速下降,保证涂料具有良好的微粒化效果;当剪切⼒消除后,迅速恢复⾼黏度状态,从⽽保证了⾦属颜料良好的定向效果以及抗流挂性能。⽔性涂料与溶剂型涂料相⽐最⼤的优点是VOC排放量低。不同⼯艺体系的VOC排放量见表2。⽬前欧洲采⽤“⽔性中涂+⽔性⾊漆+双组分罩光清漆”的⼯艺体系较为普遍,从⽽满⾜了欧洲对VOC排放的标准要求。
表2 不同涂装⼯艺体系的VOC排放量对⽐
3、⽔性涂料的⼯艺及设备设计需要注意的⼀些问题
⽔性涂料涂装⼯序与溶剂型涂料基本相同,但在设备选⽤材料和⼯艺参数设定上需根据⽔性涂料的特性进⾏选取,其典型⼯艺为:
前处理[上线→预脱脂→脱脂→⽔洗1→⽔洗2→(去离⼦⽔洗1)→(表调)→(磷化)→⽔洗3→⽔洗4→(去离⼦⽔洗2)→⼈⼯吹⽔→烘⼲]→强冷→喷底漆→流平→闪⼲→烘⼲→冷却(强冷)→喷⾯漆→流平→闪⼲→烘⼲→冷却(强冷)→下线
3.1 前处理
各类材料或制品在涂漆以前对其清除各类污物、整平及覆盖某类化学转化膜的所有准备⼯作,统称漆前表⾯处理。漆前表⾯处理技术是涂装技术的重要组成部分,在整个⼯艺过程中,需要选⽤清洗剂、表⾯调整剂、磷化剂、钝化剂、氧化剂等多种精细化⼯产品,这些化⼯产品组成复杂、性能差异⼤,如果选⽤不当或在使⽤中各槽液得不到很好的控制和管理,反⽽对涂层质量产⽣不利影响。由于⽔性涂料以⽔作为稀释剂,⽔的表⾯张⼒为72.6dyn/cm,要⽐⼀般有机溶剂⼤,是涂料常⽤有机溶剂的2.5倍(见表3),因⽽难以浸润底材,易产⽣缩孔,所以⼀⽅⾯通过在⽔性涂料⽣产配⽅中添加表⾯活性剂来降低表⾯张⼒,提⾼浸润性能,另⼀⽅⾯,在进⾏⼯件的前处理时,对⼯件表⾯处理的质量要求更⾼。
表3 涂料常⽤有机溶剂的表⾯张⼒
表3 涂料常⽤有机溶剂的表⾯张⼒
3.1.1 除油
钢铁表⾯除油程度要严格按照GB/T13312—1991的要求进⾏检查和控制。本⽅法是⽤标准G型极性溶液滴2滴
(0.1mL)在被试表⾯上,⽴即⽤玻璃棒涂成20mm×40mm的覆盖⾯积,将特制的A型验油试纸紧贴在溶液膜上,1min 后观察变⾊情况。若A型验油试纸显⾊均匀、连续完整,即为合格,反之不合格。⽆论对溶剂型涂料还是⽔性涂料,除油质量的好坏,对产品涂膜的质量都会产⽣较⼤的影响,但对于溶剂型涂料喷涂来说,⼯件表⾯除油不太彻底时,涂膜外观缺陷不会⽴即表现出来,但对⽔性涂料来说,⼯件表⾯除油不彻底,在其表⾯就难以形成完整的涂膜,所以,对⽔性涂料喷涂来说,前处理质量显得更为重要。
3.1.2 磷化
磷化膜的检验要严格按GB6807—1986进⾏,可采⽤3%氯化钠⽔溶液于15~25℃浸渍,或硫酸铜溶液点滴。也可以涂漆以后进⾏盐雾试验来考核。硫酸铜点滴液配⽅如下:CuSO4·5H2O为41g/L,NaCl为35g/L,0.1mol/L的HCl为
13mL/L。⽔性涂料对磷化膜的要求与溶剂型涂料基本相同,磷化膜必须均匀完整,细密⽆挂灰。
3.2 强冷
⽔的蒸发潜热为2457.22kJ/kg,⽽涂装常⽤溶剂的蒸发潜热:⼆甲苯为343.2kJ/kg,丁醇为590.2kJ/kg,酮类为343~444kJ/kg,都要⽐⽔低得多,所以喷涂同样厚度的涂料对⼯件的降温作⽤⽔性涂料更⼤⼀些,因此认为对于拖拉机底盘、柴油机等主要由铸件构成、涂层以防腐为主、对涂装表⾯装饰要求不⾼的⼯件,可以不设强冷。
3.3喷(底、⾯)漆
喷涂⽔性涂料所⽤的⼀般空⽓喷枪与溶剂型涂料相同,但对环境条件(主要是温度、湿度)的要求与溶剂型涂料相⽐存在⼀定的差别。在喷漆室中喷涂⽔性涂料时,⽔变成⽔蒸⽓体积膨胀1244倍,可以使喷漆室中的湿度瞬间升⾼,当湿度达到90%以上时涂在被涂物上的涂膜会流淌下来。所以,喷涂⽔性涂料时控制喷漆室的湿度很重要,温度也要保持在不产⽣流挂和流淌的范围,⼀般认为,温度在15~30℃,相对湿度在60%~80%较为适宜。由于⽔的腐蚀性⽐溶剂⼤,喷漆室尤其是循环⽔处理系统最好采⽤不锈钢制成。喷漆室内的送风必须有适当的调温调湿装置。国内汽车涂装喷漆室冬天都可以调温调湿,夏天却很少有调温调湿的,因为需要的制冷量太⼤,所以很少有送冷风的。因此在⾼温⾼湿地区,如果使⽤⽔性涂料,必须在喷漆室安装中央空调,夏季也需要送冷风,这样才能保证⽔性涂料的施⼯质量。⽔性涂料和溶剂型涂料的喷涂环境条件见图2。
图 2 ⽔性涂料和溶剂型涂料的喷涂环境条件
3.4 闪⼲
闪⼲即涂装后漆膜的流平和溶剂(包括⽔)的预蒸发过程,其⽬的是为了防⽌含有⼤量溶剂或⽔分的湿漆膜(⽔性底⾊漆中⽔的含量约为63%)突然进⼊较⾼温度(>100℃)的烘⼲炉。是否设置闪⼲⼯序,闪⼲时间和温度的具体参数要根据所使⽤的⽔性涂料的性能、对⼯件涂层的质量要求和烘⼲炉要求的温度来确定。⼀般情况下,湿碰湿⼯艺、烘炉烘⼲温度较⾼(⼀般在100℃以上,⾼于⽔的沸点温度)、对漆膜光泽和外观要求较⾼时,应该设置闪⼲⼯序。闪⼲时间的确定,对⽣产线⽽⾔,闪⼲时间主要受链速影响。闪⼲时间短,涂层内⽔分和溶剂没有及时挥发出来导致经⾼温烘烤后出现针孔、痱⼦等缺陷;闪⼲时间长,漆膜表⾯过⼲,涂层容易产⽣橘⽪等缺陷。要合理选择闪⼲时间,但同时需增加加热闪⼲区,否则容易出现流挂、⽓泡等质量问题。
3.5 烘⼲
同喷漆室的设计原则类似,烘⼲室中由于空⽓中⽔分含量较⾼也会对设备造成腐蚀,所以烘房内壁也需采⽤不锈钢制造。同时,⽔性涂料中稀释剂的主体是⽔,⽔的挥发与喷漆室的温湿度有较⼤关系。当湿度⼀定时,随着温度的升⾼,⽔的挥发速率增加;当温度⼀定时,则湿度增加,⽔的挥发受阻;当相对湿度过⼤时,⽔分挥发很慢,施⼯过程中易产⽣流挂等漆膜缺陷。由于⽔的蒸发潜热⼤(见表1),是⼀般溶剂的5~7倍,烘⼲室的热容量要适度增⼤。同时,⽔较有机溶剂蒸发慢,致使⽔性涂
料的烘⼲时间要长,涂膜和被涂物升温不宜过快。在⽔性涂料中除⽤电泳涂装法所得涂膜,受电渗作⽤使湿涂膜中的含⽔量很少,可直接经受⾼温烘烤外,其它含⽔量较⾼的⽔性涂料涂膜都要靠晾⼲和分段升温(在100℃以下保温⼀段时间),使涂膜中的⽔分基本蒸发掉,才升⾄⼯艺温度烘⼲,不然会由于⽔分在100℃时激烈沸腾⽽产⽣漆膜弊病。⽔性中涂、⾯漆和溶剂型中涂、⾯漆的典型热对流加热的烘⼲温度、时间变化曲线见图3和图4。都有这样的经验,在室外风⼝晾晒⾐服⼲得快,反之,通风不良⼲得慢或不能⼲燥,空⽓的相对湿度⼤了,也⼲得慢。这也是⽔性涂料⼲燥的原则。因⽽在晾⼲及烘⼲室中控制空⽓的湿度对烘⼲时间及效果⾮常重要。
得慢。这也是⽔性涂料⼲燥的原则。因⽽在晾⼲及烘⼲室中控制空⽓的湿度对烘⼲时间及效果⾮常重要。
图3 ⽔性涂料中涂、⾯漆的固化(烘⼲)曲线
图4 溶剂型中涂、⾯漆的固化(烘⼲)曲线
3.6 ⾃动喷涂系统
⽔性涂料的主要溶剂是⽔,具有⾼导电性,如果采⽤溶剂型涂料通常使⽤的内部加电式旋杯(见图5),⾼压静电会从输漆系统泄漏出去,因此⽔性涂料在应⽤初期⼀般使⽤外部加电式旋杯(见图6)。
图5 内部加电式旋杯
图 6 外部加电式旋杯
但由于外部加电式旋杯系统中外置的加电⼿指容易积油漆,导致清洁频次增加;同时⼿指对旋杯移动速度和环境湿度较为敏感,会造成油漆利⽤率降低8%~13%,影响油漆外观质量。随着技术的发展,⽬前内部加电式旋杯已开始在⽔性涂料喷涂线上使⽤,在喷涂开始前,油漆从调漆桶吸到储存器,然后与主循环回路断开。这样可防⽌⾼压静电漏到调漆间去,影响⽣产和造成危险。
3.7 输调漆系统
溶剂型涂料的输调漆系统可采⽤碳钢制成,⽽⽔性涂料由于⽔会使⾦属⽣锈⽽腐蚀,因此⽔性涂料的输调漆系统必须使⽤不锈钢材料。相对溶剂型⾊漆⽽⾔,⽔性⾊漆的输调漆系统更需注重低剪切应⼒控制、稳定的流量以及避免⾼压系统,⾼剪切⼒、⾼流量及⾼压⼒均会使⽔性⾊漆加速⽼化,直接影响喷涂质量,如输调漆系统的回压阀和搅拌桨必须采⽤低剪切⼒类型,否则将破坏⽔性树脂的乳化性能;溶剂型⾊漆在循环系统中的流速要求为0.3~0.7m/s,⽽⽔性⾊漆的流速则要求为0.15~0.40m/s。
4、消防及环保问题
4.1 消防问题
⽔性涂料为不燃物质,溶剂含量占10%~12%以下,不含苯、⼆甲苯等,故在设置消防设施时⾃动灭⽕消防设施和可燃⽓体报警装置原则上可不⽤考虑。在喷漆室旁放置⼀般的灭⽕器即可。但⽔性涂料的基料树脂仍为可燃物质,积漆⼲燥后仍存在着⽕的可能,所以对喷漆室、通风管道等设备设施内的积漆也要及时清除,以防积漆燃烧,发⽣⽕灾。对于⽔性涂料消防设施技术条件及废⽓处理的设备设计要求,⽬前还没有国家标准,建议国家或⾏业尽快制定相应的标准。
4.2 环保问题
使⽤⽔性涂料后,环保法规中(VOC)废⽓排放要求⽆需增加设备便可达标。但产⽣的废⽔需进⾏多级处理,使COD 达到排放要求后进⾏排放。
5、⽔性涂料的经济性
同样性能的⽔性涂料,单价⽐溶剂型涂料要⾼⼀些,但不会太⾼。以某品牌⿊⾊丙烯酸磁漆为例,与某⽔性涂料性能对⽐见表4。
表 4 某品牌⿊⾊丙烯酸磁漆与某⽔溶性丙烯酸⾯漆性能⽐较
⿊⾊丙烯酸磁漆的单价为18元/kg,溶剂单价为10元/kg,⽽某⽔性⾯漆的单价为25元/kg,以⽔作溶剂,
费⽤可忽略不计。
某⼯件油漆消耗量为:3~4kg,取4kg溶剂(稀释及清洗)消耗量为:4kg×1/3=1.33kg
油漆成本为4kg×18元/kg+1.33kg×10元/kg=85元/件
⽔性涂料成本为:4kg×25元/kg=100元/件
⽔性涂料喷漆室、流平室及烘⼲室所⽤材质最好为不锈钢,以防⽌施⼯过程中湿度⼤造成设备腐蚀,设备成本较溶剂型涂料设备成本可增加10%左右。若国家或⾏业能够颁布⽔性涂料的消防及环保设施和设备标准,⽤普通消防设施取代⾃动灭⽕系统,⽔性涂料喷涂线上不设置可燃⽓体报警装置和废⽓处理装置,则可减少设备投资50万元以上。综上所述,⽔性涂料与溶剂型涂料在使⽤、材料成本和设备投资⽅⾯两者相⽐,前者略⾼于后者,但若⽔性涂料不考虑⾃动灭⽕系统、可燃⽓体报警装置和废⽓处理装置,则两者设备投资基本相当。同时,⽔性涂料具有可回收性,根据⼯件的特点,⼀般可回收10%~30%,如果再把环保费⽤、⼯⼈操作环境⼤⼤改善、职业病减少等综合因素计算在内,前者使⽤、材料成本还要低于后者,所以⽔性涂料⽆论从经济效益还是从社会效益考虑,都是完全值得推⼴应⽤的。
表5 ⽔性涂料与溶剂型涂料成本⽐较
6、结语
溶剂型涂料和⽔性涂料的根本区别在于:溶剂型涂料使⽤了有毒、有污染、可燃烧的有机溶剂作为稀释剂,⽽⽔性涂料主要使⽤⾃来⽔作为稀释剂。尽管⽔性涂料的性能还需要完善,但代替溶剂型涂料应该是⼤势所趋。⽔性涂料普及的条件已经成熟,在未来⼏年,⽔性涂料⼤有全⾯代替溶剂型涂料之势。进⾏⽔性涂料施⼯⼯艺的研究⼗分重要,本⽂就⽔性涂料在进⾏喷涂⼯艺及设备设计时需注意的⼀些问题进⾏了简要论述,其观点是在进⾏⽔性涂料喷涂⼯艺设计时,对⼀些⽔性涂料使⽤和⽣产单位及⼀些相关技术资料的总结,供同⾏们在进⾏相关设计时参考。
更多推荐
涂料,溶剂型,系统,设备,要求,溶剂,喷漆,涂膜
发布评论