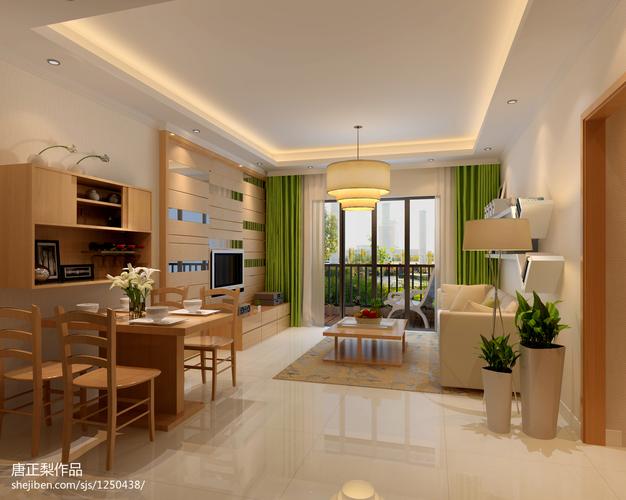
水泥生产的质量控制与管理
作者:-E3
生产中的质量管理,包括从原料进厂,一直到成品出厂以前整个生产过程 中的质量把关和质量控制工作。生产质量控制是生产质量管理不可缺少的一个重 要环节。它的作用是根据设计和工艺技术文件的规定, 控制生产过程各工序可能
出现的异常和波动,使生产处于可控状态。生产过程的质量控制目的是产品性能 质量控制,使产品达到所需性能的满足程度,保证生产出符合设计和规范质量要 求的产品,如水泥的凝结时间、强度和强度等级等。
生产工艺是连续性很强的过程,无论哪一道工序保证不了质量都将影响 产品的质量。在生产过程中原燃材料的成分及生产情况经常变动。因此必须经常 地、系统地、科学地对各生产工序按照工艺要求一环扣一环地进行严格的质量控 制,合理地选择质量控制点,采用正确的质量控制方法,把质量控制工作贯穿于 生产的全过程。
一、 原燃材料的质量控制与管理
原料的质量是制备成分合适而稳定的生料的基础条件
(一) 石灰石的质量控制
石灰石是使用最广泛的石灰质原料。其主要成分为 CaC03品位主要由 CaO含量确定。用于水泥生产的石灰石 CaO含量并非越高越好,还要看其酸性氧 化物的含量,如Si02、AI2O3、Fe2O3等是否满足配料要求。有害成分如 MgO R 20游离SiO2等也要控制。
sonocc有自己的矿山,石灰石在矿山破碎后进厂直接进破碎机破碎并 储入碎石库或进预均化堆场。
石灰石一批进行一次CaO测定或做全分析
(二) 粘土质原料的质量控制
熟料的质量控制与管理
黄土和粘土使用最广泛。其主要成分是 SiO2、AI2O3和Fe2O3衡量粘 土的质量主要看粘土的化学成分 (硅酸率、铝氧率)、含砂量、含碱量、可塑性、 需水性等工艺性质,生产
方法不同,对粘土质量要求也不尽相同
进厂后的料应分堆存放,先化验后使用。存放时平铺直取,尽量均化。
进厂粘土质原料应按时取样,每批进行一次全分析。
(三) 校正原料的质量控制
二、 石膏的质量控制
用作水泥缓凝剂的石膏主要是石膏(CaSO4 2H2O和硬石膏(CaSO4。按矿物 组成有可分为三类产品:
G类石膏:以CaSO4 2H2O的质量百分含量表示其品位
A类硬石膏:以CaSO4 2H2O+CaSO的质量百分含量表示其品位,且 CaSO4/(C aSO4・ 2H2O+CaSO4> 0.80
M类混合石膏:以CaSO4 2H2O+CaSO的质量百分含量表示其品位,且 CaSO4/
/
CaSO4 2H2O+CaSO4W 0.80
石膏进厂一批取样化验一次,基本分析检验项目有:附着水、结晶水、三氧化硫 含量
三、 生料的质量控制与管理
(一) 、生料制备过程中的质量要求
生料制备过程是将原料按比例混合,经过一系列加工之后,制成具有一定细度, 适当化学成分,均匀的生料,以满足煅烧的要求。
生料制备过程的质量控制项目有:
1、 入磨物料的配比:
2、 入磨物料的粒度:与磨机类型、规格有关,一般 25~30mn左右
3、 入磨物料的水分:与磨机类型有关 一般:干法球磨机w 1.0%~2.0%
烘干兼粉磨系统w 6.0%
(二) 、出磨生料控制项目
1、 化学成分:
生料的化学成分是通过化学分析来测量的。但由于人工做全分析所需时 间较长,分析结果反馈较慢,不便于及时指导生产。生产中往往采用一些简单、 快速的检验方法控制生料的质量。
一般:若采用人工分析,控制项目有:碳酸钙滴定值(或氧化钙)、氧 化铁
若采用仪器分析,则要看仪器性能。如采用的是钙铁分析仪,控制项目 同上;如采用多元素分析仪,可快速做全分析,则可以率值作控制项目。 一般控制指标:
TCaCO3:目标值土 0.5%,合格率》60%
CaO 目标值土 0.5%,合格率》60% 每1h测定一次
Fe2O3 目标值土 0.2%,合格率》80% 每2h测定一次
KH 目标值土 0.01~0.02
SM目标值土 0.1
IM :目标值土 0.1
2、 生料的细度:
细度影响窑内物料反应速度,进而影响熟料的产、质量及消耗。越细越 好。但过细会影响磨机产量和电耗。因此要确定合理的细度。
合理的生料细度要考虑:
(1) 一定范围的平均细度。以0.08mm方孔筛筛余表示
(2) 细度的均齐性。应尽量避免粗颗粒。以 0.2mm方孔筛筛余表示
一般控制指标:0.2mm方孔筛筛余V 1.5%; 0.08mm方孔筛筛余w目标值,合格率 > 87.5%,分磨1h测定一次。
(三) 、入窑生料的质量控制
生料出磨后进入生料均化库,对生料进行储存和均化,经过调配均化后 入窑。
对入窑生料的质量控制项目主要是化学成分, 如配有多元素分析仪,可 作入窑生料的全分析,以率值作控制指标,控制其合格率,以检验均化效果。一 般控制指标及检验频次同出磨生料,只是合格率控制指标提高
四、 熟料的质量控制与管理
熟料质量是影响水泥质量最重要的因素。 熟料的质量控制是水泥企业最 重要的工作之一。熟料质量控制,不同的生产工艺略有不同。
回转窑生产:除常规化学全分析、物理检验和控制游离氧化钙外,还要 控制烧成带温度、窑尾温度及各处负压,控制熟料的容积密度,有的厂还做岩相 结构分析和检验;
一般熟料质量控制项目有:熟料化学分析(包括 KH SM IM)烧失量、 游离氧化钙、氧化镁、安定性、强度等。
(一)、控制项目
1、 熟料的化学成分
控制目的:检验其化学成分和矿物组成是否符合配料设计的要求, 从而
判断前面工艺的状况和熟料质量,并作为调整前一工艺的依据。
控制目标:熟料中各氧化物之间的不同比例即率值, 决定着熟料中各氧 化物的含量,并直接影响熟料煅烧的难易程度及质量。 一般通过三个率值来表示 熟料中各氧化物含量之间的关系。控制范围如下:
KH 目标值土 0.01~0.02
合格率:湿法及日产2000t/d以上的预分解窑》80%
其他窑型〉70%
标准偏差:旋窑w 0.020 ;
立窑w 0.030
SM IM:目标值土 0.1 合格率》85%
检验频次:化学成分的测定应进行连续取样,使试样具有代表性,每天测定至少 一次。以上控制指标一个月统计一次。
2、 游离氧化钙(f-CaO):
控制目的:
游离氧化钙是熟料中没有参加化学反应而以游离状态存在的氧化钙。 因 其水化很慢易造成水泥安定性不良。 控制熟料中游离氧化钙的含量十分必要。 可 以对煅烧情况和熟料质量进行判断。
理论上讲,熟料中f-CaO越低越好,因其含量增加,熟料强度下降,安 定性合格率下降。确定其控制指标时应综合考虑生产工艺、原燃材料、设备、操 作水平等因素,确定一个既经济又合理的指标。
在生产中造成f-CaO含量高的原因有:
配料不当,KH过高;
煤与生料配比不均匀、不准确,煤质波动大或煤粒过粗;
入窑生料TCaCO合格率太低或生料过粗,窑内煅烧不完全;
热工制度不稳,卸料太快或偏火漏生;
熟料冷却慢,产生二次f-CaO。
如熟料出窑时f-CaO含量过高,安定性不合格,可采取以下措施减少f-CaO对强 度和安定性的影响:
熟料出窑时喷洒少量水;
加入少量的高活性混合材料制备水泥;
调整水泥的粉磨细度;
适当延长熟料的堆放时间;
和质量好的熟料搭配使用。
控制指标:
旋窑f-CaOw 1.5%,合格率》85%检验次数自定;
3、 熟料中氧化镁
控制目的:熟料中氧化镁为有害成分,含量过高会影响水泥安定性。
控制指标:国家标准规定,水泥熟料中 MgC须V 5.0%,若在5.0%~6.0% 时,要进行压蒸安定性检验。如压蒸安定性合格,则熟料中MgO含量可放宽到6. 0%
测定频次:每天至少测定一次,若 MgO含量较高,应增加测定次数。
4、熟料的立升重(容积密度)
控制目的:熟料的立升重即一立升熟料的质量, 其高低是判断熟料质量 和窑内温度(主要是烧成带温度)的参数之一,通过物料结粒大小及均匀程度, 可以推测烧成温度是否正常。
当窑温正常时,产量高,熟料颗粒大小均齐,外观 紧密结实,表面较光滑而近似小圆球状,立升重较高;物料在烧成带温度过高或 在烧成带停留时间太长,过烧料多,熟料立升重过高,熟料质量反而不好。如窑 内物料化学反应不完全,熟料颗粒小的多,而且其中还带有细粉,立升重就低, 说明窑内温度低。因此立升重应控制在一定范围之内。一般回转窑 1300~1500g/
L,立窑 850~1000g/L
控制指标:目标值土 75 g/L,最好土 50g/L以内。
测定频次:分窑1h测定一次
测定方法:
工具和仪器:孔径5mn和7mm筛子各两个;
容量为半立升的铁制圆筒两个;
磅秤一台;
留样筒两个(容量约为10kg)
操作步骤:将7mn筛放在5mn筛之上,打开取样器闸板,放取熟料。然 后将闸板关闭,筛动7mn筛中的熟料,使小于7mm勺熟料通过筛孔漏入5mn筛内。 将大于7mm勺熟料倒掉,在筛动5mm的筛子,直至每分钟通过5mm筛子的熟料不 超过50g为止。将留于5mm筛子之上的熟料倒入升重筒内,用铁尺将多出筒口的 熟料刮掉,使其与升重筒面水平,然后称量。
熟料立升重按下式计算: 立升重=(总重-皮重)X 2 g/L
5 、熟料的烧失量
控制目的:烧失量是衡量熟料质量好坏的重要指标之一。 烧失量高,说
明窑内物料反应不完全,还有部分 CaCO没有分解或煤粒未燃烧,或部分 CaCO3 虽已分解,但来不及继续完成熟料的化学反应。
控制目标:w 1.5%
测定频次:每窑每班测一次。
&熟料的物理性能
控制目的:熟料的物理性能主要指凝结时间、 安定性、强度、外观特征等。 测定作用是验证配料方案;检查窑内煅烧操作情况;作为水泥制成质量控制的依 据。
检验频次:分窑每天检验一次,取平均样。
注意:强度检验,须使用平均样,从取样到成型不得超过 2d。通过将
水泥熟料在© 500mM 500mn标准小磨中与二水石膏一起磨细至比表面积为 350
± 10m2/kg, 0.080mm方孔筛筛余不大于4%制成P型硅酸盐水泥后来进行 的。制成的水泥中S03应在2.0%~2.5%范围内。所有试样的物理检验(除28d强 度外)应在制成水泥10d内进行。
出窑熟料28d抗压强度》48Mpa每月统计一次。
(二)、熟料的管理
1、 熟料的储存
出窑熟料不允许直接入磨,应进行储存。
储存的目的:降低熟料温度,防止石膏脱水和保证粉磨效率;提高熟料易磨性。
更多推荐
熟料,质量,控制,生产,生料,水泥,检验
发布评论