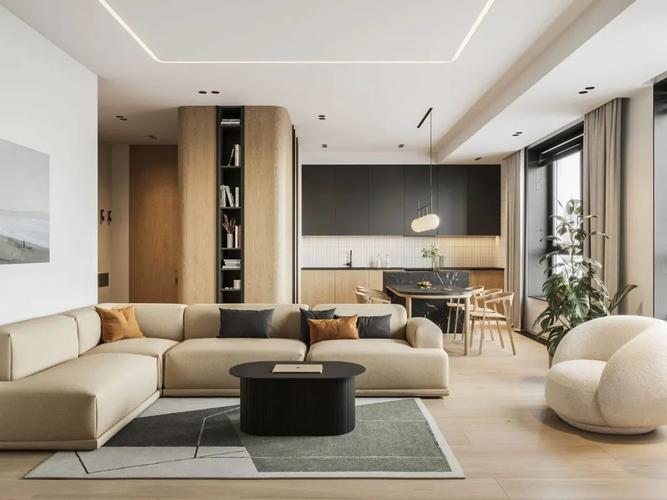
一种高温相变储热材料,属于陶瓷材料技术领域,按下述步骤制得:第一步将石英砂粉、刚玉粉、氧化铜、氧化锌按照比例混合均匀,压制成型后热处理得筛分料A;第二步,将筛分料A、炭黑、硅粉、草酸铝按照比例混合均匀,热处理后得研磨料B;第三步,将刚玉颗粒、刚玉粉、研磨料B、铝硅合金、硅粉、碳化硅粉、热固性酚醛树脂按照比例混合均匀,压制成型热处理后得成品,用该方法制备的高温相变储热材料的工作温度大于600℃,具有储热密度大、导热系数大、耐压强度高、热震稳定性高、生产成本低及工艺简单等特点。
技术要求
1.一种高温相变储热材料,其特征在于按下述步骤制得:
第一步,将40-60wt%的石英砂粉、10-30wt%的刚玉粉、5-15wt%的氧化铜、5-15wt%的氧化锌按照比例混合均匀,经50-100MPa压制成型,置于900-1200℃热处理1-3小时,粉碎、研磨、筛分得到粒度小于0.088mm的筛分料A;
第二步,将50-70wt%的筛分料A、10-30wt%的炭黑、1-10wt%的硅粉、10-20wt%的草酸铝按照比例混合均匀,置于150-300℃热处理1-3小时,研磨、筛分得到粒度小于0.045mm的研磨料B;
第三步,将20-40wt%的刚玉颗粒、10-30wt%的刚玉粉、10-30wt%的研磨料B、20-40wt%
的铝硅合金、1-10wt%的硅粉、1-10wt%的碳化硅粉、1-10wt%的热固性酚醛树脂按照比例混合均匀,经50-100MPa压制成型,置于900-1200℃热处理1-3小时,即得所述高温相变储热材料。
2.根据权利要求1所述的一种高温相变储热材料,其特征在于所述石英砂粉中SiO2的含量大于99wt%,颗粒粒度小于0.088mm。
3.根据权利要求1所述的一种高温相变储热材料,其特征在于所述刚玉粉和刚玉颗粒为棕刚玉或板状刚玉,刚玉中Al2O3的含量大于97wt%,刚玉粉的粒度小于0.088mm,刚玉颗粒的粒度为0.2-3mm。
4.根据权利要求1所述的一种高温相变储热材料,其特征在于所述氧化铜的颗粒粒度小于0.088mm。
5.根据权利要求1所述的一种高温相变储热材料,其特征在于所述氧化锌的颗粒粒度小于0.088mm。
6.根据权利要求1所述的一种高温相变储热材料,其特征在于所述炭黑的灰分小于
0.7wt%。
7.根据权利要求1所述的一种高温相变储热材料,其特征在于所述硅粉中Si的含量大于
98wt%,颗粒粒度小于0.088mm。
8.根据权利要求1所述的一种高温相变储热材料,其特征在于所述铝硅合金中Si的含量大于10wt%,颗粒粒度小于0.088mm。
9.根据权利要求1所述的一种高温相变储热材料,其特征在于所述碳化硅粉中SiC的含量大于98wt%,颗粒粒度小于0.088mm。
10.根据权利要求1所述的一种高温相变储热材料,其特征在于所述热固性酚醛树脂的室温粘度小于11000厘泊,水分含量小于14wt%。
技术说明书
一种高温相变储热材料
技术领域
本技术属于陶瓷材料技术领域,具体涉及一种高温相变储热材料及其制备方法。
背景技术
相变储热材料主要用于工业余/废热回收利用、太阳能综合开发及高温节能等领域。目前主要采用混合
烧结法和熔融浸渗法来制备相变储热材料,但都存在一些不足。混合烧结法是将基体材料、相变材料、添加剂等混匀,经成型、烧结后得到储热材料。该法相对简单,但当烧结温度过高或相变材料含量较大时会造成相变材料的蒸发流失,从而降低材料的蓄热性能。为降低相变材料固、液转变过程中的损失,有研究者将相变材料封装在专门容器内,但这会增加材料的热阻,降低传热效率、提高生产成本。熔融浸渗法则需预先制备多孔陶瓷材料,然后将液态相变材料浸渗到多孔陶瓷孔隙中,冷却制得储热材料。这种方法可以避免相变材料蒸发流失,减少烧结过程体积效应。但该法需要预先制备多孔陶瓷体,相变材料的含量取决于多孔陶瓷预制体的孔径大小及其分布状态,过程较为复杂,且制作成本高。为确保储/释热过程中材料性能的稳定性,储热材料还需具备较高的机械强度、导热系数及热震稳定性等性能,但目前的储热材料在相关方面尚存在欠缺。此外,为了提高能量转换效率和降低成本,太阳能热利用技术正朝着更高工作温度发展,热发电的工作温度已经超过600℃,而大量工业余热的温度也非常高(超过1000℃)。这些都迫切需要开发高温相变储热材料。然而,迄今为止,仍然没有成熟的高温相变储热系统稳定运行。
技术内容
本技术旨在克服现有技术存在的缺陷,目的是提供一种高温相变储热材料,制得的高温相变储热材料的工作温度大于600℃,具有储热密度大、导热系数大、耐压强度高、热震稳定性高、生产成本低及工艺简单等特点。
为实现上述目的,具体是这样来实施的:一种高温相变储热材料,其特征在于按下述步骤制得:
第一步,将40-60wt%的石英砂粉、10-30wt%的刚玉粉、5-15wt%的氧化铜、5-15wt%的氧化锌按照比例混合均匀,经50-100MPa压制成型,置于900-1200℃热处理1-3小时,粉碎、研磨、筛分得到粒度小于0.088mm的筛分料A。
第二步,将50-70wt%的筛分料A、10-30wt%的炭黑、1-10wt%的硅粉、10-20wt%的草酸铝按照比例混合均匀,置于150-300℃热处理1-3小时,研磨、筛分得到粒度小于0.045mm的研磨料B。
第三步,将20-40wt%的刚玉颗粒、10-30wt%的刚玉粉、10-30wt%的研磨料B、20-40wt%的铝硅合金、1-10wt%的硅粉、1-10wt%的碳化硅粉、1-10wt%的热固性酚醛树脂按照比例混合均匀,经50-100MPa压制成型,置于900-1200℃热处理1-3小时,即得所述高温相变储热材料。
所述石英砂粉中SiO2的含量大于99wt%,颗粒粒度小于0.088mm;
所述刚玉粉和刚玉颗粒为棕刚玉或板状刚玉,刚玉中Al2O3的含量大于97wt%,刚玉粉的粒度小于0.088mm,刚玉颗粒的粒度为0.2-3mm;
所述氧化铜的颗粒粒度小于0.088mm;
所述氧化锌的颗粒粒度小于0.088mm;
所述炭黑的灰分小于0.7wt%;
所述硅粉中Si的含量大于98wt%,颗粒粒度小于0.088mm;
所述铝硅合金中Si的含量大于10wt%,颗粒粒度小于0.088mm;
所述碳化硅粉中SiC的含量大于98wt%,颗粒粒度小于0.088mm;
所述热固性酚醛树脂的室温粘度小于11000厘泊,水分含量小于14wt%。
由于采用上述技术方案,本技术与现有技术相比具有如下积极效果:
⑴本技术通过调节结构材料与相变材料的高温反应性,控制二者的组成、形成与分布状态,因而制得的高温相变储热材料具有较高的储热密度。
⑵本技术利用结构材料的形成特点实现相变材料的微观分布,控制相变材料的转变过程状态来调节材料的吸、蓄及传热行为,因而制得的高温相变储热材料具有较高的导热系数。
⑶本技术利用不同原料之间的高温反应特性,形成耐火度高、耐压强度大、热膨胀系数低、化学稳定性高的基体材料,因而制得的高温相变储热材料具有较高的耐压强度和热震稳定性。
⑷本技术根据高温相变储热材料的结构与性能特点,将制备过程分步控制,避免采用高温煅烧等工序,既杜绝了相变材料的结构和性质衰减,又实现了产品结构与性能的巧妙控制。因此,不但所采用的原料来源广泛,而且生产工艺简单、生产成本低。
本技术制备的高温相变储热材料的工作温度大于600℃,材料的性能经检测:储热密度大于650kJ/kg,导热系数大于8.0W/( m·K),耐压强度大于20MPa,热震稳定性(1100℃水冷,次): >20。
具体实施方式
下面结合具体实施方式对本技术作进一步的描述,并非对其保护范围的限制。
为避免重复,先将本具体实施方式所涉及的原料粒径统一描述如下,实施例中不再赘述:
石英砂粉中SiO2的含量大于99wt%,颗粒粒度小于0.088mm;
刚玉粉和刚玉颗粒为棕刚玉或板状刚玉,刚玉中Al2O3的含量大于97wt%,刚玉粉的粒度小于0.088mm,刚玉颗粒的粒度为0.2-3mm;
氧化铜的颗粒粒度小于0.088mm;
氧化锌的颗粒粒度小于0.088mm;
炭黑的灰分小于0.7wt%;
硅粉中Si的含量大于98wt%,颗粒粒度小于0.088mm;
铝硅合金中Si的含量大于10wt%,颗粒粒度小于0.088mm;
碳化硅粉中SiC的含量大于98wt%,颗粒粒度小于0.088mm;
热固性酚醛树脂的室温粘度小于11000厘泊,水分含量小于14wt%。
实施例1
更多推荐
材料,相变,储热,高温,技术
发布评论