2023年12月22日发(作者:樊映川)
家具厂各工序产品质量管理检验标准
一、目的:
为加强产品质量,规范产品质量标准,要求各班组按工艺标准操作,确保质量达标。
二、规范要求:
1、生产前班组长,按图按单,按产品型号规格,批次、材质、数量、颜色等核对无错在生产。
2、各工序产品部件完成后,严格按质量流程检验标准进行检验,下工序做好质量监督检验。
3、对有质疑的产品,在自己不能做出正确处理时,应及时汇报上级管理及质检部门。:
三、机加工组、开料产品质量标准:
3.1、首先对照生产排期单,开料单,图纸与所需要材质进行核对确认无错后,在按单按图进行开料。
3.2、核对料单时在发现排期产品与料单或图纸不符时,立即停止继续生产,并及时汇报给部门管理或质检员,待做出处理确认后再生产。
3.3、材质用料,必须按图要求材质开料,不能私自更改材质。
3.4、材质要求:木皮产品木皮纹理清晰,拼缝平整,表面无损坏,无脱层,无严重残缺,无木皮死结,无木皮黑结蓝斑,无凹凸不平等。(注:部分原材料因天然问题,可根据实际情况做出判定来处理,在判断不准时及时汇报上级管理及质检。)
3.5、原木色产品用料为红山杉木皮,特殊要求粗木眼,大花纹,木皮纹理清晰等。木皮表面材质质量要求同(3.4项)一致。
3.6、开料规则:按照图纸料单尺寸规格与纹路要求进行开料,要求用料不能有杂乱材质,木皮纹路颜色基本一致。先开大件料,后开小料,废料宽度不超过30MM。开出的板件修边毛料误差正负值1MM,不需修边的净料误差±0.2MM。
3.7、电子开料锯与手动推台锯开料操作规范:必须打开底锯,控制好推动时速,确保开好料的产品部件,无缺口飞边,无明显锯印,发现类似质量问题及时停止开料或更换锯片。
3.8、所有常规班台中抽导轨方统一为:300*37*15㎜。
3.9、开料完成后,按单按图,按批次型号,配套清数堆放整齐,做好产品标识,待交接检验确认后交下工段生产。
3.10、检测工具:卷尺、卡尺、目测
3.11、检验人:操作员工、部门管理、质检。
四、机加工组:
1、机加工组、压胶产品质量标准:
1.1、按图,按单,按要求,检查上工段产品部件规格尺寸,产品批次型号,产品数量
配套,产品材质使用与产品质量等是否正确。经确认无误才继续生产。
1.2、压胶产品刷胶均匀,按技术产品骨架图纸正确摆放夹心,夹心摆放间距10-15㎝为宜,夹心双面刷胶,有排孔的位置必须有骨料。皮板位夹心摆放标准夹心留边10㎜以上。图示要求加厚部位必须按图施工加放夹心。(如:线盒孔位置,皮板位置,螺杆连接位置,孔位位置等)
1.3、夹心打钉固定,禁止夹心在产品内倒斜脱落或夹心移位。拼接产品选料整套产品表面无明显材质色差。
1.4、压料厚度允许比成品板件的厚度大0.3mm以内,长宽度误差±1mm。
1.5、压胶时间粘合标准:以保证冷压时间及粘合部位胶水表干强度,结合天气温度变化调整冷压时间。
1.5.1、气温在≤15℃以下,冷压时间为5小时以上,。
1.5.2、气温在16-25℃之间,冷压时间最低为3.5小时以上。
1.5.3、气温在26-35℃之间,冷压时间最低为3小时以上。
1.5.4、气温在≥36℃以上,冷压时间最低为2小时以上。
1.6、压胶冷压重量:
1.6.1、按仪表指示调压重量,常规工艺加压3.5T—5.0T之间。
1.6.2、压大板时可把冷压重量提高,最高不超过10.0T。
1.6.3、冷压产品在正常加压重量下,冷压时间不得超过12小时以上,在无法避免的情况下,可根据时间进行减压重量,可避免产品压变形或夹心不平等现象。
1.7、粘合类部件平整度:
1.7.1、压胶成形正视面板件对角线长度≥1400㎜翘曲度允许值≤3.00MM;<1400㎜≥700㎜的板件翘曲度允许值≤2.00㎜;<700㎜翘曲度允许值≤1.00㎜。
1.8、压胶产品面板时可使用垫板有略微向上凸模板2-4㎜;要求压胶成型后产品可上凸弧度整块顺畅,不能单点上凸或波浪状现象。
1.9、压胶好的产品部件,不得有任何爆裂,脱胶,无钉头外露等;台面面板上面不能有直钉孔;产品表面无压痕,无粘烂,无刮花等现象。
1.10、粘合台面下压后摆放:因胶水未完全干透不能及时进行铣型,待干后在进行铣型。下压产品摆放时按技术(YHJJ-GG-11060201)文件执行摆放,确保产品不变形。
1.11、检测工具:卷尺、卡尺、目测。
1.12、检验人:操作员工、部门管理、质检。
2、机加工组、封边产品质量标准:
2.1、按单,按产品型号分清部件左右配套,选用封边条规格以及封边条颜色。
2.2、常规产品封边:产品部件按图纸要求封外露边;所有活动层板四方封边。
2.3、常规黑胡桃,红胡桃、原木色、樱桃色颜色产品都用“PVC”封边条封边;班台类、职员桌类、文件柜类、茶水柜类等产品门板、抽面都封木皮封边条。
2.4、订做产品无特殊要求的按常规工艺封边,有客户特殊要求的按单要求封边。
2.5、热熔胶温度:封边热熔胶使用温度在195℃±5℃,封边速度分高、中、低;15厘板厚度使用高速封边,18厘板使用中速封边,25厘板使用低速封边。
2.6、封边后的产品质量:封边条无鼓泡,无缺口,无脱胶,无漏胶,无损坏、无波浪,无冒边等现象;木皮封边产品打磨光滑,顺畅,无残缺,不刺手等;除尘干净产品面上的杂物与胶水。
2.7、封边产品标识:常规产品在部件下口方写好产品名称批次;订做产品写好分部编码及产品批次名称;可左右互换部件(如:门板类等)的产品编码及产品名称可写在门铰位置处。
2.8、封边完成产品:做好部件配套,数据准确,堆放整齐;按颜色,按批次,按规格型号分类堆放;若有不配套差件或部件损坏,应及时汇报给部门管理处理,并做好差件记录跟踪。
3、机加工组、排钻产品质量标准:
3.1、排钻前,按单确认产品部件的规格型号,批次批量,确认无误时继续生产;对有质疑部件应及时汇报给部门管理处理,并做好跟踪记录。
3.2、孔位孔距调整:每批次产品必须按技术排孔图纸要求,进行排孔钻头孔距调整,确认首件部件孔距孔位调整无错后,在进行批量排钻生产。
3.3、排钻时产品配套,分清板件左右,板件正反面,板件纹路方向。
3.4、批量产品在排钻生产过程中,排钻人员要多次检查核对排孔部件的孔距孔位是否移位。
孔深度要求误差范围+0.5mm内,孔径允许±0.1mm内,孔轴距允许1000mm以内误差允许±0.2mm;大于1000mm小于1500mm时,误差允许±0.3mm;大于1500mm时,误差允许±0.5mm。孔位无毛刺、崩边、爆裂、塌陷、崩口、无伤皮面。无凹凸或爆裂,孔位无排穿等。
3.5、常规产品排孔要求:严格按照技术排孔图施工,任何人员不能私自调整更改排孔图标准,确保任何批次,任何时间,生产的同型号常规产品,排孔孔位孔距一致。订做产品无特殊要求,按常规产品排孔标准施工。对图纸要求要质疑的产品,应及时汇报给部门管理处理。
3.6、对排钻完成后的产品,在堆放中要确认产品左右配套正确,数据准确,同时按型号批次,规格颜色分类摆放整齐。
3.7、检测工具:卷尺、卡尺、目测。
3.8、检验人:操作员工、部门管理、质检。
4、机加工组、立刨产品质量标准:
4.1、按单要求对照产品确认一致,选用立刨刀,进行安装。
4.2、根据产品选用模板,立刨后产品正面不得留下钉孔,若无法避免可用小钉,孔径≤1.5MM 的钉子钉模板。
4.3、产品成型后边角无缺口,无波浪状,无变形,产品表面无刮花等;对角邻边对称,成型后产品长宽规格公差允许值±2.0㎜。
4.4、立刨后产品堆放整齐,大件产品与面板按技术《YHJJ-GG-11060201》文件执行摆放,避免产品再次变形。
4.5、检测工具:卷尺、卡尺、目测。
4.6、检验人:操作员工、部门管理、质检。
5、机加工组、锣机产品质量标准:
5.1、按单对照产品部件,锣机时按图纸要求使用线刀刀样。
5.2、锣好线条的产品线条无波浪状,无弯曲,无飞边缺口,曲线流畅,深浅按图纸要求确保一致。
5.3、锣皮板、锣笔槽、锣中抽口,锣线盒孔,锣连接孔位时等,都必须按图要求的规格位置
使用线刀进行施工。
5.4、锣好的产品边面平整,底部光滑,角度对称,无波浪状,无缺口,无变形,无刮花,线盒孔,笔槽无空洞等问题,开孔位置并符合技术图纸标准等工艺质量要求。
5.5、检验人:操作员工、部门管理、质检。
6、机加工压刨、吊锣产品质量标准:
6.1、按单对照产品部件,按图纸要求使用线刀刀样,分清产品部件型号规格,区分左右配套。
6.2、压刨造型产检验人:操作员工、部门管理、质检。品部件时,结合刀具与材质性能,手推力度适中,确保产品线口边角无缺口,无飞边,无变形,边口光滑顺畅,角度对称。确保正反对角线角度一致,正反对角线公差允许值为≤0.2㎜。
6.3、钻锁孔,锣拉手,锣主机孔,部分装饰部件铣型时,按图纸要求选用线刀与模板;施工中分清部件正反面,左右配套正确,造型后部件表面无刮伤,造型部位无变形,无缺口等。
6.4、检测工具:卷尺、卡尺、目测。
6.5、检验人:操作员工、部门管理、质检。
7、机加工组、台面组装产品质量标准:
7.1、按单进行生产,台面在成型组装后,长、宽规格最大公差允许值为±2.0㎜。
7.2、组合台面面板在组合中面板拼接处必须平整,木皮纹理基本一致无明显材质色差。
7.3、台面皮板对扪皮留缝标准:
7.3.1、1.8米以下台面皮板按扪仿皮标准留缝《包括1.8米》,留缝标准为2.0-2.5㎜。
7.3.2、1.8米以上班台,主席台,会议台皮板按扪西皮标准留缝,留缝标准为2.5-3.0㎜。
7.3.3、成型后皮板留缝公差允许值正负0.2㎜。《注:以上皮板留缝标准,需参照皮样
封样厚薄留缝为准。》中抽面留缝按照图纸要求执行。
7.4、皮板位夹心平整,四角角度匀称,压皮板处夹心留边10㎜以上。
7.5、台面面板工艺线,必须按照图纸生产,产品线条大小深浅一致,线条内无锣机印,无缺口,无变形,边角光滑不刺手;线盒孔内夹心无空洞,内圆无波浪状。(注:常规3厘工艺线标准为:宽3.0㎜、深1.5㎜、线型为”U”型。)
7.6、台面面板拼版处3厘线条线缝要求密实,线底平顺光滑,线缝公差允许值≤0.5㎜。
7.7、台面打磨,底磨必须平整,无波浪状,无凹凸,无槽痕,无缺口,无变形,无铁钉外冒,补好洞眼与缝隙等。在打磨平整后用“底得宝”油漆刷油做固化处理时,刷油必须饱满,避免缩水,油漆待干后用光板打磨平整光滑,棱角分明。
7.8、检测工具:卷尺、卡尺、目测。
7.8、检验人:操作员工、部门管理、质检。
五:手工组:
1、手工组、钉装产品质量标准:
1.1、台脚钉装以及门板钉装等钉装产品,按图按单要求钉装,工艺部件刷胶均匀饱满,枪钉密度控制在20-25㎝之间。钉装成型后拼缝位置公差允许值≤0.3㎜。反面拼接处钉装平整,无缝隙。
1.2、组装柜产品钉装成型后内净空长、宽、高公差允许值≤1㎜,内空对角线公差允许值≤1㎜;柜口边顺平,柜侧面无凹凸等现象。
1.3、造型挡板钉装时,刷胶均匀饱满,工艺线条角度拼接平整,线条顺畅;枪钉钉在线条隐藏处,无钉头外冒,无松动等。
1.4、所有产品台脚,挡板装饰板,都必须按图按单生产,装饰板工艺造型边都需刷好“PU”油漆打好磨。分色装饰板做成活动不用钉装,不分色的装饰板按要求钉装好,同时装饰板表面不能打钉,可打钉在边角隐蔽处。
1.5、钉装产品枪钉间距,一般为15-20CM之间打钉,根据产品结构能打在隐藏位置处,减少钉孔不外露。枪钉以外的钉眼由木工处理补好钉眼,直钉纹钉眼由油漆处理补好,钉装拼接缝隙由木工处理。
1.6、台脚、挡板等底磨产品在进行底磨处理时,底部打磨平整,无波浪状,无凹凸,无槽痕,无缺口,无变形,无铁钉外冒,补好洞眼与缝隙等。
1.7、木工毛坯产品底部刷油打磨标准:
1.7.1、台面边、柜面边、台脚上下口边等产品,用“PU”油漆或“底得宝”刷油。
1.7.2、产品装饰线,倒15R以上装饰板,在没钉装前用“PU”或“底得宝”刷油
1.7.3、25厘板直接成型的台脚与茶几台脚,木工在生产时上下口边可不刷油。
1.7.4、刷油必须饱满,避免缩水,油漆待干后用光板打磨平整光滑,棱角分明。
1.8、中抽架/面,键盘/面、吊键盘/面、活动主机架,按单按图纸工艺要求钉装。
1.9、检测工具:卷尺、卡尺、目测。
1.10、检验人:操作员工、部门管理、质检。
2、手工组、手工贴皮质量标准:
2.1、按单、选用木皮材质及颜色,按产品规格裁木皮尺寸,长边料边只允许大于20mm,宽边料只允许大于10mm。
2.2、木皮材质质量要求:木皮表面颜色纹路一致,无斑点、无腐朽、无死节,无空泡等。
2.2、台面产品贴皮上口边超过9.0㎜以上工艺线(不含9.0㎜)都要贴皮。(注:台面笔槽类似圆底线不需贴皮。)其余产品边面按单要求贴皮。
2.3、拼接组合台贴皮后,要求木皮无明显色差。《注:组合产品因特殊原因导致,需反贴木皮一块产品时,需严选木皮纹路颜色,若对不上需整套全贴木皮。》
2.4、贴皮产品刷胶时,胶水干稀适度,厚薄均匀,胶水中无颗粒状结皮等;按木皮纹理方向贴皮,木皮拼接处平整,不重叠,不留缝等。
2.6、木皮待干打磨后,产品无空泡,无缺口,无脱皮透胶,无木皮打穿,无遗漏胶水等,打磨后平整光滑,手感好,棱角分明。
2.7、检测工具:卷尺、卡尺、目测。
2.7检验人:操作员工、部门管理、质检。
3、手工组、试装产品质量标准:
3.1、要求每批次产品进行随机抽件试装1套,安装完整,产品规格符合工艺图纸和有关技术参数规定进行试装检验。(注:在不影响质量判断时,个别产品的门板,桶面、桶侧桶头尾、键盘/面,中抽/面,皮板,装饰板等可配套比对检验。)
3.2、对来料部件不符合质量要求的,不符合图纸要求与技术参数与的产品,不予以试装。
3.3、对产品组立尺寸按图要求长、宽、高进行检验,受检产品尺寸与实测误差值允许±3mm。
3.4、翘曲度检验:面板对角线长度≥1400mm、允许值≤3mm,正视面板件<1400mm,≥700mm、允许误差值≤2mm。
3.5、框架对角线长度≥1000mm或<1000mm,允许误差值≤2mm。
3.6、门、桶面与框架相邻边的分缝间隙≤2.5mm,偏差值±0.5。
3.7、孔深度误差允许+0.5内,孔径允许±0.1mm内,孔轴距允许1000mm以内误差允许±0.2mm;大于1000mm小于1500mm时误差允许±0.3mm;大于1500时误差允许±0.5mm。
3.8、产品表面光滑、无刮伤穿烂、无空泡,无遗留胶水,组合产品材质无明显色差。
3.9、产品部件边面无缺口、无波浪,面边平整、线条顺畅。
3.10、产品规格符合工艺图纸和有关技术参数规定,经确认合格后,木工部门管理员分别在流程单上签字确认,同时该流程单与图纸交予质检部门,由质检部门确认后交予后工序油漆部做生产计划。
3.11、检测工具:卷尺、卡尺、目测。
3.12、检验人:试装员、部门管理、质检。
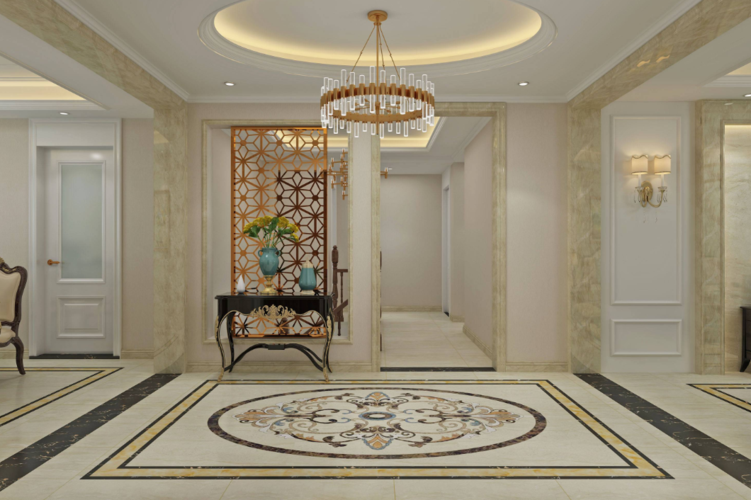
更多推荐
产品,要求,部件
发布评论