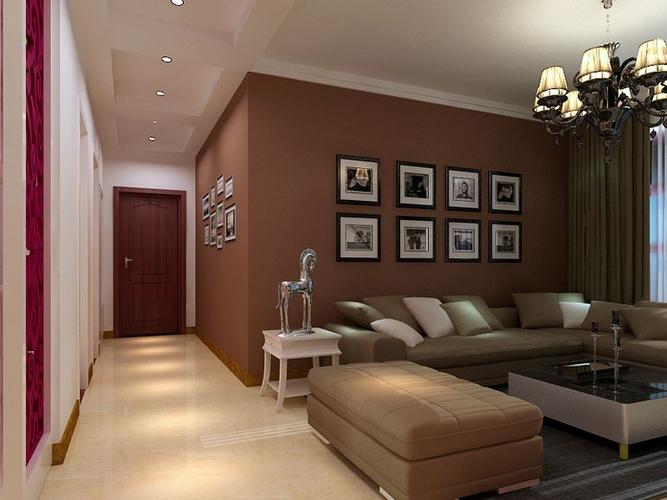
研究与探讨
压缩率。
压缩率= (1)式中:H0—热压前的厚度,mm;
H1—热压后的厚度,mm。
经计算,压制密实化表板的杨木单板一次热压压缩率为31.2 %。把宽度为335 mm的密实化杨木表板锯制成宽度为80 mm 的板条待用。
把杨木板材刨成厚度为12 mm的薄板,再锯制成尺寸(长×宽×厚)为80 mm×50 mm×12 mm的杨木芯板条待用。上层密实化杨木表板双面涂胶,下层密实化杨木表板单面涂胶,与装饰层桦木刨切薄木(0.7 mm)和杨木芯板条(12 mm)组坯,组坯时密实化杨木表板及刨切薄木的纤维方向和杨木芯板条纤维方向互相垂直。组好的地板板坯在压力0.8 MPa,温度105 ℃,时间10 min的工艺条件下,二次热压胶合成杨木复合地板。然后测量压制的复合地板的厚度,根据公式(1)计算二次热压压缩率,计算结果为4.7 %。
压制的杨木复合地板至少放置一天后,参照实木复合地板GB/T 18103-2000检测静曲强度、弹性模量、含水率和每个胶层各边剥离长度。再按公式(2)计算剥离率:
剥离率 =
(2)1.2.3 以三层密实化单板为表板的杨木复合地板的工艺研
究 测量并记录下个各层单板的厚度。将脲醛树脂胶调配好后,按照单面涂胶量为150 g/m2 涂刷在尺寸(长×宽×厚)为335 mm×335 mm×1.7 mm的杨木单板上,在压力2.5 MPa,温度105 ℃,时间1 min/mm的条件下,把3张单板压制成密实化杨木表板。测量密实化杨木表板的厚度,根据公式(1)计算一次热压的压缩率,计算结果为29.2 %。把压制的密实化表板锯制成宽度为80 mm的板条待用。
把杨木板材刨成厚度为10mm的薄板,再锯制成尺寸为80 mm×50 mm×10 mm的杨木芯板条待用。上层密实化杨木表板双面涂胶,下层密实化杨木表板单面涂胶,与装饰层桦木刨切薄木(0.7 mm)和杨木芯板条(10mm)组坯,组坯时密实化杨木表板及刨切薄木的纤维方
向和杨木芯板条纤维方向互相垂直。组好的地板板坯在
压力0.8 MPa,温度105℃,时间10 min的工艺条件下,二次热压胶合成杨木复合地板。
根据公式(1)计算二次热压的压缩率,计算结果为
图2 密实化表板杨木复合地板断面结构
1.2.1 压制密实化表板的热压压力研究 将调制好的脲醛树脂胶粘剂按照150 g/m2的单面涂胶量,均匀地涂刷在尺寸(长×宽×厚)为300 mm×87 mm×1.7 mm的杨木单板上,在热压温度105 ℃,热压时间 1 min/mm,热压压力分别为1.5 、2.0 、2.5 、3.0 MPa的条件下,把杨木单板胶合在一起,研究杨木单板的压缩程度和密实化程度,计算不同压力下的单板压缩率及压密后的密度,并检测密实化表板的MOE和MOR。
1.2.2 以双层密实化单板为表板的杨木复合地板的工艺研究 测量并记录下2层杨木单板的厚度。将脲醛树脂胶调配好后按照150 g/m2的单面涂胶量涂刷在尺寸(长×
宽×厚)为335 mm×335 mm×1.7 mm 的杨木单板上,在压力2.5 MPa,温度105 ℃,时间1 min/mm的条件下,把2张单板压制成双层单板密实化表板。测量密实化表板的厚度,然后根据公式(1)计算杨木单板一次热压的
H0-H1H0
×100%
任一胶层开胶的累计长度
该胶层总长度
×100%热压机;锯机;
游标卡尺:精度为0.02 mm。1.2 试验方法
杨木本身的材质软、密度小,强度和硬度都很低,要想完全利用杨木制作地板基材,就必须提高其自身的密度和强度。为此,本研究采用了表板密实化工艺,同时为了减少杨木地板的整体压缩损失,采用了二次热压的工艺,即首先在较高的压力下把双层或三层杨木单板热压胶合成地板的密实化表板,同时将杨木锯剖成板材,经干燥、刨削、加工成一定厚度的薄板条;然后将装饰层桦木刨切薄木、密实化表板与杨木芯板在较低的压力下,二次热压胶合成杨木复合地板。密实化表板杨木复合地板的工艺流程见图1,密实化表板杨木复合地板结构示意图见图2。
含水率分别为10.31%和9.82%,含水率梯度为0.49%。第4天到第10天为第2养生阶段,第10天的平均含水率为11.16%,表、芯层含水率分别为11.57%和10.80%,含水率梯度为0.77%。
70℃养生结果如图4所示,仅用5.5天的时间各项含水率指标便达到要求。因为在70℃下养生,试件的含水率上升速度显著加快。养生的前2天为第1阶段,平均含水率从6.31%升高至9.69%,此时表、芯层含水率分别为9.87%和9.55%,含水率梯度仅为0.32%。第2天到第5.5天为养生第2阶段,此阶段试件平均含水率从9.70%升高到13.12%,表、芯层含水率分别为13.26%和13.05%,含水率梯度为0.21%。
从我国企业实木地板坯料现有的养生方法看,多在室温条件下放置,以达到含水率平衡和减小残余应力的目的。但由于实木地板坯料多为密度较大的硬阔叶材,在室温下板材断面含水率不易达到均匀,如果含水率过低,则含水率上升速度较慢,养生周期长、养生效果不明显。鉴于本文的研究结论,有条件的企业,可以在干燥窑内采用合适的温、湿度进行养生,或建造养生室,以提高养生效率和养生效果,从而达到提高产品质量、增加经济效益的目的。参考文献:
[1] 金昌升,池永亮.强化地板生产中地板坯料养生周期 的确定[J].林产工业,2004(5):24-28.
[2] 顾炼百主编.木材加工工艺学[M].中国林业出版社. 2003,3.
(责任编辑:舒文博)
由上述试验箱中养生实验的结果可知,随养生温度的升高,养生周期缩短,最后的平均含水率越高,含水率梯度越小。室温养生22天的试件含水率仍然较低,且含水率梯度较大。而在试验箱中70℃养生仅用5.5天,试件含水率便升高至13.12%,且含水率梯度较小,仅为0.21%。这是因为:木材细胞壁内有无数的微毛细管,这些微毛细管组成微毛细管系统,当较干的木材存放在潮湿的空气中时,木材微毛细管内的水蒸气分压低于周围空气中的水蒸气分压,微毛细管便能从周围空气中吸收水分,在微毛细管内由水蒸气凝结成凝结水;这种细胞壁内的微毛细管系统从湿空气吸收水分的现象叫吸湿,而木材吸湿的速度是随温度的升高而升高的。3 结语
甘巴豆室温养生周期比较长,且横断面含水率不易均匀,22天含水率从6.26%升高至9.03%,未能达到南方地区要求的含水率,且含水率梯度较大。但在较高的温度和湿度条件下,甘巴豆地板坯料的养生周期显著缩短并且含水率梯度明显减小,养生的效果显著。甘巴豆地板坯料在40℃、55℃、70℃条件下分别养生11天、10天、5.5天含水率便达到南方地区要求的含水率。
图4 70℃养生含水率随时间变化图
养生时间/d
0 1 2 3 4 5 6
11109876
14
1312平均
1、8层
3、6层2、7层4、5层
含水率/%
(上接第10页)杨木表板的压缩率不断增加,板的致密程
度越高,MOE和MOR也得以增加。
(2) 经试验确定密实化表板热压工艺为:热压压力2.5 MPa,温度105 ℃,时间1
mm/min。在此工艺下杨木单板压密的压缩率接近30 %,密实化表板密度达到0.77 g/cm3。
(3) 将上述条件下压制的三层单板密实化杨木表板,在二次热压工艺为热压压力0.8 MPa,温度105 ℃,时间10 min的条件下,与杨木芯板和刨切的桦木薄木热压复合成地板,经过力学性能检测,其弹性模量的平均值为5 822 MPa,静曲强度的平均值为47.7 MPa,均达到了GB/T 18103-2000的标准。参考文献:
[1] 傅峰,鲍甫成.人工林杨木的用途选择——实木或单板层积 材.林业科学.1999,35(4):58-59.
[2] 王卫东,王志强,路孝君,卢晓宁.金属网增强型杨木单板 层积材的研究.南京林业大学学报(自然科学版).2003,27 (6):9-10.
[3] 卢晓宁,陈宇聪,陈颖.速生杨木单板顺纹弹性模量与预测 模型.南京林业大学学报(自然科学版).2002,26(3):9-10.[4] 陈鹏.出口地板用杨木单板生产技术关键.林业科技.2002, 27(2):48-49.
(责任编辑:舒文博)
实用技术
更多推荐
养生,含水率,单板,热压,地板
发布评论