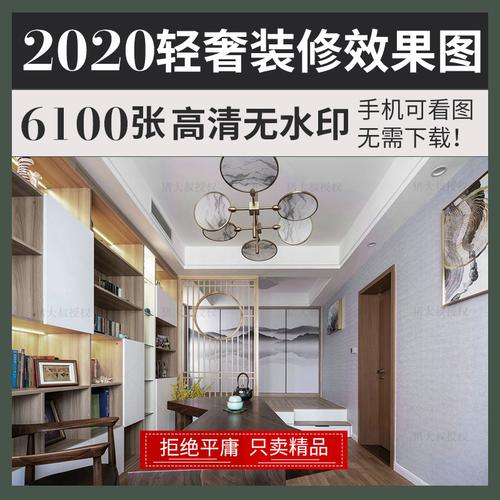
压贴缺陷及解决方法
序号 | 缺陷名称 | 术语 | 现象 | 原因 | 解决办法 |
1 | 干花(白花) | 由于树脂浸渍纸的挥发分含量过低或树脂局部固化过快等原因造成的产品表面不透明白色斑痕。 | 同位置产生,基材调头后仍然出现在钢板相应位置,有凸凹手感 | 钢板表面有凸凹现象,钢板缺陷产生干花,特殊钢板阻碍胶的流动。 | 更换钢板 |
不同位置产生,基材调头后仍然出现在不同位置 | 基材表面砂光不平或密度偏差过大 | 更换基材 | |||
同位置产生,基材调头后仍然出现在相应位置,钢板无凸凹手感 | 缓冲垫失去缓冲作用,产生干花 | 更换缓冲垫 | |||
钢板镜框严重; | 更换钢板 | ||||
下压板不平 | 调平下压板 | ||||
不同位置产生干花,调整工艺后消失 | 压贴工艺不佳,压力小或温度高或时间短 | 加压、降温或加时间。 | |||
不同位置产生干花,与基材、设备、热压均无关 | 树脂胶配比不当,渗透性差 | 更换浸渍纸(调整浸渍工艺参数) | |||
2 | 湿花(水迹) | 由于树脂浸渍纸的挥发分含量过高、基材含水率过高或压贴工艺不当而造成的贴面产品表面存在的云雾状痕迹。 | 调整工艺,更换基材后仍出现。 | 浸渍纸挥发物偏高 | 更换浸渍纸(调整浸渍工艺参数) |
钢板表面有污染,使钢板的污染粘到板面 | 钢板表面有污染,使钢板的污染粘到板面 | 更换或清洗钢板 | |||
更换基材后消失 | 基材含水率偏高 | 更换基材 | |||
调整工艺后消失 | 压贴工艺调整不当,温度过低,时间过短 | 及时调整工艺,升温,加时间 | |||
3 | 针孔 | 产品表面针状孔隙缺陷 | 整个板面或局部产生 | 上胶量偏低 | 更换浸渍纸,调整上胶量 |
纸油墨太重,浸胶渗透性差 | 调整印刷工艺, 增强胶的渗透性 | ||||
印刷纸PH值偏低,影响浸渍工艺 | 印刷更换印刷原纸或油墨 | ||||
储存时间过长,树脂老化流动性差 | 换浸渍纸,合理排计划,减少存放期 | ||||
整个板面都有 | 特殊钢板(如浮雕面)阻碍树脂流动性 | 使用特殊工艺的浸渍纸或少用特殊钢板 | |||
压贴产生针孔,调整工艺后消失 | 温度过高、树脂固化加快减弱树脂流动性,难以形成连续胶膜 | 调整工艺降温,延长热压时间 | |||
4 | 透底 | 由于装饰胶膜纸覆盖能力不够,造成基材板面上显现的缺陷 | 色泽不同,透底处一般泛底色 | 原纸定量偏差大 | 更换浸渍纸 |
浸渍涂胶不均匀 | 更换浸渍纸,调整浸渍工艺上胶均匀 | ||||
5 | 光泽不均 | 产品表面反光现象的差异 | 浸渍纸挥发物偏高,涂胶不均匀 | 加强浸渍生产过程式工艺控制 | |
原纸定量偏差大,造成局部透底严重 | 提高装饰纸质量 | ||||
浸渍纸浸、涂胶比例不当 | 改变胶的配比,提高浸渍质量 | ||||
钢模板局部脱铬 | 更换钢板进行修复 | ||||
6 | 龟裂 | 由于树脂在热压过程中固化过度或表面层与基材膨胀收缩不同而造成产品表面出现的网状细微裂纹。 | 产品表面产生不规则的裂纹,更换基材或调面后消失 | 基材表面结合强度太差或漏砂 | 更换基材,选表面结合强度高的基材 |
产品表面产生不规则的裂纹,调整工艺后消失 | 树脂在长时间高温作用下固化过度 | 调整压贴工艺,严格加强工艺控制 | |||
固定部位出现 | 压机传热系统温差太大 | 检查热油系统流量的均匀性,使温差缩小 | |||
产品表面产生不规则的裂纹,更换基材或调面后仍有 | 浸渍纸的固化时间太长造成热压时间过久 | 调整浸渍工艺参数 | |||
7 | 分层 | 基材自身、胶膜纸自身或胶膜纸与基材之间的分离现象 | 热压后产生白边,基材与胶膜纸分离 | 基材边缘出现踏边 | 选用合格基材,适当提高压力 |
热压后基材边部产生分离现象 | 基材内结合强度或密度过低 | 选用合格基材,降低压力 | |||
热压后基材边产生分离现象,并伴有撞击痕,但基材无此现象 | 生产过程中撞坏 | 维修设备,规范操作 | |||
压贴后胶膜纸与基材产生分离 | 装饰纸定量偏大,树脂胶渗透不好 | 换纸, 调整浸渍工艺加强胶渗透性 | |||
压贴后胶膜纸与基材产生分离 | 胶膜纸树脂老化(存放过期) | 不予使用 | |||
压贴后胶膜纸纸基自身分离 | 浸渍中胶未浸透 | 调整浸渍工艺,增强渗透性 | |||
压贴后油墨层与纸产生分离 | 油墨层太厚胶未能浸透 | 换纸,调整印刷工艺 | |||
同一位置产生胶膜纸与基材分离 | 钢模板局部凹陷 | 更换钢板,返修 | |||
8 | 鼓泡 | 产品表面内含气体引起的异常凸起 | 板面偶尔起泡,基材分层 | 基材含水率偏高,内结合密度不够,密度不均 | 更换基材 |
板面起小泡,纸基分层,热压正常 | 浸渍工艺不佳 | 调整浸渍工艺 | |||
板面偶尔起小泡 | 加压时间过长,压板温度过高 | 调整工艺,降低温度 | |||
板面偶尔起小泡 | 基材板面局部存在纤维团或粗纤维,对应部位出现小泡 | 更换基材 | |||
9 | 鼓包 | 产品表面内含有固体实物引起的异常凸起。 | 板面有异常凸起 | 基材表面有异常凸起 | 更换基材 |
基材表面附有异物如锯屑、砂光粉等 | 压贴前清扫基材表面 | ||||
10 | 纸板错位 | 由于胶膜纸与基材对位不准而造成的产品板材缺纸。 | 胶膜纸白边压在板上 | 因基材过宽或过长或对角线偏差过大造成胶膜纸与基材不匹配 | 选用规格尺寸合格的基材 |
胶膜纸过窄或过短或对角线偏差过大造成胶膜纸与基材不匹配 | 调整浸渍纸尺寸 | ||||
露基材,但浸渍纸尺寸大于基材尺寸 | 胶膜纸与基材对位不准 | 严格执行操作规程 | |||
11 | 破损 | 板(纸)的四角或边缘被损坏而造成的缺陷 | 装卸车或堆垛不规范造成撞坏 | 不规范操作 | 严格执行操作规程 |
纸破损,造成饰面缺纸 | 铺纸工或配纸工弄破 | 严格执行操作规程 | |||
胶带粘纸,造成饰面板缺纸 | 浸渍纸挥发物偏高或受潮 | 规范保管或更换浸渍纸 | |||
基材异物把纸顶破 | 检查基材 | ||||
12 | 污染 | 产品表面粘上或染上非胶膜纸自身物质的异物 | 浸渍纸使用环境污染,产生黑点、异物、手印、虫污等 | 使用过程二次污染 | 保持使用环境的清洁及防虫 |
浸渍过程产生尘污、手印、虫污 | 浸渍污染(手印) | 防虫、防尘、净手 | |||
压机漏油产生板污 | 压贴油污 | 维修设备 | |||
钢板上附有异物造成的污染 | 压贴污染 | 防尘、清洗钢板 | |||
开机污染 | 钢板上附有异物 | 开机前应做好生产准备清洗工作 | |||
纸张上胶粉凝聚产生污斑 | 纸张上胶粉凝聚到小车上而掉落到板面 | 对小车上凝聚的胶粉及时清除 | |||
13 | 纸屑 | 细小浸渍纸或其它纸屑(片)压贴在成品板面造成的污斑缺陷或因清边不干净,掉在板间造成板面凹坑。 | 板面细小纸屑,不能清除 | 由于浸渍切纸刀间隙不当,产生纸屑 | 及时调整间隙 |
压贴时发现纸上有纸屑未能及时清除,使用有缺陷的无法清除纸屑的浸渍纸 | 挑出有问题的纸 | ||||
清边不干净,堆码时清扫装置不佳造成掉进板间 | 刮边干净与板面清扫装置调节好 | ||||
推板时平衡纸碎屑留在压机内导致进板时把纸带到板面 | 及时对压机内异物进行清除 | ||||
块状纸片,不能清除 | 浸渍纸挥发物高而造成胶带粘纸 | 调整浸渍工艺 | |||
浸渍纸存放不好或超期、回潮造成胶带粘纸 | 加强管理,合理利用 | ||||
可以清除的纸屑,但会造成板面凹坑 | 清边不干净,堆码时清扫装置不佳造成掉进板间 | 刮边干净与板面清扫装置调节好 | |||
14 | 划痕 | 在同一位置有轻微划痕,但饰面无划伤手感 | 钢板表面划伤 | 更换钢板返修 | |
下板面同一位置有横向划伤、划伤手感明显 | 钢板、滚筒、板凳上有异物,抬板工拖板过程产生划伤 | 及时消除异物,并确认 | |||
板底对板面的划伤 | 板下弯过大,堆码时板角与板面单点接触而对板面划伤 | 调节好工艺,确保板不下弯过大 | |||
饰面板间间有异物造成两饰面同一位置划伤 | 堆码时清扫装置不佳造成碎屑掉进两饰面间 | 清扫装置调节好 | |||
15 | 压痕 | 同一位置板面出现凸凹现象 | 垫板或钢板上有异物或钢板有脱铬或凸痕 | 清洗,返修 | |
16 | 泛白 | 树脂胶固化不完全而出现发白的现象 | 树脂胶固化不完全而出现发白的现象 | 浸渍纸预固化度偏低或挥发物偏高 | 调整浸渍工艺 |
工艺不当,压贴温度较低或压贴时间较短 | 调整工艺,增高压贴温度或延长压贴时间 | ||||
17 | 爆板 | 基材自身出现大的鼓泡现象 | 在正常工艺下,间断或不间断爆板 | 基材含水率偏高,内结合密度偏低 | 更换基材 |
非正常情况爆板(基材边部发生黄变、厚度偏薄) | 压力系统故障 | 维修设备 | |||
压贴时间过长、热压温度过高或未及时把板拖出来 | 减少压贴时间、降低热压温度,及时抽板 | ||||
18 | 老印 | 板面压在钢板旧痕迹上 | 板边装饰纸被部分粘掉 | 压贴位置未对齐所致 | 调整对位 |
19 | 纹路 | 压贴后产生纵横条状纹路 | 基材表面有砂光纹路,浸渍纸不能覆盖 | 选用合格的基材 | |
20 | 亮点、亮斑 | 板面产生亮点(側视) | 浸渍胶添加剂质量原因,(不洁,过期) | 更换添加剂 | |
局部氧化铝未涂上,板面点状发亮的现象,一般呈规律性,由于滚筒上粘异物造成,主要指耐磨装饰胶膜纸 | 对滚筒进行适时检查,及时清除异物 | ||||
浸渍胶添加剂搅拌不匀 | 调整浸渍工艺 | ||||
21 | 皱褶 | 纸面折痕 | 少量纸折叠在一起颜色较深 | 印刷中原纸活皱,皱纹展开有图案、油墨 | 加强印刷质量控制,使用时挑出不合格品 |
印刷图案不连续 | 印刷时原纸死皱 | 选用印刷原纸 | |||
浸渍过程印刷纸打皱 | 调整浸渍工艺 | ||||
22 | 水纹(折皱) | 压贴成品板面呈现水波纹状皱纹 | 压贴时装饰纸局部重叠或被拉裂,呈水波纹状皱纹 | 浸渍纸与基材受热后膨胀收缩不一致,调整热压工艺能解决 | 调整生产工艺(可以调整压机加压时间) |
浸渍纸与基材受热后膨胀收缩不一致,调整热压工艺不能解决,更换基材后消失 | 更换匹配的基材 | ||||
浸渍纸与基材受热后膨胀收缩不一致,调整热压工艺不能解决 | 可采取焐板或两次压贴解决 | ||||
纸品保存环境不佳(要求20℃,湿度60﹪) | 改善保管环境 | ||||
以上方式均无法解决 | 更换印刷原纸或调整浸渍工艺 | ||||
23 | 凹坑 | 成品板板面不平,有凹陷现象 | 对光斜视板面有凹凸不平现象,严重的有小坑。 | 基材局部密度不均匀或含水率不一致,受热膨胀收缩不一样造成。 | 选用适宜的基材 |
同一位置板面出现压坑现象 | 钢板本身有凸起,缓冲垫与钢板之间有异物或上压板油渍过多造成钢板凸起 | 更换钢板,检查上压板与缓冲垫 | |||
24 | 崩边 | 产品在齐边及后加工过程中造成装饰面板边锯齿状缺陷 | 板边锯齿状缺陷 | 下料锯或刀的线速度低、钝、进料速度太快或锯齿、刀角度设计不合理等 | 改进设备或工艺 |
板边锯齿状缺陷,油墨脱层 | 油墨太重,影响胶的渗透 | 改变印刷工艺 | |||
板边锯齿状缺陷,崩边处现纸基 | 浸渍时胶渗透性差 | 调整浸渍工艺 | |||
板边锯齿状缺陷,崩边处见基材 | 基材表面强度差 | 选用适宜的基材 | |||
25 | 白点(氧化铝泛白) | 成品板面呈现的白色小颗粒 | 主要针对液体耐磨装饰纸表面的三氧化二铝颗粒未被胶膜包裹,上胶量过小或三氧化二铝加量过多及存放期过长。 | 调整浸渍工艺或及时使用 | |
压贴主要外观质量缺陷及形成原因
1.干花也称白花,是产品表面存在的不透明白色花斑,由于浸渍纸的挥发分含量过低、预固化度过高或树脂局部固化过快,树脂流动性差等原因造成的产品表面不透明白色斑痕。造成这种情况的原因也是多方面的:一是贴面用基材检测不严格,表面不平整造成局部压力不均匀;二是基材表面局部预固化层未砂净,板面树脂流展性差;三是压贴用的胶膜纸在浸渍过程中浸胶不匀 ;四是压贴热压温度过高,热压压力过低或不均匀、热压模板表面有污染物;五是由于缓冲垫局部破损(导致压力不均匀);六是由于胶膜纸储存期过长、胶膜纸预固化度过高;七是由于胶膜纸的浸胶量过大。
2. 湿花也称水迹,是产品表面存在的雾状痕迹。产生湿花的原因:一是由于胶膜纸挥发物含量过高,在压贴时排泄不出去而积于板面,或者胶膜纸受潮;二是胶膜纸预固化度过低,热压温度偏低或者热压时间偏短;三是由于基材含水率过高,导致压贴时产生过量水汽。
3. 产品分层鼓泡 分层鼓泡的主要原因有:一是热压温度过高、热压时间过长;二是基材含水率过高或者基材厚度偏薄,压贴中板材芯层产生较大的蒸汽压力;三是基材密度低,板
材抗压性能差或者热压压力过大。
4. 粘模板 粘模板是指压贴过程中板材部分或全部粘在模板上,主要原因有以下几种:一是热压时间短,热压板温度低或局部偏低,使树脂固化不完全;二是基材含水率偏高;三是模板表面不清洁,树脂中无脱模剂或脱模剂失效或涂布不均 ;四是胶膜纸的浸胶量过大,挥发物含量过高;五是热压时板坯定位不准确。
更多推荐
基材,浸渍,造成,表面,工艺,产生,调整
发布评论