德意电器官方网-北京十大顶级别墅排行榜
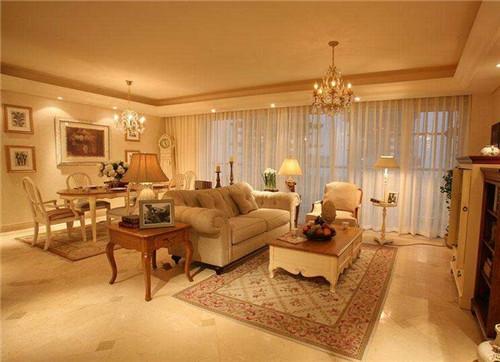
2023年4月10日发(作者:电磁炉牌子排名)
PVC发泡板材知识--⾮常全⾯
⼀、PVC发泡板介绍
PVC发泡板⼜称为雪弗板或安迪板,按制作⼯艺、外观和性能可分为PVC结⽪发泡板和⾃由发泡板。
PVC结⽪发泡板采⽤塞卢卡⼯艺⽣产,表⾯结⼀层硬⽪,光滑平整、硬度⾼、⼒学性能好,并且产品精度⾼、厚度误差
⼩,对模具、配⽅、⼯艺、原材料要求严格。
PVC⾃由发泡板,表⾯疏松,没有结⽪,呈现细密凹凸状⿇⾯,有利于印刷、喷涂、贴⾯,采⽤普通发泡模具即可⽣
产,⼯艺过程相对容易控制。
⼆、PVC发泡板的特点
实践证明,PVC发泡板具有良好的绝热、保温、隔⾳、轻承载等性能,优于其他轻质实⼼塑料膨化珍珠岩、陶粒、⽯棉
制品等保温材料,具有操作简便、机械化程度⾼、节时、省⼯特点。PVC发泡板可⽤机械垂直管道运输,缩短了⼯时,
⽐其他⽅式可提⾼6~10倍⼯效。
采⽤PVC发泡板制做保温层,⽤于屋⾯保温和外墙保温,具有⽆可⽐拟的保温性能以及对于结构层的附着性能,还有⽅
便施⼯、环保、节时、增效等诸多优越性,可以⽤来替代聚苯⼄烯(苯板)等其他隔热材料。我国南⽅地区也使⽤PVC
发泡板制作PVC发泡板砖,以达到屋⾯保温和外墙保温的⽬的。具有如下特性:
1)经济性:综合造价低。
2)保温性:导热系数为0.06-0.070W/(M.K),热阻约为普通混凝⼟的10-20倍。
3)轻质性:⼲体积密度为200-300KG/M3,相当于普通⽔泥混凝⼟的1/5~1/8左右,可减轻建筑物整体荷载。
4)抗压性:抗压强度为0.6-25.0MPA。
5)整体性:可现场浇注施⼯,与主体⼯程结合紧密,不需留界隔缝和透⽓管。
6)低弹减震性:PVC发泡板的多孔性使其具有低的弹性模量,从⽽使其对冲击载荷具有良好的吸收和分散作⽤。
7)施⼯简单:只需使⽤PVC发泡板机可实现⾃动化作业,可实现垂直⾼度200⽶的远距离输送,⼯作量为150—
300M3/⼯作⽇。
8)隔⾳性:PVC发泡板保温板中含有⼤量的独⽴⽓泡,且分布均匀,吸⾳能⼒为0.09-0.19%,是普通混凝⼟的5倍,
具备有效隔⾳的功能。
9)耐⽔性:现浇PVC发泡板吸⽔性较⼩,相对独⽴的封闭⽓泡及良好的整体性,使其具有⼀定的防⽔性能。
10)加⼊⾊母料后,产品可制成多种颜⾊,经耐候配⽅制成后,其⾊泽可长久不变,不易⽼化。
11)可像⽊材⼀样进⾏钻、锯、钉、刨、粘等加⼯,使⽤⼀般⽊材加⼯⼯具即可施⼯。成品可进⾏⼆次热成型及折叠加
⼯,可与其他PVC材料直接粘接。
三、产品不⾜⽅⾯
PVC发泡板有着众多优点,在国外被视为最有潜⼒的“传统⽊材料代替品”,根据适⽤场所的不同,产品的性能也有些不
同。例如“家装PVC板”更注重的是安全环保性能、舒适性能以及特殊环境性能,⽽“商⽤PVC板”更注重的是耐久性能、
经济性能、清洁保养性能。⼈们对PVC发泡板通常认识中的三个误区:
1、阻燃并不是“烧不着”;
有的⼈要拿打⽕机去烧PVC发泡板,看能不能烧起来,烧起来就是不防⽕,烧不起来就是阻燃。这是⼀种常见的误区,
国家对PVC发泡板防⽕等级要求达到Bf1-t0级的标准,根据国家标准不燃材料定为防⽕A级,如⽯材、⾯砖等。Bf1-t0级
阻燃标准的技术内含是直径为10㎜的棉球,蘸上酒精,放置在PVC地板上⾃然燃烧,棉球烧尽后,测量烧坏的PVC地
板痕迹的直径,如⼩于50㎜,就是Bf1-t0级阻燃标准。
2、不环保并不是靠“⿐⼦闻”;
PVC材料本⾝是不含甲醛的,PVC地板在⽣产过程中也不允许使⽤甲醛,⼀些⾼级的PVC发泡板会采⽤全新碳酸钙原
料,刚制作成的产品时会有的淡淡的味道,不会给⼈们的⾝体造成伤害,也不会让⼈感到不舒服。放置通风⼀段时间后会
散去。
3、“耐磨”并不是“⽤利器划不会划坏”;
有的⼈问起PVC发泡板的使⽤寿命与耐磨性时,顺⼿拿出⼩⼑或钥匙等利器,在PVC地板的表⾯去划,有划痕了就认为
不耐磨。其实国家对PVC地板耐磨性测试并不是简单地⽤利器在表⾯划,⽽是由国家检测机构专门测定的。
四、PVC发泡板的性能
1、⼒学性能
PVC发泡板有较⾼的硬度和⼒学性能。并随分⼦量的增⼤⽽提⾼,但随温度的升⾼⽽下降。硬质PVC的⼒学性能好,其
弹性模量可达1500-3000MPa。⽽软质的PVC的弹性1.5-15MPa。但断裂伸长率⾼达200%-450%。PVC的摩擦性⼀
般,静摩擦因数为0.4-0.5,动摩擦因数为0.23。
2、电学性能
PVC发泡板是⼀种电性能较好的聚合物,但由于本⾝的极性较⼤,电绝缘性不如PP和PE。介电常数,介电损耗⾓正切
值和体积电阻率较⼤,耐电晕性不好,⼀般适于中低压和低频绝缘材料。
3、热学性能
PVC发泡板的耐热稳定性⼗分差,140℃即开始分解,熔融温度为160℃。PVC的线膨胀系数较⼩,具有难燃性,氧化
指数⾼达45以上。
五、发泡板⽣产要求
1、⽣产⼯艺流程
硬质PVC结⽪发泡板⽣产⼯艺流程如下:PVC树脂+助剂→⾼速混合→低速冷混→锥双螺杆挤出→⼝模赋形(结⽪发
泡)→冷却定型→多胶辊牵引→切割制品→收集检验。⽣产的硬质PVC结⽪发泡板制品规格为1220mm×2440mm,
制品厚度为8~32mm。
1.2⽣产线布置
2、原材料要求
树脂:PVC⼀般选⽤8型树脂,加⼯时凝胶化速度快,加⼯温度相对较低,产品质量稳定,密度容易控制。近年来很多
⼚家换成5型树脂。
稳定剂:稳定剂的选⽤,考虑到环保且效果好⾸选稀⼟稳定剂,但因价格相对⾼,没有推⼴开来,未来随着环保的要求
⼒度加⼤,稀⼟稳定剂的市场将迎来光辉前景。钙锌稳定剂存在锌烧问题以及稳定效果略差⽤量也较少。⽬前应⽤最多
的还是铅盐稳定剂,发泡板因模具横截⾯宽、流道长且黄发泡分解产热多,要求稳定剂含铅量⾼,稳定效果好,否则制
品容易出现各种问题。
发泡剂:发泡剂的选⽤,发泡剂AC在分解过程中放出⼤量的热,容易导致断⾯中间发黄,这就要求配合⼀定量的⽩⾊
发泡剂,分解起到吸收多余热能的作⽤,要求发泡剂⽬数要⼤,才能做到发泡均匀⽆⼤泡孔。
发泡剂,分解起到吸收多余热能的作⽤,要求发泡剂⽬数要⼤,才能做到发泡均匀⽆⼤泡孔。
调节剂:发泡调节剂,通过多年的研发和改进,发泡调节剂ACR的⼯艺技术越来越纯熟,性能质量越来越稳定,发泡板
根据厚薄,薄板宜选⽤塑化快的,厚板应选⽤塑化慢溶体强度⼤的发泡调节剂。
润滑剂:润滑剂的选⽤遵循初期中期后期润滑兼顾原则,让物料在各个阶段均有润滑剂的保护,坚持长时间稳定⽣产⽽不
析出结垢。
发泡助剂:⽣产中为改善发泡质量和泡沫结构可以少量添加发泡助剂氧化锌,为减少析出可以少量添加硅酸铝。
颜料:为达到更加美观的效果,可以添加钛⽩粉和荧光增⽩剂,为提⾼耐候性可添加抗氧化剂和紫外线吸收剂。
填充剂:选⽤轻质碳酸钙即可,⽆需使⽤活性钙,选⽤以⾼⽬数为主。
3、发泡板配⽅(参考)
4、⼯艺参数的设置
硬质PVC结⽪发泡板的挤出加⼯⼯艺条件⽐常规的PVC管材和型材的加⼯条件苛刻得多。硬质PVC结⽪发泡挤出⼯
艺的关键是发泡剂的分解与成核,⽓泡的成长与固定等过程与PVC熔体的塑化与成型过程相适应。需要严格控制螺杆
转速、挤出温度、压⼒等来实现,同时还跟机头、⼝模、定型模结构有密切关系。
4.1混合⼯艺
由于异向双螺杆挤出机的混合混炼功能弱,因此在挤出之前要设置配料、热混、冷混料⼯序。本⽣产线采⽤SRL-Z系列
热冷混合机组进⾏混料。物料的混合⼯序是⼗分重要的,物料混合质量的优劣将直接影响着挤出成型过程及板材外观与
内在的质量。物料混合温度过⾼或过低,会导致物料提前分解或塑化不良。因此混料程序和温度的控制是混合⼯艺的关
键。⼀般⽣产投料顺序为PVC、稳定剂、内润滑剂、加⼯助剂、填料、外润滑剂、钛⽩娄。投⼊量
约为热混筒有效容积的60%,⾼速热混温度控制在110~120℃范围内进⾏5~10min,冷却混合⽔温在15~20℃以
下,冷混的物料5~10min后在35~40℃时从混合机放出。
4.2挤出⼯艺
1)挤出温度。为获得泡孔致密均匀、表⾯平整光洁的硬质PVC结⽪发泡板材,在⽣产中应严格控制各区间的温度。如
果机筒和螺杆温度过⾼,物料容易提前发泡造成熔体破裂,板材表⾯粗糙;如果温度太低,物料塑化不完全,板材表⾯
不平整;过渡体和模唇的温度应低于挤出温度,但温度太低会使熔体温度过低⽽失去弹性被拉断,温度过⾼会使熔体强
度和弹性降低,泡孔破裂,板材表⾯产⽣空洞缺陷。物料挤出⼀般都经过加热、恒温和保温3个过程。加
热区在挤出机排⽓⼝的前部(即⼀区输送段和⼆区压缩段);恒温区则在排⽓⼝后部(即三区排⽓段和四区计量段);
保温区主要由机头、过渡体和⼝模组成。物料在加热区需要较⼤的热量,该区温度的设定应稍⾼⼀些,以满⾜
迅速补充热量并使机筒温度环境保持稳定的要求;恒温区由于螺杆对物料的剪切和压延产⽣的内热超过物料的需要,故
该区⼀般设置加热与冷却双向温度控制装置,⽤以控制机筒的温度保持恒定,保证物料的正常塑化与挤出成型。物料经
过恒温区后已呈完全塑化状态,该区内热已不存在,为建⽴熔体压⼒需要设置加热⽚补充外热。产品试制发现,适合硬
质PVC结⽪发泡板材⽣产的各区温度:挤出机⼀区(155±5)℃、⼆区(165±5)℃、三区(170±5)℃,四区
(180±5)℃;过渡体(170±5)℃;⼝模(175±5);模唇(175±5)℃;冷却定型装置⼀区恒温控制,⼆三四区冷
却控制,模具各区冷却温度控制在5~40℃。
2)挤出速度及滞留时间。⽣产实践表明,螺杆转速与板材的挤出产量成正⽐,与板材的密度成反⽐。螺杆转速越⾼,
挤出速度快,熔体温升过快增加⼯艺控制的困难,但发泡程度均匀,制品表⾯质量好;相反,螺杆转速过低,挤出速度
慢时,会使熔体塑化不良降低⽣产效率,同时靠近模唇⼝发泡使板材表层粗糙。另外板材质量还受到物料在挤出机筒和
⼝模内滞留时间的影响,滞留时间太短,发泡剂分解不够,板材密度过⼤;滞留时间太长,容易发泡过度板材⼒学性能
降低。螺杆转速应根据结⽪发泡的不同⼯艺⽅法⽽定,需要综合考虑设备的使⽤要求和板材的冷却锯切时间,螺杆转速
和挤出速度根据板材厚度设置不同,⼀般不超过4m/min。本⽣产线的20mm板材挤出速度为0.65~0.7m/min。
3)挤出压⼒。板材发泡成败的关键在于挤出压⼒控制是否合适。螺杆转速、熔体温度及⼝模内流道的长短和压缩⽐对
挤出压⼒都有很⼤影响。螺杆转速增加使熔体挤出压⼒升⾼,可以减⼩泡孔直径增加⽓泡数量,有利于发泡过程。另外
物料塑化良好时,⼝模压⼒和电流都⽐较稳定;⽽物料塑化不良时,⼝模压⼒波动提⾼,电机电流增⼤且不稳。在实际
⽣产中,通常将主机电流和⼝模压⼒的变化作为判断挤出温度控制是否适当的重要依据。
2.2.3机头⼝模及冷却定型模具结构
机头⼝模的流道结构直接影响着制品的发泡倍率和挤出均匀性,进⽽影响制品的质量。本⽣产线⽣产宽幅硬质PVC结
⽪发泡板材,采⽤⾐架式挤出机头结构,机头内部流道组成如图3,由歧管区、扇形区、阻流区和模唇区组成,
熔体流⼊歧管后,被歧管均匀分配到整个扇形区内,保证料流在进⼊模唇区时的同向性,同时为控制⼝模中熔体的压
⼒,设置阻流区降低熔体压⼒,保证料流速度的⼀致。流道各部分长短设计应满⾜特定压缩⽐要求,保证物料不会发泡
过度。
板材加⼯时,由于冷却定型模的结构尺⼨调整成与机头⼝模的相同尺⼨,故结⽪发泡制品的密度和结⽪层厚度取决于⾃
由发泡受限程度,需要适当调节冷却定型模和⼝模之间的距离、挤出速度与定型牵引速度的⽐值及定型模的冷却强度。
5、PVC发泡板⼯艺常见问题及解决办法
PVC发泡板是⼀种具有密闭泡孔结构的板材,具有⼴泛的应⽤,⽽在PVC发泡板⽣产过程中常常会出现破孔现象。青岛
普瑞斯通塑机作为专业的PVC发泡板设备⼚家,根据多年的现场调试⽣产经验,说说其产⽣的常见原因。PVC发泡板截
⾯产⽣破泡或穿泡的主要原因从理论上讲主要为以下两个:
《1》、因熔体本⾝局部强度过低,破泡是由外向⾥形成的;
《2》、因熔体周边压⼒偏⼩,局部泡孔发⽣膨胀,强度减弱,破泡是由⾥向外形成的。
在⽣产实践中,两种作⽤可能同时存在,⼤部分破孔都是局部泡孔不均匀膨胀后,熔体强度降低所致。熔体本⾝强度过
低与熔体周边压⼒偏⼩的因素很多,概括起来,主要表现在以下七个⽅⾯。
A、熔体热稳定性差,挤出温度设定或控制不当
熔体良好的塑化是PVC发泡板制品的前提条件。如果热稳定剂存在问题,挤出温度过⾼,容易发⽣熔体局部降解且会因
熔体强度降低,⽓泡过⼤⽽被撕裂;挤出温度过低、熔体⽋塑化、强度很低,同样会出现破泡。PVC发泡板⽣产时,⼀
定要定期对稳定剂进⾏180~200度的稳定性能检验,不符合稳定性能要求的原料不得使⽤或经调整剂量,检验合格后再
⽤。
除保证熔体在挤出过程中不发⽣降解外,稳定剂还有⼀个重要的职能,即调节发泡剂分解温度。如果稳定剂加量过多或
过少致使发泡剂分解温度过低或过⾼,都不利于发泡。稳定剂应根据采⽤树脂的牌号进⾏调整,⽐如采⽤8型树脂,塑
化温度较低,稳定剂应适当增加,以便物料塑化温度与发泡剂分解温度相吻合。但若稳定剂添加过多或熔体温度过⾼,
⼜会致使发泡剂在挤出机内提前分解,致使发泡⽓体从加料孔与真空孔逸出,若稳定剂添加过少或操作温度过低,⼜会
使发泡不完全。
解决⽅案:挤出操作时,除保证熔体良好塑化外,挤出机内的熔体温度⼀定要低于发泡剂分解温度,防⽌发泡剂在机内
过早分解;出⼝模的熔体温度⼀定要达到发泡剂的分解温度区域,以利于充分发泡。挤出温度的设定和控制,还应根据
真空孔物料和开机时熔体成型形态,及时进⾏对应调整。确保物料在通过排⽓孔时基本呈橘⽪状态,螺杆底部不应有粉
料流动;熔体从⼝模挤出时表⾯应光滑,有⼀定的弹性,不得⼀出⼝模就下垂或截⾯结晶粗糙。
B、分⼦量或聚合度过低
PVC树脂⼀般根据其聚合⽅法可分为乳液法PVC和悬浮法PVC及本体PVC三种。⽣产硬质PVC发泡产品时,如采⽤乳
PVC树脂⼀般根据其聚合⽅法可分为乳液法PVC和悬浮法PVC及本体PVC三种。⽣产硬质PVC发泡产品时,如采⽤乳
液法PVC树脂可得到泡孔均匀,表⾯光滑的制品,但制品的尺⼨稳定性难以控制;且乳液法PVC树脂⽣产的成本较⾼;
若采⽤悬浮法PVC树脂,产品的外观质量和泡孔均匀度稍差。
综合⼯艺、价格及性能等⽅⾯,宜将两者按⼀定⽐例混⽤,⽐例可以为80/20-20/80之间。板材成型横截⾯积较宽,从
挤出机头进⼊⼝模要分布到⼀个相当于1.3⽶左右的宽度,要得到充分发泡的低密度塑料制品,采⽤的树脂粘度不宜过
⾼,为了有利于⽓泡的分散与膨胀,板材整个横截⾯压⼒协调⼀致,对熔体流动性要求⾼。若PVC树脂粘度过⾼,熔体
流动性差,板⾯平整度难以保证,泡孔不易扩张,导致发泡倍率低;反之,若PVC树脂粘度过低,⼜会致使熔体强度
低,容易引发破泡。
解决⽅案:⽣产结⽪PVC发泡板宜选⽤SC-7性树脂,尽量不要选⽤SC-8型树脂,或采⽤SC-8型树脂与SC-5型或SC-6
型树脂混⽤。
C、发泡剂添加不当
PVC发泡板⽣产⼀般采⽤发热型、吸热型或吸热、放热复合平衡型三种不同发泡剂。偶氮⼆甲酸铵,亦称AC,属于偶
氮基化活化物。AC发泡剂分解温度⾼,达232℃,远远超出PVC加⼯温度,使⽤时需降低分解温度。
放热型发泡剂发泡率⾼,约190-260ml/g,分解速度快、放热极⼤,但发泡时间短,突发性也强。因此当AC发泡剂⽤量
过多时,发⽓量过⼤,会使⽓泡内压⼒增长快,泡孔尺⼨⽣长过⼤,急剧释放⽓体,使泡孔结构破坏,泡孔⼤⼩分布不
均,乃⾄形成开孔结构,会在局部产⽣较⼤的⽓泡和空⽳。⽣产发泡塑料制品时,放热型发泡剂AC不得单独使⽤,应
和吸热型发泡剂配合使⽤或采⽤发热与放热平衡复合型化学发泡剂。⽆机发泡剂-碳酸氢钠(NaHCO3)属吸热型发泡
剂,虽发泡率较低,但发泡时间长,和AC型发泡剂混⽤,可以起到互补和平衡的作⽤。放热型发泡剂提⾼了吸热型发
泡剂的发⽓能⼒,吸热型发泡剂⼜使前者冷却、稳定其分解和均衡释放⽓体,抑制厚板内部过热降解,减少残留物析
出,有增⽩作⽤。
解决⽅案:在不影响发泡率前提下,可适当多添加吸热型发泡剂,取代部分放热型发泡剂,以抑制多添加放热型发泡剂
引发的破泡。1232或BLA-616发泡剂属放热与吸热平衡型发泡剂,分解⽆诱导期,分解速率快,10分钟左右即可达到
最⼤发⽓量,放⽓缓、⽆突发,最⼤发⽓量达156mL。其分解温度介于PVC加⼯温度范围内,可⽤于尺⼨较厚,形状复
杂的制品动态成型过程,以利消除破泡,保证发泡性能的稳定。
D、模具使⽤不当
结⽪PVC发泡板⽣产,根据制品厚度不同,配置的⼝模平直段长度和压缩⽐也有所不同。厚板⼝模因发泡层较厚,有弹
性变形空间,⼀般设计的⼝模平直段较长,压缩⽐较⼤,以便提⾼熔压和发泡倍率;薄板⼝模因发泡层较薄,弹性空间
⼩,刚性较⼤,⼀般设计的⼝模平直段较短,压缩⽐较⼩,以防⽌因熔压过⼤。
如果使⽤不当,⽣产薄板,误⽤厚板⼝模,则因出⼝模料流动阻⼒增⼤,出料不均,造成表⾯不平整、熔体强度降低,
甚⾄板材被拉断,⽣产周期减短;⽣产厚板,误⽤薄板⼝模,则会因出⼝模熔压偏⼩,使泡孔增⼤⽽引发破泡。
解决⽅案:不同厚度结⽪PVC发泡板⽣产前,⼀定要正确选⽤⼝模。
E、加⼯调节剂质量差或剂量不⾜
物料在发泡过程中,发泡剂分解的⽓体在熔体中形成⽓泡。这些⽓泡中存在着体积⼩的泡孔向体积⼤的泡孔扩展的趋
势。⽓泡的⼤⼩和多少不但与发泡剂的添加量有关,还与聚合物熔体强度有关。强度太低,⽓体扩散到熔体表⾯后容易
逸出,⼩⽓泡相互合并形成⼤⽓泡。⽽发泡调节剂的长分⼦链缠绕粘附在PVC的分⼦链上,形成⼀定的⽹状结构。⼀⽅
⾯促进物料塑化,另⼀⽅⾯提⾼PVC熔体强度,使发泡过程中泡孔壁能够承受泡孔内⽓体的压⼒,不致因为强度不⾜⽽
破裂。发泡调节剂可以使产品泡孔⼩⽽多,泡孔结构更均匀、合理,⼤⼤降低发泡体的密度。发泡调节剂质量差或加量
不⾜会导致发泡体强度低,出现破泡或串泡。
应该指出的是不同⼚家⽣产发泡调节剂分⼦量、粘度有很⼤不同,当发泡制品出现破泡或串泡,采⽤其他⽅法处理⽆效
时,另⾏更换发泡调节剂或适当增加剂量,往往会产⽣明显效果。但增加或更换分⼦量更⼤的发泡调节剂,会因粘度过
⼤,使得熔体中的⽓泡⽆法扩展,⽽使产品密度提⾼。并会因熔体粘度过⼤,流动性变差,导致⼝模出料不均,影响板
⾯平整,甚⾄⽣产时间不长,发⽣⼝模糊料故障,尤其是⽣产10mm厚以下板材时更易发⽣。
解决办法:⽣产不同厚度板材时,加⼯调节剂剂量也应视情况有所不同,同⼀配⽅,薄板没有泡孔,厚板出现泡孔时,
可适当多添加0.3-0.5份加⼯调节剂,仅以消除破泡为基准,微量添加,切忌不计后果,盲⽬多加,以免增加制品密度,
影响有效⽣产时间。
F、碳酸钙加量过多、粒度过⼤、活性不好
CaCO3加量太多时,虽然能形成更多⽓泡核,但如果碳酸钙加量过多或颗粒过⼤,活性不好,形成团聚,在树脂中分
散或与树脂截⾯结合不好,导致熔体强度降低,熔体中⽓泡扩展时容易产⽣破泡。
解决办法:PVC发泡板⽣产⼀定要严格控制碳酸钙剂量、粒度与活性。当碳酸钙加量过⼤时,发泡调节剂也应相应增
加。
G、板材截⾯发泡或出料不均匀,局部缺料
板材截⾯发泡或出料不均,局部缺料影响因素较多,贯穿于混料与挤出全过程。例如配⽅组分不合理,外滑太少,挤出
机5区温度易超温,从⽽致使合流芯温度⾼,板材中间出现⼤泡、串泡,发黄,板材表⾯粗糙等缺陷;单锅混料量过
多,混料温度太低、混料时间过短,内滑添加过少,易致使混合料组分分散不均。流动性差及挤出⽣产过程中⼝模温度
或螺栓调节不当,都会导致熔体从⼝模挤出时,出料不均匀,局部缺料,引发发泡熔体从薄弱环节膨胀⽽破泡。因此在
混料和挤出⽣产过程中⼀定要执⾏配⽅和⼯艺操作规程,并对破泡进⾏对应分析,分别采⽤不同⽅法处理。如果破泡⼀
直固定在同⼀位置,说明该部位熔体压⼒过低,采⽤⼝模螺栓或温度进⾏对应调整,即可解决。
除以上对应措施外,调整各段定型模板间隙差也对消除泡孔有⼀定作⽤。如果第⼀块定型板与第⼆块定型板间隙差过
⼤,会因没有经过充分冷却熔体在定型模板压⼒下被挤压的更紧密,致使密度增加并会产⽣破泡;如果第三块模板与第
四块模板间隙差过⼤,因经过充分冷却熔体,模板间已没有压缩变形余地,导致第四块模板难以到位,板材厚度增加。
⽽适当增加第⼆块与第三块模板间隙差,⼀⽅⾯可以有效防⽌发泡熔体在没有冷却前发⽣破泡,另⼀⽅⾯第三块模板在
⼀定温度下,也可以压到位,防⽌板材厚度加⼤。其次,⽣产厚板时,适当降低螺杆温度、⼝模油温、第⼀块定型装置
冷却⽔温等,也对消除破泡有相应效果。
六、塑料发泡产品各类质量缺陷类型与处理措施
发泡板材截⾯出现泡孔质量缺陷原因和处理措施:
发泡板材表⾯出现泡孔,是熔体局部密度过低的表征。⼀般出现的泡孔有条孔和圆孔两种表征,影响因素中有树脂、发
泡剂、调节剂、碳酸钙、稳定剂等原料因素,也和模具及⼯艺有关。
若发泡制品表⾯出现⼤⾯积泡孔,可适当调整发泡调节剂处理;如在发泡板表⾯偶尔出现个别泡孔,很可能和混料未按
混料程序、温度、加料程序办事,致使混料不均有关,应换料处理;如连续出现圆形泡孔,应适当调整黄⽩发泡剂剂
量;如发泡板表⾯时⽽出现长条泡孔,属于板⾯局部密度低的表征,原因⽐较复杂,应依据发⽣泡孔的时间、部位和概
率,从⼯艺上采取措施处理:
措施:
发泡板材表⾯出现的⽩带、暗带、浅灰带、亮带等质量缺陷原因和处理措施:
发泡制品表⾯出现⽩带,即发⽣在和板材挤出同⼀⽅向的⽩⾊直纹,是⼝模和⽩带对应部分板坯和定型板⾯直接接触、
摩擦的表征,⽩带和暗带不同点是两者与定型模板接触、受到模压程度有所区别。灰⾊是⽩带滞留物开始发⽣降解的表
征;亮带是板坯直接和定型接触、摩擦的表征。
原因:
1)⼝模和⽩带对应截⾯间隙设置偏⼩,导致流量偏⼩,熔体从⼝模挤出时厚度稍微减薄,经过定型板时未和定型板接
触摩擦出现的⽩带。
2)物料中夹杂不洁杂质,在⼝模中发⽣滞留,导致熔体从⼝模某部位挤出时流量减少⽽出现⽩带,尤其是添加不洁再
2)物料中夹杂不洁杂质,在⼝模中发⽣滞留,导致熔体从⼝模某部位挤出时流量减少⽽出现⽩带,尤其是添加不洁再
⽣料或组分复杂、稳定剂⽋缺的再⽣料过多,熔体从⼝模某部位挤出时产⽣滞留。若⽩带问题处理不及时,随时间延
长,⽩带将逐渐转变成浅灰带与⿊带。
3)挤出机控制温度不当,未使⽤螺杆温控装置,物料在挤出机、合流芯或⼝模挤出时截⾯温度不均衡,发⽣局部微降
解、粘料,熔体从⼝模挤出时,在⼝模某部位流速少出现⽩带。经实践验证:这和⼀些企业采⽤的3区温度、4区、5
区、合流芯温度逐渐升⾼有⼀定对应关系。
4)挤出机、合流芯或⼝模某部位存在滞留区,导致⼝模某部位流量减少,出现⽩带。
5)混合料未达到混料温度即出料,或混料未按规定程序与单埚混料量超标,致使混料组分不均,熔体从挤出机挤出产
⽣流动速度紊乱。
措施:
以上七项处理措施中第⼀、⼆、七项是事前预防措施,第三、四、五、六项是应时处理措施。当开机时出现⽩带,⼀般
都是⼝模间隙或温度设定不当造成的,及时处理即可见效;当开机⼀段时间,发⽣⽩带,基本上是合流芯、⼝模腔、挤
出机内发⽣滞留物造成的,如采⽤调整模⼝间隙和温度⽅法⽆效,应及时停机,千万不可盲⽬持续调整,以免延⼯误
时,造成更⼤浪费。停机后认真检查⼝模、合流芯中是否黏附滞留物,如未发现异常,需进⼀步检查螺筒中是否黏附滞
留物并调整挤出机轴向与径向间隙。
⼤量实践验证,处理⽩带有⼀定时效性,若处理不及时或由⽩带演变未灰带,就会失去处理良机。处理时应对挤出机螺
杆磨损和装置情况及近期⼯艺设置变动情况了如指掌,以便有的放⽮应对处理。
亮带是由于⼝模间隙调整不当,导致亮带处物料从⼝模挤出时速度增快,与⼝模发⽣直接摩擦所致,⽐较容易解决,适
当调⼩模唇对应亮带部位间隙即可。
可能有⼈认为:板材某部位出现⽩带并⾮密度低所致,出现亮带也并⾮密度⾼所致,依据是凡是⽩带对应⼝模位置熔
体,出定型模板后,⽐周围部位厚⼀些;亮带对应⼝模位置熔体,出⼝模后,⽐周围部位薄⼀些。故处理⽩带采取紧模
⼝⽅法,处理亮带松模⼝⽅法。其实处理措施恰好相反。凡是密度低的部位,经过定型模板时,未和定型模板紧密接
触,得不到充分冷却,收缩量⼩,⽽周围密度⾼部位熔体,经冷却后出现表⾯收缩,并在定型模板压⼒作⽤下,有向⽩
带部位移动倾向,⽽经冷却出定型模板后,⽩带部位就稍显厚⼀些;凡是密度⾼部位,熔体经过定型模板时,和定型模
板接触紧密,冷却充分,收缩量⼤,并在定型模板压⼒作⽤下,有向周围密度低部位移动倾向,因此经冷却后,出现亮
带的部位就稍显薄⼀些。
发泡板材易拉断等质量缺陷原因和处理措施:
原因:发泡板材⽣产中被拉断主要因素是:熔体塑化不良;强度差;操作不当、牵引速度过快或过慢,熔体通过⼝模和
定型板时承受的压⼒或阻⼒过⼤;碳酸钙过量;再⽣料稳定性差、添加量过⼤;上料罐断料等导致的流动速度紊乱等。
措施:
发泡板材厚度厚薄不均质量缺陷原因和处理措施:
原因:熔体塑化不好与出模速度差异⼤,或模腔、合流芯黏附了⼤量析出物造成的。⼀般是板⾯出现⽩带、泡孔的后发
结果。
措施:
影响板材密度的因素与降低熔体密度质量缺陷原因和处理措施:
影响发泡板材密度因素很多,既有发泡剂、发泡调节剂、稳定剂、碳酸钙、润滑剂等原材料添加不当等⽅⾯因素,也有
挤出温度、熔压、牵引速度、⼝模与定型模板之间间隙、模芯和模唇温度、定型模板之间间隙等设置不当等⼯艺⽅⾯因
素。从理论上讲,降低熔体密度有两⼤措施:⼀是添加发泡剂必须有⾜够的发泡体积和适宜的强度,⼆是定型模板提供
素。从理论上讲,降低熔体密度有两⼤措施:⼀是添加发泡剂必须有⾜够的发泡体积和适宜的强度,⼆是定型模板提供
的空间应和发泡体积相适宜,两者之间能够相互平衡。如果发泡体积不⾜,定型板提供空间过⼤,即发泡体⼩于定型板
提供发泡空间,板⾯则会不平整。反之发泡数量过⼤,定型板提供空间过⼩,即发泡体⼤于发泡空间,随发泡体承受熔
压增加,则会影响发泡,密度相应也会偏⾼;调节剂添加量过多,虽然能减少破孔,提⾼密度,但如果过量容易使发泡
困难,影响发泡。
措施:
调整时应根据⽣产所需板材质量要求,按照程序由简到繁,由⼯艺到配⽅,由减量到加量进⾏逐项对应调整。值得注意
的是:调整提⾼发泡率,降低板材密度时应按⽣产发泡板的需要各有侧重。以上许多调整措施,譬如调整措施
4)5)7)8)等都是以牺牲结⽪硬度和光亮度等情况,不可过之⽽不及,仅仅为降低密度⽽不考虑结⽪硬度和光亮度。
影响塑料发泡板出现波浪纹、云纹、横向和竖向条纹质量缺陷原因和处理措施
因素:主要和定型板压⼒、⼝模出料不稳,挤出速度与牵引速度之间相互不匹配等综合因素相关。譬如熔体从⼝模挤出
后,进⼊定型模板阻⼒过⼤,会发⽣褶皱或波浪纹;熔体出⼝模局部出料快,在模板整体压⼒作⽤下,则会形成⼩波
浪;牵引速度过慢时,在模板整体压⼒下,则会形成⼤波浪;熔体板坯从⼝模挤出后局部流速不稳,在定型模作⽤下会
产⽣云纹;板坯从⼝模挤出速度过快或牵引速度过慢,板坯进⼊定型模时受到横向挤压,则会形成横向条纹;在同样牵
引速度条件下,熔体从模⼝挤出局部出料速度不稳,⼝模出料多部分熔体进⼊定型模后,受到竖向挤压,则会形成竖向
条纹。
措施:
发泡板糊料质量缺陷原因和处理措施:
糊料,即板材表⾯局部出现变⾊、烧焦症状。⼀般发⽣在密度较⾼的薄板上,也是发泡体黏度与阻⼒过⼤的副产物。随
发泡剂调节剂量增⼤,发泡率降低,⼝模唇间隙减少,熔体流动阻⼒增⼤,熔体在某部位发⽣局部堵料、滞留,便会产
⽣糊料。凡是影响熔体流动性和稳定性因素都和糊料有直接关系。糊料⼀般发⽣在⼝模,与发⽣在定型模内析出有所不
同。
熔体在挤出过程中因混合料稳定性差,各段温度设定或控制不当,发⽣分解;或挤出机磨损严重,合流芯、⼝模腔存在
滞留料黏附等原因发⽣糊料。
措施:
发泡板芯层强度低质量缺陷原因和处理措施:
发泡板芯层强度低质量缺陷原因和处理措施:
原因:由于结⽪发泡板熔体从⼝模挤出后经过充分冷却,⼝模与定型模板间隙值和第⼀块定型板与第⼆块定型板间隙差
偏⼤;⼝模油温与预冷板及第⼀块定型板⽔温差偏⼤等原因导致结⽪发泡板⽪层硬度⾼,从⽽将同样密度发泡板⼤多数
泡孔集中到芯层,导致芯层密度、强度及硬度偏低。
措施:
发泡板出现杂质和⿊⾊斑点质量缺陷原因和处理措施:
原因:
1)再⽣料落地,回收不洁。
2)再⽣料中掺杂有糊料。
3)挤出⽣产过程中排⽓孔中出现冒料未及时处理。
4)混合料未进⾏封闭存放。
措施:
发泡板出现划痕质量缺陷原因和处理措施:
原因:主要是熔体在加⼯过程中,熔体经过时被擦伤所造成的,或混合料中混杂有铁屑等硬性物质,将合流芯与模具表
原因:主要是熔体在加⼯过程中,熔体经过时被擦伤所造成的,或混合料中混杂有铁屑等硬性物质,将合流芯与模具表
⾯划伤。
措施:
发泡板出现扭曲、不平整质量缺陷原因和处理措施:
翘曲度是结⽪发泡塑料板材⼀项重要外观质量指标。QB/T2463.2-1999⾏业标准规定:当板材厚度⼤于5mm时,其翘曲
度应⼩于或等于10mm/m(毫⽶每⽶);当板材厚度⼩于5mm时,其翘曲度应⼩于或等于5mm/m(毫⽶每⽶)。但对于
橱柜、酒柜、卫⽣洁具等家具⽽⾔,⼀些微⼩翘曲,在⼤⾯上将会导致家具严重⾛形,因此企业⼀般对翘曲度的检验要
求也⽐较严格。
原因:主要是板材熔体内聚集的应⼒不均造成的。⽣产时在定型模板和牵引装置冷却、定型、拉伸约束下,体现不出
来,但在牵引以后,熔体处于⾃由状态时,其内应⼒得以释放,才会以翘曲变形形式表现出来。结⽪发泡塑料板翘曲变
形主要表现在横向与纵向两个⽅向。其中横向翘曲变形主要是⼝模横向给料量或温度设定不均及⼝模油路、定型模板⽔
路局部堵塞,板材横截⾯油冷及⽔冷不均所致,由给料多、熔压⼤、温度⾼的⼀⾯向给料少、熔压⼩和温度低的⼀⾯弯
曲;纵向翘曲变形主要是挤出机径向和轴向间隙偏⼤,致使挤出过程中螺杆在熔体作⽤下,向上偏移,进⼊合流芯与⼝
模下部的熔体偏多;⼝模分流锥分流不均、⼝模温度设置不当、⼝模与定型模上下不对中等原因,致使出⼝模熔体偏流
严重;⼝模与定型模相互不在⼀个⽔平线上,由受⼒⼤⼀侧向受⼒⼩⼀侧弯曲;各道定型模纵向上下冷却不均,由温度
⾼⼀⾯向温度低⼀⾯弯曲。
结⽪发泡塑料板发⽣翘曲变形的原因虽然简单,但由于板⾯幅宽较⼤,且PVC流动性较差,微⼩应⼒不均都会从板⾯平
整度上体现出来,因此出来难度较⼤,调整的“度”很难把控。为了使整个横向熔体出料均匀⼀致,在设定和调整⼝模横
向间隙和各区温度时,需要根据PVC的流动性,随偏离⼝模中⼼距离⼤⼩,⼝模间隙和温度逐次提⾼,但也要防⽌“矫
枉过正”。假如⼝模唇中间间隙过⼩或⼝模唇两侧间隙过⼤与⼝模唇中⼼温度偏低,两侧温度偏⾼,中间熔体流速过
低,两侧熔体流速过⾼,亦会产⽣板材中间低、两侧翘曲的现象。
在挤出机与合流芯连接部位设置多孔板,以调整、均衡挤出⼝模的熔体压⼒。多孔板的设置应以挤出型坯具有⾜够的熔
压为准绳,控制好多孔板的孔径与孔数。孔排列要紧凑、均匀,流通截⾯约占多孔板总⾯积的50%-70%,板壁不宜太
厚。设置多孔板仅仅是为了恒温时,多孔板的流通截⾯空间可取上限,以减少多孔板的反作⽤⼒。
板⾯在⽣产时发⽣弯曲⼤部分原因都是挤出机径向或轴向间隙磨损过⼤或⼝模分流锥、燕尾型分流道磨损后分流不均所
致。正确解决措施应从两⽅⾯着⼿处理。对于挤出机新安装螺杆与螺筒及新进⼝模⼀定要严格验收,防范不合格产品投
⼊⽣产,以便把事故隐患消灭在萌芽状态。除设置多孔板外,其他处理措施均是机械应急措施。在处理弯曲故障时,各
种措施⼀定要综合利⽤,不可过多单⽤某⼀种措施,以免调整过量。同时以上处理措施势必会给板材增加⼀定内应⼒,
是以牺牲板材内在质量保证外观质量的不妥之举,建议尽量不⽤或少⽤。
总结:以上各类发泡板尽管质量缺陷表现形式各异,譬如出料不均形成的各类缺陷,所采取处理措施都有⼀定的共性,
只不过处理程序和幅度有所不同;在⼀个相互依存、制约的⽣产系统内,它们之间也存在⼀个相互作⽤和制约关系。譬
如泡孔、密度、不平整等质量缺陷,都和熔体黏度、流动性、阻⼒⼤⼩有关。若熔体黏度过低,局部熔压不均,会引发
泡孔,并使板材密度升⾼;黏度过⾼,会使泡孔发得很⼩,亦会影响板材密度与流动性,使板⾯不平整;⼝模唇间隙
⼤,挤出阻⼒⼩,有利于稳定⽣产,但会使板材密度升⾼;⼝模唇间隙⼩,熔压⾼,会降低板材密度,但随挤出阻⼒增
加,亦会影响其流动性,易使板⾯不平整。解决某⼀项质量缺陷,必须兼顾、防范与其相关的另⼀项质量缺陷,不可矫
枉过正,顾此失彼。应通过⽣产实践,反复摸索,寻找质量缺陷之间平衡点和临界点,在不影响板材相关质量缺陷的前
提条件下,掌握好调整的“度”,较好解决某⼀个质量缺陷。根据发泡板材厚度、密度要求和各类制品质量缺陷对应关
系,分别采取不同措施:即采⽤不同配⽅、⼝模与⼯艺,实施按需分配,微量调整,平衡配置,则是综合解决以上各类
问题的最佳⽅式。
发泡剂专家:
更多推荐
5mm厚pvc板材价格
发布评论