2023年12月22日发(作者:钟兆琳)
制壳耐火材料新秀 —— 熔融石英
—国外精铸技术进展述评(5)—
原载《特种铸造及有色合金》,2005(5):294~298
熔融石英在精铸中应用虽然已有相当长的历史,但以往主要用作陶瓷型芯,用作型壳则主要用于面层,背层很少使用。这种状况近10 年来在美、欧各国有很大改变。2001年美国著名耐火材料生产厂商 Minco 公司,公布了对美国熔模铸造行业制壳耐火材料使用现况的调查[1]统计数据,各种耐火材料消耗量所占比例的大致如下:
铝-硅系耐火材料55%、熔融石英30%、刚玉9%、锆石6%
可见在美国精铸业中,熔融石英异军突起,在精铸制壳耐火材料的使用量中,已仅次于铝-硅系材料,远远超过锆石等其他耐火材料,迅速成为制壳耐火材料的一枝新秀。
一.熔融石英与铝-硅系材料的比较
2000 年美国Minco Inc.在美国第48 届精铸年会和INCAST 2001(3) 发表的论文,对熔融石英和铝-硅系耐火材料进行了全面的分析对比。主要结果如下:
331)型壳重量 熔融石英密度2.2g/cm,铝-硅系材料约2.7g/cm,故同样厚度型壳,前者重量[1][2]明显轻于后者,有利于减轻工人劳动强度和机械手操作。
[1][2]2)热膨胀率 图5-1 和图5-2 所示分别为脱蜡和焙烧过程中,这二种材料热膨胀率的比较。热膨胀系数小是熔融石英的一个很大的优点,有利于减小加热时,型壳内外因温度差造成的热应力,因而有利于防止脱蜡和焙烧过程中型壳开裂和变形。同时,对提高铸件尺寸精度甚为有利。所以,尺寸精度要求高的产品,就更适合采用熔融石英。
[1][2]
图5-1 脱蜡过程中二种材料热膨胀率的比较
图5-2 焙烧过程中二种材料热膨胀率的比较
3)力学性能和透气性 表5-1所列为二种材料制得型壳的力学性能和透气性比较,结果显示,[1][2]湿强度和断裂韧度,熔融石英型壳稍低于铝-硅系型壳,但透气性却远高于铝-硅系型壳。
4)高温抗蠕变能力 当采用熔融石英撒砂料代替硅酸铝时型壳高温抗蠕变能力提高(图5-3)[1][2]
。熔融石英在高温下(约1200℃)结晶化转变可作为这种现象的一种解释(图5-4)。
表5-1 熔融石英和铝硅系材料型壳性能比较
试样名称
型壳材料
室温抗弯强度 /MPa
断裂韧度 /MPa
断裂指数
-102透气性 /10 cm
A
熔融石英粉+
30/50# 熔融石英砂
3.98
5009
0.0167
18.3
B
莫莱卡特粉+
16/30# 莫莱卡特砂
4.11
5299
0.0166
8.6
C
熔融石英粉+
16/30# 莫莱卡特砂
3.37
4223
0.0155
18.2
20
图5-3 不同材料在高温下变形量的比较
图5-4 熔融石英型壳在加热过程中的相变
5)脱壳性 容易脱壳和清理是熔融石英迅速崛起的最重要原因。不同材料型壳残留强度试验[1][2]结果见表5-2。可见熔融石英型壳残留强度大大低于铝-硅系材料。这是因为熔融石英在≈1200℃高温下会转变为方石英。实践证明,在浇注温度下,型壳中大约有70%熔融石英[2]转变为方石英。当型壳温度下降至300℃左右,方石英又由高温型转变为低温型,同时体[7]积骤变(图5-4),无数裂纹随之产生,型壳强度剧降,脱壳性随之明显改善。此外, 对于全铝-硅系型壳来说,如采用碱煮、碱爆等化学清理方法,碱液只能溶解粘结剂中的二氧化硅,对耐火粉、粒料却无能为力。但对熔融石英型壳来说,无论粘结剂还是耐火材料,碱液都有强烈的腐蚀作用。试验表明,在质量分数50%KOH溶液中沸腾碱煮,全熔融石英型[2]壳经109分钟就大部溶解,而铝-硅系型壳则看不出有什么变化。所以,采用熔融石英,也有利于碱煮、碱爆等化学清理。减少耗碱量,提高效率。
表5-2 熔融石英和铝-硅系型壳残留强度对比 (MPa)
型壳系统 经1037℃,保温1h 焙烧 经1204℃, 保温1h 焙烧
熔融石英料浆+30#/50#熔融石英砂 11.8 13.6
铝-硅料浆+16#/30#铝-硅砂 42.6 65.2
熔融石英料浆+16#/30#铝-硅砂 31.4 34.6
6)充型难易 当温度低于600℃,熔融石英热导率较铝-硅系材料差(图5-5),而比热容[2]
21
量又只有锆石的一半, 这些因素都有利于薄壁铸件的充型。但温度高于600℃,由于熔融石英透明度高,(夜间浇注时,甚至可透过型壳看见其中流动的钢液),因此辐射散热快,铸件冷却快,更容易获得健全致密的铸件,这对于浇注铝合金薄壁精铸件甚为有利,但同时铸件产生裂纹的趋势会有所增加。
图5-5 二种材料的热导率比较
与铝-硅系耐火材料相较,尽管熔融石英有着上述诸多优点,但毕竟价格较贵,是否采用,各厂家审慎行事。至于如何使用?是用于面层,还是用于背层;是单独用,还是与其他材料混合用;是用作粉料,还是用作撒砂料;都需要依本厂具体情况而定,才能获得理想效果。
二.熔融石英和锆石的比较
Minco Inc.发表于2002 年美国第50 届精铸年会的论文,对用于精铸面层的二种主要耐火材料——熔融石英和锆石进行了全面的分析对比。作为面层耐火材料,锆石具有如下优点:
1) 锆石粉粒度分布宽,一般无需级配,配制成的涂料浆流变性就很适合涂料,料浆覆盖性、流平性均属一流。此外,由于密度大,空料时涂料浆流淌快。
2) 锆石砂粒形好,多为球形(图5-6),流动性好,容易充填蜡模上的孔洞、凹槽等部位,故也很适合作为面层撒砂料。
正因为如此,长期以来以锆石为精铸型壳最佳的面层材料,已成为国内外精铸界业内人士之共识。但它也有以下缺点
1) 经常发生周期性货源短缺,供应紧张,价格较贵;
2) 由于锆石是天然矿产,所以,含有某些有机物和其它杂质在所难免。其中有的(特别是Fe2O3、磷酸钙等)会和涂料中的粘结剂、添加剂或其它耐火材料反应,造成涂料浆pH值改变而迅速老化变质,铸件表面也容易出现硅酸铁黑褐色斑疤或丘疹。
3) 由于环保法规越来越严格,近来,美、欧各国普遍更加关注锆石中放射性元素可能造成的环境问题。
与此对应,熔融石英具有如下优点:
31) 每吨熔融石英的价格就比锆石便宜,加上密度又比锆石低得多(前者2.2g/cm,后者4.7~34.9 cm),所以,用熔融石英代替锆石,可显著降低制壳成本。
2) 熔融石英原材料经过精选,再经电弧重熔,并剔除方石英,因此杂质少,纯度高。所以,涂料浆稳定性不成问题。实践证明,熔融石英-硅溶胶涂料稳定性通常可长达一年以上。
3) 高温晶化,低温相变,使铸件表面容易清理。
毋庸讳言,熔融石英也存在以下缺点:
1) 粉料粒度分布范围通常较窄,配制成涂料的涂挂性差,再加上密度小,不利于流淌、滴落;由于熔融石英涂料浆透明度高,使操作者难于识别涂层厚度和均匀程度。
2) 熔融石英砂粒形为多角形(图5-6),再加上密度小,容易架桥,形成浮砂。
采用熔融石英作面层耐火材料需要特别注意它的适用范围。从热力学角度考虑,在高温条件下,某些金属和合金元素会和二氧化硅反应,例如,航空结构件的重要合金材料IN-718[6]
22
中的铌就会与二氧化硅起反应,置换出硅而污染合金。此外,许多高温合金中都含有铝、钛或鉿、锆和镧等高活性强化元素,在浇注温度下也都有和二氧化硅反应的可能性。但从动力学角度考虑,还存在一个反应速度问题。
用熔融石英粉配制面层涂料,浇注普通碳钢和低合金钢最为稳妥。也可按适当比例和锆石粉混合浇注不锈钢。但对于含有钛、铌等高活性元素的不锈钢应慎用。一些精铸厂家认为,由于熔融石英的主要化学成分是SiO2,用它作面层材料浇注不锈钢,可能会催生黑色硅酸铁麻点或斑疤。 铸件表面一旦出现此类缺陷,防止钢液和铸件氧化是有效的应对措施。值得一提的是,由于在浇注温度下,锆石也很容易分解成ZrO2和SiO2,所以,即使采用锆石作面层材料,此类缺陷也同样时有发生。改用刚玉作面层材料才是较为彻底的解决办法。
三.国内推广应用熔融石英的迫切性和现实性
日前,由于种种原因,锆石正面临周期性货源短缺,供应紧张,价格一路飚升,令许多精铸厂家叫苦不迭。采用硅溶胶粘结剂后,型壳残留强度偏高,脱壳性差,难清理,许多铸件不得不增加化学清理工序,又造成新的环境问题。然而,国外早已相当流行的制壳材料熔融石英,国人却几乎无人问津,这不能不说是跟普遍存在的一个认识上的误区有关,这就是将制壳用和制芯用熔融石英(又称石英玻璃)混为一谈,总认为它的价格贵,无法承受。其实不然,尽管二者之间无论化学成分和晶体结构无异,但由于对型芯的耐火度和化学稳定性的要求比型壳严格,所以,对杂质含量(特别是Bi、Ag、Sb、Sn、Pb、Zn等)的要求不同(见表5-3和[7][8]表5-4)。正因为如此,二者价格相去甚远。目前,制壳用熔融石英粉,国内市场价大约为3000~4000元(人民币)/吨,国外市场价也不过约7000元(人民币)/吨,比锆石粉便宜得多,加之密度小,如能代替锆石,经济效益不言而喻。如能换来铸件脱壳、清理的优质高效,用作背层材料也不失为一种选择。
表5-3 美国Minco公司制壳用熔融石英粉的化学成分 (质量分数,%)
SiO2
>99.7
A12O3
<0.17
Fe2O3
<0.035
TiO2
<0.025
表5-4 制芯用熔融石英(石英玻璃)的化学成分 质量分数,%)
SiO2 A12O3 TiO2 MgO CaO Fe2O3 K2O Na2O
<0.01
Bi、Ag、Sb
<0.001
Sn、Pb、Zn
<0.015
K2O
<0.012
CaO
<0.0075
Na2O
<0.005
>99.8 <0.25 <0.25 <0.5 <0.06 <0.05 <0.02
注:表中数据适用于普通真空熔铸硅基陶瓷型芯。
近来国内某些精铸生产厂家的试验和经验证明,使用熔融石英型壳,钢液容易充型,脱壳性确实明显改善,好清理,代替锆石经济效益显著。与此同时,也存在以下问题值得注意:
1. 熔融石英粉配成涂料的流变行为不理想,流淌性、流平性、覆盖性等均不如锆石粉涂料,粉液比也不易达到期望的水平。由于熔融石英透明度高,涂挂模组过程中,操作者不易判断涂层厚薄和均匀程度。这些问题可考虑通过以下途径解决:
1)
改变搅拌方法,先快搅,后慢搅。
2)
合理级配粉料粒度。美、欧大量试验研究表明,熔融石英粉与硅溶胶配制涂料时,较[3][4][5]适合的粉料级配是270#或320#细粉50%,200#和120#粉料各占25%。
3) 涂料浆中加入少量钛白粉,以降低涂层的透明度,方便涂挂。
4) 采用聚合物增强硅溶胶,并添加少量改善流平性的附加物。
由此可见,推广应用熔融石英,还需要得到粘结剂生产厂商的大力支持和密切配合,国外也常有熔融石英与某种合适的粘结剂捆绑销售的做法。
2. 作为面层撒砂,由于熔融石英砂粒形为多角形(图5-6),不利于蜡模上精细部位挂砂,再加上密度小,砂粒容易架桥,形成浮砂,处置不当,浇注时容易造成钢液渗漏。对此,
23
可适当减小撒砂粒度,用70#/120#砂代替50#/100#砂;目前国产熔融石英砂中,粉尘含量高(见图5-7),也是产生浮砂的重要原因。不难看出,制订精铸用熔融石英砂/粉的产品质量标准也是当务之急。采用聚合物增强硅溶胶,也有利于减少浮砂。
图5-6 熔融石英砂(左)和锆石砂(右)的粒形对比
图5-7 进口(左)和国产熔融石英砂(右)
粉尘含量对比
3. 温度/湿度变化对型壳质量的影响,比其他耐火材料更为敏感。因此,对上述工艺条件的控制要求更严格。
4. 由于熔融石英在1200℃附近转变为方石英,随后,冷却至300℃左右产生相变。所以,型壳焙烧后应尽快浇注。如果工艺要求必须二次焙烧,则焙烧温度务必低于1000℃。
5. 由于熔融石英热膨胀系数小,铸件尺寸可能会变小。
6. 若只用熔融石英作面层耐火材料,就有可能与背层材料的膨胀率不匹配,造成型壳焙烧时,面层涂料层龟裂。
综上所述,熔融石英用作制壳背层材料,在技术上难度较小,用作面层材料,则需要下点功夫。熔融石英作为一种制壳材料,在我国推广应用尚属新生事物,需谨慎从事,一切通过试验,防止大起大落。
参 考 文 献
1
2
3
4
5
6
7
8
Jerry D. Snow & David H. Scott Minco, Inc. Comparing Fused Silica And Alumino-Silicate Investment
Refractories. INCAST , 2001(3): 24~27
Jerry D. Snow & David H. Scott .Comparison Fused Silica to Alumino-Silicates in Water Based Shell Systems.
Investment Casting Institute: 48th Annual Technical Meeting,
USA,
2000, No.17.
Ronald S. Doles. The Characterization Of Fused Silica Backup Slurries Using A Three Factor Simplex Centroid
Design. Investment Casting Institute: 45th Annual Technical Meeting,
USA, 1997, No9.
Tom Branscomb. Effect Of Fused Silica Flour Particle Size Distribution On Slurry And Shell Properties.
INCAST, 2002(4):16~17
Jeffrey C. Niles. The Effect Of Particle Size Of Fused Silica Flour On Shell Properties. Investment Casting
Institute: 45th
Annual Technical Meeting, USA,
1997 No10
Jerry D. Snow, David H. Scott and Bill S. Snyder. Permeable Prime Coats: Effect On Dewax Shell
Cracking. Investment Casting Institute 50th Technical Conference & Expo
, USA, 2002, No.17:1
佟天夫,陈 冰,姜不居. 熔模铸造工艺. 北京:机械工业出版社,1991. 381,389~390
《航空制造工程手册》总编委会. 航空制造工程手册:发电机叶片工艺. 北京:航空工业出版社,1997. 163
24
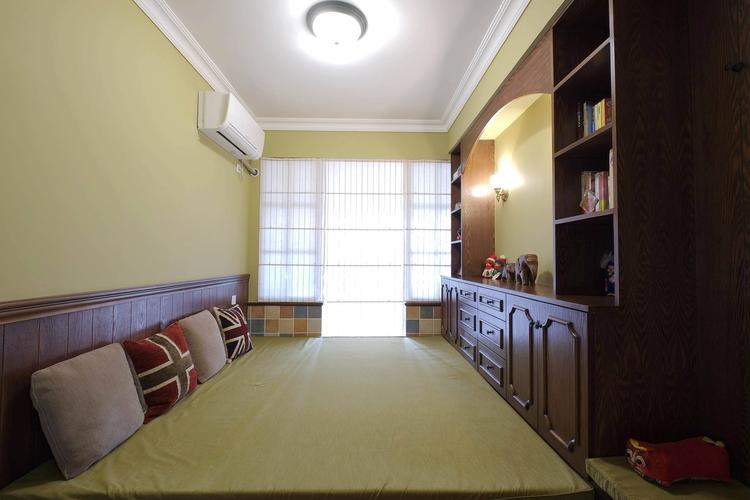
更多推荐
熔融,材料,锆石,面层,铸件,涂料,精铸,浇注
发布评论