2023年12月24日发(作者:甘维文)
车床床头箱加工工艺编制
任务:完成如图2— 1所示车床床头箱箱体机械加工工艺规程的制订 仲小批量)
床头箱设计图纸如图2-2所示。
图2-1
1
r
J
1
f
L.
1
15
■ 2 甘 ■t =3D 亍
* 60
「
n
IW 20
298 ± CL 30
<
、
、
--•
q
>
c
4
<=>
、4-M8
深
15
0
--------- 7 ------------
T
/—X r
+1
、
/1.5
/
45
45
、
V J
Ml 6X1r 5-7H
通
■!
1
J
一
335 •:
B
v->
z
CN
2扌5滦】0
〔込贷)
oo
4
B
80
A y
C
I" ±0. 3Q 0 155 ±0. 30
Q_p|//|»K |C
♦ IM
I … ■ ■■"■・■ ■■<
二
D
O
taij m
L 锄
I
丄
|0
•咛
|E|~
/ / /
1
20范国
LJJitis
内
|c
12#
-——
I
〃z “
*115
@B,
c12D±D. D27
135
E
3-MS滦12均布
f>A
3-M5淡12均+审
W0+I89L
深
3T46 12 /
(68.94〕
130
60
------
—
一
«.«1$
E
L• 05
£
87
355
80
B-B
2O
技术要求
1•铸件圆角R5-R8;
2. 铸件不得有铸造缺陷;
3. 铸件粗加工前后均需进行人工时效处理;
图2-2
第一节零件图分析
一、床头箱的功用和特点:
箱体类零件时机器及其部件的基础件之一。它将一些轴、轴承、套、齿轮等 零件装配在一起,使其保持正确的相互位置关系,并按规定的运动关系协调动作, 完成某种远动。因此,箱体类零件的加工质量对机器的精度、性能和寿命有着直 接关系。车床床头箱的功用如上述所示,其特点有许多精度要求不同的孔和平面 组成,内部结构比较简单但壁的厚薄不均匀,加工的难度较大。
、床头箱的技术要求:
床头箱的主要技术有:1.三对轴承孔的尺寸精度为IT7,表面粗糙度Ra值 为1.6um,三对同轴轴承孔轴线间的平行度公差为 0.025mm①100j7、①115j7
轴承孔轴线的同轴度为 ①0.01,箱体内壁对 ①105、①80公共轴线的垂直度为 0.015,①100端面对 ①100轴线的垂直度为0.015 ;表1 — 1是床头箱箱体的主 要加工技术要求。2.铸件不得有铸造缺陷;3.铸件粗加工前后均需进行人工时效 处理;
表1 — 1床头箱箱体的主要加工技术要求
要求内容 数值 要求内容 数值
1、①62轴承孔 4、①47轴承孔
直径 ① 62 (+0.028,-0.018 ) 直径 ① 47 (+0.024,-0.015 )
粗糙度 Ra1.6
粗糙度 Ra1.6
其对基准C的平行度 ①0.025
2、①100轴承孔 5、①25孔
直径 ① 100 (+0.022,-0.013 )
直径 ① 25 (+0.033,0)
其轴线对基准F的同轴度 ①0.015
其对公共轴线同轴度 ①0.01
其端面对基准E的垂直度 Ra1.6
3、①115轴承孔 6、对合面
直径 ① 115 (+0.022, -0.013) 直线度 0.015
其对公共轴线同轴度 ①0.01 其对基准A的垂直度 0.015
其端面对基准D的垂直度 0.015 粗糙度 Ra3.2
粗糙度 Ra1.6
第二节确定毛坯
按技术要求床头箱箱体的材料是 HT200,其毛坯是铸件。铸铁容易成型、切 削性能好、价格低廉,并且具有良好的耐磨性和减振性, 也是其它一般箱体常用 的材料。铸件毛坯的精度和加工余量是根据生产批量而定的。对于单件小批量生 产,一般采用木模手工造型。这种毛坯的精度低,加工余量大,其平面余量一般 为7〜12mm,孔在半径上的余量为8〜14mm。在大批大量生产时,通常采用金 属模机器造型。此时毛坯的精度较高,加工余量可适当减低,则平面余量为 5〜
10mm,孔(半径上)的余量为 7〜12mm。为了减少加工余量,无论是单件 小批生产还是成批生产,均需在三对轴承孔位置在毛坯上铸出预孔。表 2—2是 应用查表法得到的小批量手工砂型铸造时减速箱箱体的毛坯尺寸公差及机械加 工余量。另外,在毛坯铸造时,应防止砂眼和气孔的产生;应使减速箱箱体零件 的壁厚尽量均匀,以减少毛坯制造时产生的残余应力。 由于零件的结构复杂,壁 厚也不均匀,因此,在铸造时会产生较大的残
余应力。为了消除残余应力,减少 加工后的变形和保证精度的稳定,所以,在铸造之后必须安排人工时效处理。人 工时效的工艺规范为:加热到500C〜550C,保温4 h〜6 h,冷却速度小于或等 于30C
/h,出炉温度小于或等于200E。人工时效的方法,除了加热保温法外, 也可采用振动时效来达到消除残余应力的目的。
表2—2床头箱箱体毛坯尺寸公差及机械加工余量
项目(mm) 机械加工余量(mm) 尺寸公差(mm) 毛坯尺寸及公差
箱体长度 2 (± 1) 367 ± 1
6
箱体宽度 3 (± 1.5) 342 ± 1.5
6
箱体高度
6
3 (± 1.5) 287土 1.5
第三节定位基准的选择
床头箱箱体加工定位基准的选择 定位基准可分为粗基准和精基准,通常先
确定精基准,然后再确定粗基准。
1、 粗基准的选择 一般箱体零件的粗基准都用它上面的重要孔和另一个相距 较远的孔作为粗基准,以保证孔加工时余量均匀。床头箱箱体加工选择以重要表 面孔①115J7及①110J7为粗基准,通过划线的方法确定第一道工序加工面位置, 尽量使各毛坯面加工余量得到保证,即采用划线装夹,按线找正加工即可。
2、 精基准的选择 一般箱体零件常以装配基准或专门加工的一面两孔定位, 使得基准统一。床头箱箱体的轴承孔轴线应在对合面上,与底面也有一定的尺寸 精度和相互位置精度要求。为了保证以上几项要求,加工底座的对合面时,应以 底面为精基准,使对合面加工时的定位基准与设计基准重合; 箱体装合后加工轴 承孔时,仍以底面为主要定位基准,并与底面上的两定位孔组成典型的一面两孔 定位方式。这样,轴承孔的加工,其定位基准既符合“基准统一”的原则,也符
合“基准重合”的原则,有利于保证轴承孔轴线与对合面的重合度及与装配基准 面的尺寸精度和平行度。
第四节拟订工艺路线
一、加工方法的选择
加工方法选择原则是根据零件的加工面技术要求、工件材料、结构尺寸、生 产类型等,选择即满足零件加工质量的要求,又高效、经济的加工方法。
床头箱体材料为HT200 ,生产纲领为小批量,床头箱体的主要加工面是轴承孔和平面(包 括底面和槽)。其中:平面加工方法有车、刨、铳、磨;孔的加工方法有车、镗、钻等。但 是箱体类零件平面加工较少用车削, 因为车床主要用于加工回转类工件, 箱体类零件在车床
上装夹不方便。根据各种方案的经济加工精度(查工艺手册)
1底面平面度要求,主要表面分别选择如下:
5级精度0.015,粗糙度Ra1.6 (刮平)。因平面度要求高, 并考虑生产效率,最终加工采用划线找正,车比铣更方便按划线找正,同时此床 头箱的尺寸较小,
粗加工采用车。 有考虑到底面与方槽侧面的垂直度的要求, 在 半精加工时底面与方槽一次装夹加工。加工方案:车—刨—磨(粗、精磨) 。
2孔①110J7与基体阶梯孔 ①115J7圆柱度0.008,直径尺寸精度7级,粗
糙度 7 级,空轴线与底面及方槽有 4 级精度的平行度要求。 此为同轴承孔的加 工,加工深度较深, 最为经济、方便的加工方法为镗, 同时精镗能满足精度要求, 因为加工精度相对较高,在加工阶段划分及工序安排上重点考虑平行度的要求。 加工方案:粗镗—精镗。
3方槽两侧面间距尺寸精度 7级,直线度要求为 5级,垂直度精度要求为 8
级,粗糙度 Ra3.2 。方槽因其形状限制,加工方法为刨和铣最为方便,但直线度 要求高,所以采用刨削。 另外在工艺装备中, 可采用成形刀精刨保证尺寸精度要 求。加工方案:粗刨—宽刃精刨。
4 箱体两侧面间距尺寸精度 8 级,相对各自端孔轴线的圆跳动为 0.03, 7 级
精度要求,粗糙度要求为 Ra3.2 。两表面加工精度要求一般,铣、车均可采用
,
从箱体零件外形及定位安装方面考虑
,选用铣削。
加工方案:粗铣—精铣。
5孔6x①13定位孔尺寸精度要求为7-8级精度,表面粗糙度为 Ra12.5。此孔
直径较小,粗糙度要求不高,因而采用钻孔。但钻孔的精度较低,因而加工时要
采用合理的定位方法保证 ①13孔的位置精度。加工方案:钻。
6所有螺纹孔M8深15-20mm,粗糙度要求为Ra12.5,以及通孔 ①6.8等。
精度要求较常规,直径较小,可采用一次性钻孔并攻丝。若用需配作加工的孔, 则等待与其它零件装配后加工。
二、 加工阶段划分 加工阶段主要根据零件质量要求、结构尺寸级生产纲领来划分。 床头箱为小批量生产, 可以不严格划分, 这里根据以上各表面加工方案的选
择,部分表面的精度和表面质量要求较高, 因而将床头箱零件的加工过程分成两 个阶段,即:
粗加工阶段—去除各表面上的大部分加工余量, 为重要表面最终加工做好准 备,同时穿插部分的基准面的精加工,完成不重要表面的加工,如钻孔等。
精加工阶段—达到零件上各个表面的设计要求。
三、 工序及加工顺序安排
1 工序的集中和分散:
选好加工方法, 确定加工方案后, 进行工序安排。 工序的集中和分散也与生 产类型有关,对小批量的生产类型, 外形结构较复杂的床头箱, 为减少装夹次数, 方便生产组织,提高生产率,应使工序适当集中。
2 加工工序的安排:
加工工序安排遵循“先基后其他、先主后此、先面后孔”的原则,根据前面 所做的零件图分析、定位基准的选择、加工方案的分析,进行工序安排:
◊车基准平面
第一道切削加工工序以划线找正加工, 先加工平面基准——底面。 但是, 考虑底 面是很重要表面, 且平行度要求高, 以毛坯顶面为安装面影响加工精度, 所以先 加工顶面,再以加工后的顶面为安装面,加工底面。
◊
刨方槽 方槽也是重要的基准面,因而要安排在镗轴承孔前加工。
◊
粗铣侧面及粗镗轴承孔
箱体前后两侧面相对轴承孔有圆跳动要求, 考虑以平面为定位基准较以定位装夹 更为方便可靠, 因而安排前后侧面加工工序于轴承孔前。 并且, 铣两侧面可以与 镗孔在同一机床上加工,这样可以进行工序合并,减少搬运次数。
◊
钻孔、攻丝 在精加工前完成钻孔等相对次要的表面加工,使重要表面的终加工在最后工序, 保证加工后精度不受影响。对于各表面的螺孔,钻孔、攻丝、倒角应一次装夹定 位完成,因而尽量在螺孔所在表面终加工完成后在钻孔。顶面的螺纹孔 2xM8 , 即通孔06.8与轴承孔为交叉孔,先加工会影响轴承孔的加工精度,需要在轴承 孔加工完成后再加工。 其他面的螺纹孔为 5组分布在不同表面, 是具有对称的均 布螺纹孔,采用钻模钻孔。
◊
精加工阶段
精加工阶段是底面、 轴承孔以及前后端面的终加工, 与前同样道理, 安排基准平 面先加工, 孔后加工。最后精加工序, 有端面铣、 镗阶梯,有相互位置公差要求, 应合并工序,
一次装夹加工。 另外,对于箱体前后端的螺孔, 应在铣平面后加工。
◊
热处理
毛坯为铸件, 因而铸造后需进行时效处理; 铸件完成粗加工阶段后, 为保证高精 度要求表面的质量, 在粗加工后精加工前再安排人工时效处理。 主要工序安排好 后,还有检验、去毛刺等辅助工序,也要根据生产情况进行合理安排。
四、工艺路线拟定
床头箱体加工工艺路线: 铸件毛坯—时效处理—划线—粗车底面及顶面—刨 顶面,粗、精刨方槽至设计要求—粗铣前后两侧面—粗镗轴承孔—时效处理—钻 定位孔6x013—磨顶面及底面一精镗轴承孔、精铣两侧面一钻螺纹孔并攻丝一 检、入库。
第五节 加工余量、工序尺寸和公差的确定
一、列出各表面加工工序
底面:车—刨—人工时效—磨(粗磨、精磨) 顶面:车—人工时效—磨
孔0110J7:粗镗一人工时效一半精镗、精镗 阶梯孔①115J7:粗镗一人工时效一半精镗、精镗
方槽:粗、精刨,
二、以①110J7轴承孔为例介绍镗削加工中加工余量、工序尺寸和公
差的确定
①110J7轴承孔加工工序:粗镗一半精镗一精镗,
计算粗加工余量:Z粗(直径)=(毛坯余量-粗镗余量)=(9-4) =5mm
半精镗、精镗后应达到设计要求: ①110 ( +0.022、0)
粗镗后孔的基本尺寸:110-2x2=106mm 直径①106 mm
毛坯孔径的基本尺寸:106-5=101mm 直径 ①101 mm
按各工序经济精度确定各工序尺寸公差,各工序尺寸偏差按“如题原则” ,毛坯 公差按“双向”标注,如下:毛坯孔: ①101土 3.5 mm粗镗孔:306( +0.5、0) mm 精镗:①110
(+0.022、0) mm
第六节选择机床与工艺装备
一、机床设备的选用
单件小批量加工时,一般选用通用机床;单件小批量高精度加工时,可选用 加工中心(详见第十节);在大批生产条件下可选用通用机床加专用夹具,也可 选用高效的专用设备和组合机床。 减速箱箱体加工时机床设备的选用见表 2—5。 B665牛头刨床可刨削最大长度
650mm;
Z3050
Z3040
x
Z3040
x
Z3050
X
Z3063
X
Z3080
Z30100
X
Z30125
X
12/1 16/1
40
6/1
50
20/1
63
X25
80
31
100
40
125
最大钻 孔直径
mm
40
主轴中 心线至 立柱母 线距离
最大
最小
mm
mm
1250
350
1600
350
1600
350
2000
450
2500
500
3150
570
4000
600
主轴端 面至底 座工作 面距离
最大
最小
主轴行 程
mm
mm
mm
1250
350
315
4#
1250
350
315
4#
25-200
0
16
0.04-3.
20
16
1220
320
315
5#
25-2000
16
1600
400
400
5#
25-160
0
16
0.04-3.
20
16
2000
550
450
6#
16-125
0
16
0.04-3.
20
16
2500
750
500
6#
8-1000
22
2500
750
560
Metrie80
6.3-800
22
主轴锥 孔(莫氏)
主轴转 速范围
主轴转
速级数
主轴进 给量范 围
主轴进
r/min
25-200
0
16
0.04-3.
20
16
mm/r 0.04-3.20 0.06-3.2 0.06-3.2
给量级
16 16 16
数
工作台
尺寸
主轴箱
水平移
动距离
主电机 功率
500 >63 500 >63
mm
0 0
500 >630
630
X0 800
X0
0
1550
00
2000
800
X250 800
X250
mm 900 1250 1250 2580 3400
kW
3
-
3
-
-
-
3500
4
-
-
-
3500
5.5
-
-
-
7000
7.5
-
-
-
11000
15
-
-
-
20000
18.5
-
-
-
28500
套筒升 降距离
主轴箱
倾斜度
-
-
kg 3000
滑座移
动距离
机床重
量
机床外 型尺寸 (长2150
X
2500
X
2500
X07
3080
X
3730
X
4780
X63
5910 >200
mm
070
X
2840
070
X
2840
0
X
2840
250
X
3291
400
X
4025
0X
4600
0
X
5120
X宽X
高)
M7132
2njDLjkJ.r;rji/
M7132主要参数
主要技术规格
工作台
工作台面尺寸(宽X长)
单位
M7132/F
mm
mm
320X
1000
320X
1000X
400
最大磨削尺寸(宽X长X高)
工作台纵向移动量(液动)
工作台速度(无极调速)
工作台T形槽槽数
工作台T形槽宽度
工作台负载量(含电磁吸盘)
电磁吸盘尺寸(宽X长)
磨头
磨头横向进给(无极调速)连续
磨头横向进给(无极调速)断续
手轮每转磨头进给量(垂直)
垂直进给手轮最小刻度值
砂轮尺寸(外径X宽度X内径)
电机功率
电器设备总容量
磨头电动机功率
磨头电动机转速
mm
m/min
mm
mm
kg
mm
200-1110
3-25
3
18
624
320X
1000
m/min
mm
mm
mm
mm
0.5-3
3-30/stroke of table
0.5
0.01
巾
350X
40X
巾
127
KVA
KW
r/min
14
7.5
1440
工作精度
加工表面对基面的平行度
工作表面粗糙度
mm
卩m
300:0.005
Ra0.63
整机参数
机床外形尺寸(长X宽X高)
包装箱外形尺寸(长X宽X高)
mm
cm
kg
3000X1782X2057
286X
175X
236
~
4000/4500
争重/毛重
M7132卧轴矩台平面磨床 产品说明
本机床全面贯彻国家标准。适用于机械制造行业钢件、铸铁及有色金属等各 种金属零件的平面磨削,也可用砂轮端面磨削沟槽和侧边。特点:,磨床工作台 纵向移动和磨头横向移动为液压传动, 无级调速;磨头垂直进给为手动,配有快 速升降机构,能减轻劳动强度,提高工作效率。工作台导轨粘贴聚四氟乙烯轨软 带,耐磨性好,能耗低;磨床垂直进给导轨粘贴聚四氟乙烯软带, 进刀灵敏度高; 横向导轨采用镶钢导轨,横向精度好;机床床身采用热对称设计,热变形小;利 用回油加热床身导轨,导轨直线度变化小;机床运动平稳、性能可靠、噪音低、 精度稳定、操作方便。
X62W
X62W主要参数:
规胳
Specifics tiofi
工作台面积{傀耗媒) Bench area(wid Prt鱼军犬%向行音才功/忸动 Longitude trav白 1 (man nual/Hutomgllc) 丄一作台•天横向行称于功f忸动 Max transv^r&B travel (manvaF/e utc^matic) 壬柞舍罩大垂直行桎 手动f机动 Maj< v^nical iravEil (man uat/suloniatic) H作令第大回鹤桶廈 1 Max ralary angl$ t轴中心线至工柞台面间的距■ Distance between &f>incUe and benah lace 费轴妆速毀散 Spindle speed grads 单程 Un4t mm mm rTim mm Param&ier 320 x 1400 700/6&0 25S/240 320/300 土 45* 1 SpFecifiic^tiQn 主抽较谜堆IT Spindle sp^e&ct 工卄台进蛰■扱瞰「 " Fe^d grade oi bench 主倍动电动机功雜 Main moior pov/er 进蜓电动机功串 Fesd motor powsr 机矗外徳尺寸E J Ove-rall gize (length x width x hoiqht) Unrt 1 转 J# I _Parametef 30-1500 18 * Kw Kw mm ”」'」U・2I3一 kg l 7.5 1-5 ?294 x 1?7D k 1610 mm 机床置・ — -------------------- Weigh[ 18 30/350 2650 T68 中国第一台卧式镗床 ------ T68型 1956年,新中国第一台卧式镗床 ------- T68型卧式镗床在沈阳中捷友谊厂 T68主要参数 型号 主轴直径 主轴锥孔 工作台面积(L B) 主轴轴向行程(w) 主轴箱垂直行程(y) 工作台横向行程(x) 工作台纵向行程(z) 平旋盘滑块行程(u) 主轴转速 平旋盘转速 进级量级数 主轴每转主轴箱和工作台的进给范围 主轴每转主轴的进给量范围 平旋盘每转刀架的进给量范围 平旋盘每转主轴箱和工作台进给量范围 主轴箱、工作台的块速移动速度 主轴的块速移动速度 平旋盘滑块速移动速度 主轴允许最大扭矩 平旋盘滑块速移动速度 主轴允许最大扭矩 平旋盘允许最大扭矩 最大切削抗力 最大进给抗力 工作台最大负载 主电机功率 T68 85mm 莫氏5号 1000x800mm 600mm 755mm 850mm 1080mm 170mm 20〜1000r/min(18 级) 10〜200r/min(14 级) 18级 0.025~8mm 0.05~16mm 0.025~8mm 0.05~16mm 2400mm/min 4400mm/min 1200mm/min 110kg-m 1200mm/min 110kg-m 220kg-m 1300kg 1300kg 2000kg 6.5/8kw 机床重量 外形尺寸(长x宽x高) 11000kg 5075x2345x2730mm 二、工艺装备的选用 工艺装备主要包括刀具、夹具和量具。在工艺卡片中应写出它们的名称, 如 “键槽铣刀”、“镗模”、“塞规”等(一般普通常用的可不写)。 床头箱体的主要加工工艺是个轴承孔的镗削加工及侧面的铣削加工。 此工序 可设计如图2— 1的专用夹具,该夹具主要由压板1、垫板2、定位销3、底板4 构成,校正后紧固在工作台上。具体使用方法是:工件加工好的底平面放于专用 夹具的垫板2上,并以夹具上两个定位销3为定位基准插入工件上上道工序已加 工好的2个工艺孔中,由于2个工艺孔的形位精度和尺寸精度较高, 这样就可以 将工件精确定位在夹具上,同时用垫板2上的二个螺栓与其余二个 ①17孔配合, 上紧螺母,为提高装夹刚度,再用夹具上四个压板1压紧工件,这样就将工件牢 牢地固定在夹具上。 1、压板2、垫板3、定位销4、底板 图2— 5铳端面、镗轴承孔专用夹具 第七节确定切削用量和时间定额 一、切削用量计算 以①110轴承孔镗削为例介绍切削用量计算如下: 1、工步1—粗镗 (1)背吃刀量的确定 粗镗余量为5 mm可一次走刀加工完成,所以ap= Z粗/2=5/2=2.5 mm (2) 进给量的确定 查表《机械制造工艺设计简明手册》 P151表4 .2 — 21卧式铣镗床主轴进给量, 选取 f=0.52mm/r (3) 镗削速度的计算 查表选取 v=50m/min,由 n=1000v/ 二 d=1000X 50/ 二 x 106=150.2r/min 选主轴转速n=150r/min,求得该工步的实际镗削速度为 v=n二d/1000=150x二x 106/1000=49.9 m/min。 2、 工步2—半精镗 (1) 背吃刀量的确定 半精镗余量为3.4 mm,可一次走刀加工完成,所以ap= 3.4/2= 1.7mm (2) 进给量的确定 查表选取f=0.37mm/r (3) 镗削速度的计算 查表选取 v=60m/min,由n=1000v/ 二 d=1000x 60/ 二 x 109.4=174.6r/min 选主轴转速n=175r/min,求得该工步的实际镗削速度为 v=n二d/1000=175x二x 109.4/1000=60.1 m/min 3、 工步3—精镗 (1) 背吃刀量的确定 精镗余量为0.6 mm,可一次走刀加工完成,所以ap= 0.6/2= 0.3mm (2) 进给量的确定 查表选取f=0.15mm/r (3) 镗削速度的计算 查表选取 v=60m/min,由n=1000v/ 二 d=1000x 60/ 二 x 110=173.7r/min 选主轴转速n=175r/min,求得该工步的实际镗削速度为 v=n二d/1000=175x二x 110/1000=60.4m/min。 二、时间定额的计算 时间定额的计算参考本书第一章,在此不再详述。 第八节编写工艺文件 表3-3箱盖机械加工工艺过程卡 机械加工工艺 过产品型 LK32 零件图号 20011 程卡 号 产品名 数控 零件名称 床头箱 共1 第1 页 页 称 车床 材每毛坯可 1 每台件数 1 备 HT200 毛 铸件 毛坯 料注 坯 外型 制件数 牌号种 尺寸 类 车 工 设备 工艺装 备 工时 工序 工序内容 工 名称 间 段 准 单 终 件 序 号 10 20 铸造 清砂 铸造毛坯 清除浇注系统、冒口、型 砂、飞边、飞 刺等 人工时效 喷涂底漆 1.以直径115毛坯孔为 基准,找正,垫平。兼顾 尺寸20,划出底面加工线, 并打上样冲眼。 2.以底面加工线为基准, 划出顶面加工线(兼顾尺 寸18),打上样冲眼。 1.底面放平在工作台上, 用划针盘找平四周线条互 平,加紧,车顶面至图。 2.工件翻身,顶面吸平工 作台面,夹紧,粗车底面 至工序图尺寸。 1.工件以顶面6件一组 放平在工作台上,按线校 正,夹紧,刨底面及 110 定位槽至工序图。 1工件以底面放在铣夹具 中,槽侧面V 2靠实定位 块面,压紧工件,铣尺寸 355两侧面,控制 135,30 两尺寸。 2.工件以底面为基准,放 在夹具中,A面靠实夹具 上两定位块面,压紧工件, 铣尺寸335两侧面,控制 两端壁厚35,30两尺寸。 1.工作台上放上两定位 块,拉定位块面与工作台 纵向导轨平行三0-01,压 紧两定位块。 2.工件以底面为基准,放 在工作台上,A面靠实两 定位 块面,压紧工件,按 铸 铸 30 40 50 热处 理 油漆 划线 铸 铸 金 60 粗车 金 70 刨削 金 B2010A 80 端铣 金 X63WT 90 粗镗 金 T618 工序图粗镗各孔至工序图 尺寸要求。 100 平磨 110 铣斜 面 120 铣 1.工件顶面吸工作台面, 校金 正,平磨底面至工序图 尺寸要求。 1.工具置于铣夹具中压 紧,金 按工序图铣至尺寸要 求。 1.工件以底面为基准,放 在金 工作台上,V 2靠实两 定位块面,压紧工件,按 工序图铣至各尺寸要求。 1.工件以底面为基准,槽 A金 侧面靠实定位面,压紧 工件,精镗三轴孔至工序 图各尺寸要求。 1.工作台上放两定位块, 用金 百分表拉两定位侧面与 横向工作台导轨平行三 0-015mm,压紧定位块。 2.工件底面清理干净,以 底面为基准,横放在工作 台上,侧面靠实两疋位块 面,压紧工件按工序图要 求钻,扩,铰至尺寸要求, 孔口倒角1X45度。 1.以110X4槽为基准,钻 金 模底面4X直径13孔,并 刮平孔口直径28X1和4 —M8螺底孔位直径 6.8X15 深及 M16X1.5 螺 底孔为直径14.5通,同时 刮平孔直径30.,各孔口倒 角0.5X120°,分别攻丝 M8X12 深,M6X1.5 通。 2.模钻顶面8-M8螺底孔 为直径6.8X20深,各孔口 倒角0.5X120 ° ,攻丝 M8X15 深。 M7140H X63WT X63WT 130 精镗 T618 140 镗 T618 150 钻1 ZW3725 160 钻2 1.模钻右端上 4-M6与 3-M6螺底孔为直径5X20 深,各孔口倒角 0.5X120°,攻丝 M6X15 深。 金 2.模钻左端面上 3-3-M6 螺底孔为直径5X20深, M20X1.5螺底孔为直径 18.5通,各孔口倒角 0.5X120 ° ,分别攻丝 170 检 180 入库 M20X1.5 通,M6X15 深。 3.钻左右端孔口直径 7X60。斜孔至工序图尺 寸要求(回油孔)。 r综合检查 金 清洗,上油,入库 设计 审核 标准 会签 (日 (日 期) 化 (日 期) (日 期) 期) 标 处 更改文 记 数 件号 签 日 标 处 更 签 日 字 期 记 数 改 字 期 文 件 号 第九节零件的检验与质量分析 一、 加工后的检验 表面粗糙度检验通常用目测或样板比较法,只有当 Ra值很小时,才考虑使 用光学量仪或作用粗糙度仪; 孔的尺寸精度:一般用塞规检验;在此因是中小批生产,可用内径千分尺或 内径千分表检验。 平面的直线度:可用平尺和厚薄规或水平仪与桥板检验; 平面的平面度:可用自准直仪或水平仪与桥板检验,也可用涂色检验。 同轴度检验:一般工厂常用检验棒检验同轴度; 孔间距和孔轴线平行度检验:根据孔距精度的高低,可分别使用游标卡尺或 千分尺,也可用块规测量,在这里使用游标卡尺进行测量; 三坐标测量机可同时对零件的尺寸、形状和位置等进行高精度的测量,在某 些精度较高的场合可以使用。 二、 床头箱体加工质量分析 1、夹紧变形分析 箱体粗镗时由于切削力比较大,必须将箱体压紧。在较大的夹紧力作用下, 夹紧部位的工件形状出现变形,影响加工精度。精镗时,为了避免夹紧变形影响 孔的加工精度,在精镗之前需放松对被加工箱体的夹紧, 使变形消失于精镗余量 之中,然后再均衡,轻轻压紧进行 精镗,以提高孔系的加工精度。 由于箱体壁薄,所以当夹紧力过大或夹紧力的着力点不恰当或压铁不平稳 时,都会使工件出现夹紧变形,虽加工时尺寸已量准,但加工后撤去夹紧力,工 件便恢复原状,影响已加工好表面的精度,所以夹紧力要恰当,力应作用于主要 基面上,作用于工件刚性大的地方,如夹紧在箱体的边缘实体或有筋板的地方。 2、 切削变形分析 箱体金属分布不均,会引起较大的切削变形。如果是连续走刀完成该孔的粗 精加工,加工后就会出现“倒锥”(入口处孔径小于出口处的孔径)。这是因为在 粗加工所产生的热变形还未消除的情况下, 随着刀具的移动,精加工后实际切削 径度大于名义切削径度;同时也会出现精镗后的孔有较大的椭圆度, 这是因为在 粗加工时产生的大量切削热在不同壁厚处有不同的热膨胀: 薄壁处温度高,向外 膨胀的热变形大;厚壁处温度低,向外膨胀的热变形就小。采取粗加工后,让工 件冷却至常温后再精加工可以解决这些质量问题. 3、 镗孔方法分析 目前镗孔的主要方法有悬伸镗削法、支承镗削法和调头镗削法,由于加工方 法的不同,经常会出现较大的误差,下面是对这几种方法的比较分析。 (1) 悬伸镗削法镗孔时,机床主轴及刀杆悬伸出主轴以外,镗削时,悬臂刀 杆受到切削力矩、刀具及刀杆的自重的共同作用,产生较大的弯曲绕度,刀杆伸 出越长,贝U刀杆的刚度越小,当长径比大于 6时,镗孔的精度就不易保证。 (2) 支承镗削法镗孔时,镗杆由主轴穿过零件的同轴孔,另一端安装在机床 的尾架的支承套内。镗杆越长,刚度越小,同时,镗杆越细,转速越高,产生的 离心力就大,刀杆易震动,也会造成加工精度和加工表面的质量问题。 (3) 调头镗削法基本不存在因镗杆刚度问题而影响加工精度的问题,它是目 前许多企业采用的一种比较好的加工方法, 特别是对小批量、单件生产,此工艺 方法更为经济,它不用分析产生误差的具体原因,便于操作,同时,该方法也适 用于箱体机构不允许通镗的短距孔的加工,而此工艺方法的关键就是调头后的校 正和误差补偿问题。 轴承孔的精度要求是减速箱箱体加工中的关键问题,表 2—8列出了减速箱 轴承孔加工中的常见问题及解决办法。 表4-4床头箱轴承孔加工中常见问题及解决办法 影响因素 解决办法 1、用镗杆送进时镗杆的挠曲变形 1、采用工作台送进;2、增强镗杆 误差类别 刚性;3、改善刀具角度;4、减小 圆柱度 切削用量 2、用工作台送进时导轨的直线度 调整、维修机床 误差 3、刀具的磨损 1、提咼刀具耐用度;2、合理选用 刀具角度 4、刀具的热变形 1、使用冷却液;2、降低切削用量; 3、合理选用刀具角度 1、主轴的回转精度 正确的维修、调整机床 2、工作台送进方向与主轴的轴心 正确的维修、调整机床 线不平行 3、镗杆与导套的几何形状误差及 使镗杆和导向套的几何形状符合 圆度 配合间隙 4、加工余量不均匀"材质不均匀 技术要求并控制合适的配合间隙 1、适当增加走刀次数;2、合理安 排热处理工序;3、精加工采用浮 动镗 5、极薄的切削条件下多次重复走 1、 适当控制走刀次数及切削深度; 2、 采用浮动镗 刀形成“溜刀” 正确选择夹紧力、夹紧方向和着力 6、夹紧变形 占 八、、 7、铸造内应力 进行人工时效处理、粗加工后放一 段时间 8热变形 1、粗、精加工分开;2、充分冷却 1、镗杆的挠曲变形 1、减少镗杆的悬伸长度;2、米用 工作台送进、调头镗;3、增加镗 杆刚性,采用导向套或后立柱支承 维修机床 2、机床导轨的平面度、直线度 3、加工余量不均匀、不一致切削 1、尽量使各孔的余量均匀;2、切 削用量相近;3、适当降低切削用 用量不均衡 同轴度 量;4、增强镗杆刚性; 5、增加走刀次数 4、床身导轨与工作台面的配合间 1、 调整床身导轨与工作台面的配 合间隙; 隙 2、 镗同一轴线孔时采用同一送进 方向 平行度 1、镗杆的挠曲变形 1、增强镗杆的刚性;2、采用工作 台送进 2、工作台与床身导轨的平行度 误维修机床 差
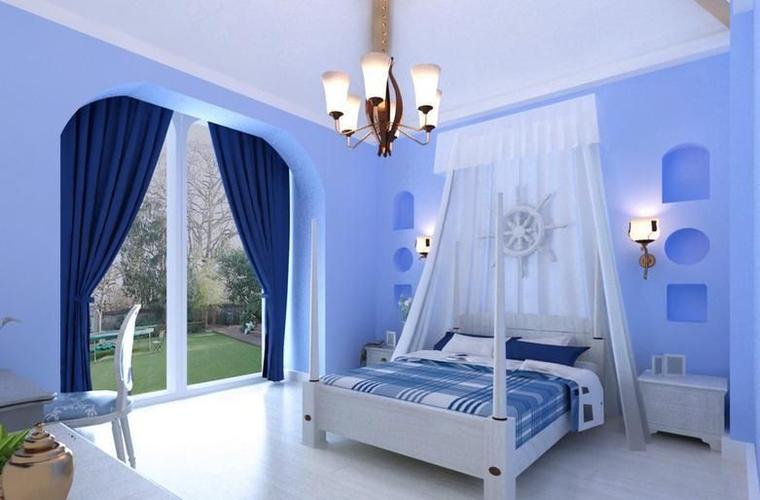
更多推荐
加工,精度,箱体
发布评论