混凝土防水材料-央视股票节目有哪些
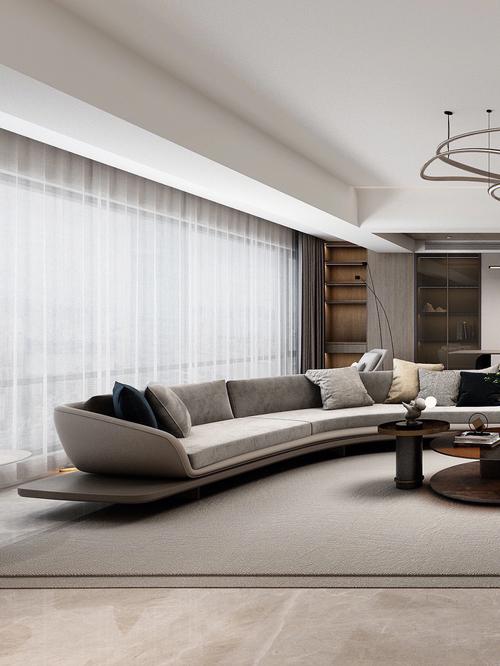
2023年9月24日发(作者:钟元辉)
定制家具施工方案
一、板材料的分类
1、实木板板材
顾名思义,实木板就是采用完整的木材制成的木板材。这些板材坚固耐用、纹路天
然,是中优中之选。但因为此板材造价高,而且施工工艺要求高,在中使用反而并未几。
实木板一般按照板材实质名称分类,没有同一的尺度规格。目前除了地板和门扇会使用实
木板外,一般我们所使用的板材都是人工加工出来的人造板。
2、夹板板材
夹板,也称胶合板、行内俗称细芯板。由三层或多层一毫米厚的单板或薄板胶贴热压
制而成。是目前手工制作家具最常用的材料。夹板一般分为3厘板、5厘板、9厘板、12
厘板、15厘板和18厘板六种规格。面板,俗称饰面板。是将实木板精密刨切成厚度为
0.2mm左右的菲薄单薄木皮,以夹板为基材,经由胶粘工艺制做成的具有单面作用的板
材。它是夹板存在的特殊方式,厚度为3厘。
3、密度板板材
密度板,也称纤维板。是以木质纤维或其他植物纤维为原料,施加脲醛树脂或其他合
用的胶粘剂制成的人造板材,按其密度的不同,分为高密度板、中密度板、低密度板。密
度板因为质软耐冲击,也轻易再加工。在国外,密度板是制作家私的一种良好材料,但因
为国家关于高度板的尺度比国际的尺度低数倍,所以,密度板在我国的使用质量还有待进
步。
4、刨花板板材
刨花板是用木材碎料为主要原料,再渗加胶水,添加剂经压制而成的薄型板材。按压
制方法可分为挤压刨花板、平压刨花板二类。此类板材主要长处是价格极其便宜。其缺点
也很显著:强度极差。一般不相宜制作较大型或者有力学要求的家私。
5、细木工板板材
细木工板,俗称。是由两片单板中间粘压拼接木板而成。的价格比细芯板要便宜,其
竖向抗弯压强度差,但横向抗弯压强度较高。
6、防火板板材
防火板是采用硅质材料或钙质材料为主要原料,与一定比例的纤维材料、轻质骨料、
黏合剂和化学添加剂混合,经蒸压技术制成的板材。是目前越来越多使用的一种新型材
料,其使用不仅仅是由于防火的因素。防火板的施工对于粘贴胶水的要求比较高,质量较
好的防火板价格比面板也要贵。防火板的厚度一般为0.8mm、1mm和1.2mm。
7、亚力克板材
亚力克板材是一种经过特殊加工的有机玻璃,它有着“塑料皇后”之美誉。它有着良
好的色泽,透明度高。其优点是出色的耐候性、良好的透明性能、可塑性良好。缺点是硬
度低、耐热性差、延伸性较低,因此易裂、易碎、易变形,且颜色不稳定,在使用过程中
容易发生起毛现象。另外,还含有对人体有害的物质。
8、三聚氰胺板板材
三聚氰胺板,全称是三聚氰胺浸渍胶膜纸饰面人造板,是一种墙面材料。其制造过程
是将带有不同颜色或纹理的纸放入三聚氰胺树脂胶粘剂中浸泡,然后干燥到一定固化程
度,将其铺装在刨花板、中密度纤维板或硬质纤维板表面,经热压而成的板。
二、板材料的选择
(1)现在什么都讲究环保,我们选材料,首先要考虑环保。
(2)看板材表面有无明显瑕疵。装饰板材表面应光洁,无毛刺和刨切刀痕,无透胶现象
和板面污染现象(如局部发黑、发黄现象),尽量挑选板材表面无裂缝、裂纹、无节子、夹
皮、树脂囊和树胶道的,整张板自然翘曲度应尽量小,避免由于砂光工艺操作不当,基材
透露出来的砂透现象。
(3)认清薄木贴面与天然木质单板贴面板材的区别。前者的板材纹理基本为通直纹理,
纹理图案有规则;后者板材为天然木质花纹,纹理图案自然变异性比较大,无规则。
(4)板材外观检验。装饰板材外观应有较好的美感,材质应细致均匀,色泽清晰,木纹
美观,板材配板与拼花的纹理应按一定规律排列,木色相近,拼缝与板边近乎平行。
(5)板材胶层结构稳定,无开胶现象。应注意板材表面单板与基材之间、基材内部各
层之间不能出现鼓包、分层的。
三、常规配料
(1)、门五金
(2)、不锈钢
(3)、藤祥
(4)、椰壳
(5)、贝母
(6)、布皮
(7)、其他
五金件的选择主要根据家具的功能需要以及成本预算来选择,装饰效果配件主要根据
需要达到的效果以及日常的维护打理等来确认。
三、设计方案
根据业主提供的装饰装修的施工图、效果图以及业主的要求,现场测量实际尺寸,绘
制出平面、立面、剖面图。图纸绘制完成后现场项目部会进行审查,根据现场的实际情况
以及自身多年的工程经验来提出一些意见及建议给家具深化方,更改完成后,提交至管理
公司及业主确认。对于一些细节以及重要部分的深化项目部会做出一些详细的说明,以便
修边
刨光
实木拼板
精剪
钻孔
制榫
车圆
砂光
木皮拼接
木皮热压
(一)、木工工序加工标准
每个部件在加工前要确认上道工序加工此部件是否合格,确定加工正反面(好面做正
面,相对不好的面做反面),核实加工板件的尺寸。
木材拼板:应牢固严密、平整,两块拼板料之间的缝隙≤0.1mm,不允许有脱胶、鼓
胀,使用拼板机将木材进行拼装时,拼板注意高低差、长短差、色差、纹理差、节疤。木
板厚度≤25mm时,压板机的压力在8—12KG为宜,木板厚度≥25mm时,压板机的压力
在12—15KG为宜。 需要拼厚的板件,所有拼板料纹理要一至即纹理为同一方向。特别
注意中间为夹心拼板部件,内部填充木材应与表面所用木材为同一品种木材,内部填充木
材允许有结疤、白边、蓝边,但不允许有腐朽材,因为腐朽材会导致压力不一至,使压好
的部件变形开裂,所用木材厚度一至,相隔的两下填充木料间距控制在80mm-100mm之
间,纹理与表面一至。
带锯:带锯前要仔细核对产品部件与生产流程表是否相符,准确无误后方可加工。确保
锯边质量,避免差错,调机后加工第一件产品是否合格,主副机手应分别检查,核对无误后方可
进行加工,并在加工中多次检查,及时发现问题,及时控制质量事故。锯边的质量要求符合工
艺规定,准确直角,大小锯路一致,误差在0.2mm之内,锯面应平滑,无崩口,无锯痕,无开裂,
无缺材,同时检查上道工序的产品质量,对不合格产品应及时选出。
手压刨:加工前应保持工作台面干净,不得有钉头、石粒、木屑等杂物,并做到加工中及
时清扫以免跳刀。操作者在接到上道工序的产品时,首先应检查无误后方可加工,同时检查刨
刀是否锋利。手压刨加工出的产品应笔直,平滑,规格标准一致,殘茬深度≤0.3mm,交角必须
保证90度,无戗茬。,并在加工中多次检查。
四面刨及立刨成型:要求加工人员有简单的识图能力,加工前应保持工作台面干净,不
得有钉头、石粒、木屑等杂物,并做到加工中及时清扫以免跳刀。检查刀具是否牢固,刀刃
是否锋利。主机手调机时应用相似的废、旧板件进行调机,主机手应对试机的部件进行检
查,达至要求后,在加工第一块部件时,并在做认真检查核对。 将使用的木料按所需要的
形状进行刨型。所刨外型与图纸误差≤0.2mm。根据图纸将木材加工成型,加工时不允许
有崩茬、毛刺、跳刀和发黑现象,加工时注意把好面当正面,有点伤痕的面用在里面。加
工的部件表面应光滑、平整、线型流畅一致,加工前检查设备部件螺丝有无松动,模板是
否安装规范,物料是否固定牢固,刀具是否装紧,加工过程中禁止顺刀进料,所刨部件外
型与图纸误差≤0.2mm。所刨边角、倒棱、圆弧一致,图纸误差≤0.2mm。 四面刨加工出
的产品应笔直,平滑,规格标准一致,呛茬深度在0.2mm之内,交角必须保证90度,无戗茬。并
在加工中多次检查。 立刨加工时,进料速度要适当。刃具要锋利,不可猛推猛拉。避免跳
刀,崩茬,发黑,吃料不均等现象。加工人员要学会根据经验撑握材质及刀型大小,调整
适当的进料速度,避免戗茬,对薄厚不均,宽窄不一的料要选出,避免损坏刀具。进料速度要适
当。刃具要锋利,不可猛推猛拉,采用送料器加工时,送料器的压力要适当。
宽砂定厚,按要求砂到符合加工要求的尺寸,机加完成后进行抛光砂,粗砂一次砂
0.2mm,抛光砂一次砂0.1mm。
精切:给毛料定长,加工过程中做到无崩茬、发黑,长与宽加工误差不超过0.2mm,
1米以下对角线≤0.5mm,1米以上板片对角线应≤1mm。
7.1仔细核对生产流程表和部件规格尺寸,明确后方可进行加工.
7.2为确保精截的加工质量,符合工艺流程,避免差错,首先检查锯截面是否方直,明确后方
可进行加工,加工时合理选料,避免不合格件流到下道工序.
7.3精截的加工质量,锯截面应平滑,整齐,无崩口,锯痕等缺点,并在加工过程中多次检查,
以防跑尺.及时发现问题,并报相关人员和质检人员进行处理.
7.4加工好的部件,必须按生产流程表分批分类摆放,不得多批多类混放,合格率要得在
98%以上。
排钻
8.1仔细检查核对部件生产流程表和图纸尺寸、材料,同所加工的部件、材料、尺寸进
行对比,看是否相符,明确后方可进行加工。能够对称加工的板件,为达到高的工作效率,
必须要求加工人员对称加工孔位。
8.2为保证加工质量,要求刀具必须锋利,刀具紧固,台面稳固,压板或台面必须保持清
洁,做好不间断清理,做到无木渣或铁钉及其它物,以防孔位偏大差,并防止压坏部件。
8.3主机手调机时应用旧板件进行调机,在加工第一块部件时,应认真检查核对,新产品或
加工工艺复杂的部件应请质检员,工段长等检查核实,部件在加工到5件左右时应再一次检
查,加工中应多次检查。
8.4钻孔质量要求符合图纸加工尺寸和工艺要求,无误差,孔深孔位标准一致, 孔 位加工
误差不得超过0.2mm,孔们倾斜度误差为0,产品要做到配套钻孔。常试装、勤检查。部
件摆放整齐,合格率要求达到99%。
单孔钻:按图纸的孔位大小和工艺要求钻孔,加工过程中做到无崩口、无毛刺现象,
孔位加工误差不得超过0.2mm,产品要做到配套钻孔。常试装、勤检查,确保产品的品
质。能够对称加工的板件,为达到高的工作效率,必须要求加工人员对称加工孔位。经常
打扫工作台面,保持钻孔的精准度。
斜切角,加工过程中做到无崩茬、发黑,产品组装时,内、外对角处误差不超过
0.2mm。
实木产品组装要求
11.1组装前应保持工作台面干净,不得有钉头,石沙粒,木屑等杂物,并做到加工中及时清
扫以免刮花、刮伤部件,出现质量事故.
11.2搬运板件时,要轻拿、轻放。要用手拿起板件,不允许拖动板件。不得有磕碰、
划痕。
11.3码放板件时,不可让板件直接与地面接触(以免划伤或吸潮气)。两两板件码放
时,正面与正面、背面与背面码放。长度超过1米的板件不可立着长时间码放,板件下面
需要有4个木条做平衡支撑。注意板材码放的高度,避免压伤。
11.4所有部件必须分类码放,不得混合堆放。
11.5所有板件在组装紧固时,夹子、组装机等要加辅助垫片。要用橡皮锤。避免划
伤、磕碰、锤坑。
11.6所有组装用的工具不可放在任何产品板件上,以免划伤板件。
11.7所有人员要爱惜产品,不得没事用手在板件上来回划动,不得座在产品上或者躺
在产品上面休息,不得把随身衣物放在产品上面。更不可把脚放在我们的板件和产品上。
不得把水杯放面产品上面或着放在离产品比较近的地方。
11.8所有部件组装时应无冒钉、漏钉现象。
11.9组装质量要求符合图纸工艺规定,产品或是部件牢固、平整,相邻部件要严密,缝隙
控制在0.3mm以内,无伤痕,无锤印。
(二)、打磨工艺标准
1、砂纸的选择
1.1实木白坯:打磨选用180#——240#砂纸
1.2夹板或一道的打磨:选用220#——240#砂纸
1.3平整底漆的打磨:选用320#——400#砂纸
1.4最后一道底漆或的打磨:选用600#——800#砂纸
1.5面漆抛光打磨:选用1500#——2000#砂纸
2、打磨工艺要求:
2.1白坯砂磨工艺要求:
2.1.1严禁出现缺材、钉眼、横砂、黑疤、崩茬、变形、砂痕、砂光圈、锯痕、凹陷等
现象。
2.1.2板件必须平整光滑,无毛刺。造型处砂磨过渡要圆滑,不能出现台阶、镂铣纹。
2.1.3机磨必须顺着木纹方向,板面上不能有横向砂印和螺旋印出现。
2.1.4组装连接处不允许有胶,连接缝隙不超过0.5mm,并进行缝隙修补,修补颜色基
本一致。
2.1.5产品表面的边角都要砂磨小圆边,板件圆边砂光弧度必须统一规范。
2.1.6直边板件边角必须呈90度,严禁砂变形。
2.1.7板件出现崩缺,要进行补木块或木灰修补并进行砂平。
2.2漆磨工艺要求:
2.2.1严禁出现透底、碰划伤、亮点、凹坑、缝隙。
2.2.2对板件轻砂细磨,边、角细砂,砂全,应做到无漏砂,不砂漏
2.2.3混油产品有缺陷的地方要用原子灰修补,清油有缺陷的地方用腻子修,修补后比
原基本微高1mm,经过2小时干燥后用320#砂纸细磨平。
2.2.4面磨正常以320#砂纸为主,不得擅自使用320#以下的砂纸,以免影响油漆质
量。
(三)、涂准工艺标准:
1、色板标准:
1.1常用生产色板必须要经相关人员批准,签字确认,将色板工艺流程附在色板背面,
并对其进行避光保存好。
1.2客户提供色板应先进行打样至少两件,一件给客户确认,一件确认后做为生产使用
依据。
1.3常用生产色板每个月要求进行更换,减少因污染造成的色变问题。
2、涂装工艺要求:
2.1涂装工艺必须严格按照色板操作程序进行。
2.2喷漆前一定要在除尘间吹净灰尘,不得未除尘直接喷涂。
2.3涂料(油漆,色浆,稀料)应严格执行配比标准。
2.4油漆着色时颜色要和封样要求一致,整体颜色均匀,无色深、色线、色差等现象。
一系列和配套产品颜色要保持一致。
2.5涂膜饱满,平整、光滑、无粗糙,脱落等现象。
2.6产品表面无污渍、积油、粘漆、超皱、发白、针孔、起粒、起泡、龟裂、刮(碰)
伤、砂印、蜡印、走枪痕迹等现象。
2.7油漆质量要求漆面结实光滑,纹理清晰干净,边角整齐,无流油、破油、气泡、粗纹、
伤痕、发白、桔皮等现象。
2.8异形、转角部位涂膜柔滑,色均匀。无少喷。漏喷等现象。
(四)、成品组装:
7.1试装部件检查与图纸是否误差,误差按“工艺标准”所要求的进行组装。与小组立
区别在于大组立完成后的是成品。
7.2小件组立:组立不用在拆开的部件,组立前应先备料,把所有要组装部件按图纸加
工的要求检查无误,部件无崩口、毛刺、发黑现象,组装第一件时,先进行试装,确写装
好后复尺与图纸尺寸误差≤0.2mm的情况下开始批量组装。组立过程中胶水布涂均匀,组
立好的半成品,应无冒钉、漏钉现象,结合严密,胶水擦拭要干净。用在柜体可视面的小
件,正面不得有钉孔,腻子。
(五)、包装工艺标准:
1、卫生要求:将检验合格的产品用风枪进行除尘,有污渍的地方用清洁布进行擦试干
净。
2、将清理后的产品摆放整齐并做好记录,对组件及配件配套齐等待包装。不能错包、
漏包。
3、先用整理好的产品用珍珠棉进行平铺包裹进行防护,包装好的产品,箱内不允许有
较大空隙,板件在箱内应基本上没有位置可移动或在允许范围内没有损坏板件的移动,空隙较
大时,必须加放泡沫填实;包装后摇动纸箱时,纸箱内产品、配件无移位现象。
4、包装板件讲究放置平稳严实,受力平衡均匀,板件长度超过2400mm、宽度超过
600mm的最多包装三层,长2400mm以内,宽600mm以内最多包装4层,板件平放拼凑
包装的要错位法放置,以减少侧面碰撞损伤。
5、柜门类两件包装,上下及中间用泡沫板进行分隔;实木门每扇包装,上下垫泡沫板
防护。
6、线条、装饰条配套打捆包装,并用珍珠棉分隔开,减少运输过程中碰伤。
7、组装品包装根据组装品外形进行珍珠棉防护后用包装纸皮进行保护,四角防护纸皮
用胶带加固;货运产品每个面用泡沫板进行防护后再用包装纸皮进行保护。
8、纸箱规格符合设计要求,外表光滑,平整、无污渍,箱唛标识内容正确无误,字迹
清晰。
9、玻璃、镜面等易碎品的包装符合防震要求,易碎品的包装有明显的标识。
10、封箱胶平整、牢固,封箱胶不能与成品直接粘接。
11、临时产品的包装可进行简易包装,分段用包装纸皮防护,长度2400mm以上5
条、1500mm-2400mm包装4条、1000mm-1500mm包装3条、1000mm以内2条
12、货运品包装要全面包装保护,对易碎品包装进行木架加固。易碎品:玻璃类、弯
孤造型类、装饰小线条类。
13、包装后的产品堆放,必须平稳,堆放高度不能超过 1.5m,遵循下重上轻,下大上小的
原因堆放,同时应按纸箱箭头所指定的方向堆放。
14、重量控制:单件包装重量在45kg以内
(六)、实木家具的用胶标准
1、拼板涂胶:胶应涂满整个拼板接触面,用胶量以压制成型后每米长度溢出胶点5至
6处的胶量最为合适。
2、榫头、榫眼的涂胶:榫头四周涂满涂,榫眼底部及四周涂胶,用胶量以组装成型后
周边溢出胶点3至4处的胶量最为合适。
3、45度涂胶部件,在45度平面处也需涂胶。
4、组装部件在涂胶后应及时清理溢出的胶,溢出的胶要清理干净,不可留有胶痕。若
是胶干后难以清理。
5、涂胶时,注意不要在产品上留有胶痕。
(七)、五金配件安装标准
1、拉手门板、抽屉拉手上下、左右按装在同一条直线上,同一柜体使用不同拉手时,
需要注意对称安装。螺杆需旋进拉手螺口内5mm以上。
2、拉手颜色、大小:同一柜子上的拉手颜色应保持一致,不能有明显的色差,不得有
掉漆等现象。因同款式的拉手有大小的不同,安装拉手时严格按设计图示的大小进行安
装。
3、滑道:安装时注意左右高度一致,前后位置一致,组装所使用的自攻丝一致,自攻
丝锁进滑道侧板上的深度要一至。
4、铰链:安装时需与柜体成直角,同一门板铰链的中心孔位要在一条直线上。
5、装饰金属件:管材和冲压件不允许有裂痕,管材无缝隙、焊接无结疤,不得有掉漆
等现象。
(八)、安装售后工艺标准:
1、套装门开启灵活,门套安装必须牢固,不可出现松动门套与门扇预留门缝,一般左
右门缝3MM,上门缝3MM,底部门缝为7MM。门套安装后必须保持水平和垂直;门在自
然状态下不能自动开启;垂直偏差不超过2MM。
2、窗套、哑口套安装后必须达到水平和垂直,接缝严整,斜角拼缝平整,线槽顺畅、
贯通,固定牢固,无松动
3、饰面板、护墙板、背景墙安装必须表面平整,留缝对接顺直、通畅;相邻两块护墙
板、装饰条无明显色差,木纹上下、左右必须追纹、同纹;阴阳角水平、垂直;阳角拼口
密缝、胶水饱满;安装牢固,平整、垂直度误差不能超过2MM,表面无刮花、碰伤等,并
且严禁使用枪钉。
4、柜体安装完成后必须水平,垂直,对角线误差小于2mm,抽屉、门扇开启灵活无
声响。
5、产品正面和抽屉门板应保持在一个平面上(如有线条边的应以线条半径为凹出高
度)。抽屉和抽屉、门和门之间边角要对应平直,木纹方向一致,颜色一致。门板与侧边面
平整、无变形,四边顺直。抽屉与柜子柜架间缝上下左右不得超过2mm。门缝左右中加起
不能超过3mm,上下不能超过3mm。
6、装饰线条、装饰柱必须达到水平和垂直,接缝严整,斜角拼缝平整,线槽顺畅、贯
通,固定牢固,无松动。
7、所有部件组装时应无冒钉现象,使用到三合一的位置不得歪斜,合页、滑道等配件
组装整齐,部件之间结合严密。
五、质量标准
1、产品工艺要求
1.1产品设计尺寸:是指产品图纸上标注的尺寸。如产品宽、高、深的外形尺寸。 1.2
外观尺寸的要求:宽度在1100mm以下的产品,宽度方向误差在±2mm, 宽度在1100mm
以上的产品,宽度方向误差在±3mm;深度在450mm以下的产品,深度方向误差在±
1mm, 深度在450mm以上的产品,深度方向误差在±2mm,在没有特殊要求的情况下,高
度误差在±5mm。
1.3功能尺寸要求:加工的产品如有特殊的功能标注,则该功能区的尺寸误差在+2mm,
如衣柜挂长衣区尺寸≥1300mm, 衣柜挂短衣区尺寸≥850mm,书柜主要放书区域高尺寸≥
320mm,深度≥250mm。
1.4外观要求:
1.4.1加工完成后的产品,总体要求所有边角要均匀一至,表面平整光滑,木纹清晰透
明。产品外表面要达到精致光滑,内表要达到细致光滑。外表面,不得有跳刀、崩茬、凸
凹的大小坑哇、划痕、交接不严(如45度交接、平接等)、钉眼(正面等可视面不可用钉
枪)、不可补腻子(因腻子上漆后颜色与色板有很大的差别,在产品上会形成一个黒点)、
不得有胶痕。内部及其它不可见部件,如柜体的后下横档等部件,要求达到细致光滑,不
许存在毛刺、锯痕和刨痕等容易伤害身体的缺陷存在,更不许有缺材现象。需要开工艺缝
的,开工艺缝大小定为:1.5*1.5mm的V型槽。
1.4.2各部件不允许存在以下缺陷:同一套系所用刀型应一致,同一产品不同部件之间
的组装余量应一至(如面板与柜体、面板与帽线之间、山板与前立挺之间的台阶尺寸等),
抽面、门板分缝应均匀一至。产品零部件接合处、榫孔结合处、装板部件和各种地角支承
部件存在松动、离缝、断裂等;产品外表倒楞、圆线、圆角存在不均匀不对称的现象;
1.4.3车枳部件,外表光滑,圆满度周圈一致,无跳刀,无划痕,无崩茬,无烤焦现
象。车枳好的部件中如有3.3中所提到的备料问题,需要重新更换。
1.4.4雕刻部件加工后,图案应均匀清晰,层次分明,过渡顺畅,花型、线型必需左右对
称,花形底部需铲平,不得有刀痕、砂痕的等。雕刻缺材处需用实木修补,不允许用锯末
修补。
1.5形状和位置要求:
1.5.1翘曲度,是指产品(部件)表面上的整体平整程度。标准规定,正视面板件,若
对角线长度L<700mm,允许差值≤1mm。若对角线长度700mm<L<1300mm,允许差
值≤2mm,若对角线长度>1300mm,允许差值≤3mm。
1.5.2 平整度,是指产品(部件)表面在0~150mm范围内的局部的平整程度。不平
度应≤0.2mm。
1.5.3 邻边垂直度,是指产品(部件)外形为矩形时的不规则程度。测量两个对角线长
度L≤1000mm允许差值≤2mm,框架对角线长度L≥1000mm,允许差值≤3mm。但最
大不得大于5mm。
1.5.4相对位置相差度,是指产品中门与框架、门与门、门与抽屉、抽屉与框架、抽屉
与抽屉相邻两表面间的距离。门与框架、门与门相邻表面间折起距离偏差(非设计要求的
距离)允许≤1mm,抽屉与框架、抽屉与门、抽屉与抽屉相邻两表面间的距离偏差(非设
计要求的距离)允许≤1mm。
1.5.5 抽屉摆动度、下垂度,是指抽屉与框架的配合精度。将抽屉拉出深度的2/3时,
摆动度应≤10mm,下垂度应≤10mm。
1.5.6 当柜子抽屉全部拉出后,柜体不能向前倾斜,如倾斜柜体需加配重,或者减小抽
箱深度的尺寸。当衣柜、酒柜、及书柜等门板全打开时,柜体不能向前倾斜,如倾斜柜体
需加配重,或者用其它方法处理(如下面加抽屉以减少门板的重量,四个门板变成五个门
板等等)。
1.5.7 产品底脚着地时与地面的不平度,是指产品底脚着地面时的平稳性。不平度应≤
2mm。
1.5.8 当产品以独立腿着地时(如椅子、沙发、四个腿的柜子等),与地面接触的四边
需要倒3*3的斜边或倒R3的圆弧。
1.5.9分缝,是指产品外部能开启和关闭部件与柜体框架间的配合间隙大小,称分缝。
抽屉与抽屉、抽屉与柜体框架分缝不得超过2mm。门板与门板、门板与柜体框架分缝为:
上2mm,下3mm、左右各为2mm。外盖门板及抽屉没有详细的设计要求时按上述要求执
行。如有设计特殊需要,则根据实际设计要求执行。以达到产品外观整体美观。
1.6零部件加工尺寸标准
1.6.1正面可视面板件:如前框(不包括前框的部份分体部件)、门板(不包括门板的
部份分体部件)、抽屉(不包括抽屉的分体部件)、前帽线,前底脚线等,部件长度L≤
1000mm时,长度方向允许误差≤0.2mm,部件长度L≥1000mm时,长度方向允许误差
≤0.5mm,所有宽度方向误差均≤0.2mm,所有厚度方向误差均≤0.2mm。
1.6.2侧面及内部主框架部件(不包括部份分体部件):如后横档、侧横档等,此部件
位于长度方向时,允许误差≤0.2mm,此部件位于宽度方向时,允许误差≤0.5mm。
1.6.3活动部件:如活动隔板,抽屉、挂衣杆、可抽拉的裤架及衣柜内装饰盒等,长、
宽允许误差均≤1mm。
百环家园-自由足球手游最新消息
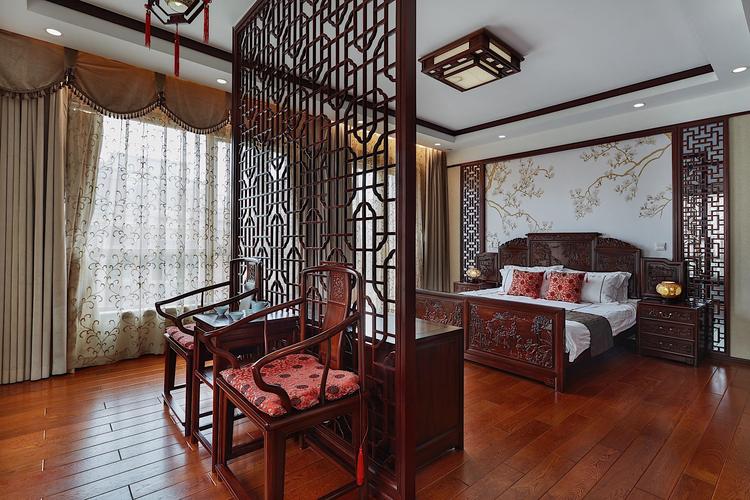
更多推荐
防火板价格
发布评论