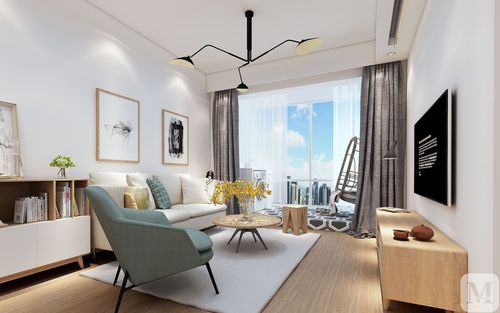
GMP医疗器械十万级生产车间空调净化系统验证方案 编制: 日期: 审核: 日期: 批准: 日期: 一、设备基本情况: 1、系统概述 1.1本公司空调净化系统分为生产车间洁净区空调系统(QS-1)和微生物室洁净区空调系统(QS-2)(QS-3)两部份,生产车间洁净区面积约302m2,微生物室洁净区面积约43m2。这三套空调净化系于2020年02月已经完成安装。由苏州安科众达净化科技股份有限公司负责安装调试。此次验证针对厂房净化工程技术改造后进行验证。 生产车间洁净区空气净化过程为:新风初效过滤 表冷加热器 风机辅助加热器 加湿中效过滤 高效过滤 室内 正压风量 排至室外(回风经回风管进入组合式空调机组初效过滤器前再循环)。 微生物室洁净区的空气净化过程为:新风初效过滤 表冷挡水风机 辅助加热器 加湿中效过滤 高效过滤 室内 正压风量 排至室外/阳性对照室全排(负压)。新空气经过空调净化系统后能够保证洁净室的空气尘埃粒子、沉降菌及环境温湿度达到产品生产、实验室检测要求。万级乱流型,采用顶送风下侧回风方式,换气次数:万级≥25次/h。净化空调系统通过对系统内各区域的送风、回风及排风风量的调节来达到各个不同洁净级别之间以及室内外压差要求。 1.2.洁净区的技术参数:
2、机组情况 2.1生产车间及微生物室洁净区空调机组:
二、验证目的 1、检查并确认空调净化系统性能、适用性、主体安装、管道安装、配套公用系统连接是否符合设计标准和GMP 要求。 2、检查并确认空调系统的空气环境各项指标是否满足生产、设计和说明书的要求。 3、确认操作、维护保养标准操作程序是否符合生产实际操作要求,是否能够正常、稳定地运行。 三、适用范围 本方案适用于本公司内部HVAC系统的安装、调试、运行过程的验证。 四、验证小组人员与职责分配
1、验证小组人员职责: 组长:负责验证方案,验证报告的审核;负责组织从验证方案起草、验证方案实施及验证报告完成全过程的组织工作。 组员:分别负责验证方案中的预确认、安装确认和运行、性能确认具体工作。 2、验证工作中各部门责任: 品质部:负责验证方案的起草、组织验证方案的的实施;组织验证方案、验证报告的会审,会签,对验证全过程实施监督;负责验证的协调工作,保证验证实施过程严格执行验证方案的规定;负责组织洁净室的温度、湿度、风速、压差的测试并填写记录;负责组织洁净室的悬浮粒子数、微生物的测定并填写记录;负责HVAC系统日常监测项目和验证周期的确认;起草有关检验标准操作规程。 设备部:负责设备的安装、调试及仪器仪表的校正;建立设备档案,负责收集验证记录;负责起草HVAC系统的操作维护、清洁的作业指导;负责HVAC系统的操作维护、清洁工作。 生产部:负责洁净室的温度、相对湿度及压差的记录:负责洁净室的清洁工作,保证安装环境、运行环境符合设计要求;负责洁净室配合设备部做好验证方案实施的组织工作。 五、进度计划 验证小组提出完整的验证计划,经总经理批准后实施,整个验证活动分四个阶段完成。 安装确认:从XXXX年XX月XX日至XXXX年XX月XX日 运行确认:从XXXX年XX月XX日至XXXX年XX月XX日 性能确认:从XXXX年XX月XX日至XXXX年XX月XX日 起草报告:从XXXX年XX月XX日至XXXX年XX月XX日 六、验证标准
七、验证用仪器仪表的校验 为保证测量数据的准确可靠,必须对安装在设备及设施上的仪器仪表以及本公司负责进行监测项目所需的仪器、仪表进行校验。(仪器仪表校验情况记录于附件1) 八、安装确认 对预安装设备的规格、安装条件、安装过程及安装后进行确认,检查空调系统在安装环境下的适应性,证实空调系统规格符合要求,设备技术资料齐全,安装条件及安装过程符合设计要求。 1、空调机组性能参数的确认 根据提供苏州安科众达净化科技股份有限公司的竣工资料,对空调机组的技术参数进行核实,核实内容包括:所选择的空调机组的风量和风压、冷却段冷凝水排放能力、过滤器的配置等。接受标准:风机的风量和风压符合设计要求的总风量和风压,空调机组的冷却段的能力符合设计的要求。(空调机组性能参数确认记录见附件2) 2、室外机和空气处理机组安装的确认 室外机和空气处理机组已安装,由设备部人员检查各功能段排列顺序应与设计图纸相符,检查其安装是否符合设计和安装规范(包括冷凝器、蒸发器管道的连接及机组的电气连接要符合使用说明书的有关要求检查安装是否符合设计和安装规范)。(室外机和空气处理机组安装确认记录见附件3) 3、风管、通风系统部件的制作与安装确认 由设备部根据设计方案及技术参数、供应商提供的技术资料等对送回风管道、风阀、高效送风口等材质与加工质量进行逐一核对检查,应符合设计标准、GMP要求。如有项目不符合规定的,由设备部负责联系供应商予以更换或改善。(风管、通风系统部件的制作与安装确认记录见附件4) 4、风管、空调设备清洁的确认 风管清洁的确认是在安装过程中完成的。通风管道安装前,要用中性清洁剂或酒精将内壁擦拭干净,用白色无脱落纤维抹布擦拭,目检无油无灰尘后在风管两端用干净的塑料膜封住,等待吊装,塑料薄膜封口一旦被损坏,就必须重新清洗,重新检验。安装过程中不能把己清洗好的风管弄脏。空调机箱要用中性清洁剂或酒精进行清洁,再更换初效及中效过滤器,风机开启后,运行一段时间,最后再安装末端的高效过滤器。(风管、空调设备清洁确认记录见附件5) 5、风管的检漏 空调净化系统通风管道安装完成后,在安装保温层之前必须进行漏风检查,检查方法采用漏光测试法:将灯泡(电压不大于36V,功率在100W 以上,带保护罩)置于风管内侧,外侧应为黑暗环境,光源沿着被测部位与接缝缓慢移动,无光线射出。漏光试验中的漏光点均应进行密封处理。对于原生产车间空调净化系统通风管道未改动已安装保温层部分须在改造前运行空调采用外部漏风检查,如听到漏风声,均应作记号以便在施工中维修。(风管检漏记录见附件6) 6、高效过滤器的安装及泄漏确认: 6.1安装前必须对洁净室进行全面清扫、擦净,净化空调系统内部如有积尘,应再次清扫、擦净,达到清洁要求。 6.2洁净室及空调净化系统达到要求后,应开启风机至少12小时后,再对洁净室四壁、顶棚、地面和静压箱四壁擦拭干净,再开启风机运行,直至确认整个系统无灰尘后,再安装末端的高效过滤器。 6.3高效过滤器安装前,必须在安装现场拆开包装进行外观检查,查看滤纸密封胶和框架有无损坏,边长、对角线和厚尺寸是否符合要求,框架有无锈斑,有无产品合格证等。 6.4安装时,外框上箭头应和气流方向一致。 6.5高效过滤器检漏的目的是通过对泄漏量测试,发现高效过滤器及其安装过程存在的缺陷,以便采取补救措施。测试方法:用粒子计数仪采样器放在被检部位下2-3cm处,以不超过2cm/s移动速度对被检过滤器的整个断面、封头、边框扫描进行检查,以粒子计数仪无脉冲现象为合格。(高效过滤器的安装与泄漏确认记录见附件7) 7、起草标准操作文件: 中央空调的操作、维护作业指导 8、安装确认结论: 空调净化系统验证报告 九、运行确认 运行确认是在设备运行状态下,对空调机组的传动系统、电气部分、动力管线、计量器具等进行检查,并将实际检测结果与工艺要求及设备设计参数进行对比,并根据对比结果总结该设备的运行确认。目的是为证明空调净化系统是否达到设计要求及生产工艺要求。 在运行确认阶段,所有的空调设备必须开动,与空调系统有关的工艺排风机也必须开动,以利于空气平衡,调节房间的压力。 空气净化系统运行确认的主要内容:空调机组运行的确认,高效过滤器的风速,房间静压差、温度与相对湿度的测试,自净时间。 1、空调机组运行的确认: 1.1 运行前,首先检查供电电源是否正常,点动接通电源后检查送风机叶轮旋转方向是否正确、运行是否正常。 1.2测量风机电机运转电压、电流。 1.3 更换新的初、中效过滤器,检查记录初、中效过滤器的阻力(过滤器的压差) 1.4 检查冷却风机运转方向 1.5检查压缩机运转情况(包括电压、电流、机体温度、吸排气压力等)是否正常,必要时添加R22氟利昂。 排气压力(高压)范围:1.6-1.9MPa 吸气压力(低压)范围:0.3-0.5 MPa 压缩机三相电流不平衡应小于5% 1.6 复核空调系统的操作、维护作业指导的适用性和合理性。(空调机组运行确认见附件8) 2、高效过滤器风速测定: 测试的目的是通过风速的测定计算证明空调系统能够提供符合设计要求的风量,再根据各房间实际风量和体积计算出换气次数,证明系统的换气次数符合洁净区的设计要求,若有偏差,应调整相应的风阀使系统符合设计标准要求 使用风速仪对洁净区各房间进行测试,换气次数和风量应符合设计要求。 标准:各风口的风量:在设计风量的85%-115% 换气次数:万级:≥25次/小时 换气次数的计算:n=(L1+L2+…Ln)/A×H 式中: n——换气次数(次/h) L1+L2+…Ln——房间各送风口的送风量(m3/h) A——房间面积(m2) H——房间高度(m) (高效过滤器风量确认记录见附件9) 3、房间静压差和温湿度的测定: 3.1房间静压差: 在风量测定后进行,房间静压差测定目的是查明洁净室空气洁净级别不同的相邻房间之间或洁净室与一般房间之间是否保持一定的压差。 ●测试仪表:洁净室压差计。 ●测试方法:应在所有房间的门关闭时进行,有排风时,应在最大排风量条件下进行,并从平面最里面的房间依次向外测定相邻相通房间的压差,直至测出洁净区与非洁净区之间的压差。 ●检测频率:每日上、下午各检测、记录1次,记录三周。 ●室内相邻不同级别房间的静压绝对值应>5Pa,洁净室与室外大气静压应>10Pa,洁净走廊与其他洁净室的压差也应>5Pa,设直排风口的洁净室静压差要小于邻近洁净房间。 根据测定结果适当调整空调系统,使各房间静压差符合标准要求,一旦调整好就不能再动。 3.2房间温湿度的测定: 房间温湿度的测定是确认空调系统具有将洁净室温度、相对湿度控制在设计要求范围的能力,温湿度的测定应在风压调整合格后进行。 ●测试仪表:洁净室温湿度表。 ●测定方法:温湿度表置于室中心或具有代表性的工作区域中心。 ●标准:温度18-28℃,相对湿度 45-65% ●频率:与风压测试同步进行,每日上、下午各检测、记录1次,记录三周。 (洁净室压差和温湿度监测记录见附件10) 4、自净时间测试: 自净时间测试的目的是确认系统在受到来自内部的污染后恢复标准要求的洁净度的能力。从而判断洁净室的动态性能。 ●测试仪表:悬浮粒子计数器 ●测试方法:洁净室自净时间的测定应在洁净室停止运行两天时间。然后开机运行,将悬浮粒子计数器的采样管放在主要工作区,测试室内粒子浓度,以一分钟的间隔测量,当粒子数不再降低且在合格范围内即为自净时间,确定测试结果是否符合设计要求。 ●选换气次数、风速、风量相对较差的房间和关键控制的进行自净验证。(洁净室自净时间测试记录见附件11) 5、运行确认结论: 空调净化系统验证报告 十、性能确认 性能确认的目的:对洁净室综合性能的监测,对空气净化系统是否能达到规定的洁净度做出判断,确认HVAC系统能够连续、稳定地使洁净区的洁净度符合设计标准及生产工艺的要求。性能确认在动态或模拟全负荷运转的情况下进行 性能确认周期:HVAC系统运行3个星期,分为3个周期,每个周期5天。 性能确认内容:悬浮粒子的测定和微生物(沉降菌)的检测。悬浮粒子的测定应在空调调试及空气平衡完成后进行。微生物的测定应在悬浮粒子测定结束,房间消毒后进行。 1、悬浮粒子的测定: 悬浮粒子的测定目的是通过悬浮粒子的测定,判断洁净室的洁净度是否达到要求。 悬浮粒子洁净度监测的采样点数目及其布置应根据产品的生产及工艺关键操作区设置,在验证时采用静态测试,即在洁净室(区)净化空气调节系统已处于正常运行状态,工艺设备已安装,洁净室(区)内没有生产人员及生产活动的情况下进行测试。 ●测试仪器:尘埃粒子计数器 ●测试方法:按《医药工业洁净室(区)悬浮粒子的测试方法》GB/T 16292-2010进行。 ●接受标准:悬浮粒子洁净度级别的结果评定,参见《洁净区悬浮粒子监测标准操作规程》规定。 ●检测频率:每周一次(悬浮粒子测试记录见附件12) 2、微生物(沉降菌)的测定: 微生物(沉降菌)的测定目的是确认生物微粒沉降密度,以此来判断洁净室是否达到规定的洁净度。本验证采用沉降菌测定方法,沉降菌用沉降浓度表示[CFU/(皿·min)]。 ●主要测定设备:Φ90mm×150mm玻璃培养皿和胰酪大豆胨琼脂培养基。 ●测试方法:按《医药工业洁净室(区)沉降菌的测试方法》GB/T 16294-2010进行。 ●接受标准:微生物(沉降菌)的测定的结果评定,参见《医药工业洁净室(区)沉降菌的测试方法》规定。 ●检测频率:每周一次(沉降菌测试结果记录见附件13) 3、HVAC系统性能确认过程中,应严格按照系统标准操作、维护保养规程、检测程序和质量标准进行操作和判定。出现个别项目不符合标准的结果时,应按下列程序进行处理: 3.1 待系统稳定后,重新检测。 3.2必要时,分区分段进行对照检测,分析检测结果以确定不合格原因。 3.3若属系统运行方面的原因,必要时报验证小组,调整系统运行参数或对系统进行处理。 若在联系运行三个周期中,悬浮粒子数、沉降菌数、压差均符合设计要求及相应级别洁净区标准规定的要求,可判定系统通过性能确认。温湿度控制的性能确认结果应以全年为一个周期,只有经历了季节变化,才能全面评价系统对洁净区温度与相对湿度的控制能力。 4、性能确认结论: 空调净化系统验证报告 十一:偏差分析 按照设计方案对HVAC系统进行安装及运行确认,在确认的过程中若出现不符合设计要求、工艺要求的情况(偏差),应进行分析,找出原因,进行纠正改进直至达到使用要求,否则该系统不能投入使用。 十二:验证结果评价及结论 在以上所有项目确认完成后,项目测试状况与接受标准一致,则可认为本次验证成功,并完成验证报告,由验证委员会审核批准后方可投入生产。 十三:拟定日常监测及再验证周期 根据验证结果及相关要求拟定日常监测及再验证周期。 验证记录空白样张:附件1—附件13 | |||||||||||||||||||||||||||||||||||||||||||||||||||||||||||||||||||||||||||||||||||||||||||||||||||
更多推荐
验证,安装,确认,空调,系统,进行,要求,检查
发布评论