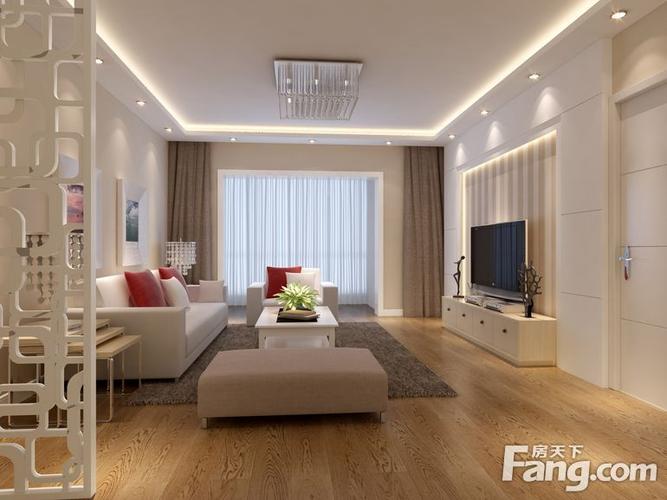
国内外先进陶瓷材料加工技术的进展300072天津大学高温陶瓷材料及工程陶瓷加工技术教育部重点实验室于思远林滨林彬
摘要随着先进陶瓷材料的开发和应用,陶瓷材料的加工技术受到人们的普遍观注,本文查阅了近二十年来有关的文献资料,对国内外陶瓷材料加工技术的研究成果进行了系统地综述,并着重从材料的去除机理,优质高效加工新工艺及加工工艺装备三方面介绍了陶瓷材料的切削加工,磨削加工,研磨,抛光和孔加工技术的进展。
先进陶瓷是采用优化配方和精细生产工艺制造,具有优良的机械、物理性能的陶瓷材料,许多性能是金属材料无法比拟的,而且与传统陶瓷不同,在70-80年代,先进陶瓷由于其优良的耐高温抗磨损性能在电子和光学高科技器件中应用日益广泛。近年来随着材料机械性能的改进,先进陶瓷作为机械结构零件新材料也显示出广阔的应用前景和巨大的市场。CI RP文献报导,到2000年日本先进陶瓷材料和器件的销售额将达到300亿日元,尤其是具有优良热性能的Si3N4, SiC非氧化物陶瓷的应用,将有更加快速的增长,由此可见这一诱人的应用前景。
从毛坯到产品,陶瓷材料需要二次加工,但由于硬脆特性,陶瓷的加工性比多属材料困难得多,因此需要开发优质高效的陶瓷加工新工艺新技术。先进陶瓷的加工,涉及到陶瓷材料的性能,加工技术,检测,连结和涂覆等许多方面,本文由于篇幅所限,只重点介绍先进陶瓷的切削加工,磨削加工,研磨抛光和孔加工技术等方面的进展。
1先进陶瓷材料的切削加工
1.1切削机理的研究
Ó1980年,日本学者杉田忠彰,根据线性断裂力学原理,研究了陶瓷切削过程的材料去除机理,提出了材料去除的三种模型:(1)不稳定裂纹扩展型,(2)裂纹残留型,(3)塑性变形型。他研制成功微细切削装置,放在SE M中直接观察了330-10004倍倍率下裂纹的产生,扩展和材料去除的脆性断裂过程。
Ó1983年,日本Kanazawa大学,K.Ueda利用断裂力学理论,初步探讨了材料的脆性断裂和塑性流动的关系,研究了材料塑性流动时的切削。
Ó1990年,日本Osaka大学,T.Nakasuji研究了光学零件的镜面切削,根据材料特性和切削参数,建立了由脆性到延性转变的模型和延性去除所需的必要条件,用上述观点实现了锗,硅和铌酸锂(LiNbO3)的镜面加工,粗糙度<20nm。
Ó1991年,日本Kanazawa大学,K.Ueda进一步用弹塑性断裂力学和J-积分方法研究了陶瓷材料脆性/延性转换模式。
Ó90年代,日本有几位学者开始用分子动力学仿真方法研究有色金属的材料去除机理,在1997年,日本Nagoyo工艺研究所T.Inamura,应用重组分子动力学原理对单晶硅以不同切削深度进行微细切削动
态仿真,研究了裂纹扩展和塑性流动的条件。结果表明,在真空条件下,无缺陷单晶在较大的切削范围里均可实现延性加工,而在大气压条件下临界切削深度的数值就小得多。
1.2切削工艺的研究
Ó1984年,鸣龙则彦在日本春、秋季学术演讲会上介绍了切削予烧结陶瓷的研究成果,对Al2O3陶瓷在500-1000e,Si3N4陶瓷在1100-1400e予烧结,切削成形后完全烧结,然后精磨制成零件,研究表明:
(1)干式切削中,CBN刀具切削1400e予烧结Si3N4寿命最长,陶瓷刀具切削Al2O3500-1000e予烧结陶瓷存在着最佳切削速度。
(2)低温予烧结陶瓷,由于强度低,可用负前角刀具大进给量切削,加工性最好。
(3)湿式切削,烧结金刚石刀具切削性能最佳。
通过予烧结,不仅比完全烧结后再磨削的成本降低,而且加工效率大大提高,因此是经济适用的重要工艺。
Ó1983年,中井哲男在3工业材料4上发表了切削完全烧结陶瓷的研究成果,研究指出:
(1)材料的硬度和断裂韧性是影响切削力的主要因素,由于硬度高,刃口难于切入,故径向力远大于其他分力达5-10倍。
(2)切削用量对温度有影响,其中切削速度影响最大。
(3)切削中刀具存在机械磨损,他学磨损和剥落,刃口的剥落是由于在热应力作用下晶界损伤和破裂所致。
目前,切削完全烧结陶瓷仍处于实验阶段,几个重要问题有待解决。
Ó1986年,Toyo大学,K.Uehara考虑到陶瓷切削的困难,采用氧乙炔火焰加热切削的方法,对莫来石和氮化硅陶瓷进行加热切削实验,测定了切削力,表面粗糙度,刀具磨损和切屑形成,发现由于切削区温度提高,陶瓷的脆性转化为塑性,在高温条件下两种陶瓷均
#
36
#5金刚石与磨料磨具工程6
具有金属切削的特性,加工表面粗糙度下降,刀具寿命显著提高,存在的问题在于刀具的冷却问题有待解决。
Ó1992年,日本T.Mariwaki在CIRP上发表了光学玻璃延性域切削的文章,指出在切削方向上,将超声振动作用于金刚石刀具上,进行钠钙玻璃端面切削,可获得R max=30nm的透明表面,实现延性域切削,通过切槽实验还弄清了由于超声振动,临界切削深度增大了。
Ó1998年,新加玻理化研究所F.Z.Fang进行单晶硅的金刚石纳米切削,采用0-25b前角刃具进行切深不断变化的锥面切削,并用SEM和AFT检测,予加工表面R a=23.8nm,R max=140nm,经延性域切削后,可稳定的获得R a=1nm的镜面,并发现:0b前角具有略大于切深的刀尖钝圆半径,产生了延性域切削所需的流体静水压力。
Ó2000年,F.Z.Fang又对ZKN7光学玻璃进行延性域切削,证实在临界切削厚度极限以下,用于裂纹扩展的能量大于塑性变形能,所以塑性变形起主导作用,可实现光学玻璃的纳米切削。
1.3金刚石切削机床的发展
Ó1962年,美国UNION C ARDIE公司超精密半球面车床,加工直径Á120mm,尺寸精度?0.6L m,R a=0. 025L m。
Ó1960-1984年,美国LLNL国家实验室DTM-1,DTM-2,DTM-3超精密金刚石车床,加工直径Á2100m m,导轨直线度0.1L m/1000mm,位移精度0. 013L m,温控20b?0.0025e,加工表面粗糙度R max=0. 007L m。
Ó80年代,英国格兰菲尔德C UPE研究所超精密金刚石镜面切削机床,加工直径Á1400mm,长600mm,径向刚度876N/L m,轴向刚度2360N/L m,机床分辨率0.015L m,加工工件平直度0.2L m,圆度0.4L m。
Ó1978年,荷兰菲利甫公司C OLATH数控超精密金刚石车床,加工直径Á200mm,长200mm,圆度<0. 5L m,R a=0.025L m。
Ó1980年,日本东京芝蒲公司超精密镜面切削机床,主轴回转精度0.05L m,轴向跳动0.2L m,形状误差<0.5L m,加工表面粗糙度R max=0.02L m。
Ó1984年,日本日立精工公司DPL-400型超精密磁盘车床,加工直径Á120mm,最小切深0.5L m,加工工件平直度0.2L m,R a=0.025L m。
2先进陶瓷材料的磨削加工
2.1先进陶瓷材料的磨削机理
Ó80年初,Frank和La wn首先建立了钝压痕器,尖锐压痕器和接触滑动三种机理分析研究模型,提出了应力强度因子公式K=A E#P/C3/2;根据脆性断裂力学条件K\K C;导出了脆性断裂的监界载荷P BC=C B# K;他又根据材料的屈服条件R\R Y,导出了塑性变形模式下临界载荷P YC=R Y3/C*3(或P YC=H Y3/C*3)。研究指出:陶瓷材料的去除机理通常为裂纹扩展和脆性断裂;而当材料硬度降低,压痕半径小,摩擦剧烈,并且载荷小时,就会出现塑性变形。
Ó1991年,东北大学郑焕文,蔡光起教授,对含钼金属陶瓷进行磨削实验,通过测定单位磨削力,磨削能和磨削比,以及SE M对表面和切削的观察,探索了金属陶瓷材料的去除机理。
Ó1989年,T.G.Bifano在ASME文献上明确提出加工脆性材料的延性域磨削新工艺,认为采用高刚度高分辨率精密磨床,通过控制进给率,就可使硬脆材料以延性域模式去除材料,并给出了临界磨削深度表达式:D C=0.15*(E/H)*(K C/H)2,根据能量守恒定律描述了延性域磨削时,进给率和材料特性的关系。
Ó1996年,美国麻省大学S.Malkin对陶瓷磨削机理进行了综述,认为陶瓷材料低成本高效率磨削的基础需要深入研究磨削机理,研究方法概括为压痕断裂力学法和加工观察法。压痕法将磨粒和工件间相互作用,用理想的小范围内压痕表示,分析应力,变形及材料去除的关系;而加工法包括测定磨削力,观察工件表面与切屑,进一步研究材料的去除机理,两者均为磨削机理的研究提供了重要见解。
Ó1994年,Keio大学,R.Rentsch将分子动力学方法首先用于磨削机理的研究,给出了第一个磨削过程的仿真结果,叙述了磨削中磨屑堆积的现象和切削过程仿真的区别。
Ó1998年,德国Ac hen生产工程研究所V.Sinhoff 利用杯形金刚石砂轮磨削光学玻璃进行了机理的研究,重点是研究脆性/延性转变的特性,并将材料中的应用分布,裂纹几何形状等损伤看成是磨粒几何形状,材料特性和外载荷等因素的函数,建立磨削评价模型,然后用T.G.Bifano能量守恒定律来描述材料的脆性去除向延性去除过程的转变过程。
2.2磨削工艺及磨削加工性的评价
80年初,日本学者富森,贵志浩三,田中义信等发表了多篇文章,阐述了Al2O3及Si3N4等陶瓷磨削的基本规律;影响磨削加工性的主要因素及金刚石砂轮的磨削性能,至今各国学者对各种先进陶瓷材料如Al2O3,Si3N4,ZrO2,Sialon,SiC,Mn-Zn铁氧体,单晶硅,光学玻璃和金属陶瓷等的磨削力,磨削热,表面质量,砂轮磨损及修整进行了系统的研究,并研制成多种具有复杂几何形状的高科技产品,已为许多工业部门所采用,已达到较高的水平。在这一领域下述几项成果具有较大的影响。
2.2.1在线电解修整金刚石砂轮(ELID)的精密磨削技术
Ó1990年,日本理化院Hitoshi Ohmori成功的开发
#
37
#
2001.4(124)
了ELID新工艺,采用微细磨粒铸铁纤维基金刚石砂轮,对硅片进行精密加工,采用普通机床在磨削过程中进行砂轮的在线修整,稳定的实现了硅片的镜面磨削。
Ó1995年,Hitoshi Ohmori又对ELID进行了进一步的研究,用几微米至亚微米金刚石磨粒的铸铁基砂轮对单晶硅,光学玻璃和陶瓷进行ELID磨削,系统的研究磨粒尺寸与粗糙度的关系,用SE M,AFT分析研究表面廓形,借助X射线,角度抛光和阶段腐蚀,研究次表面损伤,获得了高精度,优质表面,低次表面损伤的加工,表面粉糙度达几个埃,从而可代替研磨与抛光。
Ó1999年,D.Kramer提出了ECD(Electrochemical In-Process Controlled Dressing)技术,该研究与ELID不同,ECD过程不需求形成氧化膜和氢氧化物膜,而是通过测定磨粒刃口和工件表面状态来控制电化学的修整过程,据报导该技术在磨削陶瓷,PCB N,PCD和硬质合金过程中,显著改善了表面质量。
Ó1995年左右,哈尔滨工业大学袁哲俊教授等与日本理化院Hitoshi Ohmori合作,在国内开展了ELID 研究,在镜面加工技术领域取得了进展,并培养了许多人才。
2.2.2低表面粉糙度磨削
Ó1984年,日本富森等研究了Si3N4陶瓷普通磨削与火花磨削的区别,以及不同余量火花磨削的关系,杉田忠彰等在火花磨削基础上,利用磨削热水合反应这一界面反应,实现了Si3N4陶瓷R max<0.005L m低粗糙度磨削,实践证明火花磨削至今仍然是一种实用的加工技术。
Ó1990年,日本东京大学J.Ikeno采用电泳沉积方法研制成功磨粒均布的10-20纳米磨粒的磨块,采用该磨块磨削单晶硅片,加工表面无任何痕迹,Ra<0. 01L m。
Ó1994年,J.Ikeno用上述磨块制造出具有适当粘结强度的砂轮,由于砂轮的自锐和均衡的磨削负荷,加工硬脆材料时可得到R max<0.01L m的超光滑表面。
Ó1998年,日本Toyo大学Y.Tani采用电泳沉积工艺亦制成超细粒度的砂轮,对硅片进行切入磨削,获得R max<0.023L m的无损伤镜面。
2.2.3先进陶瓷的高效率磨削
Ó速度冲程磨削技术,1988年,I.Inasaki提出了先进陶瓷的3速度冲程磨削技术4,在平面磨床上增加一附加冲程工作台,用来提高工件速度,可以在磨削力不变的条件下显著提高磨削效率,但Ra增大,需要有后续的精磨工序。
Ó高密度金刚石砂轮的高效率磨削,将磨粒表面涂覆一层金属,防止磨粒破裂和改善导热性能,并增加SiC微粉使磨粒与砂轮基体受力得以缓冲,磨粒高密度化(约占体积的50%),这样可使切削刃口均匀一致,弹性系数提高,具备了高精度高效率的磨削能力。
Ó陶瓷结合剂金刚石砂轮高效率磨削:已开发成功陶瓷结合剂金刚石砂轮,这种砂轮成形修整容易,磨粒周围空隙大,冷却充分,磨粒结合力强,砂轮寿命长,故可以实现高精度高效率磨削。
Ó石材高效率磨削加工:90年代,刘培德教授在华桥大学建立了石材加工省重点实验室,研制成功大理石高效率切割砂轮,并开展了石材加工机理的研究,促进了该领域加工技术的进步。
2.3磨床与磨削中心的发展
Ó1980年,美国Moor公司M18金刚石砂轮磨床,机床具有油浴温控装置,可加工非圆形光学玻璃器件和红外幅射器件,加工精度亚微米级,加工效率高。
Ó1986年日本Tokyo University C ounterplans加工中心,机床备有各种砂轮,超声波打孔头及在线修
整装置,加工外圆,内孔,钻孔,加工质量好,效率高。
Ó1989年,Chubu大学Toyoda机床公司Toyoda平面磨床,备有零膨胀系数玻璃陶瓷主轴,亚微米切深和平面度,加工光学玻璃,陶瓷及铁氧体,R ma x=5nm。
Ó1990年,英国格兰菲尔德大学C UPE大型超精密加工机床,空气主轴,回转精度0.05L m,机床分辨率0.015L m,径向刚度876N/L m,轴向刚度2630N/L m,加工工件平面度0.2L m,圆度0.4L m。
Ó1991年,日本Toshiba公司CNC超精密磨床,用4L m细粒度金刚石砂轮磨削玻璃陶瓷,形状精度0.3L m/1000mm(曲率半径),Ra=0.6nm。
Ó1995年,日本Toyoda公司五坐标超精密数控磨床,机床位移分辨率10nm,转角分辨率0.00002b,加工SiC表面(C VD沉积),形状精度0.5L m/100*500mm2,粗糙度<5nm(rms)。
Ó1996年,日本THK有限公司智能控制平面磨床,刚度高,隔热好,备有智能控制系统,机床平面度0.5L m/200*200m m2,加工陶瓷,玻璃及硅片,平面度0.3L m/125*125mm2,R max=5nm。
3先进陶瓷材料的研磨与抛光
3.1先进陶瓷的研磨与抛光机理
研磨加工一般使用较大粒径的磨粒,其刃口曲率半径较大,常采用钝角压痕器的磨削分析模型,在研磨硬脆材料时,磨料具有滚压作用,而嵌入研具中磨粒的外露刃口通过微切削作用而去除材料;
抛光使用较小粒径的磨粒,曲率半径小,可用锐角压痕器磨削磨型,加工表面的抛光是以磨粒的微小塑性切削,生成切屑而去除材料的,此外由于接触表面局部高温和高压,生成化学反应物由抛光盘不断将材料去除的;
当用软质研磨抛光盘时,可用伴随着滑动的压痕器磨削模型,材料是以局部微裂纹扩展,塑性流动和界
#
38
#5金刚石与磨料磨具工程6
面反应去除材料的。
3.2研磨抛光工艺的实验研究
研磨抛光历史悠久,应用广泛,而又在不断发展,各国学者在此领域作了大量的研究工作,对于硅,砷化钾半导体材料,蓝宝石,铌酸锂(LiNbO3)光电子材料,压电材料,光学玻璃,磁性材料和先进陶瓷等硬脆材料的研磨抛光技术已达到一个新的水平,发表了大量的论文论述,我国浙江工业大学袁巨龙教授作了系统的研究工作,并发表了3功能陶瓷的超精密加工技术4专著。促进了研磨抛光技术的发展。
3.3先进陶瓷研磨抛光新工艺
Ó弹性发射加工技术(E.E.M)森勇藏等利用极微小磨粒,以接近水平的方向和加工表面碰撞,以原子级加工单位去除材料。由于不与工件表面接触,因此可得到无损伤表面,当使用聚氨基甲酸脂球为工具时,采用ZrO2粉末加工单晶硅,表面粗糙度达5埃。
Ó液体浮动研磨与抛光技术,渡边纯二等采用的抛光盘沿圆周均布多个斜面槽,通过圆盘转动,由液体契形成液体动压使工件悬浮,处于浮动间隙中的研磨抛光粉对工件进行抛光,抛光硬脆材料时可得到不平度0.3L m/Á76mm,表面粗糙度1nm。
Ó界面反应抛光技术,当工件与磨粒摩擦界面处于高温高压状态时,工件表面上容易形成一层化合物,在表层深度极浅的反应物很容易通过研抛而去除:机械化学固相反应抛光,安永畅男等研究了以Al2O3(青玉)和SiO2(石英玻璃)在1100K,1300K和1500K高温高压下接触界面上的界面反应,发现在极
短时间里就生成了数十埃的不稳定的机械化学固相反应物-蓝晶石,加快了研磨抛光进程,可获得无损伤表面。
水合反应抛光,杉田忠彰等研究了Al2O3(青玉), MgO和SiO2(石英玻璃)等氧化物陶瓷的水合反应,在常温下水合反应很困难,但在高温高压下,Al2O3(青玉)的水合反应物为Al(OH)3,其一般形式为Al2O3* xH2O,在高温高压下形成的水合反应物活性高,故研抛速度显著提高。
Ó磁悬浮抛光技术,利用磁力悬浮现象,在磁流体中加入非磁性磨料,当工件相对磨料进行旋转运动或相对运动时,就实现了工件表面的抛光。1990年,T. Shimida使用涂覆金刚石的磁性磨粒抛光直径Á12mm 的Si3N4圆棒,弄清了加工特性,当予加工Ra=0. 45L m,经研抛后Ra=0.04L m,而且得到了半径0.01mm 的倒棱面。4先进陶瓷材料的孔加工技术
4.1陶瓷材料孔的超声波加工
Ó50年代出现了超声加工机,过去主要采用镍片组成的换能器,能量转换率低仅为60%,虽然效率低,这种超声机械至今仍在使用。
Ó60年代,英国Ha well原子能研究中心提出超声旋转加工法,70年代原苏联和美国亦开始研究,1989年日本研制成功超声旋转加工样机,加工效率明显提高,80年代,美国B ranson公司研制成功的UMT-5型加工机是功能比较齐备,性能比较先进的代表。
Ó90年中科院声学所林中茂与11所合作研制成超声旋转加工机床,解决了光学玻璃数十毫米长的深孔加工,在加工其他材料时效率也显著提高。
Ó1996年天津大学研制开发了一台陶瓷小孔超声波磨削加工机床,采用无冷,压电陶瓷换能器,对各种先进陶瓷小孔加工进行了系统研究,和普通超声加工相比,效率可提高5-10倍。
4.3陶瓷材料的小孔激光加工
1960年以来,激光技术发展迅速,采用YAG脉冲激光发生器发出的激光光束,经聚光镜聚焦,使被加工表面聚焦部位气化,熔融和蒸发,去除材料实现小孔加工。
Ó日本安永肠男等采用YAG固体激光器对钻石,红宝石,Al2O3陶瓷进行了孔加工,加工孔径0.05-0. 2mm,厚度0.3-3mm,脉冲20-50次,加工效率非常高,加工时间仅2-5秒。
Ó1996年,天津激光研究所与天津大学合作,在YAG脉冲激光三坐标数控加工机床(美国)上,对几种陶瓷材料进行了小孔加工的系统实验,发现导热性能良好的Si3N4陶瓷小孔激光加工,效率高,质量好。而导热系数小的ZrO2,SiC陶瓷需要采取相应的措施,防止由于热应力集中导致工件的断裂。
参考文献
1Annals of the CIRP,Vol.30-49/1-2/1981-2000
2Trans.ASME,J.Eng.Ind.1990-1999
3樱井良文等.新陶瓷超精密工学.黄忠良译.复汉出版社,1983
4海野邦昭著.高能率机械加工.日刊工业新闻社,1985
5袁巨龙著.功能陶瓷的超精密加工技术.哈尔滨工业大学出版社, 2000
作者简介:于思远,男(1935-),汉族,天津大学材料学院教授,博导,主要从事精密陶瓷加工及纳米技术研究。
(收稿日期:2001-04-05)
(编辑:王孝琪)
#
39
#
2001.4(124)
Relationship between the Thermostability of C BN and Its Crystal Shape and Crystallinity
Y AN Guo jin et al(13) ,,,,,,,,,,,,
Abstract:Thermostability is one of the important inde xes of CBN.This paper studied the relationship between the ther-mostability of CBN and its crystal shape and crystallinity by using mineral microscope and DTA.It is found that,CB N crystals with perfact shape,clear planes and transparent have high thermostatility.Those with micropores on the crys-tal plane have lo wer crystallinity and thus lower thermostabi-l ity.B y means of reflecting microscope,we can test the ther-mostatility of CBN,quickly and reliably.
Key Words:CBN thermostability crystallinity Optimization of the Structure of Layered Diamond Saw Blade SHI Xiaoliang et al(15) ,,,,,,,,,
Abstract:This paper analysed the working mechanism and sintering process of layered segment of diamond saw blade by means of hotpressing sintering.Shortages of commonly used layered struc ture were pointed out.A weak-impregnated lay-er structure was proprosed and chemical plated diamond grits are suggested.Experiment results sho wed that ho-t damage of diamonds was avoided and long working life and excellent ef-ficiency of diamond saw blade were obtained.
Key Words:dia mond sa w blade layered segment
weak-impregnated layer
Some Practical Means for improving Diamond Tool Quality JIANG Rongchao et al(17) ,,,,,,,
Abstract:On the basis of our practice and investigation, some effective measures to further improve the quality of dia-mond tool are discussed.First of all,good performanced, coarse crystal,thermally stable,ultrahigh grade dia monds are needed.In order to improve the diamond retention in the bonds,it is suggested to add carbide former element metal in bond or use c oated diamond.Ultra-fine metal powder and pre-alloyed metal are suggested to use in the matrix for better bond performance.Process of powder granulation is promot-ed in producing segments to improve the distribution of dia-monds in the segment,increase the efficiency of cold press-ing,decrease the consumption of mould.Analysis and com-parison are made on commonly used sintering furnaces,their advantages and disadvantages are pointed out.Dia mond wire saws are getting wider use,HIP and HP welding are pro-posed for making the beads.Key Words:diamond tool quality improvement Manufacture of One-time Electroplated Diamond Saw Blade LIU Junjie(21) ,,,,,,,,,,,,
#GRINDING#
Progress of Advanced-ceramic Machining Technology
YU Siyuan et al(36) ,,,,,,,,,,,,,
Abstract:As the progress of advanced ceramic materials, there has been intense interest in developing the machining technique of ceramic material.On the basis of inquiring re-lated references recent years,this paper has systematically described the machining technique progress of cera mic mate-rial at home and abroad.Cutting,grinding,lapping,po-l ishing and hole machining technique of ceramic material have been emphasized in three aspects:material re moval mechanism,high efficient machining technology with good quality and machine tools.
Key Words:advanced ceramics machining progress Superfinishing of Engineering Ceramic Material
MAO Zhimin et al(40) ,,,,,,,,,,,,
Abstract:This paper analyzed the superfinishing principle of engineering ceramic material,studied the effec t of superfin-ishing process parameters,such as the pressure,amplitude and frequenc y of grinding head,the rotate speed of work-piece,and the machining time,on the workpiece surface roughness,and obtained a group of optimized superfinishing process parameters.The experiment result showed that it was completely feasible to apply superfinishing process to ceramic material.
Key Words:engineering ceramic superfinishing ortho experiment surface roughness process pa-
rameter
Aplication of Experimental Designing in Developing New Abrasive Products Z HANG Shushen et al(45)
,,,
#Dr.Fritsch.s Products#
Automatic Polishing Machine for Economic Saw Blade mannfacture(52)
,,,,,,,,,,,,,,
#De Beers Column#
Progress of the Researches on Superabrasive cutting Tool Materials(53)
,,,,,,,,,,,,,
(Translation by W ANG Qin)
更多推荐
加工,磨削,切削,陶瓷,材料,研究,表面,技术
发布评论