苏州租房网站-绿茵生态 传闻
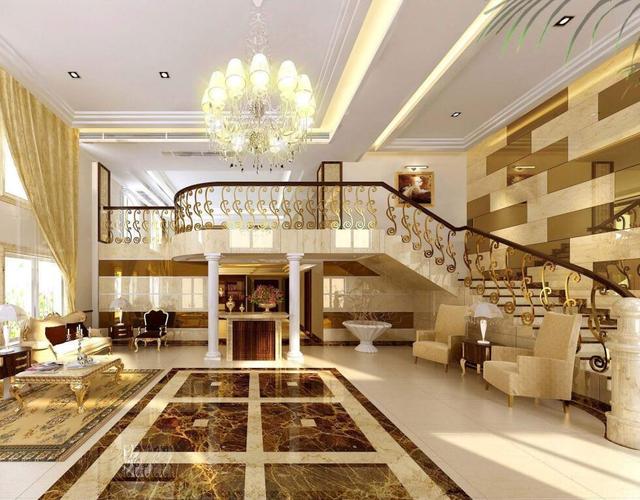
2023年10月5日发(作者:阎天恩)
压力管道元件制造工艺汇编
压力管道元件制造工艺汇编
(YGYG-01~YGYG-14)
青岛海利通
2021年01月20日
目 录
YGYG-01 热推成型钢制无缝弯头制造工艺…………………………………………… 1
YGYG-02 冷推成型钢制无缝弯头制造工艺…………………………………………… 4
YGYG-03 热煨弯管制造工艺…………………………………………………………… 8
YGYG-04 冷煨弯管制造工艺……………………………………………………………12
YGYG-05 钢制无缝异径管接头制造工艺………………………………………………14
YGYG-06 钢制无缝三通制造工艺………………………………………………………17
YGYG-07 钢制管帽制造工艺……………………………………………………………20
YGYG-08 钢制有缝管件制造工艺………………………………………………………24
YGYG-09 螺旋炉管制造工艺……………………………………………………………28
YGYG-10 热煨弯管防腐通用工艺………………………………………………………32
YGYG-11 手工电弧焊通用工艺…………………………………………………………37
YGYG-12 氩弧焊通用工艺………………………………………………………………40
YGYG-13 热处理通用工艺………………………………………………………………43
YGYG-14 压力试验通用工艺……………………………………………………………46
附件1 热推成型钢制弯头下料尺寸…………………………………………………48
附件2 冷推成型钢制弯头下料尺寸…………………………………………………49
YGYG-01 热推成型钢制无缝弯头制造工艺
1.总那么
为确保热推成型钢制无缝弯头的产品质量,规范制造工艺,严格程
序治理,特制订本工艺文件。本工艺适用于我公司生产的Φ48~Φ529—
1.5D钢制无缝弯头热推成型制造过程。
2.标准依据
GB/T 12459-2005«钢制对焊无缝管件»
GB/T 8163-1999«输送流体用无缝钢管»
3.制造工艺
热推成型钢制无缝弯头的整个制造工艺流程如下:
原材料入厂检验 → 下料 → 推制 → 整形 → 坡口 → 除锈 →
刷漆 → 标识 → 检验入库
3.1原材料入厂检验
3.1.1热推弯头用钢管必须符合相应钢管制造标准的规定。并应有制造公
司质量证明书,钢管入厂应由质检员和保管员对钢管口径、壁厚、外观质
量等进行检查验收。
3.1.2管材实物的标记、炉批号与材质证明书相符合时,可不进行复检。
同时也能够按照需方的要求对化学成份分析,力学性能分析、金相组织分
析进行复检。
3.1.3无缝钢管的内外表面不得有裂缝、折迭、皱折、离层、裂纹和结疤
等缺陷。
3.1.4钢管应整齐排列于料场或车间厂房内,不得乱摆乱放,不得有重物
挤压、碰砸,吊装时不得有碰撞现象发生。
3.2下料
3.2.1小口径钢管下料采纳锯床下料,大口径的采纳火焰自动切割器下
料。
3.2.2应依照下料规格,严格按照附表1中的尺寸参数进行下料。
3.2.3下料后应将管端毛刺或氧化铁打磨洁净,管段内外表面假设有油污
应进行清理。
3.3推制
3.3.1推制设备为液压式推制机,加热设备为中频电加热装置。
3.3.2依照弯头规格采纳最正确推制速度。
3.3.3采纳最正确加热功率与合理的冷却水流量。
3.3.4由于芯棒头在推制过程中的自然磨损,每次推制前均要对芯棒头尺
寸参数进行修磨校准。
3.3.5为了保证推制过程中的良好润滑,坯料内表面要涂刷石墨粉,采纳
合理石墨粉涂量,保证涂层厚度平均。
3.4整形
3.4.1整形设备采纳四柱液压压力机。
3.4.2整形胎具安装前应认真修磨,不准有凸起和毛刺,防止整形过程中
划伤弯头。
3.4.3上下整形胎具安装应保证良好的对中。
3.4.4弯头整形工作应在推制成型后赶忙进行,整形后弯头在静止的空气
中自然冷却。
3.5坡口
3.5.1采纳专用坡口设备进行机械式坡口。
3.5.2依照弯头规格选择安装对应的坡口胎具。
3.5.3在第一个弯头坡口时由质检员现场协助测量调整,使弯头整体尺寸
参数符合标准要求,然后利用坡口机导轨限位开关固定尺寸,即可进行批
量加工。
3.5.4坡口产生的毛刺应修磨洁净。
3.5.5坡口角度37.5±2.5°。
3.6除锈
3.6.1弯头刷漆前应对其表面进行除锈处理,目的是去除浮锈,增加油漆
附着力。
3.6.2在条件承诺的情形下,尽可能采纳抛丸除锈机对弯头进行抛丸除
锈。
3.6.3除锈成效以去掉浮锈,见到金属本色为宜。
3.7刷漆
3.7.1弯头刷漆采纳黑色或红色防锈漆。
3.7.2刷漆应平均,无漏点和流坠。
3.8标识
3.8.1成品弯头喷涂耐久性标识,字迹清晰。
3.8.2标识方法假设需方有规定,那么按需方规定执行;假设需方无规定,
那么依照产品性能按标准执行。
3.9检验入库
3.9.1弯头入库前应由质检员对几何尺寸和外观进行检验。
3.9.2弯头内外表面不得有划伤沟槽或碰撞形成的明显凹陷,没有裂纹、
结疤、折叠、分层等缺陷。
3.9.3几何形状检验按照GB/T 12459-2005标准执行。
3.9.4检验应填写«钢制弯头检验记录表»〔YGBG-02〕。
3.9.5弯头检验合格后方可入库,应按规格型号整齐摆放于指定库存区
域,并保证其不受污损、碰撞。
YGYG-02 冷推成型钢制无缝弯头制造工艺
1.总那么
为了确保冷推成型钢制无缝弯头的产品质量,规范制造工艺,严格程
序治理,特制订该工艺。本工艺适用于我公司生产的Φ32~Φ426—1.5D
冷推碳钢及不锈钢无缝弯头的制造过程。
2.依据标准
GB/T 12459—2005«钢制对焊无缝管件»
GB/T 8163—1999«输送流体用无缝钢管»
GB/T 14976-2002«流体输送用不锈钢无缝钢管»
3.制造工艺
冷推成型碳钢〔不锈钢〕无缝弯头制造工艺流程如下所示:
原材料入厂检验 → 下料 → 抛丸除锈〔清洗油污〕 → 涂层 → 推
制 → 热处理 → 坡口 → 除锈刷漆〔酸洗钝化〕→ 标识 → 检验入库
3.1原材料入厂检验
3.1.1冷推弯头用钢管必须符合相应钢管制造标准的规定。并应有制造公
司质量证明书,钢管入厂应由质检员和保管员对钢管口径、壁厚、外观质
量等进行检查验收。
3.1.2管材实物的标记、炉批号与材质证明书相符合时,可不进行复检。
同时也能够按照需方的要求对化学成份分析,力学性能分析、金相组织分
析进行复检。
3.1.3无缝钢管的内外表面不得有裂缝、折迭、皱折、离层、裂纹和结疤
等缺陷。
3.1.4钢管应整齐排列于料场或车间厂房内,不得乱摆乱放,不得有重物
挤压、碰砸,吊装时不得有碰撞现象发生。
3.2 下料
3.2.1下料设备采纳角度可调式带锯床。
3.2.2下料应严格保证长度和角度〔具体尺寸见附表2〕,否那么无法实现
推制时的自动操纵。
3.2.3为了方便快速下料,先锯大角度一端,每两节一起下料。
3.2.4为了防止偏斜,能够采纳角尺、铅坠等操纵。
3.2.5为了增加推制时的受力面积,大角度一端要进行尖角平口。
3.2.6锯切后产生的毛刺要打磨洁净,内弧尖角要光滑过度。
3.3抛丸除锈〔清洗油污〕
3.3.1冷推碳钢弯头下料后应进行抛丸除锈。
3.3.2利用悬挂式抛丸除锈机进行除锈,除锈至露出金属本色。
3.3.3不锈钢下料后要清洗掉表面的油污。
3.4涂层
3.4.1将氯化橡胶配合成一定浓度的涂层液,盛放在专用的涂层液槽内。
涂层液槽应远离火源。
3.4.2将清理洁净的管段浸泡或涂刷后悬挂晾干,使氯化橡胶在管段内外
表面形成一层具有专门强附着力的隔离膜。
3.4.3为了增加润滑,减少推制过程中管子与胎具间的摩擦,涂层晾干后
应在管段内外表面刷上一层掺有二硫化钼的动物油脂。
3.5推制
3.5.1按推制弯头的规格选择相应的外模、芯头、定位块、推杆等进行装
换模。
3.5.2推制前应认真检查模具芯棒规格是否合适,螺栓是否固定牢靠,空
载打自动试车,看各个行程限位开关是否灵敏有效。
3.5.3推制完第一个弯头后调好侧推缸行程限位开关。
3.5.4管段放入模具时要注意防止偏斜,有平口的一端置于推杆一侧。
3.5.5推制机应由专人操作,假如推不动或显现紧急情形,应赶忙按紧停
开关,升起锁模油缸,开模进行检查。
3.5.6推制时工具和杂物不要放在设备工作台面上,启动推制开关后躯体
不能伸入工作台。
3.6热处理
3.6.1冷推成型后的弯头要进行热处理,目的是排除冷加工过程中产生的
应力。
3.6.2冷推碳钢弯头加热到600℃~650℃,恒温一定时刻〔恒温时刻为每
25mm壁厚1h,且不得少于15min〕,随炉冷却至400℃以下后自然冷却。
3.6.3冷推不锈钢弯头加热到1050℃左右,出炉后急冷,冷却介质为水。
3.7坡口
3.7.1坡口设备采纳专用弯头坡口机。
3.7.2依照弯头规格选择安装对应的坡口胎具。
3.7.3在第一个弯头坡口时由质检员现场协助测量调整,使弯头整体尺寸
参数符合标准要求,然后利用坡口机导轨限位开关固定尺寸,即可进行批
量加工。
3.7.4坡口产生的毛刺应修磨洁净。
3.7.5坡口角度37.5±2.5°。
3.8除锈刷漆〔酸洗钝化〕
3.8.1冷推碳钢弯头坡口后进行抛丸除锈处理,并刷防锈油漆。
3.8.2不锈钢弯头坡口后进行酸洗钝化处理。
3.9标识
3.9.1成品弯头喷涂耐久性标识,字迹清晰。
3.9.2标识方法假设需方有规定,那么按需方规定执行;假设需方无规定,
那么依照产品性能按标准执行。
3.10检验入库
3.10.1弯头入库前应由质检员对弯头几何尺寸和外观进行检验。
3.10.2弯头内外表面不得有划伤沟槽或碰撞形成的明显凹陷,没有裂纹、
结疤、折叠、分层等缺陷。
3.10.3几何形状检验按照GB/T 12459-2005标准执行。
3.10.4检验应填写«钢制弯头检验记录表»〔YGBG-02〕。
3.10.5弯头经检验合格后方可入库,按规格型号整齐摆放于指定库存区
域,并保证其不受污损、碰撞。
YGYG-03 热煨弯管制造工艺
1.总那么
为确保钢质弯管的产品质量,规范制造工艺,严格程序治理,特制
定该工艺。本制造工艺标准适用于规格型号φ89mm-φ820mm,采纳中频感
应加热煨制的钢质弯管、不锈钢弯管加工制造过程。
2.依据标准
SY/T 5257-2004«油气输送用钢制弯管»。
GB 50235-97«工业金属管道工程施工及验收规范»
GB/T 8163-1999«输送流体用无缝钢管»
GB/T 14976-2002«流体输送用不锈钢无缝钢管»
GB 5310-1995«高压锅炉用无缝钢管»
GB 3087-1999«低中压锅炉用无缝钢管»
GB/T 9711.1«石油天然气工业 输送钢管交货技术条件 第1部分:A
级钢管»
GB/T 9711.2«石油天然气工业 输送钢管交货技术条件 第2部分:B
级钢管»
GB/T 9711.3«石油天然气工业 输送钢管交货技术条件 第3部分:C
级钢管»
API Spec 5L:2000«管线钢管»
3.制造工艺
热煨弯管制造工艺流程如下:
原材料入厂检验 → 煨制前预备 → 煨制 → 坡口 → 〔热处理〕→
成品检验
3.1原材料入厂检验
3.1.1弯管用钢管必须符合相应钢管制造标准的规定。并应有制造公司质
量证明书,钢管入厂应由质检员和保管员对钢管口径、壁厚、外观质量等
进行检查验收。
3.1.2管材实物的标记、炉批号与材质证明书相符合时,可不进行复检。
同时也能够按照需方的要求对化学成份分析、力学性能分析,金相组织分
析进行复检。
3.1.3钢管表面应光滑,不得有结疤、凹凸、不平、裂纹、重皮等缺陷,
不得有过烧现象存在。
3.1.4钢管应整齐排列于车间厂房内,不得乱摆乱放,不得有重物挤压碰
砸,吊装时不得有碰撞现象发生。
3.2煨制前预备
3.2.1煨制设备采纳中频链条〔液压〕推制机,依照管道口径和曲率半径
的不同进行工装的预备和装夹。
3.2.2假设不同口径,曲率半径的弯管煨制时,一样按照从小到大或从大
到小的加工顺序预备工装。
3.2.3卡具必须保证在夹管时的有力夹紧,确保无滑动和放松变位现象。
3.2.4调整摇臂,使卡头的垂直中心线到摆臂固定轴心的距离公差操纵在
2mm之内,从而保证弯管曲率半径。
3.2.5选择或制作相应规格的中频感应圈,感应圈喷水角度为垂直线至钢
管前进方向侧45°左右,喷水孔采纳Φ1mm或Φ1.2mm钻头打孔,喷水孔
均布于感应圈内侧一边,依照感应圈大小调剂孔的间距,感应圈越大,孔
间距越大。
3.3煨制
3.3.1钢管上线后对直管段长度和运算所得弯曲部分的长度进行画线。
3.3.2直管段长度应符合以下要求:DN≤500mm的弯管,直管段不小于
250mm;DN>500mm的弯管,直管段不小于500mm;假设需方有要求,那么
按需方要求协商一致。
3.3.2保证钢管被可靠定位并夹紧,选用摇臂强度要达到使用要求,在生
产中不发生变形。
3.3.3依照弯管口径、壁厚和曲率半径选择合理的中频输出功率和推制速
度。口径和壁厚越大,需要的中频功率越高,曲率半径越小,推制速度应
相应降低,以保证内弧质量和圆度。
3.3.4在煨制过程中不应有任何中断停留。
3.3.5用直缝钢管煨制时,如设计图无要求,其焊缝宜位于弯管中性面邻
近的外弧侧或内弧侧距中性面5°~10°范畴内。
3.3.6冷却水应采纳洁净自来水,冷却水经管路回流到冷却池冷却后循环
使用。
3.3.7批量加工时,为了便于辨论和查找,煨制成型后应将弯管的口径、
壁厚、曲率半径、角度和材质等标识在显著位置。等所有工序完成后按需
方要求或标准进行正规标识。
3.4坡口
3.4.1坡口采纳机械式坡口或火焰自动切割器切割坡口。
3.4.2当设计图对管端坡口有规定时,应符合设计图纸要求。
3.4.3当弯管壁厚大于与之相焊接的直管壁厚2mm时,应采纳内削边形式,
内坡角度不大于15°。
3.5热处理
3.5.1热煨碳钢弯管一样不需热处理。
3.5.2对L415或X60及以上钢级和处于酸性环境的弯管应进行热处理。
其他钢级或钢号的弯管由制造商与购方商定在弯制后是否需要进行热处
理。
3.5.3对公称直径大于或等于100mm,或壁厚大于或等于13mm的中、低合
金弯管,应按设计文件的要求进行热处理。
3.6成品检验
3.6.1弯管内外表面应光滑,无尖锐缺口、分层、刻痕、结疤、发裂、折
叠、撕裂、裂纹、裂缝等缺陷和缺欠,假设承诺修磨,那么修磨处应圆滑。
3.6.2弯管表面应无硬点,无过热、过烧存在。
3.6.3壁厚减薄率、圆度、弯曲角度、弯曲半径等几何尺寸和几何形状偏
差应符合标准要求。由质检员进行测量检验并填写«钢制〔高压注汽〕弯
管检验记录表»〔YGBG-03〕。
YGYG-04 冷煨弯管制造工艺
1.编制说明
为了保证冷煨弯管的产品质量,以优质的产品服务于用户,特制定了
该项制造工艺。本工艺适用于我公司Φ22-Φ114mm的冷煨弯管产品制造。
2.编制依据
GB 50235-97«工业金属管道工程施工及验收规范»
GB/T 8163-1999«输送流体用无缝钢管»
GB/T 14976-2002«流体输送用不锈钢无缝钢管»
GB 5310-1995«高压锅炉用无缝钢管»
GB 3087-1999«低中压锅炉用无缝钢管»
3.制造工艺
冷煨弯管的制造工艺流程如下:
原材料入厂检验 → 工装预备 → 下料 → 放样 →煨制 → 检验
3.1原材料检验
3.1.冷煨弯管用钢管必须符合相应钢管制造标准的规定,并应有制造公司
质量证明书,同时由检验部门对规格型号、外观等进行检查验收。
3.1.2管材实物的标记、炉批号与材质证明书相符合时,可不进行复检。
同时也可按需方要求决定进行复验。复验应包括化学成分分析、力学性能
分析,并符合钢管生产标准的有关规定。
3.1.3钢管表面应光滑,不得有结疤、凹凸、裂纹、折叠。以及超过壁厚
下偏差的缺陷、不得有过烧现象。
3.1.4关于甲方带料的钢管由保管员对规格、数量等进行验收。
3.1.5钢管应整齐排列于车间公司房以内,不得乱摆乱放,不得有重物挤
压、碰砸,吊装时不得发生碰撞。
3.2工装预备
3.2.1冷煨用弯管机设备或手动冷煨工装状况必须良好,运转灵活。
3.2.2选用冷煨弯管胎具必须与管径相符,假如需要芯棒,芯棒外壁与管
内壁间隙宜操纵在0.5mm之内。
3.2.3关于小半径采纳转胎煨制,大半径的采纳滚轮进行滚压成型。
3.3下料
3.3.1按要求长度进行切割下料。
3.3.2下料工具一样采纳无齿锯,依照需要可采纳锯床等其它下料工具。
3.2.3严格操纵下料,依照运算的下料长度下料进行切割下料。
3.2.4下料后管端毛刺应打磨洁净。
3.4放样
3.4.1依照设计或需方要求进行放样。
3.4.2放样在平台上进行,对半径较大的能够在平坦的地面进行。
3.4.3必要时可制作样板。
3.4.4对甲方提供样管的可省略此工序。
3.5煨制
3.5.1煨制前应在起弧位置画线。
3.5.2有芯棒时,需要对管子内壁进行涂油润滑。
3.5.3将管子牢固地装卡到冷煨机上,启动转胎进行煨制。
3.5.4关于一根管需要煨制多个平面弯的,需要利用水平尺进行调平。
3.5.5弯管表面不得有裂纹、起皱等质量缺陷,如在生产中发觉上述问题,
应停止生产进行整改处理。
3.6检验
3.6.1成品出厂前由质检员对表面质量和几何尺寸等进行检查验收。
3.6.2也可由甲方现场验收确认后出厂。
YGYG-05 钢制无缝异径管接头制造工艺
1.总那么
为确保钢制无缝异径管接头的产品质量,规范制造工艺,严格程序治
理,特制定该工艺。本工艺适用于我公司生产的φ25mm-φ426mm异径管
接头加工制造过程。
2.依据标准
GB/T 12459-2005«钢制对焊无缝管件»
GB/T 8163-1999«输送流体用无缝钢管»
3.制造工艺
钢制无缝异径管接头的加工工艺流程如下:
原材料入厂检验 → 下料 → 压制 → 热处理 → 坡口→ 除锈 →
刷漆 → 标识 → 检验入库
3.1原材料入厂检验
3.1.1钢制无缝异径管接头用钢管必须符合相应钢管制造标准的规定。并
应有制造公司质量证明书,钢管入厂应由质检员和保管员对钢管口径、壁
厚、外观质量等进行检查验收。
3.1.2管材实物的标记、炉批号与材质证明书相符合时,可不进行复检。
同时也能够按照需方的要求对化学成份分析,力学性能分析、金相组织分
析进行复检。
3.1.3无缝钢管的内外表面不得有裂缝、折迭、皱折、离层、裂纹和结疤
等缺陷。
3.1.4钢管应整齐排列于料场或车间厂房内,不得乱摆乱放,不得有重物
挤压、碰砸,吊装时不得有碰撞现象发生。。
3.2下料
3.2.1采纳锯床或火焰自动切割器进行下料。
3.2.2下料长度应符合技术要求。
3.2.3切割完的管段采纳车削法平坦两个端面。
3.2.4保证两端面对轴线的垂直度偏差和两端面的平行度偏差。
3.3压制
3.3.1压制时应依照规格型号选取对应的压制胎具,动力设备为四柱液压
机,压制前应检查设备,确认其处于良好运转状态。
3.3.2为降低摩擦,管段表面应进行润滑。
3.3.3胎具在液压机工作台面及管段在胎具内均应放正,管段上端与液压
机工作台面尽量保持垂直,以保证压制时管段平均受力。
3.3.4压制过程中,如发觉管段偏斜,应赶忙停机进行校正。
3.3.5对变径大的异径管接头可采取多次压制的方法,每次压制后均需要
进行热处理。
3.4热处理
3.4.1异径管接头压制成型后应进行热处理,目的是排除冷压过程中产生
的应力。
3.4.2加热到600℃~650℃,恒温一定时刻〔恒温时刻为每25mm壁厚1h,
且不得少于15min〕,随炉冷却至400℃以下后出炉自然冷却。
3.5坡口
3.5.1坡口设备采纳一般车床。
3.5.2坡口产生的毛刺应修磨洁净。
3.5.3坡口角度37.5±2.5°。
3.6除锈
3.6.1刷漆前应对异径管接头表面进行除锈处理,目的是去除浮锈,增加
油漆附着力。
3.6.2在条件承诺的情形下,尽可能采纳抛丸除锈机对其进行抛丸除锈。
3.6.3除锈成效以去掉浮锈,见到金属本色为宜。
3.7刷漆
3.7.1异径管接头刷漆采纳黑色或红色防锈漆。
3.7.2刷漆应平均,无漏点和流坠。
3.8标识
3.8.1成品异径管接头应进行耐久性标识,字迹清晰。
3.8.2标识方法假设需方有规定,那么按需方规定执行;假设需方无规定,
那么依照产品性能按标准执行。
3.9检验入库
3.9.1异径管接头入库前应由质检员对几何尺寸和外观进行检验。
3.9.2异径管接头内外表面不得有划伤沟槽或碰撞形成的明显凹陷,没有
裂纹、结疤、折叠、分层等缺陷。
3.9.3几何形状检验按照GB/T 12459-2005标准执行。
3.9.4检验应填写«异径管接头检验记录表»〔YGBG-04〕。
3.9.5异径管接头检验合格后方可入库,应按规格型号整齐摆放于指定库
存区域,并保证其不受污损、碰撞。
YGYG-06 钢制无缝三通制造工艺
1.总那么
为确保钢制无缝三通的产品质量,规范制造工艺,严格程序治理,特
制定该工艺。本工艺适用于我公司生产的钢制无缝三通加工制造过程。
2.依据标准
GB/T 12459-2005«钢制对焊无缝管件»
GB/T 8163-1999«输送流体用无缝钢管»
3.制造工艺
钢制无缝三通的加工工艺流程如下:
原材料入厂检验 → 下料 → 压制 → 热处理 → 坡口→ 除锈 →
刷漆 → 标识 → 检验入库
3.1原材料入厂检验
3.1.1钢制无缝三通用钢管必须符合相应钢管制造标准的规定。并应有制
造公司质量证明书,钢管入厂应由质检员和保管员对钢管口径、壁厚、外
观质量等进行检查验收。
3.1.2管材实物的标记、炉批号与材质证明书相符合时,可不进行复检。
同时也能够按照需方的要求对化学成份分析,力学性能分析、金相组织分
析进行复检。
3.1.3无缝钢管的内外表面不得有裂缝、折迭、皱折、离层、裂纹和结疤
等缺陷。
3.1.4钢管应整齐排列于料场或车间厂房内,不得乱摆乱放,不得有重物
挤压、碰砸,吊装时不得有碰撞现象发生。。
3.2下料
3.2.1采纳锯床或火焰自动切割器进行下料。
3.2.2下料长度应符合技术要求。
3.2.3切割完的管段采纳车削法平坦两个端面。
3.2.4保证两端面对轴线的垂直度偏差和两端面的平行度偏差。
3.3压制
3.3.1压制时应依照规格型号选取对应的压制胎具,动力设备为三通液压
成型机,压制前应检查设备,确认其处于良好运转状态。
3.3.2正确调整各限位开关,检验各操纵开关的有效性和灵敏度。
3.3.3设备应由专人操作,在生产过程中应时刻注意观看压力的读数,并
做好相应的调整,如显现压力专门或推不动等紧急情形应赶忙停机检查。
3.3.4压力机启动后,不准将头手等躯体部位压力机工作台面内。
3.4热处理
3.4.1钢制无缝三通挤压成型后应进行热处理,目的是排除冷挤过程中产
生的应力。
3.4.2加热到600℃~650℃,恒温一定时刻〔恒温时刻为每25mm壁厚1h,
且不得少于15min〕,随炉冷却至400℃以下后出炉自然冷却。
3.5坡口
3.5.1坡口设备采纳一般车床。
3.5.2坡口产生的毛刺应修磨洁净。
3.5.3坡口角度37.5±2.5°。
3.6除锈
3.6.1刷漆前应对三通表面进行除锈处理,目的是去除浮锈,增加油漆附
着力。
3.6.2在条件承诺的情形下,尽可能采纳抛丸除锈机对其进行抛丸除锈。
3.6.3除锈成效以去掉浮锈,见到金属本色为宜。
3.7刷漆
3.7.1依照用户要求决定成型后的三通成品是否需要刷漆,如需刷漆那么
采纳黑色或红色防锈漆。
3.7.2刷漆应平均,无漏点和流坠。
3.8标识
3.8.1成品三通应进行耐久性标识,字迹清晰。
3.8.2标识方法假设需方有规定,那么按需方规定执行;假设需方无规定,
那么依照产品性能按标准执行。
3.9检验入库
3.9.1三通入库前应由质检员对几何尺寸和外观进行检验。
3.9.2三通内外表面不得有划伤沟槽或碰撞形成的明显凹陷,没有裂纹、
结疤、折叠、分层等缺陷。
3.9.3几何形状检验按照GB/T 12459-2005标准执行。
3.9.4检验应填写«三通检验记录表»〔YGBG-06〕。
3.9.5三通检验合格后方可入库,应按规格型号整齐摆放于指定库存区
域,并保证其不受污损、碰撞。
YGYG-07 钢制管帽制造工艺
1.总那么
为确保钢制管帽的产品质量,规范制造工艺,严格程序治理,特制定
该工艺。本工艺适用于我公司生产的管帽工制造过程。
2.依据标准
GB/T 12459-2005«钢制对焊无缝管件»
GB/T 13401-2005«钢板制对焊管件»
GB/T 710-1991«优质碳素结构钢热轧薄钢板和钢带»
GB/T 711-1991«优质碳素结构钢热轧厚钢板和宽钢带»
GB/T 912-1989«碳素结构钢和低合金结构钢热轧冷钢板及钢带»
GB/T 3274-1988«碳素结构钢和低合金结构钢热轧厚钢板和钢带»
GB/T 3280-1992«不锈钢冷轧钢板»
GB/T 4237-1992«不锈钢热轧钢板»
3.制造工艺
钢制管帽的加工工艺流程如下:
原材料入厂检验 → 下料 → 毛坯加热 → 冲压 → 坡口 → 除锈
→ 刷漆 → 标识 → 检验入库
3.1原材料入厂检验
3.1.1制造管帽用钢板必须符合相应钢板制造标准的规定。并应有制造公
司质量证明书,钢板入厂应由质检员和保管员对钢板厚度、外观质量等进
行检查验收。
3.1.2钢板实物的标记、炉批号与材质证明书相符合时,可不进行复检。
同时也能够按照需方的要求对化学成份分析,力学性能分析、金相组织分
析进行复检。
3.1.3钢板的内外表面不得有气泡、结疤、拉裂、裂纹、折叠、夹杂和压
入的氧化铁皮,不得有分层。
3.1.4钢板应整齐排列于料场或车间厂房内,不得乱摆乱放,不得有重物
挤压、碰砸,吊装时不得有碰撞现象发生。
3.2下料
3.2.1采纳氧乙炔炬割或等离子切割器进行下料。
3.2.2下料尺寸应符合技术要求。
3.2.3下料前应依照钢板尺寸和毛坯尺寸进行合理的排版,以降低材料消
耗。
3.2.4下料时注意做好钢板的标识移植。
3.3毛坯加热
3.3.1毛坯装炉前必须把料上的杂物清扫洁净。
3.3.2毛坯入炉后要堆放整齐,最底下一块及毛坯之间要加50~100mm支
垫,不得重叠,以防止过热或烧不透。
3.3.3严格按材质操纵加热温度,加热温度要平均。炉内温度通过热电偶
来测试,温度达不到要求不能冲压。
3.3.4毛坯加热温度可参照下表:
各种钢材毛坯加热温度表
毛坯材质 Q235、20、16Mn 1Cr18Ni9Ti
加热温度 950~1000℃ 1000~1100℃
加热时刻 1min/mm 1.5min/mm
3.4冲压
3.4.1动力设备采纳315或500吨压力机,冲压前应检查设备,确认其处
于良好运转状态,选择相应型号的整套模具定位在压力机上,并用足够强
度的螺栓将上下模具分别与压力机紧固,模具应不止在压力机跨中位置,
防止偏心,上胎与下胎间隙要平均。
3.4.2为便于脱模,应在上下模具上涂刷润滑剂。润滑剂成分应符合以下
要求:
3.4.2.1碳钢润滑剂:40%石墨粉+60%机油调成糊状。
3.4.2.2不锈钢润滑剂:55%石墨粉+45%机油调成糊状。
3.4.3将加热好的管帽毛坯用专用夹具从加热炉中取出后,必须迅速将其
定好中心放在下模上,防止压偏。
3.4.4上模压到底部后,宜停留1min左右再升起。
3.4.5热压管帽终压温度应大于700℃,有专门要求的按专门工艺执行。
3.4.6应随时清除模具内的氧化物等,以防止划伤管帽或产生压坑。
3.5坡口
3.6.1小口径的管帽采纳车床进行坡口加工,大口径的利用转胎火焰切割
设备进行坡口。
3.6.2坡口角度37.5±2.5°。
3.7除锈
3.7.1刷漆前应对管帽表面进行除锈处理,目的是去除浮锈,增加油漆附
着力。
3.7.2除锈成效以去掉浮锈,见到金属本色为宜。
3.8刷漆
3.8.1管帽刷漆采纳黑色或红色防锈漆。
3.8.2刷漆应平均,无漏点和流坠。
3.9标识
3.8.1成品管帽应进行耐久性标识,字迹清晰。
3.8.2标识方法假设需方有规定,那么按需方规定执行;假设需方无规定,
那么依照产品性能按标准执行。
3.9检验入库
3.9.1管帽入库前应由质检员对几何尺寸和外观进行检验。
3.9.2管帽内外表面不得有划伤沟槽或碰撞形成的明显凹陷,没有裂纹、
结疤、折叠、分层等缺陷。
3.9.3几何形状检验按照GB/T 12459-2005标准执行。
3.9.4检验应填写«管帽〔封头〕检验记录表»〔YGBG-07〕。
3.9.5管帽检验合格后方可入库,应按规格型号整齐摆放于指定库存区
域,并保证其不受污损、碰撞。
YGYG-08 钢制有缝管件制造工艺
1.总那么
为确保钢制有缝管件的产品质量,规范制造工艺,严格程序治理,特
制定该工艺。本工艺适用于钢板制对焊管件的加工制造过程。
2.依据标准
GB/T 13401-2005«钢板制对焊管件»
GB/T 710-1991«优质碳素结构钢热轧薄钢板和钢带»
GB/T 711-1991«优质碳素结构钢热轧厚钢板和宽钢带»
GB/T 912-1989«碳素结构钢和低合金结构钢热轧冷钢板及钢带»
GB/T 3274-1988«碳素结构钢和低合金结构钢热轧厚钢板和钢带»
GB/T 3280-1992«不锈钢冷轧钢板»
GB/T 4237-1992«不锈钢热轧钢板»
GB/T 8163-1999«输送流体用无缝钢管»
3.制造工艺
钢板制对焊管件的加工工艺流程如下:
原材料入厂检验 → 下料 → 毛坯加热 → 压制 → 焊接 → 无损
检测 → 坡口 → 除锈刷漆 → 标识 → 检验入库
3.1原材料入厂检验
3.1.1制造钢板制对焊管件用钢板必须符合相应钢板制造标准的规定。并
应有制造公司质量证明书,钢板入厂应由质检员和保管员对钢板厚度、外
观质量等进行检查验收。
3.1.2钢板实物的标记、炉批号与材质证明书相符合时,可不进行复检。
同时也能够按照需方的要求对化学成份分析,力学性能分析、金相组织分
析进行复检。
3.1.3钢板的内外表面不得有气泡、结疤、拉裂、裂纹、折叠、夹杂和压
入的氧化铁皮,不得有分层。
3.1.4厚度≥25mm的15CrMoR钢板应逐张进行超声波检验,合格后方可使
用。
3.2下料
3.2.1采纳手工炬割或火焰自动切割器进行下料。
3.2.2下料尺寸应符合技术要求。
3.2.3下料前应依照钢板尺寸和毛坯尺寸进行合理的排版,以降低材料消
耗。
3.2.4下料时注意做好钢板的标识移植。
3.3毛坯加热
3.3.1毛坯装炉前必须把料上的杂物清扫洁净。
3.3.2毛坯入炉后要堆放整齐,最底下一块及毛坯之间要加50~100mm支
垫,不得重叠,以防止过热或烧不透。
3.3.3严格按材质操纵加热温度,加热温度要平均。炉内温度通过热电偶
来测试,温度达不到要求不能冲压。
3.3.4毛坯加热温度可参照下表:
各种钢材毛坯加热温度表
毛坯材质 Q235、20、16Mn 1Cr18Ni9Ti
加热温度 950~1000℃ 1000~1100℃
加热时刻 1min/mm 1.5min/mm
3.4压制
3.4.1动力设备采纳315或500吨压力机,压制前应检查设备,确认其处
于良好运转状态,选择相应型号的整套模具定位在压力机上,并用足够强
度的螺栓将上下模具分别与压力机紧固,模具应不止在压力机跨中位置,
防止偏心,上胎与下胎间隙要平均。
3.4.2为便于脱模,应在上下模具上涂刷润滑剂。润滑剂成分应符合以下
要求:
3.4.2.1碳钢润滑剂:40%石墨粉+60%机油调成糊状。
3.4.2.2不锈钢润滑剂:55%石墨粉+45%机油调成糊状。
3.4.3将加热好的毛坯用专用夹具从加热炉中取出后,必须迅速将其定好
中心放在下模上,防止压偏。
3.4.4上模压到底部后,宜停留1min左右再升起。
3.4.5热压钢板制对焊管件的终压温度应大于700℃,有专门要求的按专
门工艺执行。
3.4.6应随时清除模具内的氧化物等,以防止产生划伤或压坑。
3.5焊接
3.5.1钢板制对焊管件的焊接执行«焊接操纵程序»和«焊接通用工艺»,关
于专门要求的按技术交底和相应焊接作业指导书进行焊接。
3.5.2焊接应符合以下要求:
3.5.2.1应符合GB150、JB4708、JB4709的有关要求。
3.5.2.2管件此题的焊缝应为对洁焊缝。焊缝的对接坡口尺寸应符合
GB/T985或GB/T986标准的要求。
3.5.2.3焊接坡口的加工宜采纳机械方法。如用热切割法,必须去除坡口
表面的氧化皮,并将阻碍焊接质量的凸凹不平除打磨平坦。
3.5.2.4焊缝的对口错边量b≤10%s,且不得大于2mm。
3.6无损检测
3.6.1对以下产品应逐件进行磁粉或渗透检测:〔1〕碳钢、不锈钢材料的
三通、四通;〔2〕合金钢材料的各类管件。
3.6.2检验按JB/T4730系列标准的规定,Ⅱ级为合格。管件不得有微裂
纹。
3.6.3除用户另有要求外,管件的焊缝全长应进行100%射线检测;或100%
超声检测,并以射线检测复验,复验数量不应少于20%。射线和超声检测
按JB/T4730标准的规定,检测结果射线为Ⅱ级合格,超声为Ⅰ级合格。
3.7坡口
3.7.1利用相应的专用坡口设备进行坡口加工。
3.7.2坡口角度37.5±2.5°,钝边1.5±1.0mm。
3.8除锈刷漆
3.8.1刷漆前应对管件表面进行除锈处理,目的是去除浮锈,增加油漆附
着力。
3.8.2除锈成效以去掉浮锈,见到金属本色为宜。
3.8.3管件刷漆采纳黑色或红色防锈漆。
3.8.4刷漆应平均,无漏点和流坠。
3.9标识
3.9.1成品管帽应进行耐久性标识,字迹清晰。
3.9.2标识方法假设需方有规定,那么按需方规定执行;假设需方无规定,
那么依照产品性能按标准执行。
3.9检验入库
3.9.1入库前应由质检员对钢板制对焊管件几何尺寸和外观进行检验。
3.9.2内外表面不得有划伤沟槽或碰撞形成的明显凹陷,没有裂纹、结疤、
折叠、分层等缺陷。
3.9.3几何形状检验按照GB/T 13401-2005标准执行。
3.9.4检验结果应依照不同产品填写相应的记录表格。
3.9.5检验合格后方可入库,应按规格型号整齐摆放于指定库存区域,并
保证其不受污损、碰撞。
YGYG-09 螺旋炉管制造工艺
1.总那么
为确保螺旋炉管的产品质量,规范制造工艺,严格程序治理,特制
订该工艺。本工艺适用于我公司生产的管式加热炉螺旋炉管φ219mm以下
产品的制造过程。
2.标准依据
Q/SL0915-1999«螺旋炉管»
GB 5310-1995«高压锅炉用无缝钢管»
GB 3087-1999«低中压锅炉用无缝钢管»
GB 9948-1988«石油裂化用无缝钢管»
3.制造工艺
管式加热炉螺旋炉管制造工艺流程如下:
原材料入厂检验 → 钢管焊接 → 焊缝检验 → 热煨成型 → 整体
预制→ 无损探伤 → 水压试验 → 成品检验
3.1原材料入厂检验
3.1.1管式加热炉螺旋炉管用钢管必须符合相应钢管制造标准的规定。并
应有制造公司质量证明书,钢管入厂应由质检员和保管员对钢管口径、壁
厚、外观质量等进行检查验收。
3.1.2管材实物的标记、炉批号与材质证明书相符合时,可不进行复检。
同时也能够按照需方的要求对化学成份分析、力学性能分析,金相组织分
析进行复检。
3.1.3钢管表面应光滑,不得有结疤、凹凸、不平、裂纹、重皮等缺陷,
不得有过烧现象存在。
3.1.4钢管应整齐排列于车间厂房内,不得乱摆乱放,不得有重物挤压碰
砸,吊装时不得有碰撞现象发生。
3.2钢管焊接
3.2.1钢管焊接前应尽量采纳机械方法进行坡口,并应把距管端50mm内
的浮锈、油污等清理洁净。如采纳火焰切割,那么应将产生的氧化皮清晰
洁净,并用磨光机修磨切割缺口和坡口表面。
3.2.2钢管焊接前应做焊接工艺评定,对已有的工艺评定可直截了当引
用。
3.2.3依照对应的焊接工艺评定编写焊接作业指导书。
3.2.4焊接作业应由考试合格的电焊工担任。
3.2.5焊接过程应执行«焊接操纵程序»、«手工电弧焊通用工艺»和«氩弧
焊通用工艺»的有关规定。
3.3焊缝检验
3.3.1焊缝应与母材圆滑过渡,焊缝宽度从每边超过坡口2mm为宜,焊缝
余高不得大于1.5mm。
3.3.2焊缝及热阻碍区不得有裂纹、气孔、夹渣、凹陷、焊瘤、未熔合等
缺陷。
3.3.3焊缝咬边深度不得大于0.5mm,连续长度不得超过25mm,但总长度
不得超过焊缝周长的10%。
3.3.4焊缝应按设计要求进行无损探伤。
3.4热煨成型
3.4.1煨制设备为链条式推制机。
3.4.2先煨制一件曲率半径与螺旋炉管节圆半径相等的弯管。
3.4.3依照运算确定定位轮、起弧轮和导程轮的位置,并将其在立板上焊
接牢固。
3.4.4将焊接的钢管装夹在螺旋炉管推制作业线上,前端焊接预先煨制的
等半径弯管作为引弧管。
3.4.5启动中频,由中频加热圈进行加热煨制。中频感应圈采纳紫铜方管
制作,感应圈的内径大于钢管外径40~60mm为宜,感应圈喷水角度为垂
直线至钢管前进方向侧45°左右,喷水孔采纳Φ1mm或Φ1.2mm钻头打孔,
喷水孔均布于感应圈内侧一边,依照感应圈大小调剂孔的间距,感应圈越
大,孔间距越大。
3.4.6循环冷却用水应采纳洁净自来水。
3.4.7在煨制起始圈时应按照螺旋炉管的节圆直径、螺距〔t≥0〕、螺旋
升角等技术参数进行起弧轮和导程轮的认真调整。等煨制成型第一圈后便
不需连续调整。
3.4.8煨制成型的每圈螺旋炉管由传动支架支持,有螺距间隙的焊接圈间
支撑,直到完成全部螺旋炉管的煨制。
3.5整体预制
3.5.1煨制完成的螺旋炉管应在下线后按图纸要求进行整体预制。
3.5.2精确调整节圆直径、螺距。
3.5.3对多头螺旋炉管进行旋装。
3.5.4焊接进出口工艺接管。
3.6无损探伤
3.6.1对先期检验剩余的焊缝进行无损探伤。
3.6.2探伤方式和评定等级按设计要求进行。
3.7水压试验
3.7.1整体预制完成的螺旋炉管应按图纸要求进行水压试验。
3.7.2水压试验时,环境温度应高于5℃,试验用水应为洁净水,试验压
力应为工作压力的1.5倍。
3.7.3试压时,压力缓慢升降,当水压上升到设计压力时,应暂停升压,
检查有无渗漏或专门现象。当无渗漏和专门现象时,再升压到试验压力,
并保持10~30min,然后降到设计压力保压30min以上,进行检查,无渗
漏现象为合格。
3.7.4水压试验完成后,应将螺旋炉管内的水排净。
3.7.5填写«螺旋炉管压力试验检查记录表»〔YGBG-09〕。
3.8成品检验
3.8.1检查螺旋炉管外观质量,应无裂纹、过烧、疤痕等缺陷,如在生产
中发觉上述问题,应停止生产进行处理整改。
3.8.2几何尺寸及偏差如设计有要求应按设计要求进行检验,否那么按标
准进行检查验收。
3.8.3填写«螺旋炉管结构尺寸检验记录表»〔YGBG-05〕。
YGYG-10 热煨弯管防腐通用工艺
1.总那么
为确保热煨弯管的防腐质量,规范制造工艺,严格程序治理,特制
订该工艺。本工艺适用于我公司生产的油气输送用φ457mm以下规格热煨
弯管熔结环氧粉末喷涂和胶带冷缠防腐过程。
2.标准依据
SY/T 5257—2004 «油气输送用钢制弯管»
SY/T 0407—1997 «涂装前钢材表面预处理规范»
GB/T 8923—1988 «涂装前钢材表面锈蚀等级和除锈等级»
SY/T 0315—1997 «钢质管道熔结环氧粉末外涂层技术标准»
SY/T 0414—1998 «钢质管道聚乙烯胶粘带防腐层技术标准»
3.制造工艺
热煨弯管防腐工艺流程如下:
弯管抛丸除锈→除锈后检测→中频加热→粉末喷涂→固化→水冷却
→涂层检测→冷缠胶带→冷缠检测→成品标识→成品装运
3.1弯管抛丸除锈
3.1.1经检验合格后的弯管进行抛丸除锈处理,利用通过式弯管抛丸除锈
设备进行防腐前的表面预处理。
3.1.2抛丸除锈前应采纳适当方法将弯管外表面的油、油脂清除洁净。如
弯管表面潮湿,应预热弯管驱除潮气,预热温度为40~60℃。
3.1.3弯管抛丸除锈应达到GB/T 8923—1988中规定的Sa2/级,表面的
1
2
锚纹深度应在40~100μm范畴内,并符合环氧粉末生产厂的举荐要求。
3.1.4抛丸除锈后,应对每个弯管进行目测检查。对可能导致涂层漏点的
表面缺陷,应打磨掉,且打磨后的壁厚不应小于规定值。有疵点的弯管应
剔除或予以修整。
3.1.5抛丸除锈完的弯管应在8小时内进行粉末喷涂,当显现返锈或表面
污染时,必须重新进行抛丸除锈。
3.2除锈后检测
3.2.1抛丸除锈后的弯管要进行全面的检测,检测合格后的弯管方能进入
下一道工序。
3.2.2检测的要紧项目包括几何尺寸〔弯管的角度偏差、曲率半径偏差、
壁厚减薄率、圆度、平面度等〕和表面质量〔除锈等级、锚纹深度,是否
有夹层、较深的点蚀、划伤、气孔、砂眼等〕。
3.2.3对不合格的弯管拿出整改措施并进行修复,无法修整的弯管要予以
剔除。
3.3中频加热
3.3.1将抛丸除锈后经检验合格的弯管卡装到有动力驱动的专用摇臂上,
依照直管段的长短调整摇臂的偏心。
3.3.2在管端缠绕宽度为100mm的牛皮纸带,并保证粘贴牢固。
3.3.3用压缩空气吹扫弯管表面上的浮尘,注意一定不能用粘有油污的手
套接触管壁,更不能用棉纱擦拭,防止因炭纤维粘附造成防腐后气孔等缺
陷的显现。
3.3.4上水并启动中频,利用中频加热圈对弯管进行粉末喷涂前的加热,
加热功率一样固定在60KW左右,摇臂驱动电机转速操纵在200r/min,来
回平均行进两遍。
3.3.5加热过程中应保证温度的平均,防止局部温度过低或过高,用远红
外测温仪随时检测弯管表面温度,并及时调整中频加热的功率和摇臂行进
的速度。
3.3.6由于中频加热的固有特性,热量一样是从弯管的内壁向外返,因此
加热时要预留一定的温度余量。同时由于光管的发射率与涂层的发射率不
同,用本测温仪测得的温度有一个固定的温差,当测得表面温度达到
130~150℃时,即可停止中频加热进行喷涂。
3.4粉末喷涂
3.4.1喷涂前10分钟接通流化筒气源,使环氧粉末得到充分流化。
3.4.2检查气源及喷粉管线是否连接可靠,是否有松动现象,发觉问题及
时调整。
3.4.3每次喷粉前都要清理喷枪上吸附的粉末,防止喷粉过程中粉末突然
脱落造成的粉末堆积。
3.4.4弯管加热到合适温度后,开始粉末喷涂。
3.4.5调剂喷粉室气源压力〔一样固定在0.3Mpa〕和摇臂电机转速〔一样
在400r/min左右〕,以得到最正确的喷粉成效和涂层厚度。
3.4.6弯管外表面的涂敷温度必须符合环氧粉末涂料所要求的温度范畴,
但实际温度最高不得超过275℃。
3.4.7在喷涂过程中假如显现漏点和局部涂层过薄,应及时进行补喷。
3.4.8为了防止涂层分层现象,幸免在涂层固化后的二次喷涂,涂敷过程
中尽量采纳一次成形。
3.5固化
3.5.1由于环氧粉末的本身特性,在230℃~250℃范畴内,其固化时刻≤
1.5min,因此能够采纳自然固化方式。
3.5.2在粉末喷涂后到固化前这段时刻,不承诺有外物接触或碰撞弯管外
表面。
3.6水冷却
3.6.1为了加快生产的速度,在弯管防腐后利用水冷的方式对弯管进行降
温。
3.6.2水冷却应在涂层充分固化后进行,利用洁净的自来水对涂层表面进
行平均喷洒冷却。
3.6.3为了保持现场的干燥和洁净,冷却时要使用水槽等做好冷却水的接
收。
3.7涂层检测
3.7.1在水冷却后,进行涂层的检查验收,第一检查涂层的表面质量,外
观要求平坦,色泽平均,无气泡、开裂及缩孔,承诺有轻度桔皮状花纹。
3.7.2使用涂层测厚仪,沿每根弯管长度随机抽取三个位置,测量每个位
置圆周方向平均分布的任意四点的防腐层厚度。
3.7.3使用电火花检漏仪进行漏点检测,检漏电压5V/μm。
3.7.4填写防腐绝缘层电火花检测记录〔YGBG-13〕
3.8冷缠胶带
3.8.1冷缠胶带原材料采纳聚乙烯或聚丙烯冷缠胶带。
3.8.2冷缠作业应该在环氧粉末涂层充分固化,涂层表面冷却至40℃以下
后进行。
3.8.3胶带始端与末端搭接长度应不小于1/4管子周长,且许多于100mm。
3.8.4缠绕时管端应留150±10mm的焊接预留段,如设计有要求那么按设
计要求执行。
3.8.5胶带间搭接宽度按设计要求或标准执行。
3.9冷缠检测
3.9.1冷缠后的弯管应进行电火花检测。
3.9.2检测方式和电压依据SY/T 0414—1998«钢质管道聚乙烯胶粘带防腐
层技术标准»进行。
3.10成品标识
3.10.1对冷缠胶带完工后的弯管进行标识移植,应采纳白色油漆将标识
内容清晰标在冷缠胶带上。
3.10.2 标识的内容和方式如没有专门规定,按如下方式进行标识:
管号—材质 79548—L360
弯管口径×壁厚—弯曲半径—角度 Φ355.6×8.7—5D—90°
弯管编号 生产厂家 0620—2021 S L G J
3.11成品装运
3.11.1经检验合格的防腐弯管,用草绳进行周向缠绕,缠绕的圈数及草
绳的粗细,以堆放时被爱护涂层不受损坏为原那么。
3.11.2成品弯管应轻吊轻放,防止撞击变形和机械损害,吊索使用尼龙
吊带。
3.11.3在装运过程中假如弯管被损坏,应按照相关要求进行处理。
YGYG-11 手工电弧焊通用工艺
1.总那么
为了提高压力管道元件手工电弧焊焊接质量,特制定本工艺。当本工
艺与产品的专用工艺文件有矛盾时,以专用工艺文件的要求为准。
2.依据标准
JB/T 4709-2000 «钢制压力容器焊接规程»
JB/T 4730-2005 «承压设备无损检测»
3.技术内容
3.1流程图
对焊工的要求 焊条的选用 焊前预备
焊接规范的选择
焊接质量检查
3.2一样规定
3.2.1对焊工的要求
参加压力管道元件焊接工作的焊工,必须有相应类别的锅炉压力容器
焊工合格证书。
3.2.2施焊前,电焊工必须熟悉设计图样和焊接工艺要求。
3.2.3在以下情形下焊工有权拒绝施焊:
3.2.3.1施焊的母材、焊材不符合图样和焊接工艺。
3.2.3.2坡口尺寸和质量不符合要求。
3.2.3.3有预热要求的焊件,焊前预热不符合工艺要求。
3.2.4焊接环境应符合以下要求,施焊场所风速不得大于10m/s;相对湿
度不大于90%;气温不得低于-5℃,否那么应采取相应的防护措施。
3.2.5焊条选用
依照产品的使用条件和母材的化学成分、力学性能、焊接性能选用焊
条,焊条应有质量证明书,其质量应符合GB5117,GB5118的要求。
3.2.6焊前预备
3.2.6.1检查劳保穿戴是否齐全。工具设备是否齐全完好。
3.2.6.2检查焊机个部分是否完好,外壳是否正常接地。
3.2.6.3检查坡口质量是否符合要求。
3.2.6.4用焊条保温筒领取已烘干好的焊条。
3.2.6.5按焊接规范要求,在试件上调试好焊接规范。
3.2.7焊接规范的选择
3.2.7.1一样情形下,酸性焊条采纳正接,碱性焊条采纳支流反接。
3.2.7.2定位焊和打底焊的焊条直径不大于Φ3.2mm。填充焊和盖面焊的
焊条直径依照焊件厚度选用。
焊条直径的选择
焊件厚度〔mm〕 <4 4~12 >12
焊条直径〔mm〕 不大于厚度 φ3~4 不小于φ4
3.3焊接电流要依照焊条直径、焊条类型、焊条位置、焊件厚度等因素进
行选定。
结构钢焊条电流参考表
焊条直径〔mm〕 φ2.0 φ2.5 φ3.2 φ4 φ5 φ6
焊接电流〔A〕 40~70 60~90 90~130 140~210 170~270 220~310
铬镍不锈钢焊条电流参考表
焊条直径〔mm〕 φ2.0 φ2.5 φ3.2 φ4 φ5
焊接电流〔A〕 25~50 50~80 80~110 110~160 160~200
3.4焊接接头层数设计,一样按焊条直径为焊肉厚度进行运算,再按焊接
工艺评定和施焊体会进行调整。
3.5焊接质量检验
3.5.1焊接外观质量检验
3.5.1.1焊缝应圆滑过渡,不得有咬边、熔渣和飞溅物。
3.5.1.2焊缝的对口错边量应小于壁厚的10%,且不得大于2mm。
3.5.1.3填写«焊接焊缝检验记录表»〔YGBG-08〕。
3.5.2焊缝的内部质量检查按JB/T 4730-2005«承压设备无损检测»的要求
进行。
YGYG-12 氩弧焊通用工艺
1.总那么
1.1为了提高氩弧焊焊接质量,使氩弧焊焊接方法有效地发挥其特有的优
势,特制定本工艺。
1.2本工艺适用于氩弧焊焊接碳钢、合金钢和不锈钢。
1.3氩弧焊焊接除应执行本工艺的规定外,尚应执行产品专用工艺文件的
规定。
1.4氩弧焊焊工必须持有有关部门方法的焊工合格证,方可从事焊接工
作。
1.5焊工应按照图样或工艺文件的要求,检查组对质量及坡口型式和尺
寸,不符合要求的有权拒绝施焊。
1.6焊接应再室内进行,保证环境温度不低于5℃,假如低于5℃时,应
进行预热。
2.技术内容
2.1工艺流程图
坡口清理
焊材选择
焊缝质量检验
电流种类的选择
焊 接
2.2坡口清理
2.2.1焊接前应将坡口及其两侧20mm范畴内的毛刺、氧化皮、铁锈、油
污等清理洁净。
2.3焊材的选择
2.3.1氩气纯度必须保证大于99.9%。
2.3.2焊丝可依照焊件的材质和厚度不同来选择牌号及规格。
2.3.3采纳的钨棒必须有出厂合格证,钍钨棒的粉尘有轻微的放射性,在
磨削时应采取必要的防护措施。
2.3.4钨棒的直径可依照电流的大小和种类进行选择,具体见下表:
钨极直径选择表
钨极直径〔mm〕
承诺电流
〔A〕
电流种类
1~2 3 4 5 6
20~100 100~160 150~230 230~300 260~360 交流
10~40 30~50 40~70 60~100 100~150 直流〔反接〕
40~150 140~200 200~300 300~400 400~550 直流〔正接〕
2.4依照焊件的材质选择合适的电流种类,具体按下表执行:
电流种类选用表
材质 直流正接 直流反接 交流
碳钢 好 可用
合金钢 好 可用
不锈钢 好 可用
2.5焊接
2.5.1焊接时,依照产品的要求和工艺需要,可采纳焊缝背面衬以有槽或
无槽的可拆垫板,或者焊缝背面通氩气爱护。
2.5.2依照材料的特和工艺要求,要进行预热焊接时,应采纳中性火焰进
行焊前预热,并及时将坡口内氧化膜清晰洁净,以幸免阻碍焊接质量。
2.5.3钨极氩弧焊时,不同直径钨极的使用电流范畴应按照下表确定:
不同直径钍钨极或铈钨极的使用电流范畴
钨极直径〔mm〕
1.0 15~80 - 20~60
1.6 70~150 60~120
2.0 100~200 85~160
2.5 150~250 100~180
3.2 250~400 160~250
4.0 400~500 200~320
5.0 500~750 290~390
6.0 750~1000 340~525
直流正接 直流反接 交流
使用电流范畴〔A〕
2.5.4假如钨极与工件直截了当短路引弧,钨极容易燃烧,熄弧时应填满
弧坑。引弧时应提早送气5~10s,熄弧时应连续送气3~5s,等至钨极及
焊缝冷却后,再抬起焊枪,以免钨极及焊缝表面氧化。
2.6焊缝质量检验
2.6.1焊缝的质量应符合标准及图样的有关规定。
YGYG-13 热处理通用工艺
1.总那么
为了提高冷热加工的压力管道元件产品质量,排除加工应力,改善内
部组织,提高元件整体性能,特制定本工艺。本工艺适用于冷热加工管件
的热处理。
2.依据标准
GB 50235-97 «工业金属管道工程施工及验收规范»
GB/T 5257-2004 «油气输送用钢制弯管»
GB/T 12459-2005 «钢制对焊无缝管件»
GB/T 13401-2005 «钢板制对焊管件»
3.弯管的热处理
3.1除制作弯管温度自始至终保持在900℃以上的情形外、壁厚大于19mm
的碳素钢管制作弯管后,应按«常用管材热处理条件表»的规定进行热处
理。
3.2当«常用管材热处理条件表»所列的中、低合金钢管进行热弯时,对公
称直径大于或等于100mm,或壁厚大于或等于13mm的,应按设计文件的
要求进行完全退火、正火加回火或回火处理。
3.3当«常用管材热处理条件表»所列的中、低合金钢管进行冷弯时,对公
称直径大于或等于100mm、或壁厚大于或等于13mm的,应按«常用管材热
处理条件表»的要求进行热处理。
3.4奥氏体不锈钢管制作的弯管.可不进行热处理;当设计文件要求热处
理时,应按设计文件规定进行。
3.5油气输送用钢制弯管中,对L415或X60及以上钢级和处于酸性环境
的弯管应进行热处理,其他钢级或钢号的弯管由制造商与购方商定弯管再
弯制后是否需要进行热处理。
常用管材热处理条件表
管材类别 名义成份 管材牌号 加热速率 恒温时刻 冷却速率
碳素钢 C 10、15、20、25 600~650 当加热温恒温时刻恒温后的
C-Mn 16Mn、16MnR 600~650
C-Mn-V
中
、
低
合
金
钢
C-Cr-Mo 12Cr2Mo 700~760
C-Mo 16Mo 600~650
09MnV 600~700
15MnV 600~700
12CrMo 600~650
15CrMo 700~750
5Cr1Mo 700~760
9Cr1Mo 700~760
C-Cr-Mo-V 12Cr1MoV 700~760
C-Ni
2.25Ni 600~650
3.5Ni 600~630
热处理
温度〔℃〕
400℃时,25mm 壁不应超过
加热速率260×25/T厚1h,且不
不应大于得少于15 ℃/h,且不
205×25/T 得大于 min在恒温
˚℃/h
冷却速率度升至 应为每
260℃/h,期间内最
400℃以下高与最低
可自然冷温差应低
却 于65℃
4.管件的热处理
4.1采纳冷加工成形的管件,成形后应进行排除应力的热处理。
4.2采纳热加工成形的管件,对铬钼钢和不锈钢材料,应进行热处理;对
碳素钢材料,其最终成形温度低于750℃时,应进行热处理。
4.3无缝管件热处理方式见GB/T 12459-2005«钢制对焊无缝管件»表17
材料热处理,有缝管件热处理方式见GB/T 13401-2005«钢板制对焊管件»
表13管件热处理。
4.4无缝管件的硬度值见GB/T 12459-2005«钢制对焊无缝管件»表18管件
硬度,有缝管件硬度值见GB/T 13401-2005«钢板制对焊管件»表14管件
硬度。
4.4奥氏体不锈钢管件热处理后应进行酸洗钝化处理。
5.一样要求
5.1热处理操作人员在热处理之前应熟悉热处理工艺要求,严格按热处理
工艺文件和«热处理作业指导书»〔TYBG-13〕的规定操作和记录。
5.2送电前操作人员应认真检查电源是否正确连接,漏电爱护器是否灵
敏,有无裸露的电源线及接头,热处理设备接地是否良好等。
5.3热处理过程中操作人员应注意观看温度指示外表有无专门,如发觉温
度专门时应停止升温,分析缘故,找出问题并处理完毕后才能连续升温。
5.4对不锈钢管件进行固溶处理,处理温度为1050℃左右,出炉后急冷,
冷却介质为水。
5.5热处理后进行硬度检查〔或铁素体含量检测〕超过规定要求的应应重
新进行热处理,但重复处理次数不得超过三次。
5.6热处理应采纳自动温度记录仪记录温度曲线。
YGYG-14 压力试验通用工艺
1.总那么
1.1本工艺规定了压力试验作业的差不多要求。
1.2本工艺适用于本企业制造范畴内的压力管道元件的压力试验。
2.依据标准
GB 50235-97 «工业金属管道工程施工及验收规范»
GB/T 5257-2004 «油气输送用钢制弯管»
GB/T 12459-2005 «钢制对焊无缝管件»
GB/T 13401-2005 «钢板制对焊管件»
3.差不多要求
3.1压力试验分为液压试验和气压试验。
3.2压力试验应以液体为试验介质。当压力管道元件的设计压力小于或等
于0.6MPa时,也可采纳气体为试验介质,但应采取有效的安全措施。脆
性材料严禁使用气体进行压力试验。
3.3气体试验介质宜采纳空气、氮气或其他惰性气体。
3.4当现场条件不承诺使用液体或气体进行压力试验时,经建设单位同
意,可同时采纳以下方法代替:
〔1〕所有焊缝,用液体渗透法或磁粉法进行检验。
〔2〕对接焊缝用100%射线照相进行检验。
3.5当进行压力试验时,应划定禁区,无关人员不得进入。
3.6试验用压力表差不多校验,并在周检期内,其精度不得低于1.5级,
表的满刻度值应为被测最大压力的1.5~2倍,压力表不得少于两块。
3.7液压试验应使用洁净水,当对奥氏体不锈钢压力管道元件进行试验
时,水中氯离子含量不得超过25×10(25ppm)。当采纳可燃液体介质进
-6
行试验时,其闪点不得低于50℃。
3.8试验前,注液体时应排尽空气。
3.9试验时,环境温度不宜低于5℃,当环境温度低于5℃时,应采取防
冻措施。
3.10液压试验应缓慢升压,待达到试验压力后,稳压10min,再将试验压
力降至设计压力,停压30min,以压力不降、无渗漏为合格。
3.11当试验过程中发觉泄漏时,不得带压处理。排除缺陷后,应重新进行
试验。
4.设计验证或静水压力试验
4.1对正式生产的压力管道元件,不要求做设计验证和静水压力实验。
4.2设计验证试验的要求是做爆破强度试验。
4.3做设计验证试验的元件破裂前的压力应不小于运算验证试验压力或
元件承担住了运算验证试验压力的105%,稳压试验许多于10s而未显现
破裂,那么试验合格,即满足验证试验要求:
P=2ST/D
式中:
P——元件最小运算验证试验压力,单位为兆帕〔MPa〕;
S——试验元件的实际抗拉强度〔在代表试验元件的试件上测得〕,它
应满足材料标准中规定的抗拉强度要求,单位为兆帕〔MPa〕;
T——元件上标志的公称壁厚,单位为毫米〔mm〕;
D——规定的元件外径,单位为毫米〔mm〕。
4.4静水压力试验的压力应为元件设计压力的150%,稳压时刻许多于10s。
附件1
热推成型钢制弯头下料尺寸
〔单位mm〕
序号 弯头规格 管材规格 下料长度 备注
A
1 Φ48×4 Φ38×4 134
2 Φ57×4 Φ42×4 180
3 Φ60×4 Φ42×4 190
4 Φ60×8 Φ48×8 168
5 Φ76×6 Φ60×6 218
6 Φ76×8 Φ60×8 220
7 Φ89×6 Φ60×6 318
8 Φ108×6 Φ76×6 377
9 Φ114×6 Φ89×6 337
10 Φ133×6 Φ89×6 495
11 Φ159×6 Φ114×6 550
12 Φ159×8 Φ114×8 554
13 Φ159×10 Φ114×10 557
14 Φ219×6 Φ159×6 720
15 Φ219×8 Φ159×8 724
16 Φ219×10 Φ159×10 727
17 Φ245×8 Φ168×8 864
18 Φ245×20 Φ168×20 886
19 Φ273×8 Φ194×8 923
20 Φ273×10 Φ194×10 926
21 Φ325×8 Φ219×8 1168
22 Φ325×10 Φ219×10 1172
23 Φ377×8 Φ245×8 1412
24 Φ426×8 Φ273×8 1635
25 Φ426×10 Φ273×10 1640
26 Φ529×12 Φ377×12 1835
技术要求:
1、Φ114及以下规格钢管下料长度误差操纵在±3mm以内,端面与轴线垂直度应操
纵在±1mm以内;Φ114以上规格钢管下料长度误差操纵在±5mm以内,端面与轴
线垂直度应操纵在±2mm以内。
2、下料后将管坯端面及内外表面打磨洁净,不得有毛刺、划伤、氧化铁等。
附件2
冷推成型钢制弯头下料尺寸
〔单位mm〕
B
α
β
C
A
序号 口径 壁厚 外弧A 平口C
1 φ32 2.8 / 3.4 97 44 42 5
2 φ34 2.8 / 3.4 102 46 46 5
3 φ38 2.8 / 3.6 125 62 54 7
5 φ45 2.8 / 3.6 155 81 65 10
6 φ48 2.8 / 3.6 155 76 65 10
7 φ57 2.8 / 4.0 193 99 85 12
8 φ60 2.8 / 4.0 195 96 87 12
9 φ73 3.5 / 5.2 237 117 107 15
10 φ76 3.5 / 5.2 238 113 108 15
11 φ89 4.0 / 5.5 290 143 130 18
12 φ108 4.0 / 5.9 375 197 170 18
13 φ114 4.0 / 6.0 375 187 170 18
14 φ133 5.0 / 6.3 472 253 215 20
15 φ140 5.0 / 6.6 474 243 217 20
16 φ159 5.0 / 7.1 / 10 555 293 263 20
17 φ168 5.0 / 7.1 560 283 268 20
18 φ219 6.5 / 8.2 / 10 730 359 340 20
19 φ273 6.35 / 9.27 890 440 420 25
20 φ325 8.0 / 10 1080 544 500 25
21 φ377 8.0 / 10 1250 628 600 30
22 φ426 8.0 / 10 1400 700 660 30
内弧B 内弧B
〔碳钢〕 〔不锈钢〕
技术要求:
1、保证角度操纵,两头锯切面垂直于同一平面,长度操纵以A为主。
2、碳钢坯料切斜角度为α=30°,β=47°,不锈钢为α=30°,β=49°。
3、锯切后端面产生的毛刺要打磨洁净,内弧尖角要光滑过度。
可视对讲机价格-中微公司股票
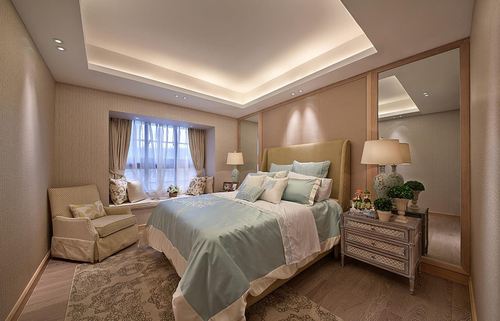
更多推荐
海利不锈钢管
发布评论