2024年1月1日发(作者:邢子陶)
实验一 车床三向力静刚度测定
一、实验目的与要求:
1.熟悉车床静刚度的测定方法。
2.比较车床各部件刚度的大小,分析影响车床刚度的各种因素。
3.巩固和验证《机械制造工艺及夹具设计》中有关系统刚度和误差复映规律的概念。
二、实验设备和仪器:
6140车床。
2.三向力静刚度测定仪。
3.千分表。
三、实验方法:
1.锁紧套与弓形体的安装:
千分表刻线向旋转刻线钢球
图 1
将紧锁套9(见图1)装在车床尾座套筒上。由于在该套上有两个相互垂直的平面,所以可将磁性表座安放在小拖板上,用百分表在套9的水平面上拉表,或将角尺放在床身上,依套9的垂直平面找正,当找正后,即将两个夹紧螺钉12固定,这时,套9上的刻线即位于车床前后顶尖轴线所处的水平平面内,随后将弓形体1装在车床两顶尖之间,摇动尾座手把将顶尖压在弓形体1右顶尖孔中,再将销8插入套9的孔中,将手把2扭入弓形体所选定º的螺纹孔中(如图1所示为30).
2.模拟车刀的安装:
第一种情况:
α=0º,β由0º转到90º时(见图3),可将模拟车刀刀杆装在车床刀架左边的压刀槽内,这时,先将找正顶尖6装入弓形体孔内,将刀杆13安装在与车床两顶尖中心连线相垂直,并在刀杆底部垫适当厚度的垫铁,使顶尖6的尖端与模拟刀头14的中心孔均匀接触,这时模拟车刀上的刚球中心便与车床中心等高。若弓形体转动不同的ß角,可将模拟车刀刀头转适应的角度,转角大小以刀头与测力圈不相撞为准。
第二种情况:
α=30º,β由0º转到90º时。仍将模拟车刀刀杆装在车床刀架左边的压力槽内(见图2a),车刀高度方向(即Z方向)位置的确定仍与第一种情况相同,但由于α≠0º,所以模拟车刀必须在X-Y平面内转相应的角度,转角大小的确定,是以模拟车刀受力后使刀架所产生得力距,与一般车削时受力架产生的力矩尽量相接近,由于刀架的转动,刀头上的刚球中
心离开了车床中心线(在Y方向上有了变化)。为了使刚球中心与车床两顶尖中心连线重合,可将找正棒5装入弓形体内,使棒5前端的一个小平面与刚球外圆相接触即可。为了将棒5由弓形体内取出,可移动大拖板,使模拟车刀与找正棒一起向车头移动,即可将棒5取出,若弓形体转动不同的β角,可将刀头14也转相应的角度,转角大小以模拟车刀刀头与测力圈不相碰撞为准。
第三种情况:
α=45º、α=60º,β由0º转到90º时。刀杆沿Z向和沿Y向位置的确定,仍与第一、二种情况相同,但由于α≥45º,为了使模拟车刀受力后使刀架所产生的力矩尽量相近,所以,应将刀杆装入刀架的右刀槽内(见图2b),并将刀架转相应的角度。
3.测力圈的安装:
将测力圈安放于手把2和模拟车刀之间(见图1),扭动手把2,测力圈便产生变形。
4.千分表的安放:
为简化起见,可将床身变形忽略不记。因此可将磁性表座装在床身上,千分表触头分别抵在车头、尾座和刀架上。
5.尾座套筒伸出长度约50毫米。
6.实验过程中应注意的问题:
(1)将刀架的纵、横楔铁特别是横向楔铁,一定要将间隙调节适当,间隙太大会发生爬行;间隙太小,刀架变形会很小。
(2)将模拟车刀刀杆牢牢的压在刀架上,否则,受力过大后刀杆会移动。
(3)将尾座的各个活动环节要紧固好。
(4)在实验过程中,将弓形体转过β角后,为了防止测力圈由弓形体内掉下,可以用一细铁丝将测力圈与弓形体连接在一起。一般刀(b)模拟刀
模拟车刀(a)一般车刀图 2
四、实验记录与数据处理:
切削力P与各切削分力之间的关系:
设切削力P与Y-Z平面间的夹角为α,载荷P在Y-Z平面内的投影与Z轴的夹角β,由图3可以看出各切削分力值为:
图 3
Px=Psinα
Py=Pcosαsinβ
Pz=Pcosαcosβ
当α=0º、β=30º、45º、60º,α=30º、β=30º、45º、60º时,切削力P与各切削分力的数值可由附表中查出。
2.静刚度的计算:由于模拟切削力施加于弓形体长度的中心处,因此,机床,床头,尾座,刀架之间的刚度关系可以用下式表示
11111()j机i刀4j头j尾
p尾p刀j刀j尾j头yyy尾
刀
头 而
p头式中Y头、Y刀、Y尾为在其中所受不同载荷的情况下,车头、刀架、尾座的对应变形值,该值可由千分表读出,显然,P刀=Py,P头、P尾为Py所引起的在车头和尾架处的作用力。
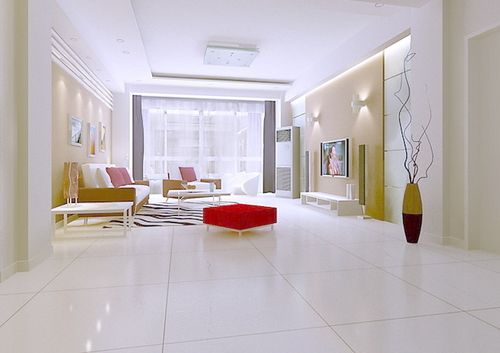
更多推荐
车床,刀架,模拟
发布评论