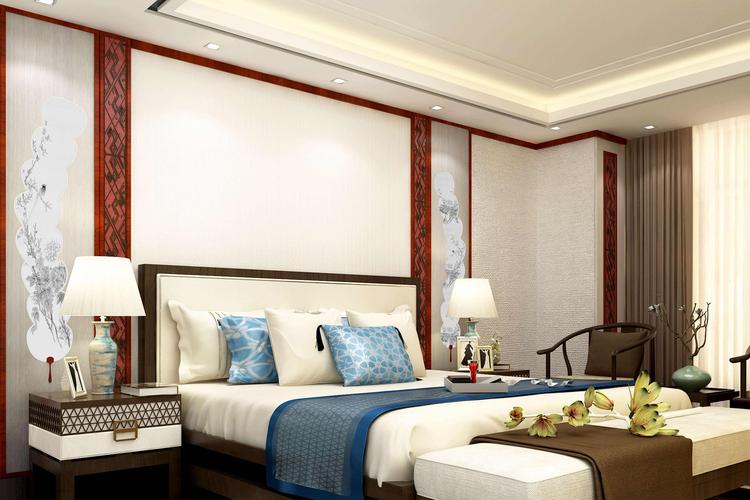
1 实验目的
通过陶瓷工艺设计性综合实验,达到以下目的:
(1)深刻常用陶瓷原料在陶瓷坯料中的作用;
(2)掌握坯料配方设计和实验研究方法;
(3)掌握实验技能,提高动手能力;
(4)提高分析问题和解决问题的能力;
(5)为毕业论文实验、进一步深造或从事专业技术工作奠定良好的基础。
2 实验安排
2.1查资料,进行坯体配方设计和计算, 完成实验方案设计报告。
2.2实验过程(4~5周)
2.2.1原料处理(粉碎机或研钵)
(颗粒小于1mm或全部通过20目筛)
2.2.2配料、球磨、烘干、造粒
配料量 300g
2.2.3成型
按模具尺寸、每个7g原料成型试样33个以上, 测试烧结温度范围用20个,按烧成温度烧成10个
图2-1 实验流程
2.3完成实验总结报告(2周)
3设计内容
3.1课题背景、目的和意义
目前,我国的陶瓷墙地砖生产量在世界排名第一,陶瓷墙地砖已经广泛用于楼堂馆所及民用建筑,在国民经济和人民生活中,该产业的位置已经今非昔比、相当重要。墙地砖的生产,首先涉及的便是坯釉料配方,例如设计配方前应该考虑什么问题, 关于配方的一般工艺技术问题,已经有不少的文章作了详细的论述,然而高度和全面性则不够。行内人士都知道,陶瓷墙地砖坯釉料配方是陶瓷生产企业生产和技术管理中非常重要的部分。本人在这里仅就其坯料着手,并充分考虑到低温一次快烧对坯料要求的特点, 优级品率达到85%-90% ,烧成周期约28min ,最高烧成温度约1180℃并希望通过试验,不断调整配方,使其不仅可以作为实验研究,而且还能投入到大生产中。在这里对陶瓷墙地砖坯料配方设计问题作一简述,旨在抛砖引玉。
3.2配方设计
表3-1实验原料的化学组成(wt%)
原料 | SiO2 | Al2O3 | Fe2O3 | TiO2 | CaO | MgO | K2O | Na2O | 烧失量 |
石英 | 98.5 | 0.7 | 0.1 | 0.1 | - | 0.3 | 0.3 | ||
长石 | 64.3 | 18.9 | 0.1 | - | 0.6 | 0.2 | 13.7 | 2.1 | 0.5 |
生砂石 | 44.2 | 39.5 | 0.2 | 0.1 | 0.2 | - | - | - | 15.8 |
碱矸 | 37.5 | 39.3 | 0.6 | 1.4 | 1.4 | 1.8 | 0.2 | 2.1 | 15.7 |
滑石粉 | 62.0 | 0.4 | 0.1 | - | 1.5 | 30.5 | - | - | 5.5 |
洪江土 | 49.5 | 34.4 | 0.4 | - | 0.3 | 0.1 | 1.2 | 0.4 | 13.3 |
苏州土 | 46.43 | 39.87 | 0.50 | - | 0.32 | 0.10 | - | - | 12.30 |
表3-2 初步设计的坯料的化学成分
SiO2 | Al2O3 | Fe2O3 | TiO2 | CaO | MgO | K2O | Na2O |
67.0 | 24.5 | 1.4 | 0.3 | 2.0 | 1.0 | 2.0 | 1.8 |
3.3计算过程
表3-3不含烧失的实验原料的化学组成(wt%)
原料 | SiO2 | Al2O3 | Fe2O3 | TiO2 | CaO | MgO | K2O | Na2O |
石英 | 98.8 | 0.7 | 0.1 | 0.1 | - | 0.3 | ||
长石 | 64.4 | 18.9 | 0.1 | - | 0.6 | 0.2 | 13.7 | 2.1 |
碱矸 | 44.5 | 46.6 | 0.7 | 1.7 | 1.7 | 2.1 | 0.2 | 2.5 |
滑石粉 | 65.6 | 0.4 | 0.1 | - | 1.6 | 32.3 | - | - |
所用原料的百分含量:
滑石粉:1.0/32.3=3.1%
长石:(1.8+2.0)/(13.7+2.1)=24.1%
碱矸:(24.5-0.4*3.1%-18.9*24.1%)/46.6=42.8%
石英:1-3.1%-24.1%-42.8%=30%
制备300g坯料所用的原料质量
滑石粉:300*3.1%=9.3g
长石:300*24.1%=72.3g
碱矸:300*42.8%=128.4g
石英:300*30%=90g
3.4最终设计的配方
表3-4 实际设计的坯料的化学组成
SiO2 | Al2O3 | Fe2O3 | TiO2 | CaO | MgO | K2O | Na2O |
66.2 | 24.7 | 0.4 | 0.8 | 0.9 | 2.0 | 3.4 | 1.6 |
表3-5 最终设计的原料配方组成
滑石粉 | 长石 | 石英 | 碱矸 |
3.1% | 24.1% | 42.8% | 30% |
3.5性能测试
3.5.1烧成过程的变化及烧成温度的确定
⑴ 烧成过程的变化
物理变化:体积收缩至稳定,气孔率大变小至很小稳定,强度增大,密度增大。
化学变化:高岭土→莫来石、无定形铝硅化合物、液相
长石 → 液相、析出二次莫来
石英 → 液相、石英
⑵烧成温度的确定
烧成温度:达到性能要求所需的热处理温度。
瓷化温度:气孔率最小、密度最大时的温度(范围),此时强度最大。
确定方法:测定不同温度小收缩率、气孔率(吸水率),作温度-收缩率,温度-吸水率图。
更多推荐
实验,配方,设计,温度,坯料,陶瓷
发布评论